The coupling quality of ball-and-socket joints in plunger assemblies is critical to the performance of aviation plunger pumps. Traditional inspection methods, such as red lead coloring, have limitations that can mask actual coupling issues, leading to performance challenges despite meeting dimensional tolerances. This article presents an optimized inspection method using a refined coloring medium and procedure to enhance the accuracy and reliability of coupling quality assessment. The method has been validated in production and applied to similar components, reducing rework rates and production costs.
Overview of Ball-and-Socket Joint Coupling in Plunger Assemblies
The ball-and-socket joint in plunger assemblies, is a critical component in aviation plunger pumps. The coupling quality directly affects the pump’s performance, reliability, and lifespan. The joint consists of a plunger ball head and a slipper socket, requiring precise dimensional tolerances and smooth operation without jamming. The radial clearance between the ball head and socket must be ≤0.01 mm, with free rotation and no binding to meet performance requirements.
Traditional inspection relies on ensuring individual dimensional tolerances, surface roughness, and contour accuracy, followed by a coloring test using red lead to verify coupling quality. However, this approach often fails to detect subtle coupling issues, resulting in qualified components that still cause performance issues during pump operation. The optimized method addresses these shortcomings by improving the coloring medium and inspection process.
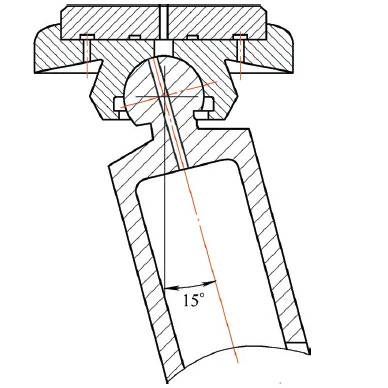
Precision Requirements for Plunger Assembly Components
Сайт precision of the ball-and-socket joint components is paramount to achieving the required coupling quality. Below are the detailed specifications for the plunger ball head and slipper socket.
Plunger Ball Head Specifications
The plunger ball head, made from Cr12MoV steel, must meet stringent dimensional and surface requirements (Plunger Head Dimensions). The key specifications include:
- Диаметр: Sφ9 +0.1/0 mm
- Contour Accuracy: 0.005 mm
- Шероховатость поверхности: Ra = 0.05 μm
These parameters ensure the ball head fits precisely within the socket while maintaining smooth rotational movement.
Slipper Socket Specifications
The slipper socket must also adhere to strict tolerances to ensure proper coupling. The key specifications are:
- Диаметр: Sφ9 mm (ensuring clearance within the assembly)
- Roundness: 0.005 mm
- Шероховатость поверхности: Ra = 0.05 μm
These requirements are critical to maintaining geometric and motion precision, directly impacting the plunger pump’s performance and longevity.
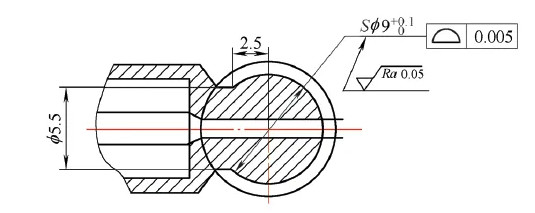
Traditional Coloring Inspection Method
The traditional method for inspecting ball-and-socket joint coupling involves applying red lead to the ball head and rotating it within the socket to assess contact patterns. A coupling quality is deemed acceptable if the coloring rate (contact area) is ≥90% (Coloring Inspection Diagram). This method evaluates whether the components meet the required clearance (≤0.01 mm) and operate without binding.
However, the red lead method has significant limitations. The thickness and uneven application of red lead can mask non-contact areas, leading to false positives where the coupling appears acceptable but fails during operation. The method’s reliance on operator skill and experience further introduces variability, reducing its reliability.
Analysis of Coloring Inspection Principles
The ideal coupling state requires the plunger ball head to rotate freely within the slipper socket without binding, even when individual components meet dimensional tolerances. However, cumulative errors in dimensions, contour deviations, or operational factors can cause binding or poor coupling quality. To address this, a standardized coloring gauge is used as a reference ball head, grouped by dimensional increments of 0.005 mm within the tolerance range. This gauge ensures consistency and interchangeability, overcoming the variability of individual plunger heads.
The coloring gauge is coated with a medium and rotated within the socket to assess contact patterns. The goal is to verify that the coupling achieves a contact rate of ≥90%, indicating a high-quality fit. However, the traditional red lead medium often leads to misleading results due to its thickness and poor control over application uniformity.
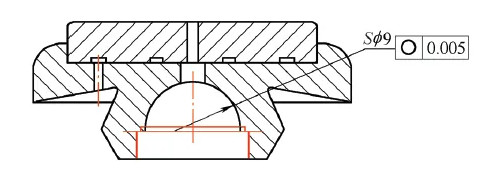
Limitations of Traditional Coloring Inspection
Despite its widespread use, the red lead coloring method has notable drawbacks, identified through extensive production validation:
- Inconsistent Application: The thickness and uniformity of red lead are difficult to control, requiring skilled operators to achieve reliable results.
- Masking of Non-Contact Areas: Thick red lead layers can transfer to non-contact surfaces during rotation, falsely indicating a high contact rate.
- Operational Variability: The method’s dependence on operator experience introduces inconsistencies, affecting inspection reliability.
These issues result in components passing inspection but failing during pump operation, leading to rework and increased production costs.
Optimized Coloring Inspection Method
To address the limitations of the red lead method, a new coloring medium was developed, consisting of a mixture of Prussian blue, castor oil, and titanium dioxide (TiO₂) in a 1:1:1 volume ratio. This mixture is thinner and more uniform than red lead, improving the accuracy of contact pattern assessment. The optimized method includes the following steps:
- Preparation of Coloring Medium: Mix Prussian blue, castor oil, and titanium dioxide in equal parts, stir until a creamy consistency is achieved, and let it settle for 24 hours in a sealed container.
- Application: Apply a thin, uniform layer of the mixture to the coloring gauge using a cotton ball or chamois leather, minimizing thickness while ensuring coverage.
- Inspection Process: Insert the coated coloring gauge into the socket, rotate it 15° to 45°, and perform at least four back-and-forth rotations along the circumference to create continuous contact marks.
- Evaluation: Assess the contact pattern, requiring a coloring rate of ≥95%. Non-colored areas are permitted only at the socket’s mouth.
This method simulates the plunger assembly’s operational conditions, ensuring the coupling is free of binding and meets performance requirements.
Implementation and Results
The optimized coloring inspection method has been implemented in production with significant improvements. The use of the Prussian blue mixture eliminates the masking effect of thick red lead, providing a clearer indication of actual contact areas. The method’s reliability is enhanced by the standardized coloring gauge, which ensures consistency across inspections.
Key results include:
- Reduced Rework Rates: The rework rate for plunger assemblies decreased by over 50%, as the method accurately identifies coupling issues before assembly.
- Improved Coupling Quality: The method ensures a coupling contact rate of ≥95%, eliminating binding during pump operation.
- Cost Savings: By reducing rework and improving component reliability, production costs have been significantly lowered.
The following table summarizes the comparison between the traditional and optimized methods:
Параметр | Traditional Red Lead Method | Optimized Prussian Blue Method |
---|---|---|
Coloring Medium | Red lead | Prussian blue, castor oil, titanium dioxide (1:1:1) |
Contact Rate Requirement | ≥90% | ≥95% |
Rework Rate Reduction | Baseline | >50% |
Reliability of Contact Assessment | Moderate (prone to masking) | High (clear contact patterns) |
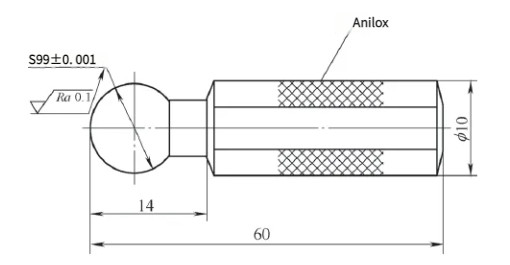
Application Scope and Benefits
The optimized coloring inspection method is suitable for ball-and-socket joints with contour accuracy ≤0.005 mm, making it applicable to precision coupling quality checks in similar components. Its adoption in batch production has demonstrated its effectiveness in improving inspection accuracy and component reliability. The method eliminates the quality risks associated with traditional red lead inspection, ensuring flexible operation without binding and preventing false positives.
The approach has been widely adopted in the production of similar components, providing a reliable and repeatable process for quality control. It also serves as a reference for other precision coupling inspections, offering a systematic and standardized solution.
Заключение
The optimized coloring inspection method for ball-and-socket joints in plunger assemblies addresses the limitations of traditional red lead inspection. By using a thinner, more reliable Prussian blue mixture and a standardized coloring gauge, the method achieves a higher contact rate requirement (≥95%) and significantly reduces rework rates. Its implementation ensures precise coupling quality, eliminates operational binding, and lowers production costs. The method’s success in production validates its effectiveness and provides a valuable framework for inspecting similar precision components.