Flexibility in CNC (Computer Numerical Control) machining factories is a critical factor that determines their ability to adapt to varying production demands, improve efficiency, and maintain competitiveness. By integrating flexible manufacturing systems (FMS) and leveraging the capabilities of CNC machines, factories can respond effectively to changes in product types, production volumes, and process sequences. This article explores the technical, operational, and strategic importance of flexibility in CNC machining, emphasizing its role in enhancing productivity, reducing costs, and meeting customer requirements.
Understanding Flexibility in CNC Machining
Flexibility in CNC machining refers to the ability of a manufacturing system to adapt to changes in production requirements with minimal downtime, cost, or manual intervention. This adaptability is achieved through advanced automation, computer-controlled machinery, and modular system designs. Flexibility is typically categorized into two primary types: machine flexibility and routing flexibility.
Machine Flexibility: This allows a CNC system to perform multiple operations on a single part or produce different types of parts using the same machine. For example, a CNC machine with multiple axes (e.g., 5-axis or 6-axis models) can handle complex geometries and diverse materials, such as metals, plastics, or composites, without requiring significant reconfiguration.
Routing Flexibility: This enables the system to reroute parts to alternative machines or adjust the sequence of operations when needed. For instance, if one machine is down for maintenance, routing flexibility ensures production continues by redirecting tasks to other available machines.
These forms of flexibility are supported by automated systems, such as CNC machines, robotic arms, and material handling systems like conveyors or automated guided vehicles (AGVs). Together, they create a dynamic production environment capable of handling diverse manufacturing needs.
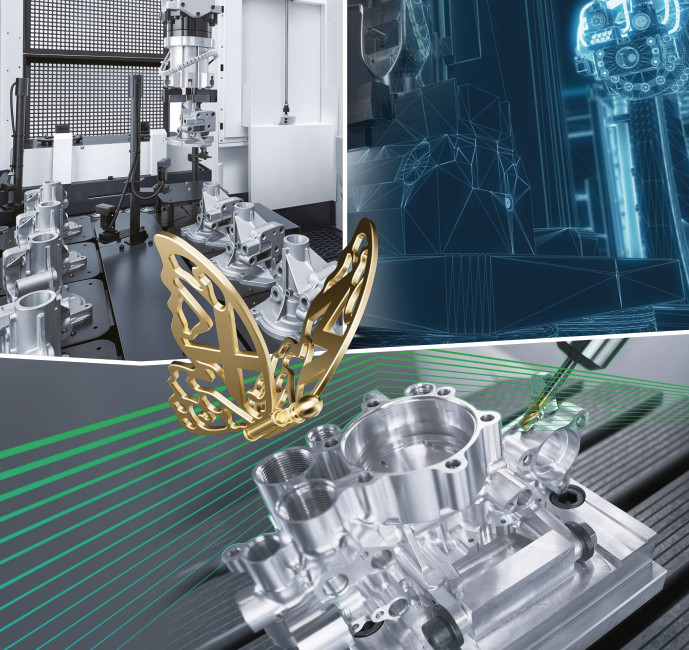
Key Components of a Flexible CNC Machining System
A flexible CNC machining system relies on several core components that work together to ensure adaptability and efficiency. These components are designed to integrate seamlessly, enabling the system to respond to changes in production requirements.
Component | Описание | Role in Flexibility |
---|---|---|
CNC Machines | Computer-controlled machines (e.g., lathes, mills, routers) capable of performing multiple operations with high precision. | Enable rapid reprogramming to produce different parts or adjust operations, supporting machine flexibility. |
Material Handling Systems | Automated systems like conveyors, AGVs, or robotic arms that transport parts and tools between workstations. | Facilitate routing flexibility by ensuring smooth movement of parts to alternative machines or processes. |
Control Software | Centralized software that manages machine operations, production schedules, and data monitoring. | Coordinates tasks, optimizes workflows, and enables real-time adjustments to production changes. |
Tooling Systems | Interchangeable tools and fixtures that can be quickly adapted for different parts or processes. | Support machine flexibility by allowing rapid tool changes to accommodate varied production needs. |
These components form the backbone of a flexible manufacturing system, enabling CNC factories to achieve high levels of adaptability and efficiency.
Benefits of Flexibility in CNC Machining Factories
Flexibility in CNC machining factories delivers several technical and operational advantages that directly impact productivity, cost-efficiency, and product quality. Below are the key benefits, each explained in detail.
Enhanced Production Efficiency
Flexible CNC systems reduce setup times and minimize downtime during production changeovers. For example, a CNC machine with a large tool matrix (e.g., 160 tools) can switch between tasks without requiring manual tool changes, reducing setup time by up to 50% compared to traditional systems. Automated material handling systems, such as AGVs, further streamline workflows by transporting parts between workstations with minimal delay. This efficiency is critical in high-mix, low-volume production environments where frequent changes in product types are common.
Additionally, flexible systems can operate continuously (24/7) with minimal human intervention, maximizing machine utilization. For instance, a flexible manufacturing cell (FMC) with a single CNC machine and an automated pallet system can achieve up to 80% reduction in in-process inventory, as parts are processed and moved efficiently without bottlenecks.
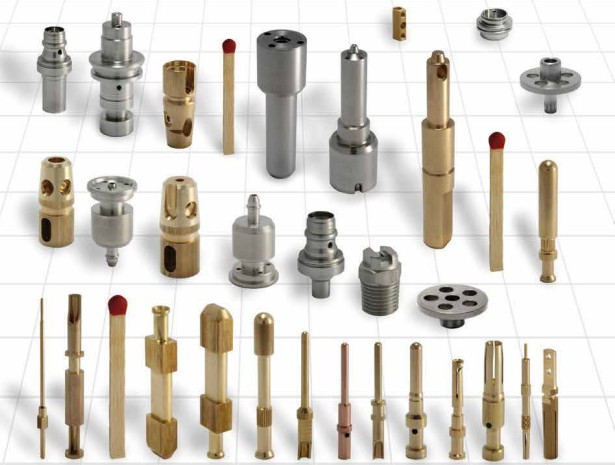
Improved Product Customization
Flexibility enables CNC factories to produce customized parts tailored to specific customer requirements. CNC machines integrated with CAD/CAM software can execute complex designs with tolerances as tight as 0.001 inches (0.0254 mm). This precision is vital for industries like aerospace, where components such as airfoils or landing gear require exact specifications, or medical device manufacturing, where implants demand high accuracy.
Moreover, flexible systems allow for rapid reprogramming to accommodate design changes. For example, a 5-axis CNC machine can produce intricate geometries in a single setup, reducing the need for multiple machines or manual adjustments. This capability supports small-batch production of customized products, enabling factories to meet niche market demands without compromising efficiency.
Scalability for Varying Production Volumes
Flexible CNC systems are highly scalable, allowing factories to adjust production volumes based on demand. For instance, a modular FMS can integrate additional CNC machines or workstations without disrupting existing operations. This scalability is critical for industries with fluctuating demand, such as automotive manufacturing, where production may shift from 1,000 units to 10,000 units within weeks.
Routing flexibility further enhances scalability by enabling the system to distribute workloads across multiple machines. If demand for a specific part increases, the system can allocate additional machines to the task, maintaining consistent output without overloading individual units. This adaptability ensures factories can respond to market changes while maintaining quality and delivery timelines.
Reduced Labor Costs and Improved Safety
Automation in flexible CNC systems reduces the need for manual labor, lowering operational costs. For example, a single operator can manage multiple CNC machines in an FMS, compared to traditional setups where each machine requires a dedicated operator. This can reduce labor costs by up to 30% in some cases, depending on the complexity of the system.
Additionally, flexible systems enhance workplace safety by minimizing human intervention in hazardous tasks. CNC machines equipped with safety features, such as automatic shutoffs or enclosed workspaces, reduce the risk of accidents. Automated material handling systems further decrease the need for workers to handle heavy or dangerous materials, improving overall safety.
Consistent Quality and Reduced Errors
Flexible CNC systems incorporate real-time monitoring and quality control mechanisms to ensure consistent output. Integrated sensors and inspection systems detect deviations in part dimensions or surface finish, flagging issues for immediate correction. For example, a CNC machine with in-process gauging can maintain tolerances within 0.0005 inches (0.0127 mm), ensuring high-quality parts across production runs.
By reducing reliance on manual processes, flexible systems also minimize human error. CAD/CAM integration ensures that designs are translated accurately into machine instructions, eliminating mistakes caused by manual programming or setup. This consistency is essential for industries like electronics, where even minor defects can lead to product failures.
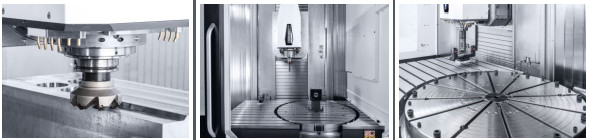
Applications of Flexibility in CNC Machining
Flexibility in CNC machining is particularly valuable in industries requiring high precision, customization, or variable production volumes. Below are key applications where flexibility plays a critical role.
Промышленность | Application | Flexibility Benefit |
---|---|---|
Аэрокосмическая промышленность | Production of airfoils, manifolds, and landing gear components. | Rapid reprogramming for complex geometries and tight tolerances (e.g., 0.001 inches). |
Автомобили | Manufacturing of engine parts, transmission components, and custom interiors. | Scalability to handle varying production volumes and quick changeovers for different part types. |
Медицина | Production of implants, surgical instruments, and diagnostic devices. | Высокая точность and customization for patient-specific requirements. |
Электроника | Fabrication of circuit board components and enclosures. | Flexibility to produce small batches with frequent design changes. |
These applications demonstrate how flexibility enables CNC factories to meet diverse industry demands while maintaining efficiency and quality.
Operational Considerations for Implementing Flexibility
While flexibility offers significant advantages, implementing it requires careful planning and investment. CNC factories must consider several factors to ensure successful integration of flexible systems.
System Design and Integration: Designing a flexible CNC system involves selecting compatible components, such as CNC machines, material handling systems, and control software. For example, a factory may choose a 5-axis CNC machine with a tool capacity of 120 to handle diverse tasks. Integration requires robust software to coordinate operations and ensure seamless communication between components.
Skilled Workforce: Flexible systems require operators with expertise in programming, maintenance, and system management. Training programs are essential to equip workers with the skills needed to operate advanced CNC machines and troubleshoot issues. For instance, a CNC machinist must be proficient in CAD/CAM software to program complex parts accurately.
Maintenance and Reliability: Flexible systems are complex and require regular maintenance to prevent downtime. For example, a CNC machine with IoT connectivity can monitor tool wear and signal maintenance needs, reducing unexpected failures. Factories must establish maintenance schedules and stock critical spare parts to ensure continuous operation.
Initial Investment: The cost of implementing a flexible CNC system can be significant, including expenses for machines, software, and training. However, the long-term benefits, such as reduced labor costs and increased productivity, often justify the investment. Factories should conduct a cost-benefit analysis to determine the feasibility of adopting flexible systems.
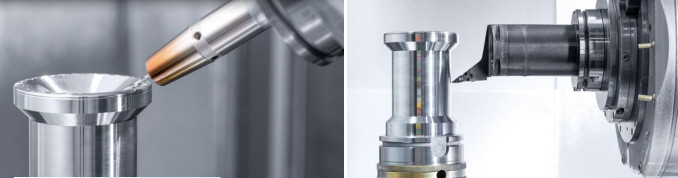
Заключение
Flexibility in CNC machining factories is a cornerstone of modern manufacturing, enabling factories to adapt to changing production demands, improve efficiency, and deliver high-quality, customized products. By leveraging machine flexibility, routing flexibility, and advanced automation, CNC factories can reduce downtime, lower costs, and meet the needs of diverse industries. While implementing flexible systems requires careful planning and investment, the benefits of enhanced productivity, scalability, and quality make it a critical strategy for staying competitive in today’s manufacturing landscape.