Precision machining is a specialized manufacturing technology that produces parts with exceptional dimensional accuracy, superior surface quality, and extremely tight tolerances. It is a critical process in industries requiring high-performance components, such as aerospace, automotive, electronics, medical devices, and optical systems. Unlike conventional machining, precision machining achieves tolerances in the micrometer (μm) or nanometer (nm) range, with surface roughness values as low as Ra 0.1 μm or below. This comprehensive guide explores the definition, key characteristics, major process types, applications, and technical complexities of precision machining, providing a detailed, technical perspective on its role in modern manufacturing.
The importance of precision machining lies in its ability to meet the stringent requirements of advanced industries. Components produced through these methods must adhere to exact specifications to ensure functionality, reliability, and safety. This article delves into the intricacies of precision machining, offering a systematic and professional analysis supported by specific parameters and examples, while maintaining a clear and structured format for accessibility and understanding.
Definition of Precision Machining
Precision machining encompasses a range of manufacturing processes that remove material (through cutting, grinding, or erosion) or reshape materials (via forming or additive methods) to create parts with high dimensional accuracy and surface quality. The hallmark of precision machining is its ability to achieve tolerances as tight as ±0.001 mm (1 μm) and surface roughness values below Ra 0.1 μm. This level of precision is made possible through the use of advanced computer numerical control (CNC) machines, high-precision tools, and sophisticated measurement systems.
Unlike traditional machining, which may tolerate deviations in the range of ±0.1 mm, precision machining operates at micro- and nanoscale levels, making it suitable for producing complex, high-value components. The process integrates advanced technologies, such as CNC systems, computer-aided design (CAD), and computer-aided manufacturing (CAM), to execute highly controlled operations. Real-time monitoring and feedback systems further ensure dimensional accuracy and surface quality during production, minimizing errors and ensuring consistency.
Precision machining is typically employed in applications where even minor deviations can lead to significant performance issues or product failure. For example, in aerospace, a turbine blade with a dimensional error of just a few micrometers could compromise engine efficiency, while in medical devices, imprecise components could affect patient safety. The reliance on precision machining underscores its critical role in modern manufacturing.
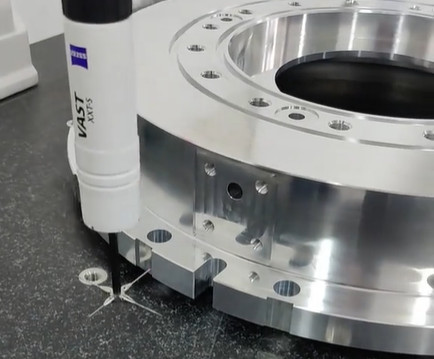
Key Characteristics of Precision Machining
Precision machining is distinguished by several core characteristics that enable it to meet the demanding requirements of high-tech industries. These attributes highlight its technical sophistication and versatility.
- High Accuracy: Precision machining achieves dimensional tolerances ranging from ±0.001 mm to ±0.0001 mm (0.1 μm). This level of accuracy is essential for components requiring precise fits, such as aerospace turbine blades impellers or semiconductor wafer molds, where deviations can lead to functional failures.
- Superior Surface Quality: The process produces surfaces with roughness values as low as Ra 0.025 μm, reducing or eliminating the need for secondary finishing operations like polishing. This is critical for applications such as optical lenses or medical implants, where surface smoothness directly impacts performance.
- Complex Geometries: Precision machining can create intricate three-dimensional shapes, micro-features (e.g., holes or slots with diameters below 0.1 mm), and high-aspect-ratio structures. This capability is vital for producing complex components like turbine impellers or microfluidic chips.
- Material Versatility: The process accommodates a wide range of materials, including metals (e.g., aluminum alloys, титан, stainless steel), ceramics, composites, and engineering plastics. This versatility allows precision machining to serve diverse industries with varying material requirements.
- Automation and Intelligence: Precision machining integrates CNC systems, CAD/CAM software, and in-process inspection technologies to ensure high efficiency, repeatability, and quality control. Automated systems reduce human error and enable consistent production of complex parts.
- High Cost: The use of advanced equipment, specialized tools (e.g., diamond or cubic boron nitride), and controlled environments (e.g., temperature-regulated workshops) results in higher costs. This makes precision machining ideal for high-value, low-volume production where quality outweighs cost considerations.
These characteristics collectively enable precision machining service to deliver components that meet the rigorous standards of advanced industries, ensuring reliability, performance, and safety.
Major Types of Precision Machining Processes
Precision machining service encompasses a variety of processes, each tailored to specific applications, materials, and accuracy requirements. The following sections detail the primary techniques, their mechanisms, and their applications.
Precision Cutting
Precision cutting involves removing material using rotating tools or workpieces to achieve high accuracy and surface quality. It is one of the most widely used precision machining service methods due to its versatility and efficiency. Key processes include:
- CNC Turning: In CNC turning, a workpiece rotates while a fixed cutting tool shapes features such as cylindrical surfaces, internal bores, or threads. Modern CNC lathes achieve tolerances of ±0.002 mm (IT5-IT6) and surface roughness of Ra 0.1 μm. Applications include the production of shafts, bushings, and threaded components for automotive and aerospace industries. For example, a stainless steel shaft for an aircraft landing gear requires roundness within 0.002 mm to ensure proper fit and function.
- CNC Milling: This process uses rotating multi-point tools to machine flat surfaces, grooves, or complex contours. CNC milling machines, particularly those with five-axis capabilities, can produce intricate parts with tolerances as tight as ±0.005 mm and surface roughness of Ra 0.2 μm. They are widely used for manufacturing molds, dies, and aerospace components like structural brackets.
- Five-Axis Machining: Пятиосевая обработка allows simultaneous movement along five axes (X, Y, Z, and two rotational axes), enabling the production of complex three-dimensional shapes. This method achieves tolerances below ±0.01 mm and is used for parts like turbine blades or impeller geometries in aerospace engines. For instance, a titanium alloy turbine blade may require a profile tolerance of ±0.005 mm to ensure aerodynamic performance.
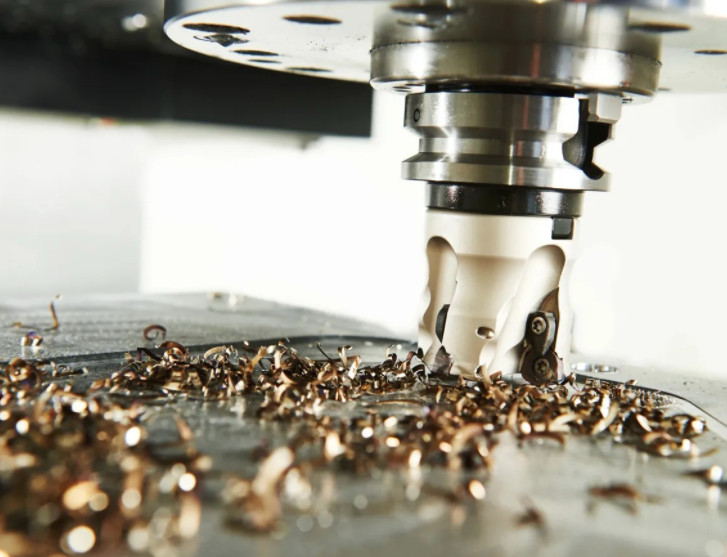
Прецизионное шлифование
Grinding uses abrasive wheels to remove minute amounts of “material, achieving superior surface finishes and tight tolerances. It is often employed for finishing operations or machining hard materials. Key grinding processes include:
- Шлифование поверхности: This process produces flat surfaces with roughness values as low as Ra 0.025 μm and flatness within 0.001 mm. It is used for precision dies, gauges, and machine bases. For example, a steel mold for plastic injection requires a surface finish of Ra 0.05 μm to ensure smooth part release.
- Cylindrical Grinding: This shapes cylindrical parts like bearings, shafts, or rollers, achieving roundness within 0.001 mm and surface roughness of Ra 0.05 μm. It is critical for components requiring high dimensional stability, such as automotive crankshafts.
- Ultra-Precision Grinding: Using diamond or cubic boron nitride (CBN) wheels, this process machines hard materials like ceramics or carbides with nanoscale accuracy. It is used for optical components, achieving surface roughness below Ra 0.01 μm, as seen in the production of infrared lenses.
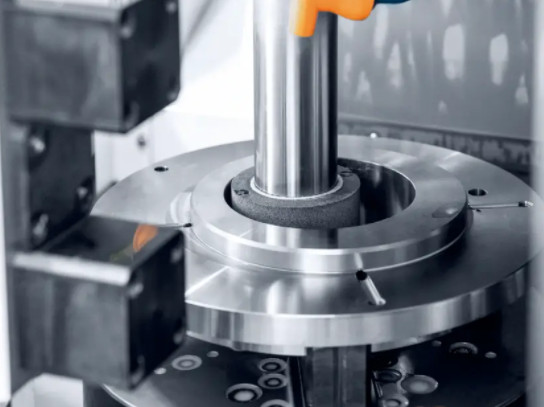
Электроэрозионная обработка (EDM)
EDM uses electrical sparks to erode material, making it ideal for hard metals or intricate shapes that are difficult to machine with conventional tools. The process achieves tolerances of ±0.005 mm and is used for mold cavities, micro-holes (e.g., 0.1 mm diameter), and complex dies. For example, EDM is employed to create fuel injector nozzles with hole diameter tolerances of ±0.001 mm. However, EDM is slower than mechanical cutting, making it suitable for low-volume, high-precision tasks.
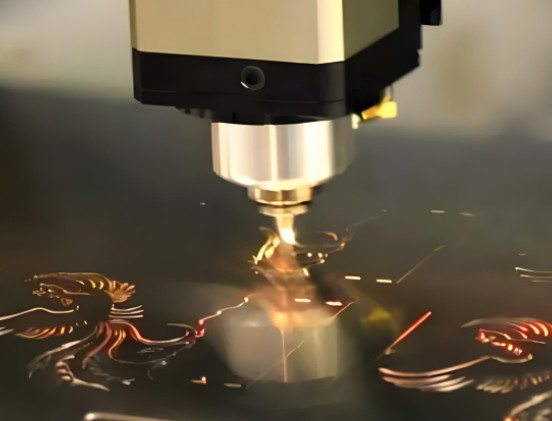
Laser Machining
Laser machining employs focused laser beams for cutting, drilling, or surface treatment. It offers non-contact processing, eliminating mechanical stress, and achieves feature sizes as small as 10 μm with tolerances of ±0.002 mm. This method is ideal for brittle materials like glass or ceramics and is widely used in microelectronics (e.g., circuit board drilling) and medical device manufacturing (e.g., stent cutting). For instance, laser machining can create micro-holes in a ceramic substrate with a diameter accuracy of ±0.001 mm.
Ultra-Precision Machining
Ultra-precision machining pushes accuracy to the nanoscale, often requiring specialized tools and controlled environments. Key techniques include:
- Single-Point Diamond Turning: This uses diamond-tipped tools to machine optical surfaces, achieving roughness below Ra 0.01 μm and form accuracy within 0.1 μm. It is used for lenses, mirrors, and infrared optics, such as telescope mirrors requiring surface flatness below 0.01 μm.
- Chemical Mechanical Polishing (CMP): CMP combines chemical etching and mechanical polishing to achieve surface flatness within 0.5 nm. It is critical for semiconductor wafers, ensuring planarity for integrated circuit fabrication.
- Ion Beam Machining: This uses ion beams to etch materials with sub-nanometer precision, suitable for micro- and nanostructures in optics and electronics. For example, ion beam machining can create diffraction gratings with feature sizes below 10 nm.
Аддитивное производство
Precision additive manufacturing, such as stereolithography (SLA) or selective laser sintering (SLS), builds parts layer by layer with resolutions as fine as 10 μm. These methods are used for complex geometries in aerospace (e.g., lightweight lattice structures) and medical applications (e.g., custom implants). For instance, SLA can produce microfluidic chips with channel widths of 50 μm, complementing subtractive precision machining service for hybrid manufacturing approaches.
Applications of Precision Machining
Precision machining is integral to industries requiring high-performance components with stringent specifications. The table below summarizes key applications, example components, and precision requirements.
Промышленность | Приложения | Example Components | Precision Requirements |
---|---|---|---|
Аэрокосмическая промышленность | Turbine blades, engine components, satellite parts | Titanium alloy blades | Tolerances ±0.005 mm, Ra 0.1 μm |
Автомобили | Engine blocks, crankshafts, fuel injectors | Fuel injector nozzles | Hole diameter ±0.001 mm |
Electronics/Semiconductor | Chip molds, MEMS, optical components | Semiconductor wafers | Surface roughness Ra 0.01 μm |
Медицинские приборы | Implants, surgical tools, microfluidic chips | Orthopedic screws | Thread tolerance ±0.002 mm |
Optics | Lenses, mirrors, laser components | Telescope mirrors | Surface flatness <0.01 μm |
In aerospace, precision machining produces turbine blades with tolerances of ±0.005 mm to ensure aerodynamic efficiency. In the automotive industry, fuel injector nozzles require hole diameter tolerances of ±0.001 mm for optimal fuel delivery. Semiconductor manufacturing relies on CMP to achieve wafer flatness within 0.5 nm, while medical devices like orthopedic screws demand thread tolerances of ±0.002 mm for secure implantation. Optical systems, such as telescope mirrors, require surface flatness below 0.01 μm to ensure accurate light reflection.
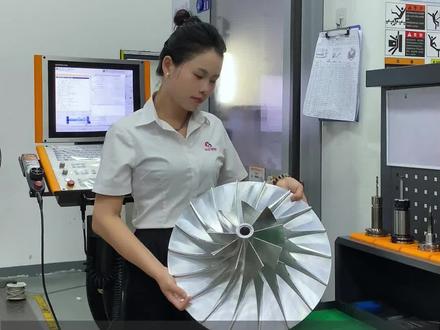
Technical Complexities in Precision Machining
Precision machining service involves several technical complexities that must be addressed to achieve desired outcomes. These challenges stem from equipment, materials, and process control requirements.
- Equipment and Tooling: High-precision CNC machines, such as ultra-precision lathes costing over $500,000, require regular maintenance to maintain accuracy. Tools like diamond or CBN cutters must maintain edge sharpness within 0.1 μm to prevent defects. The high cost and maintenance demands limit accessibility for smaller manufacturers.
- Thermal and Vibrational Effects: Heat generated during machining service can cause thermal expansion, leading to dimensional errors. For example, a temperature change of 1°C can cause a 10 μm expansion in a 1-meter steel part. Vibration from machine tools can also introduce errors, requiring temperature-controlled environments (±0.1°C) and vibration-dampening systems to maintain tolerances below ±0.001 mm.
- Material Challenges: Hard materials like titanium alloys or ceramics increase tool wear and machining difficulty. Titanium’s low thermal conductivity causes heat buildup, necessitating specialized cooling systems. Ceramics, being brittle, require low-force techniques like laser machining to prevent cracking.
- Measurement and Inspection: Verifying micro- and nanoscale tolerances requires advanced tools like laser interferometers or coordinate measuring machines (CMMs), which can detect deviations as small as 0.1 μm. These systems are costly and require skilled operators to ensure accurate measurements.
- Process Stability: Maintaining consistent cutting parameters (e.g., spindle speed, feed rate) is critical. For example, a variation of 0.01 mm/s in feed rate can cause defects in high-precision parts. Advanced control systems and real-time monitoring are essential to ensure process stability.
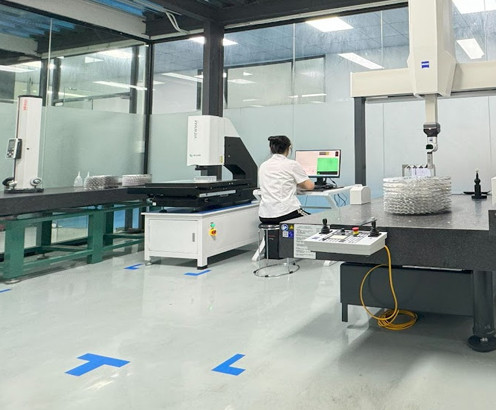
Kesu Precision Machining: Your Partner in Excellence
At Kesu, we redefine precision machining with cutting-edge technology and unmatched expertise, delivering components with micro-level accuracy and superior quality. Kesu is a top-notch custom parts manufacturing provider offering high-quality and precision machining services. In CNC precision machining Kesu is among the top manufacturer of machine parts all over the world and in China they are the top 5 best service providers of CNC precision machining parts.
Заключение
Precision machining is a cornerstone of modern manufacturing, enabling the production of high-accuracy, high-quality components for critical applications. Through processes like CNC cutting, grinding, EDM, laser machining, ultra-precision techniques, and additive manufacturing, it meets the stringent demands of industries such as aerospace, automotive, electronics, medical devices, and optics. Despite challenges like high equipment costs, material difficulties, and the need for precise process control, precision machining delivers unmatched performance for complex, high-value parts. Its ability to achieve tolerances as tight as ±0.001 mm and surface roughness below Ra 0.1 μm ensures its indispensability in high-tech manufacturing. For further details on specific processes or applications, consulting technical resources or industry experts is recommended.
Frequently Asked Questions (FAQs) About Precision Machining
What is precision machining, and how does it differ from traditional machining?
Precision machining is a set of manufacturing processes that produce parts with extremely tight tolerances (often ±0.001 mm or tighter) and superior surface quality (surface roughness as low as Ra 0.1 μm or below). It uses advanced technologies like CNC systems, high-precision tools, and real-time monitoring to achieve micro- or nanoscale accuracy.
In contrast, traditional machining typically tolerates larger deviations (±0.1 mm or more) and focuses on general shaping rather than microscale precision. Precision machining is critical for industries where even minor errors can cause failure, such as aerospace or medical devices.
What are the key characteristics of precision machining?
Precision machining is defined by:
High accuracy: Tolerances as tight as ±0.0001 mm (0.1 μm).
Superior surface quality: Surface roughness below Ra 0.1 μm (often Ra 0.025 μm or lower).
Complex geometry capability: Production of intricate 3D shapes, micro-features (e.g., 0.1 mm diameter holes), and high-aspect-ratio structures.
Универсальность материалов: Compatibility with metals (titanium, stainless steel), ceramics, composites, and engineering plastics.
Автоматизация: Integration of CNC, CAD/CAM, and in-process inspection for consistency.
Более высокая стоимость: Due to advanced equipment, specialized tools, and controlled environments.
What are the main types of precision machining processes?
Key processes include:
Precision cutting: CNC turning (cylindrical parts), CNC milling (complex contours), and five-axis machining (intricate 3D shapes).
Precision grinding: Surface grinding (flatness), cylindrical grinding (round parts), and ultra-precision grinding (nanoscale accuracy with diamond wheels).
Электроэрозионная обработка (EDM): Uses electrical sparks to erode hard materials, ideal for micro-holes or complex dies.
Laser machining: Non-contact processing for brittle materials (glass, ceramics) with feature sizes as small as 10 μm.
Ultra-precision machining: Techniques like single-point diamond turning (optical surfaces) or ion beam machining (sub-nanometer precision).
Аддитивное производство: Layer-by-layer 3D printing (e.g., SLA, SLS) with resolutions as fine as 10 μm.
What technical challenges are involved in precision machining?
Key complexities include:
Equipment costs: High-precision CNC machines and tools (e.g., diamond cutters) can exceed $500,000, with strict maintenance requirements.
Thermal/vibrational effects: Temperature fluctuations (even 1°C) or vibrations can cause dimensional errors, requiring controlled environments (±0.1°C) and vibration-dampening systems.
Material difficulties: Hard materials (titanium, ceramics) increase tool wear and require specialized cooling or low-force techniques.
Measurement demands: Verifying micro/nanoscale tolerances requires advanced tools like laser interferometers or CMMs (capable of detecting 0.1 μm deviations).
Process stability: Maintaining consistent parameters (e.g., feed rate) is critical, as small variations (0.01 mm/s) can cause defects.
Can precision machining be used for high-volume production?
While precision machining is often associated with low-volume, high-value parts (due to high costs), it can be scaled for moderate volumes using automated CNC systems and standardized processes. However, high-volume production may require optimizing tooling, reducing setup times, or combining with additive manufacturing for hybrid approaches to balance precision and efficiency.
Which industries rely on precision machining, and what are typical applications?
Precision machining is critical in:
Аэрокосмическая промышленность: Turbine blades (tolerances ±0.005 mm), engine components, and satellite parts.
Автомобили: Fuel injector nozzles (hole tolerance ±0.001 mm), crankshafts, and engine blocks.
Electronics/semiconductors: Semiconductor wafers (surface flatness within 0.5 nm) and microcircuit components.
Medical devices: Orthopedic screws (thread tolerance ±0.002 mm), surgical tools, and microfluidic chips.
Optics: Telescope mirrors (surface flatness <0.01 μm), lenses, and laser components.