Precision machining is a cornerstone of modern manufacturing, enabling the production of high-accuracy components with tight tolerances for industries such as aerospace, automotive, medical, and electronics. This process involves removing material from a workpiece to create parts that meet exact specifications. Central to precision machining is Computer Numerical Control (CNC), which automates tools like lathes and milling machines to achieve consistent, repeatable results. This article provides a comprehensive exploration of precision machining, focusing on CNC technology, lathes, and milling processes, with detailed parameters and practical insights to demonstrate expertise and reliability.
Understanding Precision Machining
Precision machining refers to subtractive manufacturing processes that shape raw materials into finished parts with exceptional accuracy. Unlike traditional manual machining, precision machining relies on advanced computer-controlled systems to execute complex designs with minimal human intervention. The process is critical for producing components with tolerances as tight as ±0.0025 mm, ensuring functionality and compatibility in high-stakes applications.
The primary tools in precision machining include CNC lathes, milling machines, grinders, and electrical discharge machines (EDM). Each tool serves specific purposes, from crafting cylindrical parts to creating intricate geometries. The integration of Computer-Aided Design (CAD) and Computer-Aided Manufacturing (CAM) software enhances precision by translating 3D models into machine-readable instructions, known as G-code and M-code, which dictate tool movements, speeds, and cutting depths.
Key industries rely on precision machining for components such as engine parts, surgical instruments, electronic housings, and aerospace prototypes. The process supports a wide range of materials, including metals (e.g., aluminum, steel, titanium) and plastics (e.g., ABS, polycarbonate), ensuring versatility across applications.

CNC Technology in Precision Machining
Computer Numerical Control (CNC) is the backbone of precision machining, automating the control of machine tools through pre-programmed software. CNC systems interpret CAD designs and convert them into precise instructions for cutting, shaping, and finishing workpieces. This automation ensures repeatability, reduces human error, and enables scalability for high-volume production.
CNC machines operate along multiple axes, typically ranging from 2 to 5 axes, depending on the complexity of the part. A 3-axis CNC machine moves along the X, Y, and Z axes, while 4- and 5-axis machines add rotational axes (A and B) for intricate geometries. The use of high-pressure coolant systems prevents chip buildup, maintaining precision during operations.
Key CNC Parameters:
パラメータ | 説明 | 代表値 |
---|---|---|
主軸回転数 | Rotational speed of the cutting tool or workpiece | 1,000–24,000 RPM |
フィード・レート | Speed at which the tool advances into the material | 0.01–0.5 mm/rev |
切り込み | Amount of material removed per pass | 0.1–5 mm |
寛容 | Allowable deviation from specified dimensions | ±0.0025–0.01 mm |
CNC systems also incorporate advanced features like automatic tool changers, tool magazines, and coolant systems to enhance efficiency. For example, a 5-axis CNC machine can produce complex parts in a single setup, reducing production time and improving accuracy.
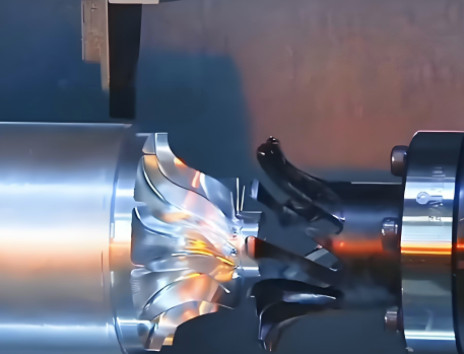
CNC Lathes: Precision Turning Operations
CNC lathes are specialized machines designed for turning operations, where a workpiece rotates against a stationary cutting tool to produce cylindrical or axially symmetrical parts. These machines are ideal for creating components like bolts, shafts, screws, and bushings. The workpiece is secured in a chuck or between centers, and the cutting tool moves linearly along the X and Z axes to shape the material.
Types of CNC Lathes:
- 2-Axis Lathes: Basic models for simple cylindrical parts, moving along X (radial) and Z (axial) axes.
- Multi-Axis Lathes: Incorporate additional axes (e.g., Y-axis or C-axis) for complex features like off-center drilling or milling.
- Swiss-Type Lathes: Feature a sliding headstock and guide bushing for enhanced support, ideal for long, slender parts with tolerances as tight as ±0.005 mm.
Key Lathe Parameters:
パラメータ | 説明 | 代表値 |
---|---|---|
Swing Over Bed | Maximum diameter of the workpiece | 200–1,000 mm |
Distance Between Centers | Maximum length of the workpiece | 500–3,000 mm |
切断速度 | Speed of the workpiece surface relative to the tool | 50–500 m/min |
工具材料 | Material of the cutting tool | Carbide, High-Speed Steel (HSS) |
CNC lathes excel in producing features like threads, grooves, tapers, and bores. For instance, a typical operation might involve turning a steel rod to a diameter of 50 mm with a tolerance of ±0.01 mm, using a carbide insert at a spindle speed of 1,500 RPM and a feed rate of 0.2 mm/rev. Swiss-type lathes are particularly effective for high-precision, small-diameter parts, such as medical implants, due to their ability to minimize vibration and deflection.
CNC Milling: Versatile Material Removal
CNC milling involves using a rotating cutting tool to remove material from a stationary workpiece, creating complex shapes, slots, and surfaces. Milling machines are versatile, capable of producing flat surfaces, contours, and intricate geometries. They are widely used for parts like brackets, housings, and molds in industries such as automotive and aerospace.
Types of CNC Milling Machines:
- Vertical Machining Centers (VMCs): Feature a vertically oriented spindle, suitable for flat workpieces and die-sinking applications.
- Horizontal Machining Centers (HMCs): Have a horizontally oriented spindle, ideal for heavy workpieces requiring machining on multiple sides.
- 5-Axis Milling Machines: Allow simultaneous movement along five axes, enabling complex geometries in a single setup.
Milling Process Parameters:
Milling operations are governed by parameters that influence surface finish, tool life, and production efficiency. For example, milling an aluminum block might involve a 4-flute end mill at 12,000 RPM, a feed rate of 0.1 mm/tooth, and a depth of cut of 2 mm. The choice of tool material (e.g., carbide for harder metals) and coolant type (e.g., water-based emulsion) significantly affects performance.
Milling operations include face milling (creating flat surfaces), peripheral milling (shaping edges), and slot milling (cutting grooves). Advanced 5-axis milling machines can produce complex parts, such as タービンブレード, with tolerances of ±0.005 mm in a single setup, reducing the need for multiple operations.
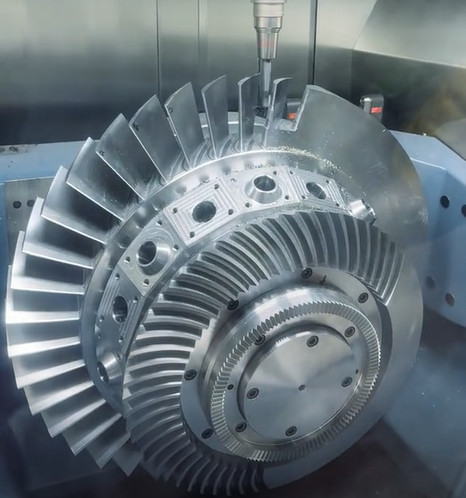
Materials in Precision Machining
Precision machining supports a wide range of materials, each requiring specific tools and parameters to achieve optimal results. Common materials include:
- 金属: Aluminum (tensile strength: 90–300 MPa), stainless steel (tensile strength: 500–1,000 MPa), titanium (tensile strength: 900–1,600 MPa), and brass (tensile strength: 200–500 MPa).
- プラスチック: ABS (tensile strength: 40–60 MPa), polycarbonate (tensile strength: 55–75 MPa), and PEEK (tensile strength: 90–100 MPa).
- コンポジット: Carbon fiber-reinforced polymers (tensile strength: 500–2,000 MPa) and fiberglass (tensile strength: 100–300 MPa).
Material properties, such as hardness and thermal conductivity, dictate machining parameters. For example, titanium requires lower cutting speeds (30–60 m/min) and high-pressure coolant to manage heat, while aluminum allows higher speeds (200–400 m/min) due to its softer nature.
Applications of Precision Machining
Precision machining is integral to industries requiring high-accuracy components. Key applications include:
- 航空宇宙 Turbine blades, landing gear components, and structural parts with tolerances of ±0.01 mm.
- 自動車: Engine blocks, transmission gears, and suspension components requiring durability and precision.
- メディカルだ: Surgical instruments, implants, and diagnostic equipment with biocompatible materials like titanium.
- Electronics: Housings, connectors, and heat sinks with intricate designs and tight tolerances.
For example, a CNC lathe might produce a titanium medical implant with a diameter of 10 mm and a tolerance of ±0.005 mm, while a 5-axis milling machine could create an aerospace bracket with complex contours in a single setup.
Post-Processing and Finishing
Post-processing is often required to achieve the desired surface finish and dimensional accuracy. Common techniques include:
- 研磨: Uses abrasive wheels to achieve surface roughness as low as Ra 0.2 µm.
- Deburring: Removes burrs and sharp edges to improve safety and aesthetics.
- 研磨: Enhances surface quality for low-friction applications, such as hydraulic rods.
- Electroplating: Applies a metal coating to improve corrosion resistance and durability.
For instance, a machined steel component might undergo grinding to achieve a surface finish of Ra 0.4 µm, followed by electroplating with nickel to enhance corrosion resistance.
Limitations and Considerations
While precision machining offers unmatched accuracy, certain limitations must be addressed to ensure optimal outcomes. Workpiece size is constrained by the machine’s work envelope, typically limited to 1,000 mm x 1,000 mm x 500 mm for milling machines and 1,000 mm in length for lathes. Material selection also poses challenges, as harder materials like titanium require specialized tools and slower cutting speeds, increasing production time. Additionally, improper tool selection or machine setup can lead to issues like tool chatter, poor surface finish, or dimensional inaccuracies.
To mitigate these, machinists must carefully select tools, optimize cutting parameters, and maintain machines regularly. For example, using a dull tool on a stainless steel workpiece can cause chatter, leading to surface roughness exceeding Ra 1.6 µm, which may require additional finishing.
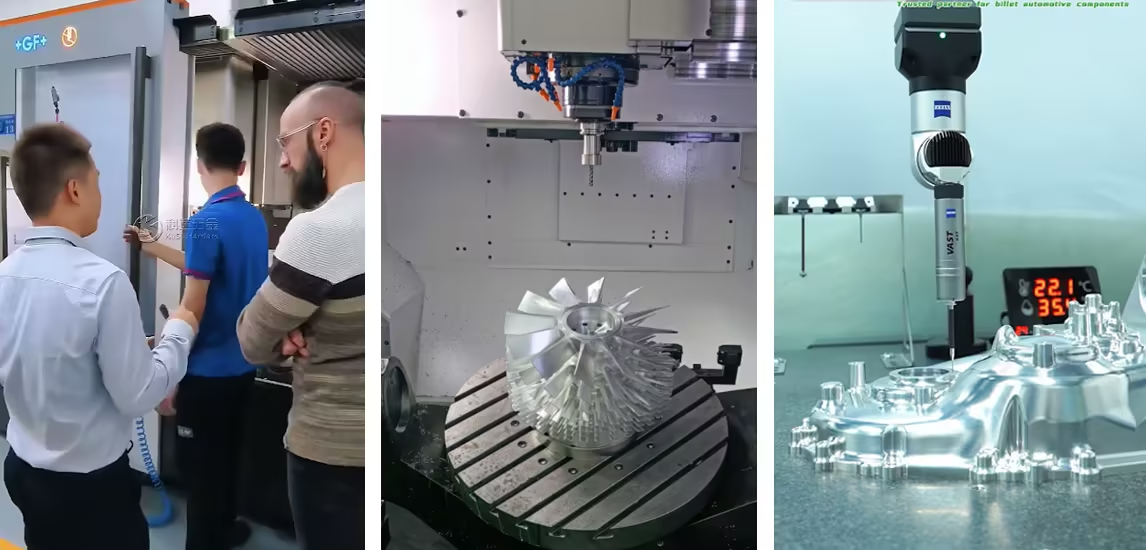
Kesu Precision Machining: Where Accuracy Meets Innovation
Kesu Precision Machining delivers industry-leading precision components with tolerances as tight as ±0.0025 mm, leveraging advanced CNC technology—including 5-axis milling, Swiss-type lathes, and automated turning systems—to craft high-accuracy parts for aerospace, medical, automotive, and electronics sectors. Our expertise spans a wide range of materials, from titanium and stainless steel to high-performance plastics, ensuring flawless execution of complex geometries, whether for prototypes or high-volume production, backed by cutting-edge CAD/CAM integration and a commitment to uncompromising quality that turns your most demanding designs into reality.
結論
Precision machining, powered by CNC technology, lathes, and milling processes, is a vital manufacturing method for producing high-accuracy components. By leveraging advanced automation, precise parameters, and versatile materials, it meets the stringent demands of industries like aerospace, automotive, and medical. Understanding the capabilities and limitations of CNC lathes and milling machines, along with proper material and parameter selection, ensures consistent, high-quality results. This detailed exploration underscores the technical expertise and systematic approach required for successful precision machining.