Нержавеющая сталь обладает преимуществами в коррозионной стойкости и износостойкости. Готовые изделия из нержавеющей стали обладают высокой прочностью и вязкостью. Они широко используются в механическом оборудовании, пресс-формах и других областях. Детали из нержавеющей стали являются ключевыми компонентами определенного механического оборудования и имеют высокие требования к точности.
Нержавеющая сталь трудно поддается резке. Если обрабатываемость высококачественной углеродистой стали 45 используется в качестве эталона (установленного на 1,0), то обрабатываемость аустенитной нержавеющей стали 304 составляет около 0,37. Нержавеющая сталь - это легированная сталь с содержанием хрома более 12% или никеля более 8%. Ее теплопроводность плохая, и возникают такие проблемы, как прилипание ножей и нелегкое разрушение стружки при обработке. Из-за плохой теплопроводности нержавеющей стали температура ее резки выше, чем температура резки обычной стали, до 1000℃, и детали деформируются во время обработки, что затрудняет контроль точности. Во время фактического процесса резки тепло, переносимое железной стружкой, составляет не более Fz (подача на лезвие) с обеих сторон. Если обрабатываемый материал обладает идеальной теплопроводностью, то тепло будет передаваться внутрь по поверхности Fz за короткое время, отводя больше обработанного тепла. Степень влияния различных параметров резания на остаточное напряжение также различна. От большого к малому изменяются скорость резания, глубина резания и величина подачи, что согласуется с влиянием параметров резания на силу резания и температуру резания, указывая на то, что влияние параметров резания на обработку остаточных напряжений также происходит через механические и тепловые эффекты. Поэтому установка разумных параметров резания имеет преимущества в снижении деформации при обработке деталей. Нержавеющая сталь сваривается с большой деформацией, и зона сварки начинает уменьшаться под действием напряжения. Растягивающее остаточное напряжение возникает в зоне сварки, а сжимающее остаточное напряжение воздействует на окружающую зону сварки. Материалы из нержавеющей стали подвергаются разной степени усадочной деформации. Область сварки велика, а время сварки велико, соответственно, увеличивается деформация сварочной заготовки.
Оптимизация конструкции деталей и производственного процесса
Оптимизированный дизайн
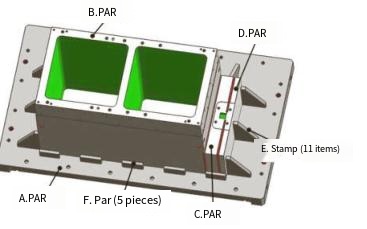
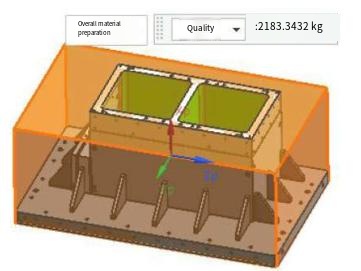
При разработке модели обработки детали с учетом ее свойств, особенности формы крупных деталей декомпозируются на несколько твердотельных моделей. Как показано на рис. 1, разложенные компоненты - это A, B, C, D, E и F, а характеристики разложенных компонентов становятся простыми. По сравнению с материалами, необходимыми для подготовки всего материала до разложения и материалами, необходимыми для подготовки одной детали после разложения, разложение материала позволяет сэкономить 55,4% материала, как показано на рисунке 2. Обрабатываемые детали разлагаются на отдельные простые компоненты, что упрощает характеристики обработки, снижает сложность обработки, а также уменьшает объем удаления. Соответственно снижаются производственные затраты, такие как время обработки и использование инструмента, что позволяет снизить производственные затраты, а также избежать большого количества конструкций электродов, обработки электродов, обработки разряда и т. д. Метод проектирования с разбивкой целого на части позволяет снизить стоимость обработки деталей, сократить цикл обработки и повысить конкурентоспособность.
Анализ производственного процесса
Обработанные детали можно разделить на 2 основных компонента корпуса A, B и более мелкие компоненты C, D, а также множество усиливающих ребер E, F, и более 20 компонентов инкрустированы (см. рис. 1). Сложности в контроле точности обработки детали: ① Основной компонент корпуса имеет большой размер, стенку и большой объем удаления, что приводит к длительному времени резки и большой деформации напряжения, что может легко привести к чрезмерной разнице в размерах обработки; ② Все инкрустации требуют уплотнения сварочного соединения, а площадь сварки велика, что затрудняет контроль деформации обрабатываемых деталей.

Точность изготовления деталей должна быть высокой. Как показано на рисунке 3, степень плоскостности максимальной плоскости должна составлять 0,05 мм. Компонент A относится к типу крупногабаритных плат. Отдельная деталь имеет большую деформацию, и величину деформации после сварки трудно оценить; боковые стенки двусторонних пазов детали B перпендикулярны под углом 90°, высота составляет 425 мм, а вертикальность должна составлять 0,05 мм. Необходимо выполнить технические требования чертежей, а обработка затруднена.
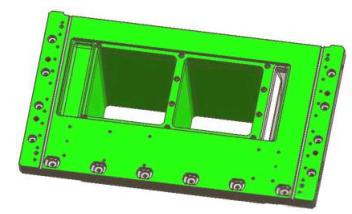
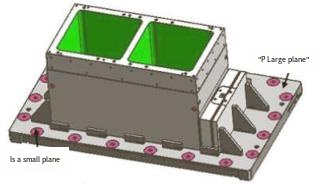
Согласно приведенному выше анализу, после завершения изготовления отдельного компонента сварка и инкрустация не могут гарантировать соблюдение требований к допуску деталей. Поэтому при составлении технологического процесса однокомпонентная деталь обрабатывается с запасом, позиционирование штифта (отверстия), затяжка винта (отверстия), сборка интегрирована, сварка и инкрустация не могут быть гарантированы, а затем детали доводятся до требуемого размера. Для деталей с высокими требованиями к точности деформация напряжения отдельной заготовки снимается и устраняется путем грубой фрезерной обработки, старения с воздушным охлаждением и обработки без излишков. Поверхности, которые невозможно обработать после сборки, и детали с низкими требованиями к точности обрабатываются на месте за один проход в соответствии с требованиями чертежей, а затем компоненты собираются и свариваются в единое целое. Наконец, детали с высокими требованиями к точности и резервным запасом подвергаются тонкой обработке, как показано на рис. 4. Вышеупомянутые методы обработки позволяют эффективно контролировать точность обработки. Что касается поверхностей деформации, которые невозможно контролировать, то большая плоскость P1, показанная на рисунке 5, деформируется после сварки и не поддается контролю, но существуют также требования к плоскости. Исходя из требований к использованию механических деталей, модель конструкции оптимизируется, а малая плоскость P2 увеличивается в соответствии с реальными потребностями использования. После сварки и деформации малая плоскость P2 подвергается тонкой фрезеровке. Это позволяет не только упростить обработку, но и обеспечить технические требования к обработке деталей и снизить стоимость обработки.
Обработка компонентов
Обработка компонента B
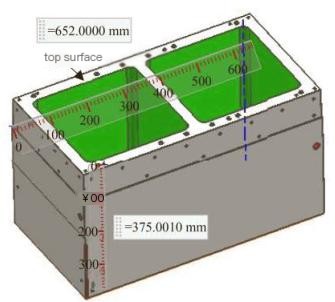
Компонент B показан на рис. 6 и обрабатывается на эффективном ЧПУ. Компонент представляет собой грубую фрезерную резку сложной заготовки, 70% материала, подлежащего удалению, и глубокой полости обработки, для того, чтобы уменьшить сложность удаления стружки, выбрать горизонтальный станок с ЧПУ обработки, в соответствии с условиями сайта, чтобы определить параметры обработки показаны в таблице 1, эффективность резки инструмента достичь 40мин / время, может уменьшить частоту операторов, чтобы изменить инструмент для повышения эффективности обработки. Этапы обработки следующие.
(1) Черновая фрезеровка на станке с ЧПУ высотой 375 мм, оставляя припуск на одну сторону 2 мм в осевом направлении, заготовка вокруг профильной поверхности, два сквозных паза пока не обрабатываются.
(2) Грубая фрезеровка на станке с ЧПУ по форме поверхности, два сквозных паза, радиальный, осевой припуск 2 мм/одна сторона.
(3) Старение при воздушном охлаждении в течение 48 ч.
(4) Станок с ЧПУ фрезерует нижнюю поверхность, отверстия под штифты, отверстия под винты, снимает фаски, фрезерует нижнюю поверхность и компоненты A для вставки.
(5) Станок с ЧПУ вокруг боковой фрезеровки, обработки винтовых отверстий, отверстий для штифтов, 648 мм × 346 мм × 82 мм шаг поверхности не обрабатывается на данный момент, оставляя последующую сборку после сварки, а затем обработки.
(6) Сборка, кламмер через штифт и отверстие, сборка компонентов A, B, C, D и усиление, после сварки.
Обработка компонента A

Компонент A относится к типу тонких пластин, как показано на рисунке 7, большой диаметр фрезы резки обработки экструзии генерирует большую силу легко деформировать компонент, для того, чтобы уменьшить риск деформации и повысить эффективность обработки, выбор D21mm фрезы, быстрое удаление остаточного материала. Этапы обработки следующие.
(1) Станок с ЧПУ черновая обработка передней и нижней особенности, радиальные и осевые оставить одну сторону припуск 2 мм; обработка завершена, заготовка в неограниченном состоянии, в машине микрометр тест плоскостности <2 мм для квалифицированных, может войти в следующий процесс.
(2) Старение с воздушным охлаждением в течение 48 ч.
(3) Обнаружение плоскостности <2 мм является квалифицированным, может войти в следующий процесс.
(4) ЧПУ станок обработки передней, большой плоскости фрезерования осевой маржи 0,1 мм (последующее шлифование до окончательного размера); укрепление позиции слот, штифт отверстие обработки на месте, вокруг стороны профиля радиальной маржи 0,5 мм. обработки нижней поверхности максимального профиля заготовки четыре стороны от центра X0Y0, дно поднял 0,1 мм; 6 M10mm потайной стол резьбовые отверстия на месте, остальные характеристики радиальной, осевой Оставить маржу 1 мм / односторонней обработки.
(5) Отшлифуйте нижнюю поверхность, чтобы увидеть свет, переднюю поверхность до окончательного размера (0,1 мм припуска, оставленного в предыдущем процессе), верхнюю поверхность отшлифуйте до окончательного размера, для и компонентов B, C, D, E, F вставки.
(6) Сборка, зажимы через штифты и отверстия, сборка компонентов A, B, C, D, E, F и усиление, после сварки.
Обработка мелких деталей
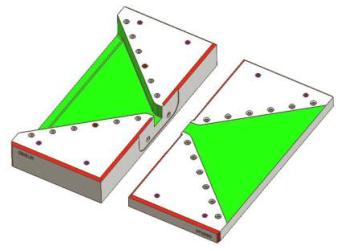
Небольшие компоненты C и D, как показано на рис. 8, имеют низкие требования к точности и обрабатываются непосредственно до окончательного размера в соответствии с чертежами, прежде чем комбинация будет сожжена. Чертежи арматуры E, F требуют свободных допусков, несколько компонентов арматуры объединяются в заготовку материала, а затем обрабатываются методом резки проволоки и придания формы.
Сварка в сборе
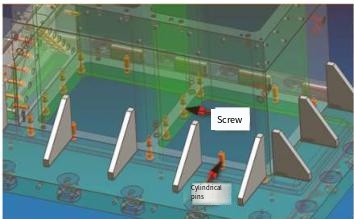
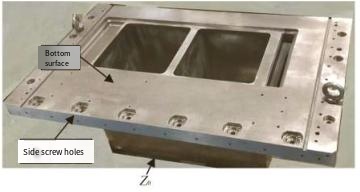
Крупные детали из нержавеющей стали процесс сварки, из-за сложности, должны быть предсказаны в процессе сварки возможной деформации, заранее принять профилактические меры для контроля. Процесс заключается в расположении свариваемых деталей, используя конструкцию ряда штифтов (отверстия для штифтов), винтов (отверстия для винтов) для точной сборки и крепления деталей, как показано на рисунке 10, чтобы гарантировать, что заготовка в процессе сварки минимизирует смещение и относительное положение заготовки и заготовки к заготовке остается неизменным. В процессе сварки необходимо освоить параметры и методы сварки, порядок и т.д., чтобы гарантировать, что деформация нержавеющая сталь части могут быть эффективно контролироваться. Сборка сварки после комбинации обработки, как показано на рисунке 11, конкретные шаги реализации следующие.
(1) Обнаружение плоскостности нижней поверхности ≤ 0,5 мм является квалифицированным, может войти в следующий процесс.
(2) Обработка нижней поверхности на станке с ЧПУ, максимальная форма компонента A, четыре стороны центра X0Y0, назначенная поверхность для Z0, точная фрезеровка максимальной формы, нижней плоскости, обработка особенностей нижней поверхности до окончательного размера; точная фрезеровка сквозного паза 1/2 высоты до окончательного размера, как показано на рисунке 12. Поскольку общая высота двух сквозных пазов детали составляет 425 мм, угол R составляет 18 мм, выберите D32 мм круглый нос фрезы (твердосплавные антивибрационные стойки инструмента), длина нависания после зажима составляет 215 мм, обработка 1/2 высоты паза для обеспечения жесткости инструмента, чтобы обеспечить окончательную обработку точности размеров, после обработки, используя микрометр для обнаружения сквозных пазов были закончены фрезерования стороны перпендикулярности, плоскостность ≤ 0,02 мм квалифицируется. Обработка верхней поверхности, суб-центр был фрезерован через четыре стороны канавки для X0Y0, фрезерование захвата оставшихся 1/2 высоты через канавку; обработка P2 показано на рисунке 5 небольшой плоскости, P1 большой плоскости сварочной деформации является большим, сложные функции, и нет требований к сборке, больше не обрабатывается, обработка завершена с микрометром, чтобы обнаружить был фрезерован через канавку стороны двух, перпендикулярность, плоскостность ≤ 0,02 мм квалифицируется. Внедрение технологического контроля в производственный процесс деталей, деталей ключевых размеров в режиме реального времени инспекции и подтверждения деталей не обрабатываются на месте или сборки необоснованных частей, чтобы быть исправлены в своевременном порядке, чтобы гарантировать, что детали в обработке следующей машины для достижения требований квалифицированных.
(3) Финишная обработка с ЧПУ резьбовые отверстия по бокам компонента A и 82-миллиметровые ступеньки и резьбовые отверстия компонента B.
(4) 600# наждачная бумага полировка нижней большой плоскости, два сквозных паза и нижней поверхности особенности, удалить ЧПУ фрезерные линии.
Проверка эффективности
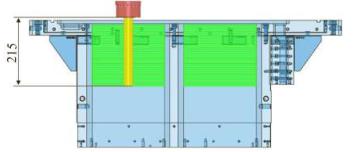
Шероховатость поверхности и точность размеров являются двумя важными параметрами в индексе оценки качества, эти два параметра от поверхностного эффекта, геометрической точности, чтобы отразить хорошее или плохое производство деталей. Через вышеуказанный процесс обработки и проверки обработки деталей партии, окончательный размер, данные обнаружения шероховатости достигли технических требований чертежей, особенно наиболее трудно контролировать нижнюю большую плоскость, показанную на рисунке 11, плоскостность обнаружения значения ≤ 0.023 мм, на рисунке 12 показаны два через канавку с четырех сторон плоскостности и перпендикулярности <0,05 мм. из данных размерного контроля, видно, что этот тип деталей из нержавеющей стали, через вышеуказанный процесс, может контролировать обработку, обжиг и сварку. процесс, может контролировать деформации, возникающие при обработке, сварке, чтобы обеспечить качество обработки.
Крупные детали из нержавеющей стали обработки с использованием метода разложения, может эффективно снизить сложность обработки частей и уменьшить деформацию обработки, компоненты, чтобы принять отверстие для штифта (гвоздь) позиционирования и винтовые отверстия (гвозди) крепежные меры для обеспечения точности сборки и уменьшить деформацию сварки; процесс резки, уменьшить скорость резки, глубина резки, подача на край может гарантировать, что нержавеющая сталь резки плавно; разложение компонентов одного куска При обработке, оставить соответствующий запас, сборки и сварки после объединения, а затем отделки, может обеспечить точность ключевых размеров.

Высокоточная пятиосевая обработка крупных деталей из нержавеющей стали
Решение KeSu по пятиосевой обработке предназначено для деталей из нержавеющей стали. В нем используются передовые технологии ЧПУ и обширный опыт работы в отрасли, что позволяет без труда справляться со сложными геометрическими формами и требованиями к высокой точности. От аэрокосмической промышленности и медицинского оборудования до автомобильного производства - мы гарантируем, что каждая деталь будет иметь безупречную обработку поверхности, точные размеры и надежную работу. Благодаря интеллектуальной оптимизации траектории обработки мы сокращаем производственные циклы и затраты, сохраняя при этом исключительное качество. Выбирайте нас, и ваши детали из нержавеющей стали будут плавно переходить от проекта к готовому изделию, обеспечивая успех вашего проекта!
Заключение
Обработка крупных деталей из нержавеющей стали, отличающихся высокой прочностью, вязкостью и плохой обрабатываемостью, сопряжена со значительными трудностями в контроле деформации и обеспечении точности. Благодаря использованию подхода декомпозиционного проектирования сложная деталь разбивается на более простые компоненты (A, B, C, D, E, F), что позволяет сократить расход материала на 55,4%, упростить характеристики обработки и снизить стоимость производства. Оптимизированный процесс производства, включающий черновое фрезерование, старение с воздушным охлаждением, точную сборку с креплением на штифтах и винтах, а также стратегическое резервирование, эффективно снижает деформацию, вызванную напряжением при резке и сварке. Критические этапы обработки, такие как фрезерование с ЧПУ с тщательно подобранными параметрами и инструментами, обеспечивают высокую точность, а плоскостность и перпендикулярность соответствуют строгим требованиям (≤0,05 мм и ≤0,02 мм, соответственно). Послесварочная обработка и технологический контроль гарантируют точность размеров и качество поверхности. Такой комплексный подход, включающий оптимизацию конструкции, контролируемую обработку и точную сборку, успешно решает проблемы обработки нержавеющей стали, обеспечивая высокую точность, снижение деформации и повышение эффективности производства крупногабаритных компонентов.
ЧАСТО ЗАДАВАЕМЫЕ ВОПРОСЫ
Почему нержавеющая сталь трудно поддается обработке по сравнению с другими материалами?
Нержавеющая сталь, например аустенитная нержавеющая сталь 304, имеет рейтинг обрабатываемости около 0,37 по сравнению с высококачественной углеродистой сталью 45 (рейтинг 1,0). Высокая прочность, вязкость и плохая теплопроводность этой стали приводят к таким проблемам, как прилипание инструмента, трудности при снятии стружки и высокие температуры резания (до 1000°C), которые вызывают деформацию и затрудняют контроль точности.
Как метод декомпозиционного проектирования помогает при производстве крупных деталей из нержавеющей стали?
Метод декомпозиционного проектирования разбивает крупные детали на более простые компоненты (например, A, B, C, D, E, F), сокращая расход материалов на 55,4%, упрощая особенности обработки, снижая сложность обработки и уменьшая производственные затраты. Это сводит к минимуму необходимость в сложных конструкциях электродов и сокращает время обработки, повышая конкурентоспособность.
Каковы основные проблемы, связанные с обеспечением точности при обработке деталей из нержавеющей стали?
Основные проблемы включают: большой размер деталей и удаление материала (например, 70% для компонента B), что приводит к длительному времени резки и деформации, вызванной напряжением; большие зоны сварки, вызывающие усадку, создающие растягивающее остаточное напряжение в зоне сварки и сжимающее напряжение в окружающих областях, что затрудняет соблюдение жестких допусков (например, плоскостность и перпендикулярность 0,05 мм).
Какие меры обеспечивают точность сварки и минимизируют деформацию?
Точность сварки обеспечивается за счет использования штифтовых и винтовых отверстий для точного выравнивания, контроля параметров и последовательности сварки, а также послесварочной обработки с ЧПУ критических поверхностей (например, сквозных канавок до плоскостности/перпендикулярности 0,02 мм) и полировки наждачной бумагой 600# для удаления линий фрезерования.
Как проверяется конечное качество деталей?
Качество проверяется с помощью контроля размеров и шероховатости поверхности, при этом достигается плоскостность большой плоскости дна ≤0,023 мм и плоскостность/перпендикулярность пазов ≤0,05 мм (боковые поверхности ≤0,02 мм). Проверки процесса в реальном времени обеспечивают своевременное внесение корректировок, гарантируя соответствие техническим требованиям.