Ultra-precision grinding achieves exceptional dimensional accuracy of 0.1 μm and surface roughness (Ra) values between 0.008 and 0.025 μm. This process is critical for soft materials used in industries requiring high precision and superior surface quality, such as optics, aerospace, and medical devices. Soft materials, characterized by high ductility, low hardness, high thermal expansion, and strong plasticity, present unique challenges during ultra-precision grinding. Common issues include grinding wheel clogging, surface scratches, high surface roughness, material deformation, and low machining efficiency. Through extensive testing and analysis, this article provides a systematic approach to address these challenges, focusing on equipment selection, grinding wheel specifications, coolant systems, dressing techniques, and optimized grinding parameters to enhance efficiency and surface quality.
Challenges in Ultra-Precision Grinding of Soft Materials
Soft materials pose distinct difficulties in ultra-precision grinding due to their material properties. The following sections detail the primary issues encountered during the process, based on practical observations and analysis.
Grinding Wheel Clogging
The high ductility of soft materials results in sticky chips that adhere to the grinding wheel, causing clogging. This reduces the wheel’s cutting efficiency, necessitating frequent dressing and tool setting, which significantly lowers productivity and increases downtime.
Surface Scratches and High Roughness
The “self-sharpening” phenomenon, where abrasive grains fracture or detach from the grinding wheel, often leads to surface scratches. This is particularly problematic for coated materials, where the coating may peel off. Additionally, improper wheel selection, inadequate coolant application, or poorly dressed wheels can result in high surface roughness values, failing to meet stringent quality requirements.
Material Deformation
Due to their low hardness and high ductility, soft materials are prone to deformation under grinding forces. This complicates achieving tight dimensional tolerances, especially in applications requiring sub-micron accuracy.
Low Machining Efficiency
Low machining efficiency arises from several factors: frequent wheel dressing due to clogging, limited machine tool stability, and suboptimal grinding parameters such as wheel speed, feed rate, and depth of cut. These issues collectively reduce throughput and increase production costs, impacting delivery schedules.
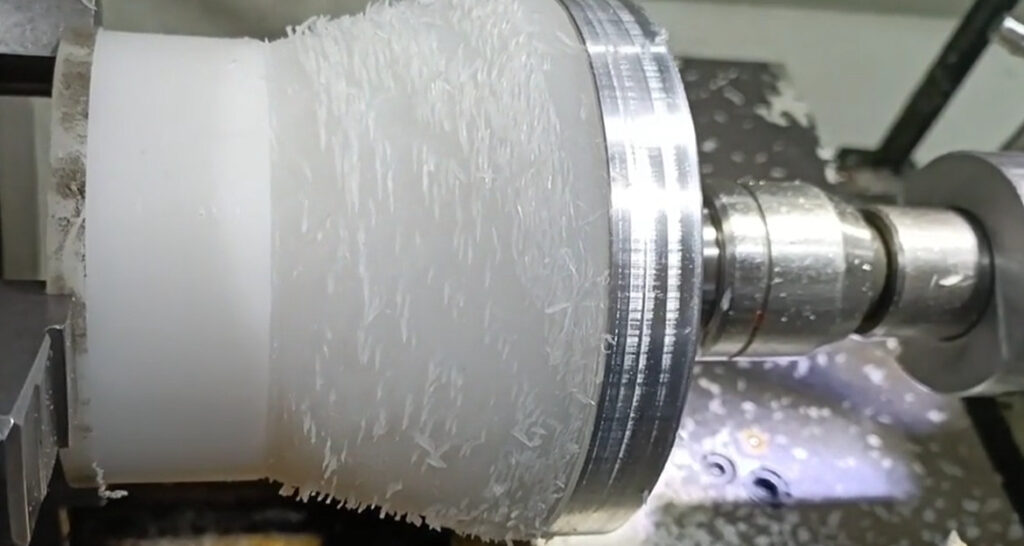
Solutions for Ultra-Precision Grinding of Soft Materials
To overcome the challenges of ultra-precision grinding, a systematic approach is required, addressing equipment, grinding wheels, coolants, dressing techniques, and process parameters. The following solutions are derived from rigorous testing and practical experience, ensuring high efficiency and surface quality.
Selection of Grinding Equipment
The choice of grinding machine is foundational to successful ultra-precision grinding of soft materials. Key requirements include:
- High Rigidity: The machine’s spindle unit must exhibit excellent rigidity to minimize vibrations, ensuring consistent wheel-workpiece contact and precise material removal.
- Sub-Micron Precision: A feed system with a resolution of ≤0.002 mm per increment is essential for achieving the required dimensional accuracy.
- Thermal Stability: Effective heat dissipation in the spindle and machine structure prevents thermal deformation, which is critical for soft materials with high thermal expansion coefficients.
- Low-Speed Stability: The machine must avoid “crawling” at low feed rates to ensure smooth wheel dressing and consistent surface quality, as crawling can introduce surface irregularities.
Selecting a machine with these attributes ensures stable operation, reduces errors, and supports the production of high-quality surfaces.
Grinding Coolant Selection
Effective coolant application is critical for managing heat, reducing friction, and preventing wheel clogging. The following guidelines ensure optimal coolant performance:
- Pressure and Filtration: Maintain sufficient coolant pressure to flush away chips and abrasive debris. Use paper filtration or combined magnetic and paper filtration to keep the coolant clean, preventing contamination that could cause surface scratches.
- Nozzle Angle: Position coolant nozzles at an angle of ≤20° to the grinding zone to ensure thorough flushing, reducing thermal damage and enhancing lubrication.
- Coolant Type: Use chemical synthetic coolants with low concentration to prevent surface corrosion while providing adequate lubrication and cooling. Low-concentration coolants also minimize wheel clogging by reducing chip adhesion.
Proper coolant management improves machining efficiency, extends wheel life, and enhances surface quality by maintaining a clean grinding interface.
Grinding Wheel Selection
The grinding wheel is a critical component in ultra-precision grinding. For soft materials, the wheel must balance cutting efficiency with surface quality. Extensive testing has identified a wheel with the specification 54A320G8V as optimal. Its key features include:
- Ceramic Bond: Ceramic bonds outperform corundum bonds due to their micro-fracturing behavior, which ensures stable grinding performance and good shape retention. This reduces surface scratches and maintains consistent quality.
- High Porosity (Rating 8): A large-pore structure (porosity rating 8) enhances chip clearance, increases material removal rates, and allows more coolant to reach the grinding zone, reducing friction and surface damage.
- Fine Grain Size (320 Grit): Ultra-fine 320-grit abrasives minimize grain fracture and detachment, reducing the self-sharpening effect and preventing surface scratches.
- High Abrasive Hardness and Strong Bonding: These properties ensure the wheel maintains micro-cutting edges after dressing, achieving low surface roughness values critical for ultra-precision applications.
This wheel configuration delivers stable performance and high surface quality, addressing the challenges of soft material grinding.
Diamond Dresser Selection and Wheel Dressing
Effective wheel dressing is essential for maintaining the wheel’s geometry and surface quality. The following guidelines ensure optimal dressing:
- Dressing Parameters: Use a dressing feed of 0.001–0.003 mm and a transverse feed rate of 50–100 m/min. If surface roughness is still suboptimal, further reduce the transverse feed rate to enhance wheel smoothness.
- Dresser Quality: Select high-quality, wear-resistant single-point natural diamond dressers to ensure sharp and consistent dressing, minimizing wheel surface irregularities.
- Dresser Installation:
- Clamping Length: Minimize the dresser’s overhang, following the formula: maximum overhang (b) = 2 × contact length (a). This reduces vibrations and improves dressing precision.
- Dressing Angle: Set the dresser at a 10°–15° angle relative to the wheel’s horizontal axis. Rotate the dresser 90° periodically to prevent tip dulling, ensuring consistent dressing performance.
- Resistance Axis Angle: Limit the angle between the dresser and the wheel’s resistance axis to ≤15° to optimize dressing efficiency and minimize wheel damage.
These practices produce a smooth, well-dressed wheel surface, reducing the risk of scratches and improving surface roughness.
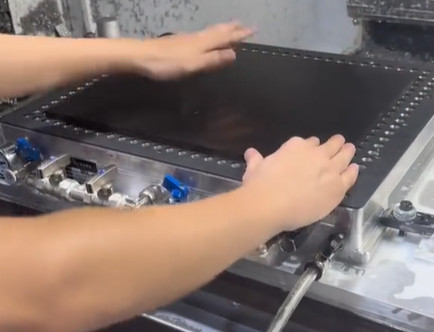
Optimized Grinding Parameters
Grinding parameters must be tailored to the material and desired outcome. Ultra-precision grinding of soft materials typically involves two stages: rough grinding and finish grinding. The parameters for each stage are outlined below.
パラメータ | Value |
---|---|
Wheel Speed (m/s) | 30–40 |
Workpiece Speed (m/min) | 10–20 |
切り込み (mm) | 0.005–0.01 |
Longitudinal Feed Rate (mm/min) | 1000–1500 |
Rough grinding focuses on efficient material removal while maintaining acceptable surface quality and dimensional accuracy to prepare for finish grinding.
パラメータ | Value |
---|---|
Wheel Speed (m/s) | 25–35 |
Workpiece Speed (m/min) | 5-10 |
切り込み (mm) | 0.001–0.003 |
Longitudinal Feed Rate (mm/min) | 500–800 |
Finish grinding prioritizes surface quality and dimensional precision, using smaller depths of cut and slower feed rates to achieve the required Ra values and tolerances.
結論
Ultra-precision grinding of soft materials requires a comprehensive approach, integrating high-rigidity equipment, carefully selected grinding wheels, effective coolant systems, precise dressing techniques, and optimized grinding parameters. By addressing challenges such as wheel clogging, surface scratches, material deformation, and low efficiency, the solutions outlined in this article—based on extensive testing and practical experience—enable manufacturers to achieve sub-micron accuracy and superior surface quality. Implementing these strategies enhances machining efficiency, improves product quality, and ensures reliable delivery of high-precision components.