Wire Electrical Discharge Machining (EDM) equipment, first developed in the Soviet Union in the 1960s, has become a cornerstone of precision manufacturing. Initially, these machines used manual feed with mineral oil as the working fluid, which limited processing speed and practicality due to high insulation properties. Today, wire EDM is widely used globally, with China being one of the earliest adopters for industrial applications. By the 1970s, China developed its first digitally controlled wire EDM machine, leading to the high-speed wire EDM (WEDM-HS) system, while Europe and Japan focused on low-speed wire EDM (WEDM-LS). Wire EDM machines now account for over 60% of electrical discharge machining tools worldwide.
The working principle of wire EDM involves a continuously moving fine metal wire (electrode wire) that generates pulse spark discharges to erode the workpiece, enabling precise cutting of complex and small components, such as cold stamping dies and gear cutters. Its advantages include minimal machining allowance, 高精度, and short production cycles. However, faults during operation can lead to part rejection, making fault analysis and preventive maintenance critical for stable performance.
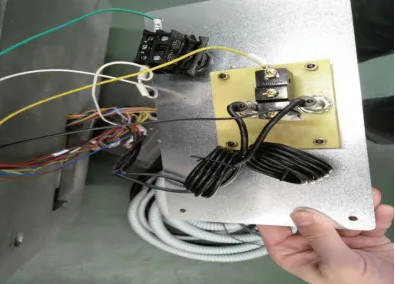
Typical Faults in Wire EDM Equipment
Wire EDM equipment is susceptible to several recurring faults that disrupt operations. Below is a detailed analysis of the most common issues, their causes, and targeted repair strategies based on practical experience.
Frequent Wire Breakage
Frequent wire breakage is one of the most common issues in wire EDM, leading to downtime and potential workpiece damage. The causes vary depending on operational conditions:
- Immediate wire breakage upon contact with the workpiece: This is often due to a short circuit caused by a breakdown in the power tube of the amplifier board, resulting in uncontrolled high-frequency discharge that burns the electrode wire. The solution involves replacing the damaged power tube and inspecting the amplifier board for further faults.
- Wire breakage during commutation: Faulty or contaminated travel switches (e.g., stuck due to oil or debris) or poor contact in the switch can cause wire breakage. Cleaning the switch with a cloth or replacing it resolves the issue.
- Wire breakage during processing: Common causes include poor contact in the conductive block (e.g., due to wear or oil contamination), improper parameter settings (e.g., large pulse width and small pulse interval when cutting thick workpieces), or inadequate working fluid. Approximately 40% of wire breakage incidents are linked to dirty or improper working fluid. Blocked pipelines can also reduce fluid supply, exacerbating the issue. Solutions include cleaning or replacing the conductive block, adjusting pulse parameters (e.g., pulse width of 10–50 µs and pulse interval of 20–100 µs for optimal performance), and ensuring clean, adequate working fluid through regular pipeline maintenance.
No Spark Generation
The absence of sparks prevents machining and is another prevalent fault. The causes and troubleshooting steps include:
- Poor conductive block contact (high probability): This can be diagnosed by short-circuiting the high-frequency line (negative) to the worktable (positive) using a wire. If sparks appear, the conductive block is faulty and should be cleaned or replaced. If no sparks are observed, the issue lies in the front-end circuit.
- Front-end circuit faults (low probability): Potential causes include damaged high-frequency lines, faulty power tube boards, damaged high-frequency resistors, lack of 12V output from the power board, or a defective interface board. Additionally, a faulty ammeter can be tested by short-circuiting it; if the machine resumes normal operation, replace the ammeter.
Low Machining Efficiency
Low machining efficiency, despite normal high-frequency operation and no alarms, is a frequent issue that slows production. Key causes include:
- Poor conductive block contact (60% probability): Scratches or oil contamination on the conductive block reduce efficiency. Cleaning the block with a cloth and lightly sanding it with fine sandpaper (e.g., 1000-grit) restores performance.
- Improper parameter settings: Incorrect pulse width (e.g., exceeding 50 µs for thin materials) or pulse interval (e.g., below 20 µs) settings, or improper tracking speed, can reduce efficiency. Adjust parameters based on material thickness and type (e.g., pulse width of 20–30 µs for steel workpieces 10–50 mm thick).
- Electrode wire vibration: Vibration causes inconsistent cutting, reducing efficiency. Replacing the guide wheel assembly, typically every 500–1000 hours of operation, resolves this issue.
- Machine retraction: Wire EDM requires a small gap (0.01–0.03 mm) between the electrode wire and workpiece for effective machining. Excessive cutting speed or poor chip evacuation can cause short circuits, prompting the system to retract. During retraction, the wire remains energized, affecting the workpiece. Causes include:
- Dirty working fluid or blocked pipelines: These hinder chip evacuation, triggering retraction. Replace working fluid every 100–200 hours and clean pipelines regularly.
- Worn electrode wire: A thinner wire increases resistance, reducing cutting ability and causing retraction. Replace the wire (e.g., molybdenum wire, 0.18–0.25 mm diameter) when wear exceeds 10% of its original diameter.
- Improper parameter settings: Excessive cutting speed or small pulse intervals (e.g., <20 µs) cause retraction. Adjust the feed rate to 0.5–2 mm/min for stable operation.
Insufficient or No Working Fluid
Working fluid is critical for wire EDM, serving three main functions: compressing the discharge channel for precise sparks, cooling the high-temperature discharge area (up to 10,000°C), and removing debris. Insufficient or absent working fluid halts machining. Causes include:
- Blocked pipelines: Clogged valves or nozzles restrict fluid flow. Regular cleaning every 100 hours prevents this.
- Clogged water filter: Replace filters every 200–300 hours to maintain flow.
- Water pump issues: Internal leaks or burnt-out motors reduce fluid delivery. Inspect and repair or replace pumps as needed.
- Low fluid levels: Monitor and replenish fluid reservoirs to maintain 50–100 liters, depending on machine specifications.

Preventive Maintenance Strategies
Preventive maintenance is essential to minimize faults and ensure stable wire EDM operation. The following measures address the unique characteristics of wire EDM and its common faults.
- Conductive block maintenance: Inspect conductive blocks weekly for scratches or oil contamination. Replace blocks with visible wear (e.g., grooves deeper than 0.5 mm) or clean with a cloth and 1000-grit sandpaper to ensure good contact.
- High-frequency line inspection: Check lines monthly for wear, breaks, or contamination. Reconnect or replace damaged cables to maintain consistent electrical performance.
- Guide wheel condition: Inspect guide wheels every 500 hours for scratches or bearing noise. Replace the guide wheel assembly if vibrations or wear are detected.
- Electrode wire condition: Monitor wire diameter and replace when wear exceeds 10% (e.g., from 0.2 mm to 0.18 mm) to prevent resistance buildup.
- Working fluid system maintenance: Inspect water pumps, filters, valves, and pipelines every 100 hours. Replace working fluid every 100–200 hours and clean filters to ensure proper flow (e.g., 5–10 liters/min).
- Mechanical component checks: While some wire EDM components have automatic lubrication, others require manual lubrication every 50–100 hours. Create a maintenance log to track inspections and ensure consistent care.
Maintenance Schedule
Component | Inspection Frequency | Action |
---|---|---|
Conductive Block | Weekly | Clean with cloth and sandpaper or replace if worn |
High-Frequency Line | Monthly | Inspect for damage, reconnect or replace |
Guide Wheel | Every 500 hours | Replace if worn or noisy |
Electrode Wire | Daily | Replace if wear exceeds 10% |
Working Fluid System | Every 100 hours | Inspect pump, filter, valves; replace fluid |
Mechanical Parts | Every 50–100 hours | Manual lubrication and inspection |
結論
Wire EDM equipment is critical for precision machining but is prone to faults such as frequent wire breakage, lack of spark, low efficiency, and insufficient working fluid. These issues, if unaddressed, can lead to costly downtime and workpiece damage. By understanding the root causes—such as poor conductive block contact, improper parameters, or inadequate fluid systems—and implementing targeted repair strategies, technicians can restore machine performance. Equally important is preventive maintenance, which involves regular inspections of conductive blocks, high-frequency lines, guide wheels, electrode wires, and fluid systems, as well as adherence to a structured maintenance schedule. These measures, grounded in practical experience, ensure stable operation, reduce fault rates, and extend equipment lifespan, enabling reliable and efficient production.