This study presents a detailed investigation into achieving a mirror finish on copper alloy V-grooves, specifically for parts made from H62 brass, targeting a surface roughness of Ra=0.2μm and a coaxiality of φ0.01mm. Through systematic experimentation, the research optimizes tool selection, machining parameters, and programming methods to enhance surface quality while maintaining dimensional accuracy. The findings provide a reliable, experience-based methodology for high-precision machining of copper alloy components, supported by practical trials and validated through batch production.
Introduction to Copper Alloy Machining Requirements
The increasing demand for high-performance components in industries such as electronics and aerospace has driven stricter requirements for dimensional accuracy, geometric tolerances, and surface finish. Copper alloys, particularly H62 brass, are valued for their excellent mechanical properties, including high plasticity and good machinability. However, their tendency to stick to cutting tools makes grinding unsuitable, as it can lead to surface imperfections and tool wear. Turning, particularly mirror finish turning, is the preferred method for achieving the desired surface roughness. This study analyzes the factors influencing surface roughness in copper alloy machining and develops a turning process to meet the Ra=0.2μm requirement for V-groove structures, providing a theoretical and practical foundation for improving part quality.
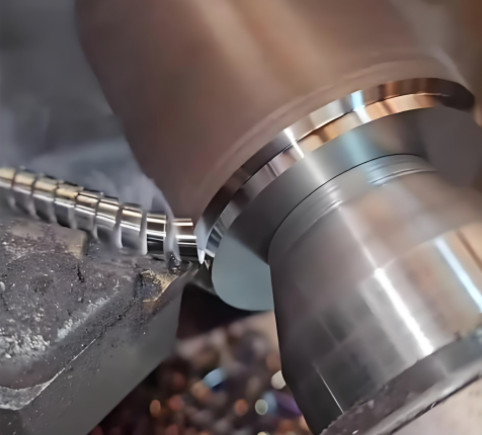
Part Structure and Machining Specifications
The component under study is a copper alloy part made from H62 brass, featuring a V-groove with a 60° angle. The design specifications mandate a coaxiality of φ0.01mm between the V-groove and the inner cylindrical surface, alongside a surface roughness of Ra=0.2μm. H62 brass offers favorable mechanical properties, including good plasticity and machinability, but its adhesive nature during machining can lead to tool sticking, complicating the achievement of a mirror finish. Current factory processes achieve a surface roughness of Ra=0.8μm, which falls short of the design requirement. This gap necessitates a detailed exploration of machining techniques to optimize surface quality while ensuring dimensional precision.
Evaluation of Machining Processes
Three machining approaches were considered to achieve the target surface roughness: mirror finish turning, cloth wheel polishing, and electrolyte plasma polishing. Each method was assessed for its feasibility, compatibility with existing equipment, and ability to meet the stringent surface quality requirements.
Mirror Finish Turning
Mirror finish turning was identified as the most practical approach due to its alignment with existing lathe capabilities and straightforward process control. This method involves selecting appropriate tools, optimizing machining parameters, and refining programming techniques to achieve a mirror-like surface. The key aspects of this approach are detailed below.
ツール選択
Tool material is critical for achieving a mirror finish. The factory initially used cemented carbide tools, composed of tungsten carbide (WC), tungsten-cobalt-titanium (WC-TiC), or tungsten-titanium-tantalum-cobalt (WC-TiC-TaC), bonded with cobalt or nickel through powder metallurgy. These tools offer high hardness, wear resistance, and thermal stability, making them suitable for rough machining of non-ferrous metals like copper alloys. However, for mirror finish turning, diamond tools were preferred due to their exceptional hardness, low friction coefficient, high thermal conductivity, and minimal affinity with copper, which reduces the formation of built-up edges.
Polycrystalline diamond (PCD) tools with ultra-fine particles were selected for their balance of sharpness, durability, and cost-effectiveness. The chosen tool was a Kyocera PCD insert (VBMT110301NE KPD001) with a 35° tip angle and a 0.1mm tip radius, mounted on an MVVNN symmetrical tool holder to minimize interference during V-groove machining. The ultra-fine PCD structure enhances tool strength, wear resistance, and edge sharpness, enabling stable, high-quality surface finishes.
Machining Parameters
Machining parameters, including feed rate, spindle speed, and–
depth of cut, directly influence surface roughness. In mirror finish turning, reducing the feed rate below a critical threshold shifts the primary influence to spindle speed. Similarly, when the depth of cut falls below a specific value, surface roughness increases rapidly, while above this value, it exhibits a near-linear increase. Experimental trials were designed to identify optimal parameter combinations for H62 brass, focusing on achieving the Ra=0.2μm target. Parameters were systematically varied to balance surface quality, tool life, and machining efficiency.
Tool Geometry Considerations
The 60° V-groove geometry required careful tool angle selection to avoid interference during machining. Two insert angles, 35° and 45°, were tested with different mounting configurations. The 35° insert was selected for its compatibility with the V-groove’s geometry, reducing the risk of tool-workpiece interference and ensuring precise contouring of the groove. The symmetrical MVVNN tool holder further facilitated accurate tool positioning and stability during machining.
Cloth Wheel Polishing
Cloth wheel polishing was evaluated as a secondary method to improve surface roughness from Ra=0.8μm to Ra=0.2μm. This technique uses cloth wheels of varying hardness, determined by stitching distance, to polish the workpiece surface. Three wheel types were considered: non-stitched whole cloth wheels for complex geometries, air-cooled cloth wheels for larger parts, and stitched cloth wheels for simpler shapes. A circumferential speed of 22–30 m/s was recommended for copper alloy polishing. However, the small size of the V-groove posed significant challenges in fixturing and achieving uniform polishing across the groove’s surface, making this method less practical for the application.
Electrolyte Plasma Polishing
Electrolyte plasma polishing involves passing an electric current through a polishing solution, causing metal ions to detach from the workpiece surface, particularly at protrusions, to achieve a smoother finish. Key factors affecting polishing quality include solution temperature, processing time, solution concentration, immersion depth, and flow rate. While the factory had access to plasma polishing equipment, the small V-groove dimensions required complex fixturing and equipment modifications to ensure uniform polishing. These complexities, coupled with the need for extensive parameter optimization, rendered this method less viable compared to mirror finish turning.
Selected Machining Process
After a comprehensive evaluation, mirror finish turning was selected as the optimal process due to its compatibility with existing lathe equipment, process simplicity, and ability to achieve the target surface roughness. The approach focused on optimizing tool selection, machining parameters, and programming methods. Collaboration with tool manufacturers enabled the customization of PCD inserts, and extensive experimental trials were conducted to refine the process for H62 brass V-grooves.
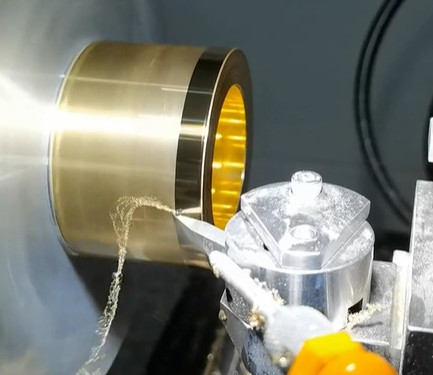
Experimental Trials and Optimization
Systematic experiments were conducted to develop a robust mirror finish turning process, focusing on programming methods, spindle speed, feed rate, and depth of cut. The trials were structured to address issues encountered during machining and ensure consistent, high-quality results.
Programming Methods
Two programming approaches were evaluated: contour tracing and direct forming tool machining. Direct forming tool machining offers higher efficiency but results in poorer surface roughness and increased tool wear due to continuous contact with the workpiece. Contour tracing, where the tool follows the V-groove’s profile incrementally, provides better surface consistency and reduces axial forces, improving coaxiality. Based on these advantages, contour tracing was adopted for the experimental trials.
Experimental Procedure
The trials were conducted in three phases to systematically refine the process:
- Cylindrical Surface Testing: Initial experiments were performed on a cylindrical surface to establish baseline machining parameters while minimizing tool wear. The PCD insert and contour tracing method achieved a mirror finish on the cylindrical surface, validating the tool and programming approach.
- Preliminary V-Groove Machining: Using the parameters from the cylindrical tests, V-groove machining was attempted. When the part thickness was reduced to 0.8mm, tool marks appeared, likely due to vibrations caused by thin walls. This issue prompted adjustments to reduce the depth of cut and feed rate while increasing spindle speed to minimize vibration effects.
- Refined V-Groove Machining: To address tool marks and surface blemishes, the process was further optimized. Cemented carbide tools were used for rough machining, leaving a 5mm machining allowance to protect the PCD insert. Finish machining was performed with the PCD insert at a spindle speed of 1200 r/min and a feed rate of 0.03 mm/r. This configuration eliminated blemishes, achieving a uniform mirror finish with consistent tool marks.
Experimental Results
The optimized process achieved a surface roughness of Ra=0.0638μm, significantly surpassing the target of Ra=0.2μm. The V-groove surface was smooth, free of blemishes, and exhibited uniform tool marks, indicating a stable and repeatable process. Surface roughness was measured using a precision roughness tester, confirming consistent results across multiple parts. Batch production trials further validated the process, demonstrating stable dimensional accuracy and surface quality that met all design specifications.
パラメータ | Value |
---|---|
工具材料 | Ultra-fine PCD (Kyocera VBMT110301NE KPD001) |
Tool Tip Angle | 35° |
Tool Tip Radius | 0.1 mm |
主軸回転数 | 1200 r/min |
フィード・レート | 0.03 mm/r |
Roughing Allowance | 5 mm |
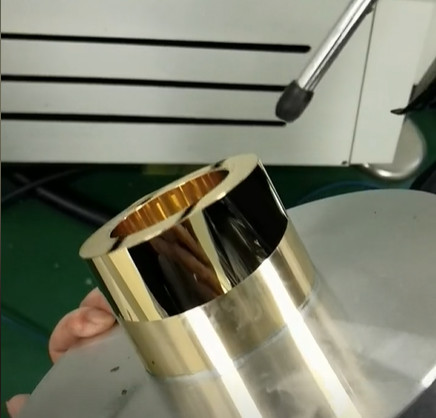
結論
Through systematic experimentation, this study developed a robust mirror finish turning process for copper alloy V-grooves, achieving a surface roughness of Ra=0.0638μm, well below the target of Ra=0.2μm. The use of ultra-fine PCD inserts (Kyocera VBMT110301NE KPD001), mounted on an MVVNN symmetrical tool holder, combined with optimized machining parameters (spindle speed of 1200 r/min, feed rate of 0.03 mm/r, and a 5mm roughing allowance), ensured a high-quality, mirror-like surface finish. The contour tracing programming method minimized axial forces, enhancing coaxiality and surface consistency. Batch production trials confirmed the process’s reliability, with stable dimensional accuracy and consistent surface quality across multiple parts.
The optimized parameters and methodology are applicable to other copper alloy components requiring mirror finish surfaces, offering a scalable solution for 高精度加工. The study’s findings provide a practical, experience-based framework for manufacturers seeking to improve surface quality in non-ferrous metal machining, demonstrating the effectiveness of combining advanced tool materials, precise parameter control, and systematic process optimization.