Extrusion taps, also known as thread-forming taps, have emerged as a significant advancement in deep-hole threading processes. Unlike traditional cutting taps, which remove material to form threads, extrusion taps deform the material to create threads without producing chips. This article provides a comprehensive analysis of the advantages and limitations of extrusion taps in deep-hole threading, based on practical experience and experimental data. It aims to serve as a technical reference for manufacturers considering the adoption of extrusion taps.
Introduction to Extrusion Taps
In deep-hole threading, traditional cutting taps often face challenges such as early wear, chipping, or breakage due to poor cooling or chip evacuation. These issues lead to frequent tool changes, reduced tool life, and inconsistent thread quality. Extrusion taps address these challenges by forming threads through plastic deformation, eliminating chip production and offering distinct advantages in tool life, efficiency, cost, and thread quality. However, their application is constrained by specific equipment and material requirements, which must be carefully evaluated.
This article draws on practical experience with extrusion taps in a manufacturing setting, focusing on their performance in threading blind holes with depths up to 70 mm. The following sections detail the advantages and limitations of extrusion taps, supported by experimental data and technical insights.
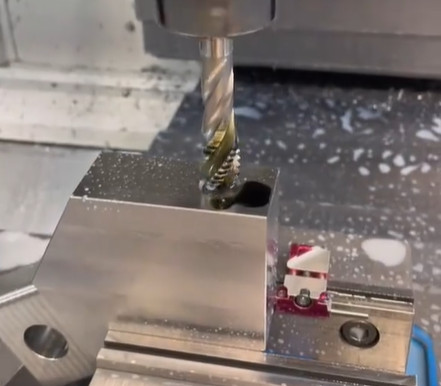
Advantages of Extrusion Taps
Extrusion taps offer several benefits over cutting taps, particularly in deep-hole and blind-hole threading applications. These advantages include extended tool life, improved machining efficiency, reduced costs, and enhanced thread quality.
Extended Tool Life
One of the most significant advantages of extrusion taps is their extended tool life. In a specific case study involving a product with six 70 mm deep blind holes requiring internal threads, traditional cutting taps exhibited short tool life and frequent failures. Despite various improvements, cutting taps could not meet the desired durability targets.
Extrusion taps from reputable domestic and international brands were tested in batches. The results showed a remarkable improvement, with some extrusion taps achieving a tool life over 40 times that of cutting taps. This improvement stems from the unique wear mechanism of extrusion taps. When the front cutting edge of an extrusion tap wears, adjacent calibration teeth take over, adding one more tooth to the forming process. This allows the tap to continue producing complete threads, albeit with a slightly reduced effective thread depth. The primary failure mode is thread size reduction, which is less catastrophic than the chipping or breakage common with cutting taps.
Wear on extrusion taps typically manifests as minor edge damage, which does not immediately affect performance. As the thread size decreases, operators can detect increased machine torque or abnormal sounds, allowing timely tool replacement before quality issues arise.
Improved Machining Efficiency
Extrusion taps significantly enhance machining efficiency due to their extended tool life and higher processing speeds. In the case study, the frequency of tool changes dropped dramatically. Cutting taps required multiple replacements daily, whereas extrusion taps needed replacement only once every few days, reducing downtime and increasing throughput.
Additionally, extrusion taps can operate at higher spindle speeds than cutting taps. In a machining center performing drilling, reaming, chamfering, and threading in a single setup, the use of extrusion taps reduced total machining time by 14%. This improvement translates to a corresponding 14% increase in production capacity for the threading operation, making extrusion taps a valuable tool for high-volume manufacturing.
Cost Reduction
Although extrusion taps have a higher initial cost than cutting taps, their extended tool life results in significant cost savings. In the case study, the per-part cost of using extrusion taps was at least 50% lower than that of cutting taps, despite the higher unit price. This cost advantage is particularly pronounced in challenging applications, such as deep-hole threading, blind-hole threading, or processing high-viscosity materials.
In easier machining conditions, cutting taps can achieve very low costs, and extrusion taps may not offer a significant advantage. However, in demanding scenarios, the durability and reliability of extrusion taps make them a cost-effective choice. The cost-benefit analysis depends on the specific application, but extrusion taps consistently outperform cutting taps in difficult threading tasks.
Enhanced Thread Quality
Extrusion taps produce threads with superior strength and quality compared to cutting taps. According to data from tool manufacturers, threads formed by extrusion are at least 20% stronger than cut threads. This strength increase results from the plastic deformation process, which densifies the material and induces cold work hardening, enhancing surface strength.
As a chipless process, extrusion tapping eliminates issues associated with chip residues in deep or blind holes, which can interfere with bolt engagement and damage threads during assembly. Even if an extrusion tap experiences minor tooth chipping, it does not result in defective threads, ensuring consistent quality. Major manufacturers are increasingly recognizing these benefits and recommending extrusion taps for new product designs requiring high-strength threads.
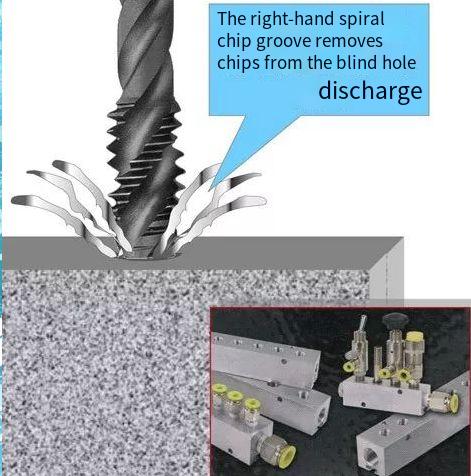
Limitations of Extrusion Taps
Despite their advantages, extrusion taps have specific limitations that must be addressed to ensure successful application. These include high equipment precision and torque requirements, inability to rework threads, unsuitability for brittle materials, restrictions on thread pitch, and strict requirements for pilot hole preparation.
High Equipment Precision and Torque Requirements
Extrusion taps require rigid tool holders to maintain alignment between the tap and the pilot hole. Poor equipment precision can lead to misalignment, causing uneven thread heights—excessive on one side and insufficient on the other. This misalignment can result in interference during bolt assembly, rendering the part unusable.
Torque requirements for extrusion taps are significantly higher than for cutting taps. For example, torque monitoring data for an M12×1.25 mm extrusion tap showed a torque increase of over 50% compared to a cutting tap, though still below the torque required for drilling. Most standard equipment can handle this torque, but larger thread pitches, such as M16×1.5 mm, may trigger spindle motor overload alarms. Before adopting extrusion taps, manufacturers must verify that their equipment can provide the necessary torque.
Inability to Rework Threads
Threads formed by extrusion taps cannot be easily reworked. If a thread is incomplete due to insufficient depth or a broken tap, manual reworking is not feasible. Machine-based reworking is challenging due to difficulties in achieving precise repositioning, which can lead to excessive deformation, tap breakage, or thread damage. If thread depth is inadequate, the part is typically scrapped. To avoid batch failures, the first piece produced with an extrusion tap must be carefully inspected.
Unsuitability for Brittle Materials
Extrusion taps rely on plastic deformation to form threads, making them unsuitable for brittle materials that lack sufficient ductility. Attempting to use extrusion taps on such materials can result in cracking or failure to form proper threads.
Restriction to Small Thread Pitches
Extrusion taps are generally limited to thread pitches of 3 mm or less. Larger pitches require excessive material deformation, which can cause internal tearing or demand torque levels beyond the capacity of standard equipment. This limitation restricts the use of extrusion taps in applications requiring coarse threads.
Strict Pilot Hole Requirements
The success of extrusion tapping depends heavily on the precision of the pilot hole. Tool manufacturers often recommend a pilot hole diameter calculated using the formula: D = Dn - 0.5P, where D is the pilot hole diameter, Dn is the nominal thread diameter, and P is the thread pitch. However, testing on 48MnV forged steel revealed that a modified formula, D = Dn - 0.6P, produced threads closer to the geometry of cut threads.
The pilot hole diameter must be controlled within a tolerance of ±0.05 mm. Deviations can lead to quality issues:
- Oversized pilot holes: Result in insufficient thread height, reducing thread strength.
- Undersized pilot holes: Cause excessive thread height, leading to crescent-shaped thread crests or complete crest closure, as shown in Figure 4 (not included here). This increases friction, potentially causing tap breakage or thread gauge failures during inspection.
Undersized pilot holes pose a greater risk, as they can lead to catastrophic failures, whereas oversized holes primarily affect thread strength.
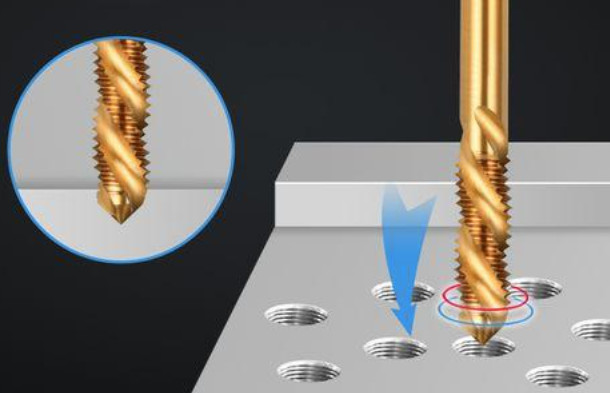
Practical Considerations
To maximize the benefits of extrusion taps, manufacturers must address the following considerations:
Aspect | Consideration |
---|---|
Equipment Selection | Ensure machines have sufficient torque and precision for rigid tool holding. |
Pilot Hole Preparation | Use precise drilling tools and verify pilot hole diameter based on material properties. |
Inspection Protocols | Implement rigorous first-piece inspections to verify thread depth and quality. |
Material Compatibility | Confirm that the workpiece material has sufficient ductility for thread forming. |
By addressing these factors, manufacturers can mitigate the limitations of extrusion taps and achieve consistent results.
Conclusion
Extrusion taps offer significant advantages in deep-hole and blind-hole threading, particularly for small-pitch threads in ductile materials. Their extended tool life, improved efficiency, reduced costs, and enhanced thread quality make them a valuable tool in challenging machining applications. However, their use requires careful consideration of equipment capabilities, pilot hole precision, and material properties. Through systematic testing and application, extrusion taps have proven to be a reliable and cost-effective solution, providing a practical reference for manufacturers seeking to optimize their threading processes.