製造需要 精度 そして 効率 競争力を維持するために5軸CNCマシニングは、3軸システムの限界を克服し、高品質で複雑なパーツの製造を可能にする。その柔軟性と精度は、航空宇宙、自動車、医療機器製造、金型製造などの産業にとって不可欠です。以下は、精密部品の5軸CNC加工の主な利点です。

複雑な形状の取り扱い
5軸CNCマシニングは、複雑で非標準的な形状を簡単に加工します。X、Y、Zの直線運動に限定された3軸加工機とは異なり、5軸システムには2つの回転軸(A軸とB軸またはC軸)が含まれています。これにより、切削工具をあらゆる角度から加工物にアプローチさせることができ、複雑なサーフェス、アンダーカット、不規則な形状の加工を1回のセットアップで行うことができます。
航空宇宙およびタービン製造におけるアプリケーション
航空宇宙産業やタービン産業では、タービンブレードなどのコンポーネントに5軸加工が使用されています、 インペラやエアロダイナミクスパーツに使用されます。これらの部品は、複雑な曲線、輪郭のあるサーフェス、厳しい公差(±0.005 mm以上)を特徴としており、3軸加工機では複数のセットアップを行わないと達成することが困難です。タービンブレードでは、正確な曲率で5面の加工が必要になることがあります。5軸加工では、これを1回のセットアップで完了し、寸法精度と一貫性を確保します。
DMG MORI DMU 50のようなハイエンド5軸加工機の仕様には、±0.002 mmの位置決め精度と、このような用途に理想的な最高18,000 RPMの主軸回転速度が含まれています。これらの機械は、航空宇宙分野で一般的なインコネルやチタンなどの材料を、工具の摩耗を最小限に抑えて加工します。
セットアップ時間とエラーの削減
複数のセットアップ 三軸加工 の場合、ミスアライメントのリスクが生じ、精度が損なわれます。5軸加工では、1つの治具を使用するため、位置決め誤差を最小限に抑えることができます。複数の角度を必要とする金型キャビティは、1つの基準に対して加工することができ、±0.003 mmという厳しい公差を実現します。これは、Haas UMC-750を使用している金型製造会社のケーススタディに見られるように、3軸システムと比較してセットアップ時間を最大50%短縮します。
シングルセットアップ加工は、医療用インプラントや自動車用金型のような精密部品のバッチ生産に不可欠な再現性を高めます。
ワークフローの合理化
オペレーションを統合することで、5軸加工はワークフローを簡素化します。航空宇宙用構造部品のような複雑な部品には、次のような加工が必要な場合があります。 ミーリング穴あけ、輪郭加工。5軸加工機では、これらを1サイクルで行うため、ハンドリングや固定具の必要性が軽減されます。これにより、人件費が削減され、リードタイムが短縮されます。一部のメーカーでは、総加工時間が30~40%短縮されたと報告しています。

精度と表面品質の向上
5軸CNCマシニングがもたらすもの より厳しい公差 そして 優れた表面仕上げ.同時に多軸を動かすことで、振動や工具のたわみを最小限に抑え、より滑らかな切削軌跡を実現します。これは、医療用インプラントや高性能エンジン部品など、非常に高い精度が要求される部品に不可欠です。
最適化されたツールパス
5軸加工における動的な工具姿勢制御は、複雑なサーフェスに対する垂直性を維持し、スキャロッピングを低減し、Ra 0.2 µmの仕上げ精度を保証します。生体適合性のために表面粗さがRa 0.4 µm以下でなければならない医療用インプラントでは、これは非常に重要です。Mazak INTEGREX i-400のような機械は、±0.01度の角度精度を達成し、このような精度をサポートします。
ツールパスの最適化により加工誤差を低減放物面リフレクターを加工する際、5軸システムは切り屑の負荷を一定に保ち、軸制御の制限により3軸システムが遭遇する偏差を回避します。
後処理を最小限に抑える
5軸加工による優れた表面品質が、後加工の必要性を低減。自動車エンジン部品は、機械から直接鏡面仕上げ(Ra 0.1~0.3 µm)を実現するため、研磨が不要になります。これにより、研磨などの二次加工が最小限に抑えられるため、生産コストを10-20%節約できます。オークマのMU-5000Vのデータでは、3軸システムと比較して25%の仕上げ面精度の向上が確認されています。
バッチ間の一貫性
5軸加工は、大量生産における均一性を保証します。切削条件を一定に保つことで、バッチ間で同一のパーツを生産することができます。これは、コネクターに±0.01 mmの公差が要求されるエレクトロニクスのような産業には不可欠です。シーメンスNXのような高度なCAMソフトウェアは、正確な5軸ツールパスを生成することで、これを強化します。
生産時間の短縮
5軸CNCマシニングは、1回のセットアップで多面加工を可能にし、繰り返しの位置決めをなくすことで、生産サイクルを短縮します。これにより、生産が加速され、スループットが向上します。
シングル・セットアップの効率
3軸加工機で複数回のセットアップが必要な金型も、1回の5軸加工サイクルで完了します。アンダーカットや角度のある自動車用金型は、15,000 RPMで同時5軸加工をサポートするHermle C 42 Uのような5軸加工機では、60%の短時間で加工できます。この効率性は、自動車や家電の分野では不可欠です。
ダウンタイムの最小化
セットアップ時間の短縮により、機械のダウンタイムが減少します。3軸システムでは、複雑なパーツの再固定に2~3時間を要することがありますが、5軸機では同じ作業を30分以内で完了します。これにより、機械の稼働率が向上し、5 軸技術を採用した結果、20% の生産量増加を報告した工場もあります。
大規模プロジェクトのためのスケーラビリティ
5軸加工は、大規模プロジェクトでも効率的に拡張できます。構造部品を製造する航空宇宙メーカーは、段取り替えを最小限に抑えたバッチ加工からメリットを得ています。FANUC Robodrill D21LiB5 のような機械は、15~25% のサイクルタイム短縮を実現し、品質を犠牲にすることなくスケーラビリティを実現します。
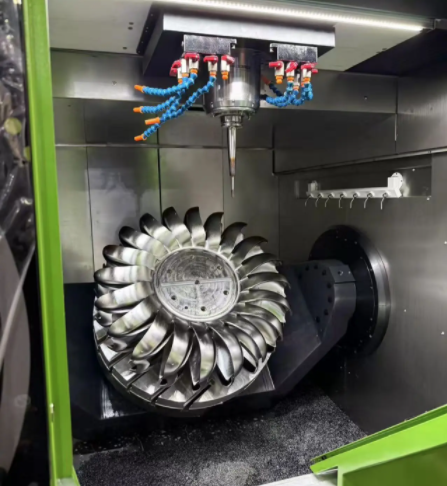
工具寿命の延長とコスト削減
5軸CNC加工は、理想的な工具角度を維持することで切削を最適化し、応力と摩耗を低減します。オーバーハングの少ない短い工具は剛性を高め、振動を最小限に抑え、パフォーマンスを向上させます。
最適化された切削条件
最適な切削角度を維持することで、工具摩耗が20~30%減少することが、サンドビック・コロマント社の研究で報告されています。チタンの加工では、5軸加工機が工具経路を調整して熱の蓄積を最小限に抑え、工具寿命を最大50%延長します。これは、超硬エンドミルのような高コストの工具にとって非常に重要です。
メンテナンスコストの削減
工具の摩耗が減少するため、交換やメンテナンスのコストが削減されます。チタン加工用の超硬工具1本のコストは、$100~$300です。工具寿命を30%延ばすことで、大量生産工場では年間数千ドルの節約になります。セットアップ回数が減ることで人件費が削減され、15%の削減を報告するメーカーもあります。
エネルギー効率
5軸加工機は、サイクルタイムが短いため、部品あたりの消費電力が少ない。GF Machining Solutions社の調査によると、5軸システムは複雑なパーツの加工において、3軸加工機よりも10~15%少ない電力を使用し、コスト削減と持続可能性に貢献しています。
難削材の加工
現代の製造業には、高い強度と靭性で知られるチタン合金、ステンレス鋼、複合材などの素材が使用されています。5軸CNCマシニングは、これらの材料を精密かつ制御しながら加工することに優れています。
タフな素材における精度
チタン合金 (Ti-6Al-4Vなど)では、低速切削(50~80m/min)と高トルクが要求される。Makino T1のような5軸加工機は、安定した切りくず負荷を維持し、Ra 0.5 µmの表面仕上げを達成します。これはランディングギア部品のような航空宇宙部品にとって非常に重要である。
複合材料の取り扱い
炭素繊維強化ポリマー(CFRP)などの複合材料は、層間剥離を起こしやすい。5軸加工では、特殊なツールパスを使用して繊維の引き抜きを最小限に抑え、きれいなエッジを実現します。CMS Aresのような機械は、CFRP加工に理想的な最高24,000 RPMの主軸速度を提供します。
業種を超えた汎用性
医療機器(ステンレス製インプラント)からエネルギー分野の部品(インコネル製タービンブレード)まで、5軸加工は多様な材料に適応します。高硬度材(60 HRCまで)にも対応できるため、ハイエンド用途には欠かせません。

ケーズハードウェアによる精密5軸CNC加工
Kesu Hardware Groupでは、最新鋭のAFM 5軸およびMikron 5軸CNCマシニングセンターにより、複雑で高品質な部品を必要とする産業向けに、比類のない精度と汎用性を提供しています。
ミクロンE 700Uと大ストロークGMU-800EVO(プラットフォームサイズ800mm、X/Y/Zストローク:850/950/550mm)を含むケスの先進設備により、非標準の高精度部品をMOQなしでワンストップソリューションとして提供し、自動車、医療、航空宇宙、エレクトロニクス産業の厳しい要求を満たします。今すぐ2D/3D図面をアップロードして、即座に見積もりを取得し、品質と効率に対するケスのコミットメントを体験してください。
結論
5軸CNCマシニングは、次の点で大きな飛躍を意味する。 精密製造従来の3軸システムに比べ、比類のない利点を提供します。複雑な形状を扱い、精度を高め、生産時間を短縮し、工具寿命を延ばし、難しい材料を加工するその能力は、高品質の精密部品を生産するために不可欠な技術となっています。精度、効率、多用途性が求められる産業にとって、5軸加工は単なるツールではなく、イノベーションと卓越性を推進する競争上の優位性なのです。
5軸CNCマシニングに投資することで、メーカーは従来の方法の限界を克服し、オペレーションを合理化し、今日の市場の厳しい要求を満たす優れた製品を提供することができます。航空宇宙部品、複雑な金型、高性能な自動車部品の製造のいずれにおいても、5軸加工の利点は、精度と効率の両立を保証します。
よくある質問精密部品の5軸CNC加工
5軸CNC加工とは?
5軸CNCマシニングは、5つの移動軸(X、Y、Z、および2つの回転軸、通常はAとBまたはC)を持つマシンを使用して、1つのセットアップで複雑なパーツを加工し、3軸システムよりも高い柔軟性と精度を提供します。
5軸加工はどのように精度を向上させるのか?
より滑らかなツールパス、最適な工具角度の維持、振動の低減を可能にし、±0.002 mmという厳しい公差とRa 0.4 µm以下の仕上げ面精度を実現します。
5軸加工のメリットを最も享受できる産業は?
航空宇宙産業、自動車産業、医療産業、金型製造産業は、複雑な形状、厳しい公差、チタンや複合材料のような難易度の高い材料を必要とするため、その恩恵を受けている。
5軸加工は費用対効果が高いか?
セットアップ時間を短縮し、工具寿命を延ばし、後加工を最小限に抑えることで、高精度アプリケーションにおける15-30%のコスト削減につながります。