The rapid evolution of technology has driven the continuous advancement of 3C products—computers, communications, and consumer electronics. These products are integral to daily life, with boundaries between categories increasingly blurred due to advancements in intelligent chips, IoT, big data, and 5G. Traditional appliances are also converging into the 3C ecosystem, forming interconnected smart home networks. This article examines the mold manufacturing characteristics and production processes for 3C products, with a focus on mold development, fabrication techniques, and assembly workflows, emphasizing practical, technical, and systematic approaches.
Overview of 3C Products
3C products encompass computers (e.g., laptops, tablets), communication devices (e.g., smartphones, routers), and consumer electronics (e.g., smartwatches, home appliances). The demand for high-quality, diverse, and rapidly iterating 3C products has placed significant pressure on mold manufacturing and production processes. Molds must deliver high precision, durability, and short development cycles to meet market expectations. Additionally, the integration of 3D printing into production workflows has enhanced efficiency and flexibility, particularly in プロトタイピング and assembly.
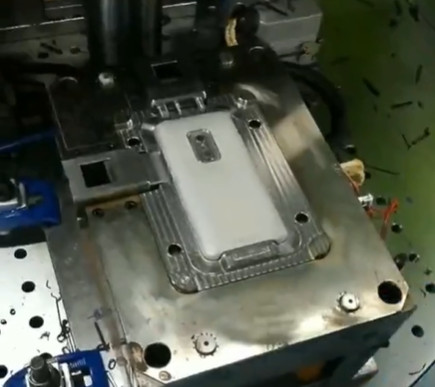
Mold Development for 3C Products
Mold development is a critical phase in 3C product manufacturing, requiring meticulous planning to balance precision, cost, and development time. For example, developing a mold for a robotic vacuum cleaner illustrates the complexity involved. A robotic vacuum typically consists of a main unit and a charging dock, with the main unit further divided into four key modules: the housing, power system, electrical components, and consumables.
- Housing: Includes the outer shell and base plate, defining the product's appearance and structural integrity.
- Power System: Comprises components for mobility, cleaning, and suction, such as motors and brushes.
- Electrical Components: Encompasses sensors, battery packs, wireless communication modules, and intelligent chips for control and connectivity.
- Consumables: Replaceable parts like side brushes, main brushes, dust filters, water tank filters, and mopping cloths.
To support rapid product iteration and cost reduction, mold development emphasizes modularity. The housing module often requires new molds for each iteration due to aesthetic and structural updates. The power system may involve motor adjustments, which can be accommodated by modifying existing housing molds. Electrical components, such as control units, are designed for interchangeability to minimize mold changes. Consumables are standardized to reduce the need for new molds, thereby lowering costs and simplifying inventory management.
This modular approach reduces the number of molds required, shortens development cycles, and enhances production efficiency. For instance, by designing universal controller housings and minimizing changes to consumable molds, manufacturers can reduce part variety, streamline assembly, and lower inventory costs. A typical robotic vacuum may require 10–15 molds, with housing molds accounting for 60% of the total due to their complexity and frequent updates.
Mold Fabrication Techniques
Mold fabrication for 3C products demands a combination of advanced and conventional machining techniques to meet precision and cost requirements. The choice of technique depends on the component’s function, surface finish, and structural complexity.
Component Type | Recommended Technique | メリット |
---|---|---|
Streamlined Housing | High-Speed Machining Center | High precision for curved surfaces, reduced polishing time |
Complex Surfaces (e.g., Reflective Lamp Covers) | Mirror EDM (Electrical Discharge Machining) | Near-final surface roughness, minimal post-processing |
Small-Diameter Internal Threads | Slow Wire EDM or Gear/Chain-Driven Demolding | Accurate thread formation, simplified demolding |
Standard Components | CNC Machining, Wire Cutting | Cost-effective for less complex parts |
For streamlined housings, high-speed machining centers achieve surface precision within ±0.01 mm, reducing polishing time by up to 30%. For complex surfaces, such as diamond-patterned lamp covers, mirror EDM delivers surface roughness values (Ra) as low as 0.2 µm, minimizing post-processing. Small-diameter internal threads, common in 3C products, can be fabricated using slow wire EDM for precision or gear/chain-driven demolding for efficiency. For standard components, conventional CNC加工 and wire cutting remain cost-effective, with tolerances typically within ±0.05 mm.
A practical example is the mold for an electrical control module housing, where cable exit holes are spaced less than 1 mm apart, creating a high-risk area for damage during injection molding. To address this, the mold incorporates modular inserts for the exit holes, machined using wire cutting to a precision of ±0.1 mm. These inserts can be replaced in under 10 minutes during production, minimizing downtime. The mold cavity’s mating surfaces are machined using CNC to match the insert’s dimensions, ensuring seamless integration. This approach reduces mold maintenance costs by up to 25% and allows for rapid adaptation to design changes without developing new molds.
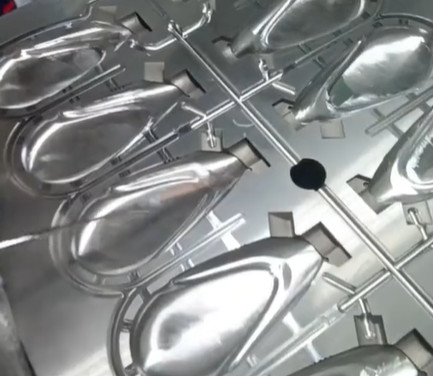
Assembly Workflow Optimization
The assembly process for 3C products is critical to achieving high efficiency and quality, particularly under rapid iteration cycles. Modular fixtures play a pivotal role in streamlining assembly, especially for products like remote controls, which require precise alignment of buttons, circuit boards, and housings.
For high-volume, stable products, fixtures are fabricated using conventional machining to ensure durability and precision. For new or iterating products, 3D printing enables rapid fixture production, reducing lead times from weeks to days. 3D-printed fixtures can be made from materials like PLA (Polylactic Acid) for rigid components or TPU (Thermoplastic Polyurethane) for elastic modules, which provide a 0.1–0.2 mm interference fit for secure component holding without additional materials.
A notable application is in the assembly of remote controls, where fixtures are designed in modular groups. Stable designs use fixed modules, while new designs leverage 3D-printed modules tailored to specific shapes. This approach reduces fixture development costs by 20–30% and shortens production line changeover times by up to 40%. Additionally, 3D printing enables conformal cooling channels or airflow paths in fixtures, replacing traditional suction cups and improving component stability during assembly by 15%.
During trial assembly, 3D-printed fixtures allow for rapid iteration. For example, if a new remote control design requires adjusted button spacing, a revised TPU fixture can be printed overnight, compared to a week for traditional machining. This flexibility ensures that assembly lines remain agile, supporting the fast-paced demands of 3C product development.
Role of 3D Printing in Production
3D printing has transformed 3C product manufacturing by enabling rapid prototyping, fixture production, and even direct component fabrication. Its key advantages include:
- Speed: Prototypes and fixtures can be produced in hours, compared to days or weeks for traditional methods.
- Material Versatility: Supports rigid plastics (PLA, ABS) and elastic materials (TPU), catering to diverse assembly needs.
- コスト効率: Reduces tooling costs for low-volume or iterative designs by up to 50%.
- カスタマイズ: Enables conformal designs, such as airflow channels, improving fixture performance.
For instance, in robotic vacuum production, 3D printing is used to create prototype molds for initial testing, reducing development time by 2–3 weeks. In assembly, 3D-printed TPU fixtures with elastic properties eliminate the need for secondary padding, simplifying workflows and reducing material costs by 10–15%. The technology also supports rapid iteration of consumable components, such as dust filters, by enabling quick mold adjustments without significant retooling.
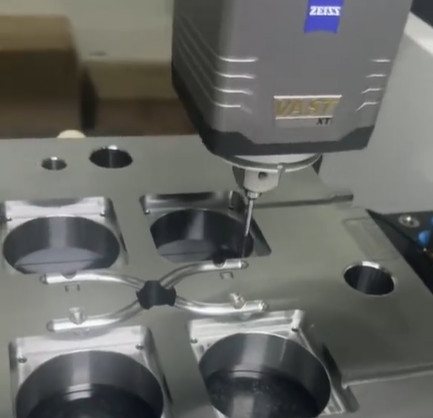
Practical Considerations in Mold and Production Design
Effective mold and production design for 3C products requires a systematic approach to balance performance, cost, and scalability. Key considerations include:
- Modular Design: Standardizing components and inserts reduces mold development costs and supports rapid iteration.
- Material Selection: Choosing appropriate mold materials (e.g., P20 steel for durability, aluminum for prototypes) impacts cost and lifespan.
- Process Optimization: Combining advanced techniques (e.g., mirror EDM) with conventional methods (e.g., CNC) ensures cost-effectiveness.
- Maintenance Planning: Designing molds with replaceable inserts minimizes downtime and maintenance costs.
For example, a mold designed with P20 steel can withstand 500,000–1,000,000 injection cycles, compared to 50,000–100,000 for aluminum, making it suitable for high-volume 3C products. By incorporating replaceable inserts for high-wear areas, manufacturers can extend mold life by 20–30% while maintaining production continuity.
結論
Mold manufacturing and production processes for 3C products demand precision, efficiency, and adaptability to meet the industry’s rapid iteration cycles. By leveraging modular mold designs, advanced fabrication techniques, and 3D printing, manufacturers can reduce costs, shorten development times, and enhance production flexibility. Assembly workflows benefit from modular fixtures and 3D-printed components, enabling seamless adaptation to new designs. These strategies, grounded in technical expertise and systematic planning, ensure that 3C products meet the high standards of quality and diversity required in today’s market.