Selecting a reliable CNC (Computer Numerical Control) factory is critical for ensuring high-quality parts, timely delivery, and cost-effective production. This guide outlines systematic, experience-based criteria for evaluating CNC factories, from initial quotation to final delivery. With a focus on technical rigor and professional standards, the following sections provide detailed parameters and practical considerations to establish trust and ensure successful partnerships.
Quotation Process: Transparency and Accuracy
The quotation phase sets the foundation for a successful collaboration. A reliable CNC factory should provide clear, detailed, and accurate quotes that reflect their technical expertise and commitment to transparency.
- Detail Level: Quotes should include itemized costs for materials, machining, finishing, inspection, and shipping. For example, a quote for a stainless steel part should specify material grade (e.g., 304 or 316), machining hours, and surface finish requirements (e.g., Ra 0.8 µm).
- Response Time: A professional factory responds within 24-48 hours, indicating efficient internal processes. Delays beyond 72 hours may signal poor organization.
- Technical Clarifications: The factory should proactively seek clarifications on drawings or specifications. For instance, if a tolerance of ±0.01 mm is specified, they should confirm feasibility for the material and geometry.
- Cost Breakdown: A transparent quote separates fixed costs (e.g., setup fees) from variable costs (e.g., per-unit machining). This helps evaluate scalability for small (10 units) or large (1,000 units) batches.
Key Parameter: Ensure quotes align with ISO 2768-1 standards for general tolerances unless более жесткие допуски are explicitly requested. For example, a medium-class tolerance for a 100 mm dimension should be ±0.2 mm.
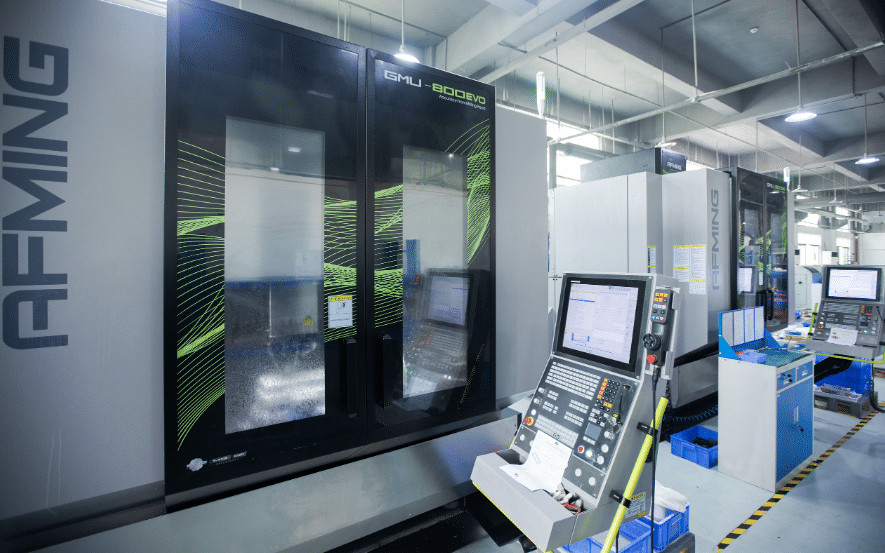
Technical Capabilities: Machinery and Expertise
A CNC factory’s technical capabilities determine its ability to produce parts that meet design specifications. Evaluating machinery, tooling, and staff expertise is essential for ensuring precision and reliability.
- Machine Types: Verify the factory has appropriate CNC machines, such as 3-axis, 4-axis, or 5-axis mills, lathes, or Swiss-type machines. For complex geometries, 5-axis machines are preferred due to their ability to machine multiple surfaces in a single setup.
- Material Range: The factory should handle a variety of materials, including metals (aluminum, steel, titanium), plastics (ABS, PEEK), and composites. For example, machining titanium requires specialized tools and slower cutting speeds (30-50 m/min).
- Tolerance Capabilities: Confirm the factory can achieve required tolerances. Standard tolerances are ±0.05 mm, but high-precision parts may require ±0.005 mm, achievable with advanced machines like Mazak or DMG MORI.
- Staff Expertise: Skilled operators and engineers are critical. Look for certifications (e.g., AS9100 for aerospace) or evidence of in-house training programs.
Тип машины | Max Part Size (mm) | Допуск (мм) | Типовые применения |
---|---|---|---|
3-Axis Mill | 1000 x 500 x 500 | ±0.05 | Flat parts, simple geometries |
5-Axis Mill | 500 x 500 x 500 | ±0.01 | Complex, multi-angle parts |
Токарный станок с ЧПУ | Ø 300 x 600 | ±0.02 | Cylindrical parts, shafts |
Quality Assurance: Standards and Inspection
Quality assurance (QA) is a cornerstone of reliability. A professional CNC factory implements robust QA processes to ensure parts meet specifications and industry standards.
- Certifications: Look for ISO 9001 certification, which ensures consistent quality management. Industry-specific standards like AS9100 (aerospace) or IATF 16949 (automotive) add credibility.
- Inspection Equipment: The factory should have coordinate measuring machines (CMM), optical comparators, or surface roughness testers. For example, a CMM can measure tolerances to ±0.001 mm accuracy.
- Inspection Frequency: Verify the factory conducts first article inspections (FAI) and in-process checks. FAI reports should include measured dimensions, material certifications, and compliance with drawings.
- Traceability: Reliable factories maintain material and process traceability. For instance, a batch of aluminum parts should include a material certificate specifying alloy composition (e.g., Al 6061-T6).
Key Parameter: Surface finish should meet specified roughness values (e.g., Ra 1.6 µm for general-purpose parts, Ra 0.4 µm for polished surfaces). Verify the factory’s ability to measure and achieve these values.
Production Capacity: Scalability and Lead Times
A factory’s production capacity affects its ability to meet demand and deliver on time. Assessing capacity ensures the factory can handle your project’s volume and schedule.
- Machine Availability: Confirm the number of CNC machines and shifts (e.g., 24/7 operations). A factory with 20 machines running two shifts can handle larger orders than one with five machines on a single shift.
- Batch Size Flexibility: The factory should support prototyping (1-10 units), small batches (10-100 units), and production runs (100+ units). Setup costs should decrease per unit for larger orders.
- Lead Times: Standard lead times for CNC parts are 5-10 days for prototypes and 2-4 weeks for production. Rush orders should be available with clear surcharges (e.g., 20% premium for 3-day delivery).
- Subcontracting Policies: Ask if the factory subcontracts work. Subcontracting can introduce delays or quality inconsistencies unless tightly controlled.
Key Parameter: For a 100-unit order of aluminum brackets (100 x 50 x 10 mm), expect a lead time of 10-15 days with a setup cost of $200-$500, depending on complexity.
Supply Chain Management: Materials and Logistics
Effective supply chain management ensures consistent material quality and timely delivery. A reliable factory maintains strong supplier relationships and robust logistics processes.
- Material Sourcing: The factory should source materials from certified suppliers. For example, steel should come with mill certificates verifying properties like tensile strength (e.g., 500 MPa for 4140 steel).
- Inventory Management: Check if the factory stocks common materials (e.g., Al 6061, stainless 304) to reduce lead times. Custom materials like titanium may require 1-2 weeks for procurement.
- Logistics: Verify shipping options (e.g., DHL, FedEx) and packaging standards. Parts should be packed to prevent damage, using foam inserts or anti-corrosion coatings for metals.
- Customs Compliance: For international orders, the factory should provide accurate HS codes and export documentation to avoid delays.
Key Parameter: Material lead time for standard alloys should not exceed 3 days. For exotic materials, allow 7-14 days for sourcing.
Communication and Support: Building Trust
Effective communication fosters trust and ensures project alignment. A reliable factory prioritizes responsiveness and technical support throughout the process.
- Point of Contact: The factory should assign a dedicated project manager fluent in English (or your preferred language) to handle inquiries.
- Technical Support: Engineers should be available to discuss design for manufacturability (DFM) feedback. For example, they might suggest increasing a fillet radius from 0.5 mm to 1 mm to reduce machining time.
- Progress Updates: Expect regular updates on production status, especially for large orders. Weekly reports should include milestones like material receipt, machining completion, and inspection.
- After-Sales Support: The factory should offer rework or refunds for non-conforming parts. A clear return policy (e.g., 30-day inspection period) is a sign of reliability.
Key Parameter: Response time for technical queries should be within 24 hours, with detailed explanations referencing drawings or specifications.
Cost Management: Balancing Quality and Price
While cost is a key factor, the cheapest option is not always the most reliable. A professional factory balances cost with quality, offering competitive pricing without compromising standards.
- Pricing Structure: Compare unit prices across factories for identical parts. For a 50 x 50 x 10 mm aluminum block, expect $10-$20 per unit for 100 units, including milling and anodizing.
- Hidden Costs: Beware of unlisted fees for setup, tooling, or inspection. A reliable factory discloses all costs upfront.
- Volume Discounts: Economies of scale should reduce per-unit costs. For example, a 1,000-unit order may cost 30% less per unit than a 100-unit order.
- Payment Terms: Standard terms are 30% upfront, 70% upon delivery. Flexible terms (e.g., 50/50) may be negotiated for long-term partnerships.
Cost Component | Amount (USD) | Примечания |
---|---|---|
Материал | 300 | Al 6061, 2 kg/unit |
Обработка | 800 | 3-axis milling, 1 hr/unit |
Анодирование | 200 | Type II, black |
Setup Fee | 250 | One-time cost |
Total | 1,550 | $15.50/unit |
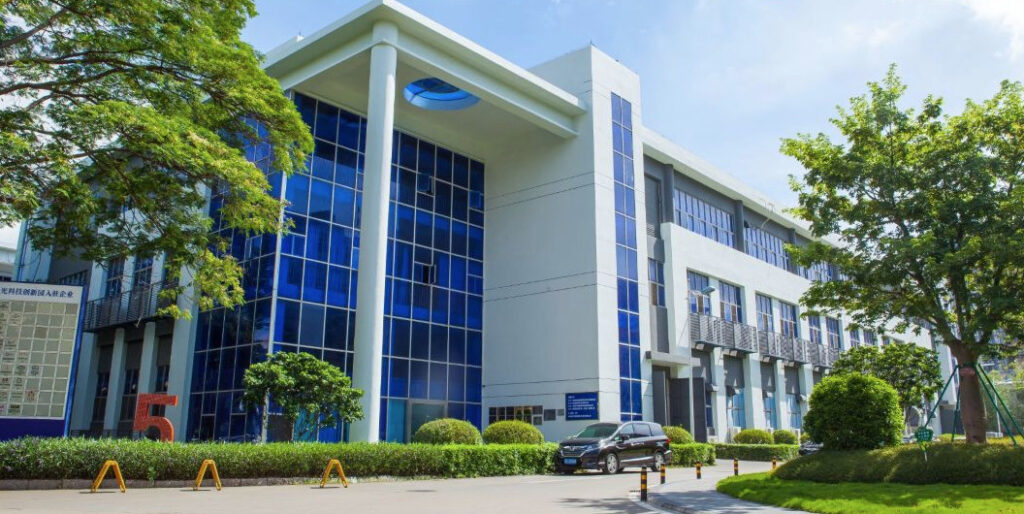
Factory Evaluation: Due Diligence and Audits
Before finalizing a partnership, conduct due diligence to verify the factory’s reliability. On-site or virtual audits provide insights into their operations and culture.
- Facility Audit: Assess machine conditions, cleanliness, and workflow. Modern factories use ERP systems to track production, indicating efficiency.
- Reference Checks: Request case studies or client testimonials. For example, a factory serving aerospace clients likely maintains high standards.
- Trial Orders: Start with a small batch (e.g., 10 parts) to evaluate quality, communication, and delivery. This minimizes risk before committing to larger orders.
- Financial Stability: Ensure the factory is financially sound to avoid disruptions. Public records or credit reports can provide insights.
Key Parameter: During audits, confirm the factory’s calibration records for inspection equipment, updated at least annually to ensure accuracy.
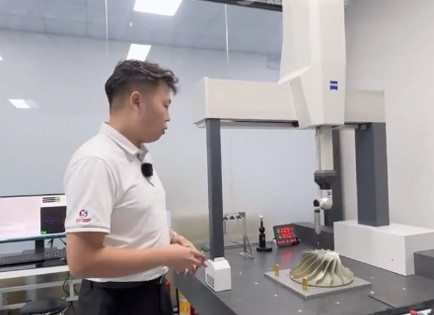
Kesu: Precision Perfected, Every Time
Kesu is your trusted partner for precision CNC machining. We combine cutting-edge technology with unparalleled expertise to deliver flawless parts that meet your exact specifications. From прототипирование to high-volume production, we ensure uncompromising quality, reliable lead times, and transparent communication every step of the way. Experience the Kesu difference—where accuracy and efficiency drive your success.
Заключение
In conclusion, selecting a reliable CNC factory requires a systematic evaluation of quotation accuracy, technical capabilities, quality assurance, production capacity, supply chain management, communication, cost, and overall reliability. By prioritizing these criteria and verifying them through audits and trial orders, you can establish a trusted partnership that delivers high-quality parts on time and within budget.