Selecting a CNC machining factory is a critical decision that directly impacts project timelines and production efficiency. Delivery delays can disrupt supply chains, increase costs, and damage customer relationships. This guide provides a systematic, experience-based approach to choosing a CNC factory to ensure timely delivery of machined parts. By focusing on technical and operational factors, businesses can minimize delays and maintain reliable production schedules.
Evaluate Factory Production Capacity
Production capacity determines a factory’s ability to handle order volumes without delays. Overloading a factory beyond its capabilities often results in extended lead times. To assess capacity:
- Equipment Availability: Verify the number and type of CNC machines (e.g., 3-axis, 5-axis mills, or lathes). A factory with 20+ machines, including multi-axis systems, can typically handle complex orders faster than one with fewer than 10 machines.
- Shift Patterns: Factories operating multiple shifts (e.g., 24/7) process orders quicker than those limited to single shifts. Confirm the factory’s operating hours and workforce size, aiming for at least 50 skilled operators for medium-scale projects.
- Order Backlog: Request data on current order backlog. A factory with a backlog exceeding 80% of capacity for the next 4 weeks may struggle to meet deadlines.
Before committing, request a capacity assessment report detailing machine utilization rates and staffing levels. This ensures the factory can accommodate your order without scheduling conflicts.
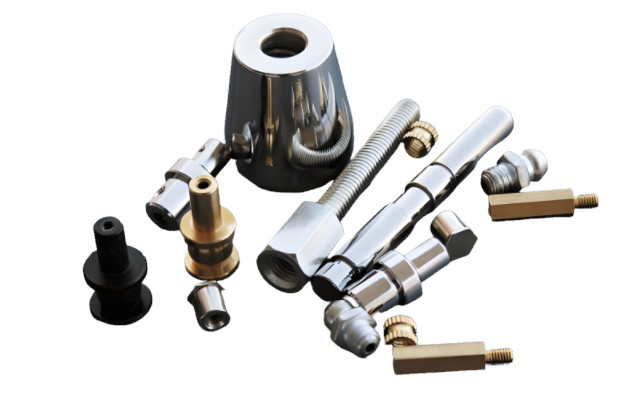
Assess Raw Material Supply Chain
Raw material availability is a common cause of delays in Обработка на станках с ЧПУ. Issues like supplier delays or quality inconsistencies can halt production. To mitigate risks:
- Supplier Relationships: Choose factories with established partnerships with at least 3-5 reliable material suppliers. These partnerships ensure consistent delivery of materials like aluminum 6061, stainless steel 304, or titanium within 3-5 days.
- Inventory Management: Confirm the factory maintains stock levels for common materials (e.g., 500-1000 kg of aluminum or steel). Factories with real-time inventory tracking systems reduce procurement delays by 20-30%.
- Material Quality Control: Ensure suppliers provide materials meeting standards like ASTM or ISO. Factories should conduct incoming inspections, rejecting materials with deviations exceeding ±0.01 mm in critical dimensions.
Request a supplier list and material procurement timelines to verify the factory’s ability to secure materials promptly. Factories with diversified suppliers are less vulnerable to disruptions.
Verify Production Management Systems
Efficient production management minimizes delays by optimizing workflows. Factories with robust systems ensure smooth operations. Key considerations include:
- Production Scheduling: Look for factories using Enterprise Resource Planning (ERP) systems to create schedules based on real-time data. Schedules should prioritize orders with lead times under 7 days and balance machine loads to avoid bottlenecks.
- Real-Time Monitoring: Factories with Manufacturing Execution Systems (MES) track production progress, detecting issues like tool wear or machine downtime within 10-15 minutes. This reduces delays by up to 25%.
- Управление качеством: Ensure the factory has a Quality Management System (QMS) certified to ISO 9001. QMS processes, such as in-process inspections, prevent rework, which can delay delivery by 2-5 days.
Ask for a demonstration of the factory’s ERP or MES software to confirm its capabilities. Factories with integrated systems are better equipped to meet deadlines consistently.
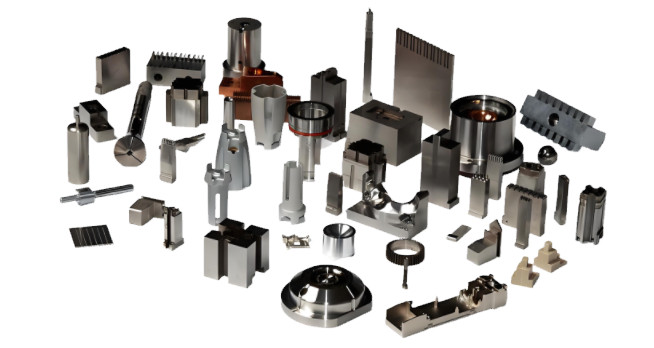
Examine Technical Capabilities
Technical expertise and equipment condition directly affect machining efficiency. Complex parts or outdated machines can extend lead times. To evaluate technical capabilities:
- Технические характеристики машины: Confirm machines support high-speed cutting (e.g., spindle speeds of 10,000-20,000 RPM) and tight tolerances (±0.005 mm). Multi-axis machines reduce setups, cutting lead times by 15-20%.
- Maintenance Protocols: Factories should follow preventive maintenance schedules, inspecting machines every 500-1000 operating hours. This reduces downtime risks, which can delay production by 1-3 days.
- Operator Skills: Ensure operators are trained in CAD/CAM software and have 3-5 years of experience. Skilled operators optimize tool paths, reducing machining time by 10-15%.
Request machine specifications and maintenance logs to verify equipment reliability. Factories with advanced technology and skilled staff deliver parts faster.
Optimize Part Design for Manufacturability
Part design complexity affects machining time and delivery. Simplifying designs reduces production steps and delays. Key strategies include:
- Simplify Geometries: Avoid features like deep pockets (>10:1 depth-to-width ratio) or thin walls (<0.5 mm), which require slower cutting speeds and increase machining time by 20-30%.
- Standardize Materials: Use readily available materials like aluminum 6061 or ABS plastic, which machine faster than exotic alloys like Inconel, reducing lead times by 2-4 days.
- Minimize Tolerances: Specify tolerances only where necessary (e.g., ±0.01 mm for non-critical features). Overly tight tolerances (±0.001 mm) can double inspection times.
Collaborate with the factory’s engineers during the Design for Manufacturability (DFM) review to identify design improvements. Factories offering free DFM feedback can reduce lead times by 10-15%.
Ensure Effective Communication
Clear communication prevents misunderstandings that lead to delays. Factories with strong communication protocols streamline project execution. Consider:
- Project Management: Factories should assign a dedicated project manager to provide updates every 2-3 days. This ensures alignment on timelines and specifications.
- Order Tracking: Choose factories with online portals for real-time order status updates. Portals reduce response times for inquiries by 50%.
- Technical Drawings: Provide detailed drawings with all dimensions, tolerances, and material specifications. Incomplete drawings can delay production by 1-3 days.
Establish communication protocols before production starts, including preferred contact methods and update frequency. Factories with responsive teams minimize delays caused by miscommunication.
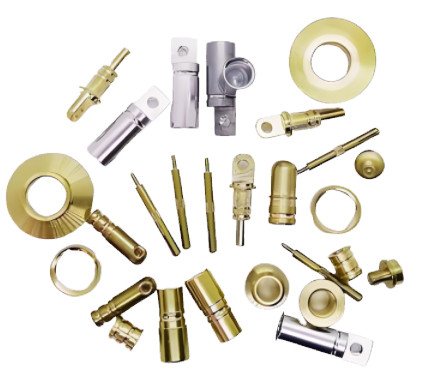
Assess Logistics and Shipping Capabilities
Logistics delays can negate efficient production. Factories with optimized shipping processes ensure timely delivery. Key factors include:
- Logistics Partners: Verify the factory works with 2-3 reputable logistics providers offering expedited shipping options (e.g., 2-5 day delivery for international orders).
- Packaging Standards: Ensure parts are packaged to withstand transit conditions (e.g., using foam inserts for parts with tolerances <±0.01 mm). Proper packaging reduces damage-related delays by 90%.
- Shipping Tracking: Factories should provide real-time shipment tracking via integrated logistics systems. This allows proactive resolution of delays, reducing delivery time by 1-2 days.
Request a logistics plan detailing shipping methods and timelines. Factories with integrated logistics systems deliver parts 10-20% faster than those relying on manual processes.
Review Past Performance and Certifications
A factory’s track record and certifications indicate reliability. Factories with proven performance are less likely to cause delays. Evaluate:
- Delivery History: Request data on on-time delivery rates. Aim for factories with at least 95% on-time delivery over the past 12 months.
- Сертификаты: Look for ISO 9001, AS9100, or IATF 16949 certifications, which ensure standardized processes. Certified factories reduce delays by 15-20% due to consistent quality control.
- Client References: Contact 2-3 previous clients to confirm the factory’s reliability. Positive feedback on lead times and communication builds trust.
Review case studies or performance reports to assess the factory’s ability to meet deadlines. Certified factories with strong references are more dependable.
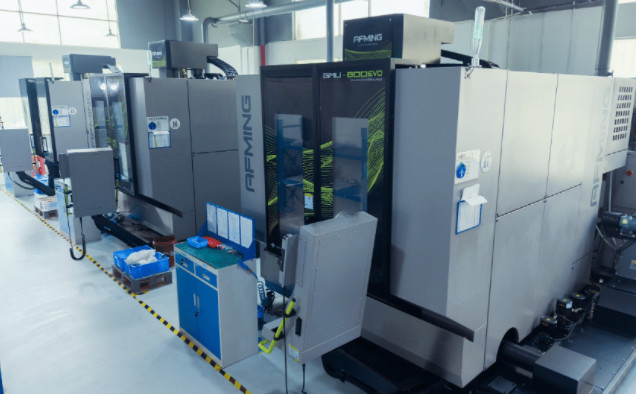
Key Metrics for Factory Selection
The following table summarizes critical metrics to evaluate when choosing a CNC machining factory to avoid delivery delays:
Фактор | Recommended Metric | Impact on Delivery |
---|---|---|
Production Capacity | 20+ machines, 24/7 shifts | Reduces lead times by 20-30% |
Raw Material Supply | 3-5 suppliers, 500-1000 kg stock | Prevents procurement delays |
Production Management | ERP/MES systems, ISO 9001 | Minimizes bottlenecks by 25% |
Technical Capabilities | 10,000-20,000 RPM, ±0.005 mm tolerances | Cuts machining time by 15% |
Logistics | 2-5 day expedited shipping | Ensures timely delivery |
Заключение
Avoiding delivery delays when choosing a CNC machining factory requires a systematic evaluation of production capacity, supply chain, management systems, technical capabilities, design optimization, communication, logistics, and past performance. By prioritizing factories with robust processes, advanced technology, and reliable track records, businesses can ensure timely delivery of high-quality parts. Use the metrics and strategies outlined in this guide to select a factory that aligns with your project’s timeline and quality requirements.