Ultra-precision machining, commonly referred to as superfinishing, is a surface finishing process that enhances workpiece surface quality by significantly reducing surface roughness, eliminating grinding defects, and extending component service life. This article provides a comprehensive, technical, and systematic examination of ultra-precision machining, detailing its principles, methods, tool selection, process parameters, and applications across various industries. The content is structured to deliver reliable and professional insights, focusing on practical implementation and effectiveness.
Introduction to Ultra-precision Machining
Ultra-precision machining is a surface finishing technique designed to refine and polish workpiece surfaces to achieve exceptional smoothness and precision. By employing fine abrasive tools, such as superfinishing stones, under controlled conditions, it reduces surface roughness from typical grinding values of Ra 0.2–0.4 μm to as low as Ra 0.006–0.05 μm. This process eliminates microscopic defects and subsurface damage caused by prior machining, resulting in improved durability, reduced wear, and enhanced performance of components. Ultra-precision machining is widely applied in industries requiring high-precision components, such as automotive, aerospace, bearings, and precision tooling.
The process is valued for its ability to improve surface texture, forming cross-hatched patterns that retain lubricants effectively, reduce friction, and enhance the operational life of parts by up to five times. Its efficiency, simplicity, and compatibility with automation make it a preferred choice for finishing critical components like crankshafts, camshafts, bearings, and precision gauges.
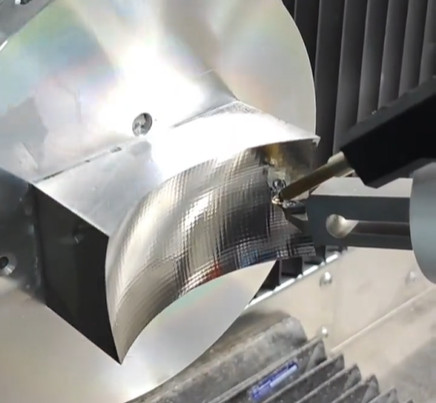
Principles and Characteristics of Ultra-precision Machining
Principles of Ultra-precision Machining
Ultra-precision machining involves the use of fine abrasive stones, typically made of micro-powder abrasives, applied to the workpiece surface under controlled pressure and oscillatory motion. The process removes minute amounts of material, typically less than 0.001 mm, through short-stroke reciprocating motion. The key parameters include:
- Pressure (F): Applied force on the abrasive stone, typically 20–30 MPa/cm².
- Amplitude (A): Oscillation stroke length, ranging from 1–6 mm.
- Workpiece Speed (vc): Rotational or linear speed of the workpiece, varying from 4–30 m/min.
- Feed Rate (vf): Longitudinal or axial feed speed, generally below 7 m/min.
The micro-abrasive action refines the surface without altering dimensional accuracy, producing a smooth, defect-free finish with a cross-hatched texture that enhances lubricant retention.
Characteristics of Ultra-precision Machining
Compared to conventional grinding, ultra-precision machining offers distinct advantages:
- Improved Surface Quality: Reduces surface roughness to Ra 0.006–0.05 μm, extending component life by up to five times.
- Enhanced Performance: Produces smoother operation with reduced noise and vibration in assembled components.
- Minimal Material Removal: Removes less than 0.001 mm, compared to 0.01 mm in grinding, ensuring dimensional stability.
- Superior Surface Texture: Creates a cross-hatched pattern, unlike the linear texture of grinding, improving lubricant retention and reducing wear.
- High Efficiency: Completes in seconds (typically 5–15 seconds), offering significantly higher productivity than mirror grinding.
- Automation Compatibility: Uses simple equipment, easily integrated into automated and standardized production lines.
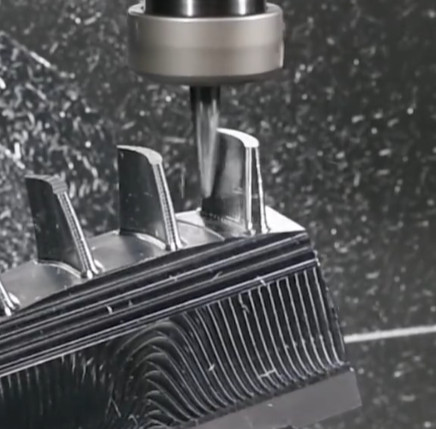
Ultra-precision Machining Methods
Ultra-precision machining methods vary based on workpiece geometry, clamping method, and feed type. Clamping can be centerless or centered, while feed methods include axial, plunge, or circumferential feed. The following sections detail methods for specific geometries.
Machining Cylindrical Surfaces
Ultra-precision machining of external cylindrical surfaces is common for components like crankshafts そして camshafts. Methods include:
- Small-Diameter Cylinders: The workpiece rotates on guide rollers with axial feed, using hyperbolic guide rollers and variable-speed drives for precision.
- Large-Diameter or Stepped Shafts: The workpiece rotates on cylindrical guide rollers without axial feed, suitable for stepped or large-diameter components.
- Long or Conical Cylinders: Uses axial feed with double-center clamping for longer or conical workpieces, ensuring uniform finishing.
Machining Bearing Raceways
Bearing raceways require precise finishing to ensure smooth operation. Methods include:
- Inner Ring Raceways: Plunge-cut method with centered or centerless clamping, using concave-shaped stones to achieve a slightly convex raceway profile (1–4 μm).
- Large Conical Raceways: Axial feed with dwell at both ends, using cam mechanisms to control stone movement for uniform finishing.
- Spherical Roller Raceways: Workpiece rotates with centered or centerless clamping, while the stone oscillates and applies pressure for precise finishing.
Machining Spherical Surfaces
Spherical surfaces, such as those in ball joints, are machined with rotating workpieces and oscillating stones. Narrow grooves on the stone surface facilitate cooling and lubrication, ensuring uniform material removal and surface quality.
Machining Flat Surfaces
Flat surface machining is used for components like precision gauges and rollers. Methods include:
- Rectangular Planes: Processed using plunge or axial feed, depending on workpiece dimensions.
- Circular Planes: The workpiece rotates, and the stone, longer than the workpiece radius, oscillates off-center to cover the entire surface.
- Annular Planes: Uses cylindrical stones with radial oscillation and workpiece rotation for uniform finishing.
- Roller End Faces: Stones are shaped with a narrower outer edge and wider inner edge to compensate for varying cutting speeds across the radius.
Vibration mechanisms, such as pneumatic or mechanical machining heads, achieve frequencies of 1,000–3,000 cycles/min and amplitudes of 1–6 mm, ensuring precise control.
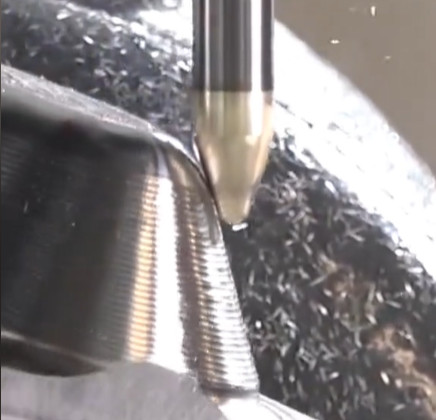
Selection of Abrasive Stones
The choice of abrasive stones is critical for achieving desired surface quality and efficiency. Key considerations include abrasive type, grain size, binder, hardness, and structure.
パラメータ | 説明 | Application |
---|---|---|
Abrasive Type | White Alumina (WA), Green Silicon Carbide (GC), Cubic Silicon Carbide (SC), Cubic Boron Nitride (CBN), Diamond (D), Chromium Oxide | WA for carbon/alloy steels; GC for hard brittle materials; CBN for tough materials; Diamond for high-hardness materials; Chromium Oxide for ultra-low roughness. |
Grain Size | W5–W28 (W20–W28: Ra 0.1–0.2 μm; W5–W10: Ra 0.012–0.025 μm) | Coarser grains (W20–W28) for higher efficiency; finer grains (W5–W10) for ultra-smooth surfaces. |
Binder | Resin or graphite | Ensures abrasive retention and stability. |
硬度 | Softer for hard workpieces/large contact areas; harder for soft workpieces/small contact areas | Optimizes wear resistance and self-sharpening. |
Structure | Porosity 43–49%, organization number 9–12 | Facilitates chip removal and lubricant retention. |
Stones are treated post-sintering with wax, stearic acid, or sulfur to enhance self-sharpening and durability. For overly hard stones, soaking in a 3% potassium hydroxide solution followed by rinsing and boiling in water adjusts hardness to the desired level.
Process Parameters for Ultra-precision Machining
Optimal process parameters ensure efficiency and surface quality. Key parameters include:
パラメータ | Value | 備考 |
---|---|---|
Machining Allowance | 0.003–0.02 mm | 0.01–0.02 mm for Ra 0.8 μm; 0.003–0.01 mm for Ra 0.2–0.4 μm. |
Stone Pressure | 20–30 MPa/cm² | Higher for rough machining; lower for fine machining. |
フィード・レート | <7 m/min; 1.0–1.5 m/min for short parts | Ensures uniform material removal. |
Vibration Frequency | 300–3,000 cycles/min | Adjusts based on surface requirements. |
Vibration Amplitude | 1–6 mm | Controls material removal rate. |
Workpiece Speed | 4–15 m/min (rough); 15–30 m/min (fine) | Optimizes surface finish and efficiency. |
Cutting Fluids in Ultra-precision Machining
Cutting fluids are essential for cooling, lubrication, and chip removal. Preferred fluids have low viscosity to facilitate cleaning and chip expulsion. Common formulations include:
- Standard Mixture: 80% kerosene + 20% machine oil.
- Specialized Fluids: Oils with extreme pressure additives (S, P, Cl) for enhanced lubrication.
- Aluminum/Bearing Steel: 100% kerosene for fine machining.
Fluids must be strictly filtered to maintain cleanliness and prevent abrasive contamination, ensuring consistent surface quality.
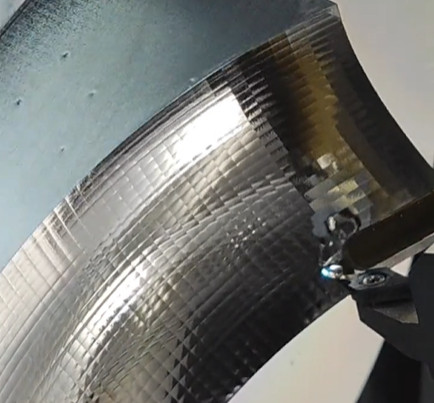
Applications of Ultra-precision Machining
Ultra-precision machining is applied to a wide range of materials and components, including:
- Materials: Steel, cast iron, phosphor bronze, aluminum, glass, granite, silicon, germanium.
- Components: Crankshafts, camshafts, cutting tools, rollers, bearing raceways, precision gauges, electronic instrument parts.
- Geometries: External/internal cylinders, planes, spheres, arcs, and complex profiles.
The process is critical in industries where surface quality directly impacts performance, such as automotive engines, aerospace components, and high-precision bearings.
Practical Considerations
Achieving optimal results in ultra-precision machining requires careful attention to several factors:
- Stone Wear: Regular inspection and dressing of stones are necessary to maintain consistent abrasive performance.
- Parameter Control: Precise control of pressure, feed rate, and vibration is critical to avoid over- or under-finishing.
- Fluid Maintenance: Contaminated cutting fluids can introduce scratches or inclusions, compromising surface quality.
These considerations highlight the importance of process monitoring and maintenance to ensure repeatable, high-quality outcomes.
結論
Ultra-precision machining is a proven and efficient surface finishing method that delivers superior surface quality, extended component life, and enhanced performance. By carefully selecting abrasive stones, optimizing process parameters, and using appropriate cutting fluids, manufacturers can achieve surface roughness values as low as Ra 0.006 μm, eliminate grinding defects, and produce lubricant-retaining surface textures. Its versatility across materials and geometries, combined with its compatibility with automation, makes ultra-precision machining an indispensable process in precision manufacturing.