Honing machining is a specialized low-speed grinding process used for high-precision surface finishing. It is an efficient method for achieving superior surface quality and dimensional accuracy, particularly for holes, but also for flat, spherical, and cylindrical surfaces. This article provides a systematic and technical exploration of honing machining, covering its characteristics, principles, tools, parameters, and applications, with a focus on practical and professional insights.
Characteristics of Honing Machining
Honing machining is distinguished by its versatility, precision, and ability to produce high-quality surfaces. Below are its key characteristics:
- Wide Processing Range: Honing is primarily used for finishing holes, including cylindrical, stepped, blind, and conical holes. It can also be applied to flat surfaces, spherical surfaces, and external cylindrical surfaces. The process accommodates hole diameters from 1 mm to over 1200 mm and lengths up to 12,000 mm, making it suitable for nearly all workpiece materials.
- High Surface Quality: Honing produces a cross-hatched surface pattern, which enhances lubricant retention and extends component life due to improved wear resistance. The low cutting speed—typically a fraction of conventional grinding—minimizes grinding forces and heat, preventing surface burns, cracks, or metallurgical changes.
- High Processing Accuracy: Honing achieves roundness and cylindricity within 0.005–0.01 mm and surface roughness values (Ra) of 0.05–0.2 μm. While it excels in dimensional accuracy, it does not improve positional accuracy, making it a suitable replacement for some grinding processes with comparable efficiency.
- Low Machine Tool Requirements: Honing can be performed on dedicated honing machines or adapted to lathes, boring machines, or drilling machines, reducing dependency on high-precision equipment.
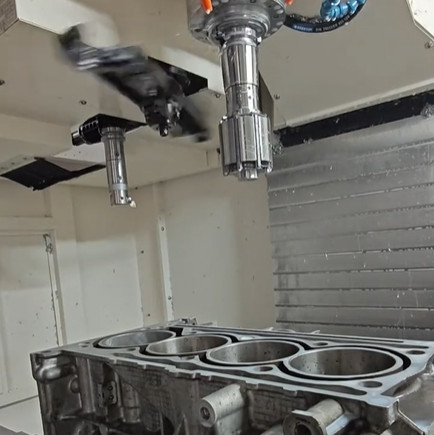
Principles of Honing Machining
Honing machining involves the use of a honing head equipped with multiple oilstones arranged circumferentially. These oilstones are radially expanded by an expansion mechanism to contact the workpiece surface, typically the inner wall of a hole, under controlled pressure. The honing head (or workpiece) rotates and reciprocates, creating a low-speed grinding action. Key aspects of the honing principle include:
- Floating Connection: To mitigate misalignment between the machine spindle and workpiece center, the honing head is connected to the spindle via a floating mechanism. This allows the workpiece hole to guide the honing process, ensuring precision.
- Cross-Hatched Pattern: The simultaneous rotation and reciprocation of the honing head produce a spiral cutting trajectory, resulting in a cross-hatched surface pattern. This non-repetitive motion ensures uniform interference and continuous refinement of the surface, improving roundness, cylindricity, and surface roughness.
- Self-Correcting Process: During honing, the oilstones and workpiece surface mutually correct each other. As interference points are gradually removed, dimensional accuracy improves until the desired specifications are achieved.
Structure of Honing Heads
The honing head is a critical component that directly influences machining accuracy, efficiency, and surface quality. Its design must ensure uniform expansion, effective coolant flow, and easy chip removal. The typical structure includes:
- Honing Head Body: The main framework that houses other components.
- Oilstone Holder: Secures the oilstones and facilitates their radial movement.
- Oilstones: The abrasive tools responsible for material removal.
- Guide Strips: Ensure alignment and stability during machining.
- Spring and Tapered Core: Control the radial expansion of oilstones for consistent pressure.
Honing heads are designed based on workpiece geometry and include variations such as constant-pressure expansion, stepped-hole honing, manual expansion, universal joint types, single-oilstone, split-tile, blind-hole, and conical-hole honing heads. Proper design ensures uniform oilstone expansion, accurate positioning, and efficient chip and coolant management.
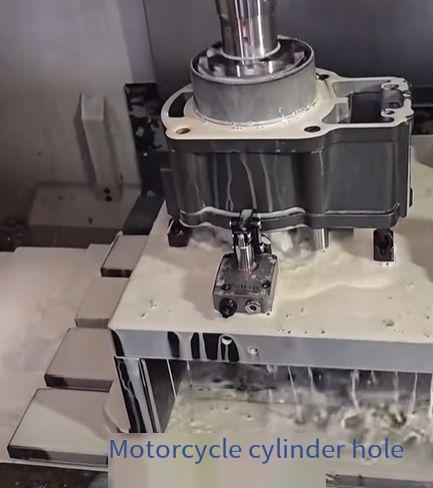
Selection of Oilstones
The choice of oilstones is critical for achieving desired machining outcomes. Key considerations include:
Abrasive Material
Oilstones are made from abrasives such as corundum, carbides, synthetic diamond, or cubic boron nitride (CBN). Synthetic diamond and CBN are preferred for modern applications due to their exceptional hardness (3–4 times that of corundum or carbides), durability, sharp cutting edges, and cost-effectiveness. For small holes (a few millimeters), metal-bonded or electroplated oilstones are used, while resin-bonded oilstones are common for larger applications.
Grain Size
The abrasive grain size determines surface roughness and machining efficiency. The following table summarizes the relationship between grain size and surface roughness:
Grain Size | Surface Roughness (Ra, μm) | Application |
---|---|---|
F120–F150 | 0.8 | Rough honing |
F150–F240 | 0.4 | Semi-finish honing |
F240–W20 | 0.05–0.2 | Finish honing |
Bond and Concentration
Resin bonds are widely used for their flexibility, while ceramic bonds were common in older applications. For superabrasives like diamond and CBN, concentration (abrasive mass per cubic centimeter) is critical. Common concentrations are 75% (3.13 ct/cm³) and 100% (4.4 ct/cm³), balancing cost and performance.
Oilstone Dimensions
Oilstone width and length are chosen based on workpiece material and geometry:
- Hard Materials: Narrower oilstones to reduce cutting forces.
- Soft or Plastic Materials: Wider oilstones to improve chip evacuation.
- Brittle Materials: Wider oilstones for stability.
- Length: Typically 1.0–1.5 times the hole diameter for general holes, or 1/2–2/3 of the hole length for small holes. Excessive length increases mass but improves guidance, while short oilstones may compromise cylindricity.
The total oilstone width should be 15–28% of the hole circumference to balance efficiency and surface quality.
Honing Parameters
Honing parameters are carefully selected to optimize machining outcomes. Key parameters include:
Resultant Cutting Speed (vc)
The resultant cutting speed is a combination of circumferential speed (v, 20–60 m/min) and reciprocating speed (va, 18–25 m/min), producing a cross-hatch angle (θ) of 40°–90°. The resultant speed typically ranges from 18–35 m/min, creating the characteristic cross-hatched surface pattern.
Oilstone Working Pressure
The pressure exerted by oilstones on the workpiece surface varies by machining stage:
- Rough Honing: 0.2–0.5 MPa
- Ultra-Finish Honing: 0.05–0.1 MPa
Feed Rate
The radial feed rate depends on material hardness, abrasive grain size, and machining stage:
- Rough Honing: 1.8–3.2 μm/r
- Finish Honing: 0.1–1.5 μm/r
Stroke Length and Overrun
The stroke length (l) is calculated as l = L + 2a – l1, where L is the workpiece length, a is the overrun (1/5–1/3 of oilstone length l1), and l1 is the oilstone length. Proper overrun ensures uniform cylindricity.
Honing Allowance
The honing allowance depends on prior machining errors and production volume:
- Single-Piece Production: 0.04–0.1 mm
- Batch Production: 0.02–0.06 mm
The allowance is typically 2–2.5 times the total error from the previous process.
Honing Fluid
Honing fluid provides cooling, lubrication, and chip removal. Common formulations include:
- Steel: 80–90% kerosene + 10–20% spindle oil, or 55% kerosene + 40% oleic acid + 5% turpentine.
- Cast Iron: Kerosene, or kerosene + 10–20% spindle oil.
- Bronze/Aluminum Alloys: Kerosene.
Fluids must be filtered to prevent surface scratches. These formulations also apply to wheel honing.
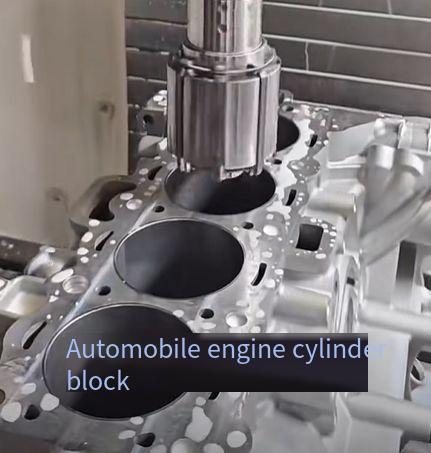
Wheel Honing Machining
Wheel honing is a variant of honing used for finishing internal and external cylindrical surfaces, such as shafts, rollers, sleeves, and bearing raceways. It employs fine-grained abrasive wheels under elastic pressure for low-speed grinding.
Principles of Wheel Honing
In wheel honing, the workpiece rotates, driving the honing wheel(s) passively. The wheel axis intersects the workpiece axis at 27°–35°, and axial feed under spring pressure facilitates low-speed grinding. Single-wheel, double-wheel, or multi-wheel configurations are used, with double-wheel setups shown for external cylindrical surfaces.
Characteristics of Wheel Honing
- Surface Quality: Achieves Ra values of 6.3–12.5 μm in one pass, reducible to 0.2–1.6 μm with multiple passes.
- Durability: Enhances wear and corrosion resistance.
- Low Prior Process Requirements: Requires only 0.03–0.1 mm allowance, suitable for difficult-to-grind parts like slender shafts or long cylinders.
- Versatility: Applicable to various materials, including steel, cast iron, and hard alloys, and adaptable to lathes, milling machines, or boring machines.
Wheel Honing Tools
Wheel honing tools vary by production volume and workpiece size. Single-wheel tools are simple and versatile, while double- or multi-wheel tools are used for high-volume production. Abrasives include white corundum (F150–F240) for general use, or boron carbide, diamond, or CBN for hard materials. Resin-bonded wheels are common, and wheels are machined with PCD tools to ensure concentricity.
Wheel Honing Parameters
Key parameters include:
- Speed (vc): 50–60 m/min, or up to 150 m/min with rolling bearings.
- Feed Rate: 1–3 mm/r to maintain surface quality.
- Honing Allowance: 0.05–0.1 mm.
- Contact Pressure: 50–200 MPa to avoid bearing overheating.
Honing Fluid and Considerations
The same honing fluids as bar honing are used. If continuous fluid application is not possible, grinding paste with oleic acid can be applied. Issues like poor wheel-workpiece contact or surface waviness can be addressed by ensuring coaxiality or flipping the wheel 180°.
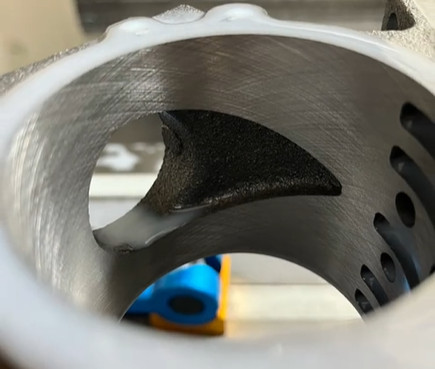
Conclusion
Honing machining is a highly effective finishing process known for its simplicity, precision, and versatility. Its ability to achieve excellent surface quality and dimensional accuracy with minimal equipment requirements makes it a valuable technique in industries requiring high-precision components. By understanding the principles, tools, and parameters outlined in this article, manufacturers can optimize honing processes for a wide range of applications.