CNC (Computer Numerical Control) machining is a cornerstone of modern manufacturing, enabling the production of precise, complex components across industries such as aerospace, automotive, and medical. The quality of CNC-machined parts is influenced by multiple factors, with machining experience playing a pivotal role. This article examines how experience in CNC services affects product quality, emphasizing operator expertise, process optimization, equipment maintenance, and quality control. By focusing on technical proficiency and systematic approaches, we highlight why seasoned expertise is critical for achieving consistent, high-quality outcomes.
Operator Expertise and Its Role in Precision
The skill and experience of CNC operators directly influence the quality of machined parts. Experienced operators possess a deep understanding of CNC systems, including programming, setup, and operation, which minimizes errors and enhances precision. They can interpret complex blueprints, optimize tool paths, and adjust machining parameters to meet tight tolerances, often within ±0.001 inches (±0.025 mm) for high-precision industries like aerospace.
Experienced operators excel in selecting appropriate cutting tools, feed rates, and spindle speeds. For example, a seasoned operator might choose a carbide end mill with a specific coating (e.g., TiAlN) for machining stainless steel, ensuring a surface finish with roughness (Ra) below 0.8 micrometers. They also understand material properties, such as the hardness of titanium (approximately 36 HRC), and adjust parameters to prevent tool wear or workpiece deformation. In contrast, novice operators may struggle with these decisions, leading to issues like dimensional inaccuracies or poor surface finishes.
Training programs, such as those aligned with the National Institute for Metalworking Skills (NIMS), provide operators with hands-on experience in operating 3-axis and 5-axis CNC machines. Over time, operators develop an intuitive sense for detecting anomalies, such as vibrations indicating improper clamping, which can cause chatter marks or misalignment. This expertise reduces the error rate to less than 1%, compared to higher rates for less experienced operators, ensuring consistent quality across production runs.
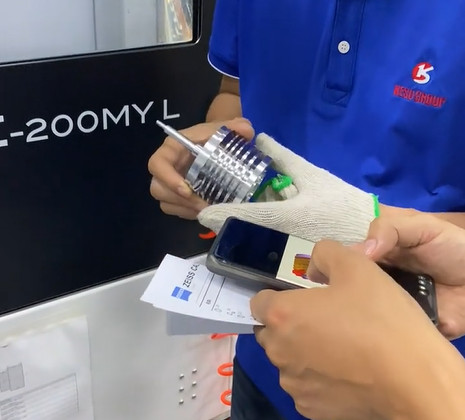
Process Optimization Through Accumulated Knowledge
Experienced CNC services implement optimized processes refined through years of practice, directly impacting product quality. Process optimization involves fine-tuning machining parameters, such as cutting speed, feed rate, and depth of cut, to achieve efficiency without compromising precision. For instance, a service provider with extensive experience might use a cutting speed of 100-150 m/min for aluminum alloys with a feed rate of 0.1-0.2 mm/rev, balancing tool life and surface quality.
Experienced teams also leverage advanced software, such as CAD/CAM systems, to simulate tool paths before machining. This reduces errors like tool collisions or inefficient paths that increase cycle times. For example, optimizing tool paths can reduce machining time by up to 20% while maintaining tolerances within ±0.002 inches (±0.05 mm). CNC services with years of experience have established standard operating procedures (SOPs) that ensure repeatability, critical for mass production where consistency is paramount.
Another aspect of process optimization is material selection and handling. Experienced CNC services maintain databases of material behaviors, enabling them to choose alloys like 6061-T6 aluminum for its machinability or 316 stainless steel for corrosion resistance. They also implement precise fixturing techniques, ensuring workpieces are securely clamped to prevent movement, which could lead to dimensional errors or surface defects.
Equipment Maintenance and Calibration
Regular maintenance and calibration of CNC machines are critical for maintaining quality, and experienced CNC services excel in these areas. CNC machines, such as mills and lathes, rely on precise components like spindles, bearings, and ball screws, which wear over time. Services with extensive experience implement preventive maintenance schedules, reducing unplanned downtime by up to 30% compared to less experienced providers.
For example, spindle accuracy is vital for quality, as deviations can cause vibrations or thermal deformation. Experienced maintenance teams monitor spindle runout, ensuring it remains below 0.0002 inches (0.005 mm) to prevent inaccuracies. They also use circulating lubrication systems with oil temperature controllers to maintain spindle temperatures within 20-30°C, minimizing thermal expansion. Calibration, performed using tools like laser interferometers, ensures machine accuracy aligns with ISO 230-2 standards, achieving positional accuracy within ±0.0004 inches (±0.01 mm).
Experienced CNC services also conduct routine cleaning to remove debris and lubricate moving parts, preventing issues like tool chatter or premature wear. These practices ensure machines operate at peak performance, producing parts with consistent quality across thousands of cycles.

Quality Control and Inspection Processes
Quality control (QC) is integral to CNC machining, and experienced CNC services implement robust inspection processes to ensure parts meet specifications. These processes include raw material checks, in-process monitoring, and final inspections, all of which benefit from years of refined expertise.
Raw material inspection ensures materials meet hardness and strength requirements. For example, a service might verify that a batch of 4140 steel has a tensile strength of 655 MPa before machining. In-process monitoring involves real-time adjustments to parameters like feed rate (e.g., 0.05-0.15 mm/rev for steel) to correct deviations. Final inspections use precision instruments like coordinate measuring machines (CMM) to verify dimensional accuracy within tolerances, such as ±0.0005 inches (±0.0127 mm) for aerospace components.
Experienced CNC services also employ statistical process control (SPC) to analyze production data, identifying trends or variations before they escalate. SPC can reduce defect rates by 15-20% by enabling early corrective actions. Compliance with standards like ISO 9001 or AS9100 ensures that quality processes are systematic and auditable, enhancing reliability and customer trust.
The following table summarizes key quality control checks and their impact:
Quality Control Stage | Key Actions | Impact on Quality |
---|---|---|
Raw Material Inspection | Verify material properties (e.g., hardness, tensile strength) | Ensures material suitability, reducing defects |
Мониторинг в процессе производства | Adjust cutting speed, feed rate, tool wear | Minimizes deviations during machining |
Final Inspection | Use CMM, calipers, micrometers for dimensional checks | Confirms parts meet tolerances and standards |
Consistency in Mass Production
CNC machining excels in producing identical parts repeatedly, and experience enhances this capability in CNC services. Providers with years of operation have refined setups to achieve repeatability within ±0.0001 inches (±0.0025 mm), critical for industries like automotive where components must fit seamlessly in assemblies. Experienced operators use G-code and M-code programming to ensure consistent tool movements, reducing variations across batches.
For example, in producing engine components, an experienced CNC service can maintain a cycle time of 2-3 minutes per part while achieving a surface finish of Ra 0.4 micrometers. This consistency stems from optimized workflows, such as automated tool changes and precise fixturing, developed through years of trial and error. In contrast, less experienced services may struggle with setup variations, leading to higher rejection rates or rework costs.
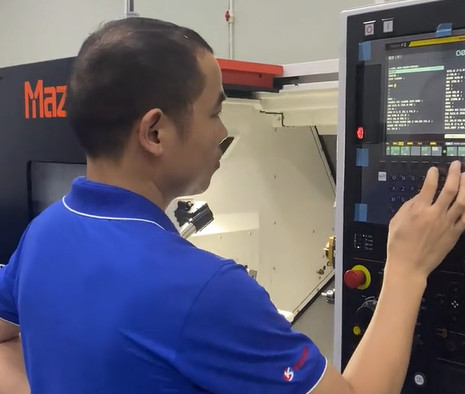
Efficiency and Cost Reduction
Experienced CNC services improve efficiency, directly impacting quality by reducing errors and waste. For instance, optimized tool paths and cutting parameters can decrease material waste by 10-15%, while precise setups reduce cycle times by up to 25%. This efficiency ensures parts are produced within specifications, minimizing costly rework or scrap.
Experienced services also invest in operator training and process documentation, creating a knowledge base that reduces reliance on individual expertise. This systematic approach ensures that even new operators can achieve high-quality results by following established protocols. Additionally, experienced services negotiate better material and tool supplies, ensuring consistent quality inputs, which further enhances output reliability.
Industry-Specific Applications and Expertise
Experience in specific industries, such as aerospace or medical, enhances quality due to specialized knowledge. For example, aerospace CNC services understand the need for lightweight titanium components with tolerances of ±0.0002 inches (±0.005 mm) to withstand extreme conditions. Medical CNC services focus on biocompatible materials like PEEK, ensuring implants meet FDA standards with surface finishes below Ra 0.2 micrometers.
Experienced services also adapt to industry-specific challenges. In automotive manufacturing, they produce transmission components with consistent hardness (e.g., 58-62 HRC) to ensure durability. This expertise comes from years of working with industry standards, enabling CNC services to anticipate and address unique requirements, resulting in higher-quality outputs.

Kesu CNC: Where Experience Crafts Perfection
With decades of expertise honed across aerospace, automotive, and medical industries, Kesu CNC transforms precision into possibility. Our seasoned operators master tight tolerances (±0.0001 inches), optimal toolpaths, and material nuances—from titanium’s strength to PEEK’s biocompatibility—ensuring every part meets strict custom standards. Backed by rigorous quality control, proactive equipment calibration, and industry-specific know-how, we deliver consistent, high-performance components that redefine reliability. Choose Kesu: where experience isn’t just a skill—it’s your guarantee of excellence.
Заключение
CNC machining experience profoundly impacts quality in CNC services through operator expertise, process optimization, equipment maintenance, and robust quality control. Experienced operators leverage their knowledge to achieve precision, while optimized processes and maintenance ensure consistency and efficiency. Rigorous quality control, backed by industry standards, minimizes defects and ensures compliance. Services with extensive experience produce parts with tight tolerances, superior surface finishes, and high reliability, meeting the demands of industries like aerospace, automotive, and medical. By investing in training, documentation, and systematic approaches, experienced CNC services deliver consistent, high-quality results, reinforcing their value in modern manufacturing.