Five-axis CNC machining is a cornerstone of modern manufacturing, particularly for industries requiring high-precision components, such as aerospace, mold making, and shipbuilding. This article examines the technical advantages of five-axis CNC machining, the features of the Heidenhain control system, and the practical application of tool radius compensation in milling complex parts. Through a detailed case study, we demonstrate the effectiveness of tool radius compensation in simplifying programming, enhancing machining accuracy, and ensuring consistent part quality.
Introduction to Five-Axis CNC Machining
Five-axis CNC machining is designed to address the challenges of producing complex parts with intricate geometries, such as freeform surfaces and multi-angle features. Unlike traditional three-axis machining, five-axis systems incorporate three linear axes (X, Y, Z) and two rotational axes (typically A or B, and C), enabling the tool to approach the workpiece from multiple angles. This capability is critical for industries where precision and surface quality are paramount.
The increasing demand for high-precision components has driven the adoption of five-axis CNC machines. These systems offer enhanced flexibility, reduced setup times, and improved surface finishes, making them ideal for manufacturing complex parts in a single setup. Additionally, the integration of advanced numerical control systems, such as the Heidenhain system, enhances the machine’s usability and performance, ensuring consistent results in high-stakes applications.
Characteristics and Advantages of Five-Axis CNC Machining
Five-axis CNC machining offers distinct technical advantages over traditional three-axis systems, addressing limitations in machining complex geometries and improving overall efficiency.
Key Characteristics
The defining feature of five-axis CNC machining is its ability to control three linear axes and two rotational axes simultaneously. This allows the tool to maintain optimal orientation relative to the workpiece, enabling the machining of complex surfaces and angles that are inaccessible to three-axis systems. Five-axis machining can be categorized into two types:
- Positioning Five-Axis: The tool’s axis vector is fixed during machining, with the X, Y, and Z axes controlling the tool path while the A (or B) and C axes adjust the tool’s orientation.
- Five-Axis Simultaneous Machining: The tool’s axis vector changes dynamically throughout the cutting path, controlled by all five axes to achieve complex tool paths.
技術的な利点
The advantages of five-axis CNC machining are rooted in its ability to streamline processes and enhance precision:
- Reduced Setup Times: By allowing multi-angle machining in a single setup, five-axis systems minimize the need for multiple clamping operations, reducing setup errors and time.
- Improved Tool Utilization: For steep or complex surfaces, shorter tools can be used, reducing deflection and extending tool life while maintaining precision.
- Enhanced Surface Quality: The ability to use the tool’s side and bottom edges optimizes cutting conditions, improving surface finish and reducing the need for manual polishing.
- Shortened Production Cycles: Integration with high-speed machining reduces reliance on secondary processes like electrical discharge machining (EDM), streamlining production and reducing lead times.
These advantages make five-axis CNC machining indispensable for industries requiring high precision and efficiency.
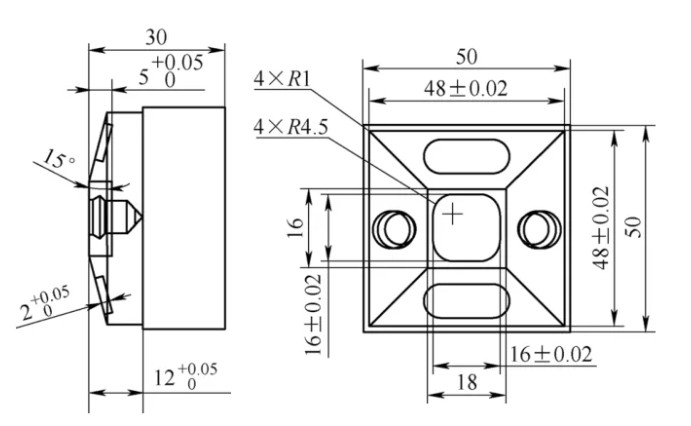
Heidenhain Control System Features
The Heidenhain control system is widely regarded for its robustness and user-friendly interface, making it a preferred choice for five-axis CNC machining. Designed for shop-floor programming, it supports ミーリング, drilling, boring, and contour machining with high precision and efficiency.
Key features of the Heidenhain system include:
- Structured Programming: The system uses clear forms and graphical interfaces to simplify programming, enabling operators to create complex tool paths efficiently.
- User-Friendly Interface: Intuitive controls and a logical layout reduce the learning curve, making it accessible for operators of varying skill levels.
- High-Speed and High-Precision Capabilities: Optimized algorithms ensure fast processing and precise tool movements, critical for complex geometries.
- Coordinate Transformation Cycles: The system supports transformations such as origin shifts, mirroring, rotation, and scaling, enabling flexible machining of tilted or rotated workpieces.
These features enhance the system’s compatibility with various CNC machines, ensuring reliable performance in demanding applications.
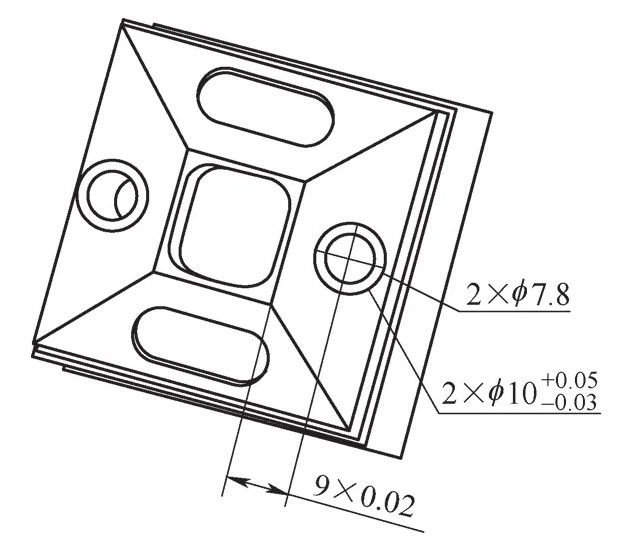
Tool Radius Compensation in CNC Milling
Tool radius compensation is a critical aspect of CNC milling, allowing programmers to account for variations in tool dimensions without modifying the core program. This technique is particularly important in five-axis machining, where precision is paramount, and tool wear, regrinding, or replacement can affect machining outcomes.
Principles of Tool Radius Compensation
で CNCフライス加工, tool radius compensation adjusts the tool path to account for the actual radius of the tool, ensuring the machined contour matches the programmed dimensions. This is achieved by offsetting the tool’s center path by the tool’s radius, which is stored in the machine’s tool table. The process involves:
- Measuring the actual tool radius (R′) using a three-coordinate measuring machine.
- Performing rough machining with a predefined tool radius (χ) and measuring the resulting dimensions.
- Calculating the machining allowance (δ) and adjusting the tool radius in the tool table for finish machining.
Graphical Analysis Method for Tool Radius Compensation
The graphical analysis method simplifies the understanding and application of tool radius compensation. By visualizing the tool path and machining allowance, operators can accurately calculate the required compensation values. Below is an example of applying this method to a part with a 48 ± 0.02 mm slot, using a φ10 mm milling cutter with an assumed radius (χ) of 5.1 mm.
External Contour Machining
For external contour machining, the tool path is offset outward from the part’s contour. The process is as follows:
パラメータ | 説明 | Value |
---|---|---|
χ | Assumed tool radius | 5.1 mm |
δ | Machining allowance | Variable |
A | Measured dimension | 48.1 mm |
B | Ideal dimension | 48.2 mm |
C | Measured dimension | 48.3 mm |
If the measured dimension is 48.1 mm, the actual tool radius is calculated as 5.05 mm; if 48.3 mm, it is 4.95 mm. These values are entered into the tool table for finish machining, ensuring the final dimension falls within the 48 ± 0.02 mm tolerance.
Internal Contour Machining
For internal contour machining, the tool path is offset inward. Using the same φ10 mm cutter and assumed radius of 5.1 mm, the process is similar:
パラメータ | 説明 | Value |
---|---|---|
χ | Assumed tool radius | 5.1 mm |
δ | Machining allowance | Variable |
D | Measured dimension | 47.7 mm |
E | Ideal dimension | 47.8 mm |
F | Measured dimension | 47.9 mm |
Measured dimensions of 47.7 mm or 47.9 mm correspond to actual tool radii of 4.95 mm or 5.05 mm, respectively, which are adjusted in the tool table for finish machining.
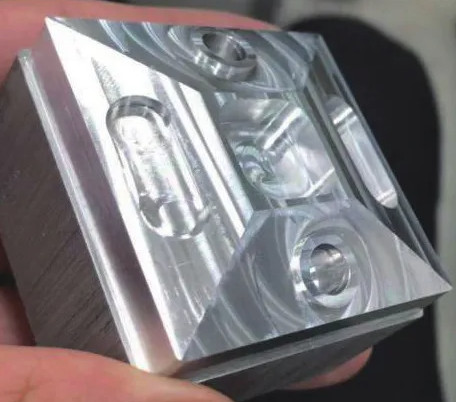
Case Study: Milling a Complex Part
To illustrate the practical application of five-axis CNC machining and tool radius compensation, we analyze the milling process of a complex part with four inclined planes, a central hole, a keyway, and a boss, as described in the original document.
Part Description
The part features a 48 ± 0.02 mm outer contour, a 16 × 16 mm central hole, four inclined planes, a keyway (8.5 +0.04/0 mm), a boss, and two φ7.8 mm holes. The Heidenhain system is used to program the machining process, leveraging its coordinate transformation and milling cycles.
加工プロセス
The machining process involves the following steps:
- Outer Contour Milling: A φ10 mm milling cutter is used with an assumed radius of 5.1 mm for rough machining. After measuring the resulting dimensions, the tool radius is adjusted (e.g., to 5.05 mm or 4.95 mm) for finish machining to achieve the 48 ± 0.02 mm tolerance.
- Central Hole Milling: The 16 × 16 mm hole is machined using the same cutter, with a rough machining depth of 5.025 mm. After measurement, tool radius and length compensation are adjusted for finish machining.
- Inclined Plane Milling: Coordinate transformation is applied by rotating the C-axis to align the machining plane. The milling depth (H) is calculated as H = 3.88 mm using the formula H = L₂ × tan(α), where L₂ = 48 mm and α = 9°. The depth is set to -4 mm for safety.
- キー溝加工: A φ6 mm cutter is used to machine the 8.5 mm keyway, with a rough machining width of 8.52 mm. Tool radius compensation is applied for finish machining.
- Boss Milling: A circular boss cycle is used, with tool radius compensation applied to ensure dimensional accuracy.
- Hole Drilling: Two φ7.8 mm holes are drilled using a drilling cycle, with a depth of -11.25 mm, ensuring precise coordinate settings.
結果
The part is machined within specified tolerances, demonstrating the effectiveness of the Heidenhain system’s coordinate transformation and tool radius compensation. The process minimizes setup changes, reduces machining time, and ensures consistent quality.
結論
Five-axis CNC machining, supported by advanced control systems like Heidenhain, offers significant advantages in manufacturing complex parts. The ability to machine multi-angle features in a single setup reduces setup times, enhances precision, and improves surface quality. Tool radius compensation, facilitated by graphical analysis, simplifies programming and ensures dimensional accuracy without modifying the core program. The case study highlights the practical application of these techniques, demonstrating their reliability and efficiency in achieving high-quality results.