Computer Numerical Control (CNC) machining is a cornerstone of modern manufacturing, enabling factories to produce high-precision parts with speed and consistency. To meet the demands of rapid delivery, CNC factories must optimize production efficiency systematically. This article explores proven strategies and technical approaches to enhance throughput, reduce lead times, and maintain quality, drawing on industry experience and practical insights. Below, we detail key methods to achieve these goals, ensuring a professional, systematic, and reliable framework for CNC operations.
Streamlining Workflow with Advanced Planning
Effective production begins with meticulous planning. CNC factories that prioritize rapid delivery implement structured workflows to minimize downtime and ensure seamless operations. Advanced planning involves several critical steps:
- Job Scheduling: Factories use software like ERP (Enterprise Resource Planning) systems to schedule jobs based on machine availability, material readiness, and delivery deadlines. For example, scheduling software can prioritize high-urgency orders, allocating them to machines with the shortest setup times.
- Production Forecasting: Accurate demand forecasting ensures raw materials and tools are available when needed. This reduces delays caused by material shortages. A factory processing 500 parts per week might maintain a buffer stock of 10% to handle unexpected orders.
- Process Mapping: Mapping each production stage—design, programming, machining, and inspection—identifies bottlenecks. For instance, a factory might discover that tool changes take 15% of production time and adjust by standardizing tool setups.
By integrating these steps, factories can reduce idle time by up to 20%, ensuring machines operate at maximum capacity. Planning also involves real-time monitoring, where dashboards display machine status, allowing supervisors to reassign tasks dynamically if a machine goes offline.
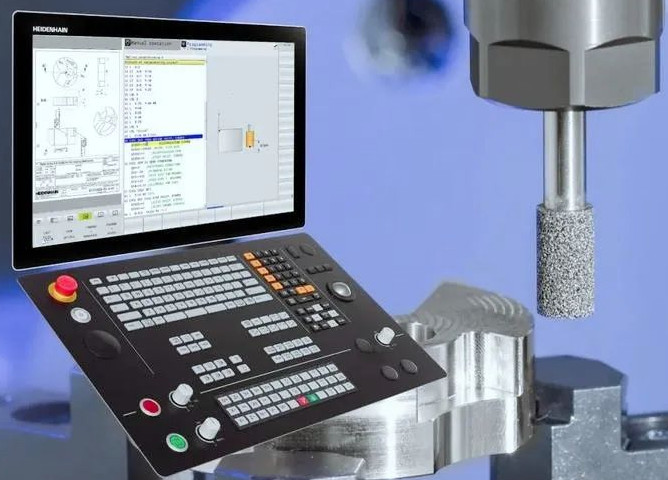
Optimizing CNC Machine Setup and Operation
Machine setup and operation are critical to production efficiency. Minimizing setup times and maximizing machine uptime directly contribute to rapid delivery. Key strategies include:
- Standardized Tooling: Using standardized tool holders, such as HSK or BT systems, reduces setup time. For example, a factory using HSK63 holders can swap tools in under 30 seconds compared to 2 minutes for non-standardized systems.
- High-Speed Machining Parameters: Optimizing cutting speeds and feeds enhances throughput. For aluminum machining, a spindle speed of 12,000 RPM with a feed rate of 200 inches per minute can reduce cycle time by 25% compared to conservative settings.
- Multi-Axis Machining: 5-axis CNC machines allow complex parts to be machined in a single setup, reducing repositioning time. A 5-axis mill can access five sides of a part, cutting setup time by up to 40% compared to 3-axis machines.
- Toolpath Optimization: CAM software generates efficient toolpaths, minimizing non-cutting movements. For instance, a trochoidal milling path can reduce machining time by 15% for complex geometries.
Factories also implement automatic tool changers (ATCs) with capacities of 20–60 tools, enabling uninterrupted operation for diverse parts. Regular calibration ensures machines maintain tolerances within 0.001 inches, critical for industries like aerospace and medical devices.
Implementing Automation for Continuous Production
Automation is a cornerstone of efficient CNC factories, enabling 24/7 production with minimal human intervention. Key automation strategies include:
- Robotic Loading Systems: Robots load and unload workpieces, reducing manual handling time. A robotic arm can load a part in 10 seconds, compared to 30 seconds for manual loading, increasing throughput by 15% in high-volume settings.
- Pallet Changers: Automatic pallet changers allow continuous machining by swapping workpieces without stopping the machine. A dual-pallet system can reduce downtime by 50%, as one pallet is machined while the other is loaded.
- In-Process Monitoring: Sensors monitor tool wear and machine vibrations, adjusting parameters in real-time. For example, a vibration sensor can detect a worn tool and trigger a replacement, preventing defects and saving 5–10% of production time.
Automation reduces labor costs and human error, ensuring consistent quality. A factory producing 10,000 parts monthly can save 100 labor hours by automating loading and unloading, translating to significant cost savings.
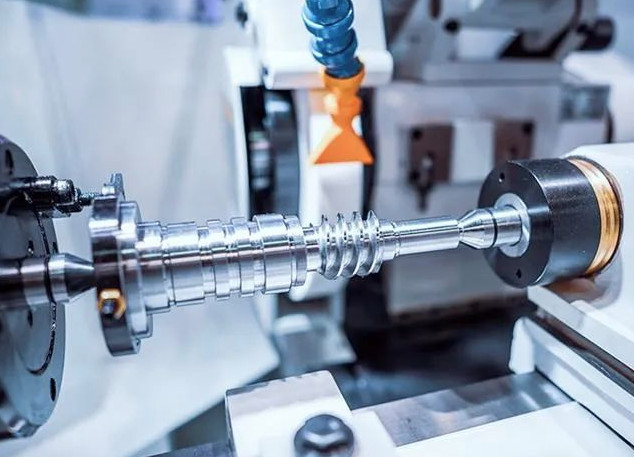
Leveraging Software for Precision and Speed
Advanced software integration is essential for optimizing Производство с ЧПУ. Factories rely on CAD/CAM systems, simulation tools, and real-time monitoring software to enhance efficiency. Key applications include:
- CAD/CAM Integration: CAD software designs parts, while CAM software generates G-code for machining. Seamless integration reduces programming time by 30%, as designs are directly translated into machine instructions.
- Simulation Software: Virtual simulations identify potential collisions or inefficiencies before machining begins. A simulation can reduce setup errors by 90%, saving hours of rework.
- Real-Time Data Analytics: Software tracks machine performance, identifying inefficiencies. For example, analytics might reveal that a machine runs at 70% capacity, prompting adjustments to increase utilization to 85%.
Factories using cloud-based CAM systems can share programs across multiple machines, ensuring consistency and reducing programming time by 20%. These tools also support rapid prototyping, allowing design iterations in hours rather than days.
Enhancing Material Management for Faster Turnaround
Efficient material management ensures raw materials are available and processed optimally, reducing delays. Strategies include:
- Inventory Control: Just-In-Time (JIT) inventory minimizes storage costs while ensuring material availability. A factory might maintain a 2-day material buffer for high-demand metals like aluminum 6061 or stainless steel 304.
- Material Optimization: Nesting software arranges parts on raw material sheets to minimize waste. For sheet metal, nesting can reduce material usage by 10–15%, lowering costs and speeding production.
- Supplier Coordination: Strong relationships with suppliers ensure timely delivery of materials. Factories often use electronic data interchange (EDI) to automate ordering, reducing lead times by 2–3 days.
Effective material management ensures production lines remain active, with material-related delays accounting for less than 5% of downtime in well-optimized factories.
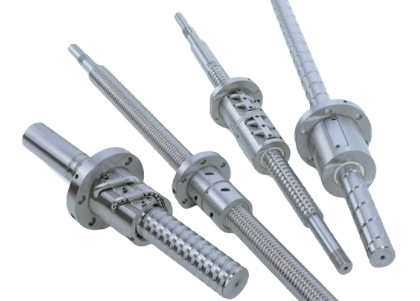
Maintaining Quality Control for Consistent Output
Rapid delivery requires consistent quality to avoid rework, which delays production. CNC factories implement robust quality control (QC) systems:
- In-Line Inspection: Coordinate Measuring Machines (CMMs) inspect parts during production, ensuring tolerances within 0.0005 inches. This reduces post-production inspection time by 50%.
- Statistical Process Control (SPC): SPC monitors production data to detect deviations. For example, a factory might set a control limit of ±0.002 inches for a critical dimension, triggering alerts if exceeded.
- Operator Training: Certified operators follow standardized procedures, reducing human error. Training programs cover G-code programming, tool selection, and safety protocols, ensuring 99% defect-free output.
By integrating QC into the production process, factories achieve a first-pass yield rate of 95% or higher, minimizing rework and ensuring on-time delivery.
Workforce Training and Skill Development
A skilled workforce is critical to efficient CNC operations. Factories invest in training to enhance productivity:
- Certification Programs: Operators complete courses in CNC programming and operation, typically requiring 6–12 months. Certified operators can reduce setup errors by 25%.
- Cross-Training: Training workers on multiple machines increases flexibility. A cross-trained operator can switch between milling and turning machines, reducing staffing bottlenecks by 15%.
- Continuous Learning: Regular workshops on new software or machining techniques keep skills current. For example, training on advanced CAM features can reduce programming time by 10%.
A well-trained workforce ensures machines operate at peak efficiency, with operator errors contributing to less than 2% of production issues.
Key Performance Indicators for CNC Efficiency
Tracking performance metrics allows factories to measure and improve efficiency. The following table outlines key indicators and their impact:
Metric | Описание | Target | Impact |
---|---|---|---|
Machine Utilization | Percentage of time machines are actively machining | 85–90% | Higher utilization reduces idle time, increasing throughput |
Cycle Time | Time to complete one part | Reduce by 20% | Shorter cycles enable faster delivery |
First-Pass Yield | Percentage of parts meeting specs on first attempt | 95%+ | Reduces rework, saving time and costs |
Setup Time | Time to prepare machine for new job | Under 30 minutes | Faster setups increase production capacity |
Regularly monitoring these metrics ensures factories identify inefficiencies early, maintaining rapid delivery schedules.
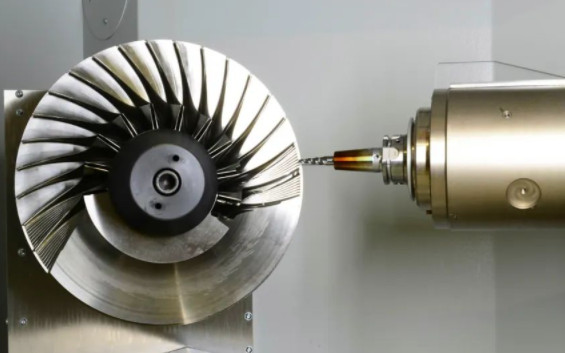
Case Study: Efficiency in Action
A mid-sized CNC factory producing 2,000 aerospace components monthly implemented several strategies to optimize efficiency. By adopting 5-axis machining, the factory reduced setup time by 35%, saving 50 hours monthly. Automation via robotic loading cut labor costs by 10%, while CAM software optimization reduced cycle times by 15%. The factory also used SPC to maintain a 98% first-pass yield, minimizing rework. As a result, lead times dropped from 10 days to 7 days, enabling the factory to meet urgent client demands while maintaining quality.
Заключение
Optimizing production efficiency in CNC factories for rapid delivery requires a systematic approach, integrating advanced planning, automation, software, material management, quality control, and workforce training. By focusing on standardized processes, real-time monitoring, and data-driven decisions, factories can achieve machine utilization rates above 85%, cycle time reductions of 20%, and first-pass yields exceeding 95%. These strategies, grounded in technical expertise and industry experience, ensure CNC factories deliver high-quality parts on time, meeting the demands of modern manufacturing.