Precision machining and traditional machining are two fundamental approaches in manufacturing, each with distinct characteristics that make them suitable for specific applications. Precision machining leverages advanced technologies to achieve high accuracy and tight tolerances, while traditional machining relies on conventional tools and methods. This article provides a comprehensive comparison of these two methods, focusing on accuracy, efficiency, cost, and applicable fields, alongside a detailed explanation of the precision machining process flow.
精度
Accuracy is the hallmark of precision machining, distinguishing it significantly from traditional methods. Precision machining employs computer numerical control (CNC) machines, laser cutting, and electrical discharge machining (EDM) to achieve tolerances as tight as ±0.001 mm (1 micron) or even at the nanometer level for specialized applications. For instance, in the medical industry, components such as surgical implants require diameters as small as 0.1 mm with surface finishes of Ra 0.1 μm to ensure biocompatibility and functionality.
Traditional machining, on the other hand, typically uses manual or semi-automatic lathes, milling machines, and grinders. These methods are limited by factors such as tool wear, operator skill, and machine rigidity, resulting in tolerances ranging from ±0.01 mm to ±0.1 mm. While sufficient for many applications, these tolerances cannot meet the stringent requirements of industries like aerospace or electronics, where precision machining excels.
The difference in accuracy stems from the technology used. Precision machining relies on real-time feedback systems, such as laser interferometry and digital encoders, to monitor and adjust the machining process dynamically. Traditional machining lacks such sophisticated control, making it prone to cumulative errors, especially in complex geometries.
効率性
Efficiency in manufacturing is measured by production speed, setup time, and the ability to handle complex parts. Precision machining, while highly accurate, often involves longer processing times due to its intricate setup and multi-step processes. For example, CNC加工 requires programming, tool path optimization, and sometimes multiple setups to achieve the desired geometry. A single precision part, such as a turbine blade for aerospace, may take several hours to machine due to the need for slow, precise cuts to maintain tolerances of ±0.005 mm.
Traditional machining, by contrast, is generally faster for simpler parts. Manual lathes or milling machines can produce components like basic shafts or brackets in minutes, with minimal setup time. However, this efficiency diminishes for complex parts requiring multiple operations, as traditional methods often necessitate manual repositioning or tool changes, increasing the risk of errors.
In high-volume production, precision machining can improve efficiency through automation. CNC machines can operate continuously with minimal human intervention, using automated tool changers and robotic loading systems. Traditional machining, while quicker for low-volume or simple tasks, struggles to match this level of automation, making it less efficient for large-scale production of intricate components.
コスト
Cost is a critical factor in choosing between precision and traditional machining. Precision machining incurs higher costs due to several factors: advanced equipment, specialized tooling, and skilled labor. A high-end CNC machine, for example, can cost upwards of $100,000, with additional expenses for maintenance, software, and high-precision tools like diamond-coated cutters. The labor cost is also significant, as operators require training in CAD/CAM software and CNC programming.
Traditional machining is generally more cost-effective for simpler applications. Basic lathes or milling machines cost between $10,000 and $50,000, and their operation requires less specialized training. Tooling costs are also lower, as traditional methods use standard tools like high-speed steel cutters, which are less expensive than the carbide or ceramic tools used in precision machining.
Material waste also affects cost. Precision machining minimizes waste through optimized tool paths and precise material removal, which is critical for expensive materials like titanium or Inconel used in aerospace. Traditional machining, however, may result in higher material waste due to less precise cutting, increasing costs for high-value materials. Despite its higher upfront costs, precision machining can be cost-effective in industries like medical or aerospace, where quality and reliability outweigh initial expenses.
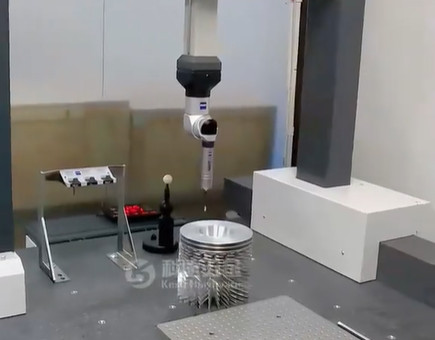
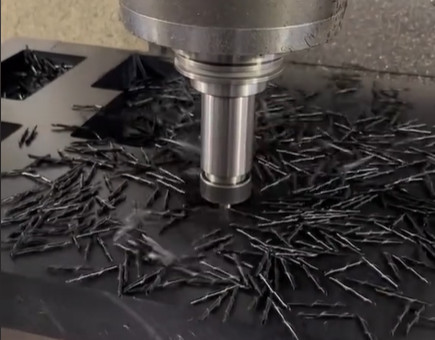
Applicable Fields
The choice between precision and traditional machining depends on the application’s requirements. Precision machining is indispensable in industries demanding high accuracy and complex geometries, such as:
- メディカルだ: Manufacturing of implants, surgical tools, and diagnostic equipment with tolerances of ±0.002 mm and surface finishes of Ra 0.05 μm.
- 航空宇宙 Production of タービンブレード, engine components, and structural parts requiring tolerances of ±0.01 mm and high fatigue resistance.
- Electronics: Fabrication of microchips, connectors, and circuit board components with features as small as 0.01 mm.
- 自動車: High-performance engine parts and transmission components with tight tolerances for efficiency and durability.
Traditional machining is better suited for applications with less stringent requirements, such as:
- Furniture Manufacturing: Production of structural components like brackets or frames, where tolerances of ±0.1 mm are acceptable.
- General Machinery: Fabrication of gears, shafts, or housings for industrial equipment with moderate precision needs.
- 建設: Manufacturing of fittings or supports where functionality trumps precision.
The choice of method depends on the balance between precision, production volume, and cost constraints specific to the industry.
Precision Machining Process Flow
The precision machining process is a systematic sequence of steps designed to produce high-accuracy components. Below is a detailed breakdown of the complete process flow:
- Design and CAD Modeling: The process begins with creating a detailed 3D model using CAD software (e.g., SolidWorks, AutoCAD). The model specifies dimensions, tolerances (e.g., ±0.001 mm), and surface finish requirements (e.g., Ra 0.1 μm).
- CAM Programming: The CAD model is imported into CAM software (e.g., Mastercam, Fusion 360) to generate tool paths. Parameters like cutting speed (e.g., 500–2000 RPM), feed rate (e.g., 0.05–0.2 mm/rev), and depth of cut (e.g., 0.1–1 mm) are optimized.
- Material Selection: Materials like stainless steel, titanium, or engineering plastics are chosen based on the part’s requirements. For example, aerospace parts may use Ti-6Al-4V for its strength-to-weight ratio.
- Machine Setup: The CNC machine is prepared, including mounting the workpiece, installing tools (e.g., carbide end mills), and calibrating the machine using probes or laser systems.
- Machining Operations: Operations like milling, turning, drilling, or EDM are performed. For instance, a 5-axis CNC machine may be used for complex geometries, achieving tolerances of ±0.005 mm.
- In-Process Inspection: Real-time monitoring using coordinate measuring machines (CMM) or laser scanners ensures accuracy. Deviations are corrected by adjusting tool paths or parameters.
- Finishing Processes: Surface treatments like grinding, polishing, or anodizing achieve required surface finishes (e.g., Ra 0.05 μm for medical implants).
- Final Inspection and Quality Control: The finished part undergoes rigorous inspection using CMM, profilometers, or X-ray systems to verify dimensions, tolerances, and material properties.
- Packaging and Delivery: Parts are cleaned, packaged to prevent damage, and shipped to the client with documentation like inspection reports.
This structured process ensures consistency and reliability, critical for high-stakes applications.
Comparison Summary
The following table summarizes the key differences between precision and traditional machining:
アスペクト | 精密機械加工 | Traditional Machining |
---|---|---|
精度 | ±0.001 mm to nanometer-level tolerances | ±0.01 mm to ±0.1 mm |
効率性 | Slower due to complex setups; efficient for automation | Faster for simple parts; less efficient for complex tasks |
コスト | Higher due to equipment, tooling, and labor | Lower for simple applications |
アプリケーション | Medical, aerospace, electronics, automotive | Furniture, general machinery, construction |
結論
Precision machining and traditional machining serve distinct purposes in manufacturing. Precision machining excels in applications requiring 高精度, complex geometries, and superior surface finishes, albeit at higher costs and longer production times. Traditional machining offers a cost-effective and efficient solution for simpler parts with looser tolerances. Understanding the requirements of the specific application—whether it’s the tight tolerances of a medical implant or the straightforward geometry of a furniture bracket—guides the choice of method. By leveraging the strengths of each approach, manufacturers can optimize quality, cost, and efficiency to meet diverse industry needs.