Precision machining is a critical process in modern manufacturing, enabling the production of components with exceptional accuracy and surface quality. It serves as a foundation for industries requiring high-performance and reliable parts, such as aerospace, electronics, medical devices, and energy. By achieving tolerances at the micrometer and sub-micrometer levels, precision machining ensures components meet stringent functional demands.
Definition and Scope of Precision Machining
Precision machining refers to manufacturing processes that achieve dimensional accuracies of ±0.1μm to ±1μm, shape accuracies (e.g., roundness, straightness) of 0.05μm to 0.1μm, and positional accuracies (e.g., parallelism, perpendicularity) of 0.1μm to 0.2μm. Unlike conventional machining, which operates at millimeter-level tolerances and prioritizes basic shape and size, precision machining focuses on extreme precision and surface finishes as fine as Ra 0.02μm to Ra 0.1μm. This level of accuracy is essential for applications like optical lens manufacturing, where surface quality directly impacts optical performance.
The scope of precision machining includes a wide range of techniques, such as precision turning, milling, grinding, drilling, boring, and specialized methods like electrical discharge machining (EDM), laser machining, and electron/ion beam machining. Each technique is tailored to specific materials, geometries, and precision requirements, forming a versatile technical framework for advanced manufacturing.
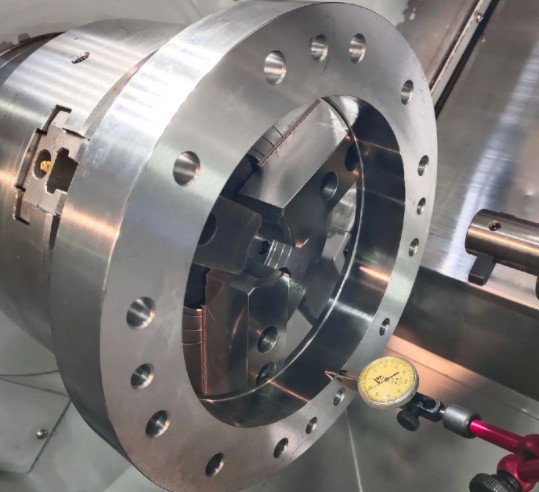
Importance of Precision Machining
Precision machining is vital in industries where component performance and reliability are critical. In aerospace, it ensures turbine blades withstand extreme temperatures and stresses while maintaining aerodynamic efficiency. In electronics, it enables the production of microchips with nanoscale features, driving advancements in computing power. In medical device manufacturing, precision machining produces surgical tools and implants with biocompatible surfaces, reducing patient risks. By delivering consistent, high-quality components, precision machining supports product performance across these sectors.
Factors Influencing Precision Machining Difficulty
The difficulty of precision machining is determined by several material properties:
- Hardness: Higher hardness increases tool wear and requires specialized cutting tools.
- Thermal Conductivity: Low thermal conductivity leads to heat accumulation, affecting tool life and surface integrity.
- Ductility: Ductile materials may form continuous chips, complicating chip evacuation.
- Brittleness: Brittle materials are prone to cracking, requiring careful control of cutting parameters.
- Machinability: A material’s response to cutting, influenced by its microstructure and composition.
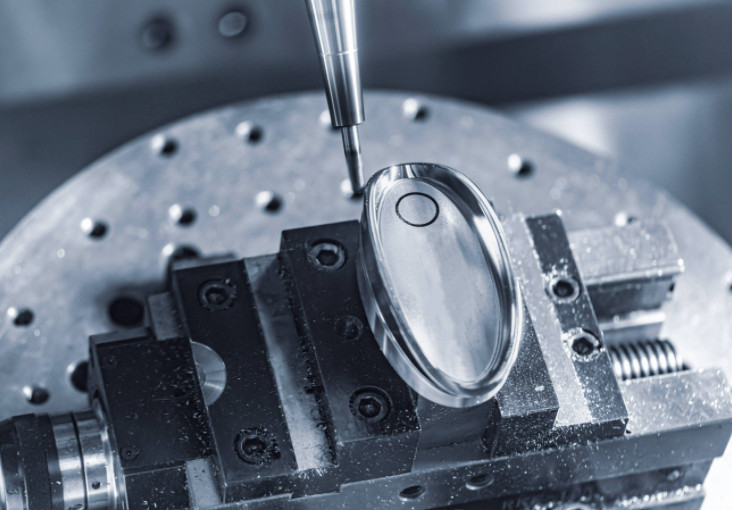
Precision Machining Difficulty by Material Type
The following sections detail the machining characteristics of various materials, focusing on their specific properties and the technical considerations required for precision machining.
Material Properties | Key Considerations |
---|---|
Metal - Aluminum Alloys (e.g., 6061-T6) Hardness: 95–100 HV Thermal Conductivity: 167 W/m·K Machining Difficulty: Low | High thermal conductivity allows faster cutting speeds. Softness can lead to burr formation, requiring sharp tools and high spindle speeds (e.g., 10,000–20,000 RPM). |
Metal - Stainless Steel (e.g., 304) Hardness: 200–250 HV Thermal Conductivity: 16 W/m·K Machining Difficulty: Moderate | Work hardening increases tool wear. Use coated carbide tools and moderate cutting speeds (e.g., 100–150 m/min) with coolant to manage heat. |
Metal - Titanium Alloys (e.g., Ti-6Al-4V) Hardness: 300–350 HV Thermal Conductivity: 6.7 W/m·K Machining Difficulty: High | Low thermal conductivity causes heat buildup, leading to tool wear. Requires low cutting speeds (e.g., 30–60 m/min) and high-pressure coolant (e.g., 70–100 bar). |
Metal - Inconel (e.g., 718) Hardness: 400–450 HV Thermal Conductivity: 11 W/m·K Machining Difficulty: Very High | High hardness and toughness cause rapid tool wear. Use ceramic or CBN tools with slow speeds (e.g., 20–40 m/min) and rigid machine setups. |
Ceramic - Silicon Carbide (SiC) Hardness: 2500–2800 HV Thermal Conductivity: 120 W/m·K Machining Difficulty: Very High | Brittle nature requires diamond tools and ultra-precision techniques like grinding or laser machining. Low feed rates (e.g., 0.01–0.05 mm/rev) minimize cracking. |
Ceramic - Alumina (Al2O3) Hardness: 1500–1800 HV Thermal Conductivity: 30 W/m·K Machining Difficulty: High | High hardness demands diamond-coated tools. Use low cutting depths (e.g., 0.1–0.5 mm) and vibration-assisted machining to reduce subsurface damage. |
Composite - Carbon Fiber Reinforced Plastics (CFRP) Hardness: ~100 HV (matrix, e.g., epoxy) Thermal Conductivity: 0.5–5 W/m·K Machining Difficulty: High | Risk of delamination and fiber pullout. Use high-speed spindles (e.g., 15,000–25,000 RPM) and polycrystalline diamond (PCD) tools with low feed rates (e.g., 0.02–0.1 mm/rev) to prevent material splitting. |
Composite - Glass Fiber Reinforced Plastics (GFRP) Hardness: ~100 HV (matrix) Thermal Conductivity: 0.5–5 W/m·K Machining Difficulty: Moderate | Less abrasive than CFRP, but fiber tear-out is a challenge. Use carbide tools with moderate speeds (e.g., 100–200 m/min) and coolant to reduce heat-induced matrix degradation. |
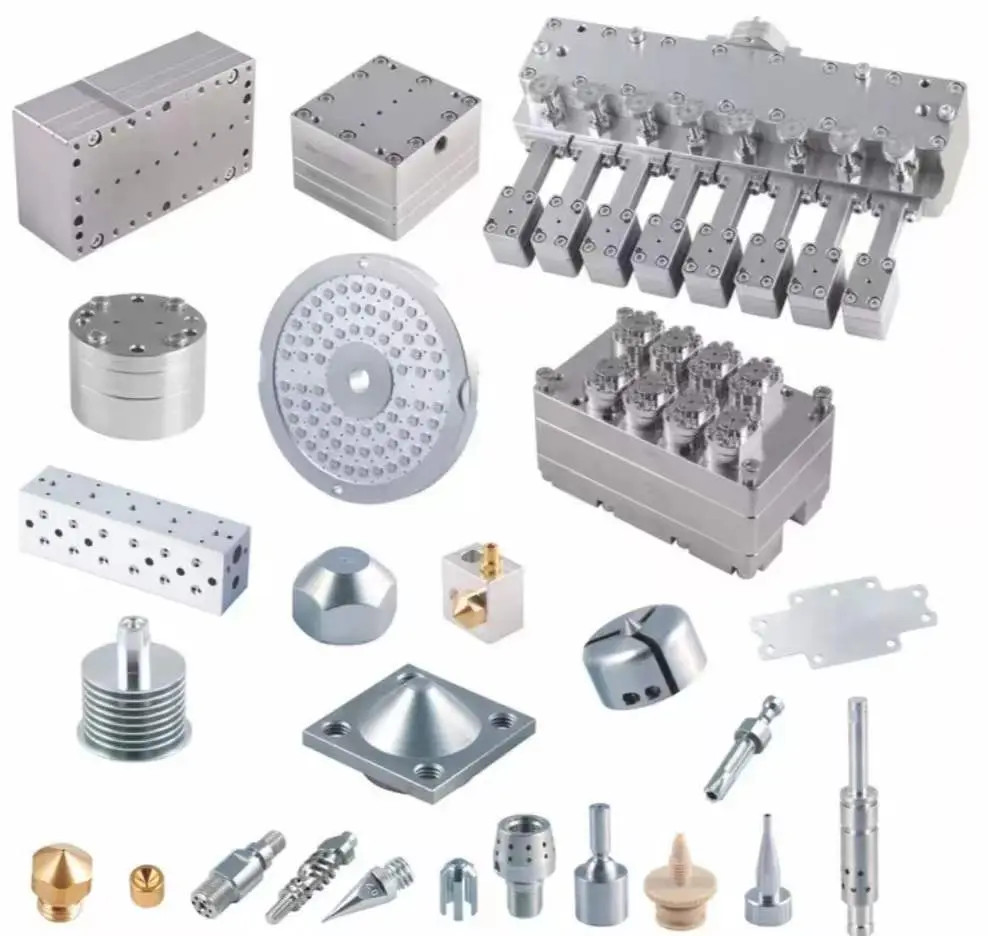
Types of Precision Machining
Precision machining techniques are categorized into cutting, grinding, and specialized processes. Each method employs distinct principles and tools to achieve the required precision, tailored to specific applications and materials.
Precision Cutting
Precision Turning: Precision turning involves rotating a workpiece on a lathe while a cutting tool removes material in a linear motion. High-precision spindles ensure rotational accuracy, and tools like cubic boron nitride (CBN) or diamond achieve superior surface finishes. This method is used for cylindrical parts, such as optical lenses (spherical or aspherical shapes) and precision shafts, with dimensional tolerances of ±0.1μm to ±1μm and surface roughness of Ra 0.05μm to Ra 0.2μm.
Precision Milling: Precision milling uses rotating multi-point cutters to shape complex surfaces, such as mold cavities or contours. Key considerations include cutter geometry, tooth count, and cutting parameters like speed and feed rate. In mold manufacturing, precision milling achieves tolerances of ±0.02mm to ±0.05mm for plastic or die-cast molds, with surface roughness of Ra 0.1μm to Ra 0.4μm. Cutter materials—hardened alloys for general metals, ceramics for high-speed cuts, or diamond for non-ferrous materials—impact precision and tool life.
Cutting Parameters: Parameters like cutting speed, feed rate, and depth of cut are critical. For example, machining aluminum alloys at high cutting speeds (e.g., 1000 m/min) and low feed rates (e.g., 0.05 mm/rev) minimizes cutting forces and heat, improving surface quality. Optimal parameter selection reduces workpiece deformation and enhances dimensional accuracy.
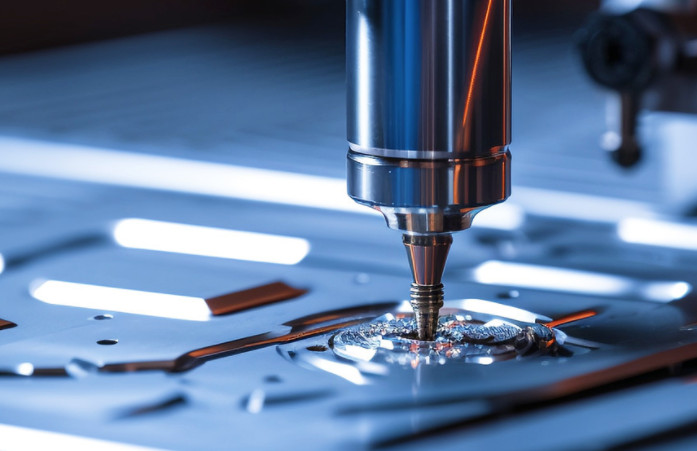
Precision Grinding
Precision grinding uses abrasive wheels to remove minute material layers, achieving tolerances of ±0.01μm to ±0.1μm and surface roughness of Ra 0.01μm to Ra 0.05μm. Abrasive grains (e.g., aluminum oxide for steel, silicon carbide for hard alloys) cut, scrape, and polish the workpiece surface. This process is ideal for components like precision screws, guide rails, and bearings, where extreme accuracy is required.
Wheel Selection and Dressing: The choice of grinding wheel—based on abrasive type, grain size, hardness, and bonding agent—determines machining quality. Fine-grain wheels produce smoother surfaces, while periodic dressing with diamond pens or rollers maintains wheel sharpness and geometry. For example, grinding hardened steel requires CBN wheels, while softer materials may use aluminum oxide.
Grinding Parameters: Key parameters include wheel speed, feed rate, and depth of cut. A wheel speed of 20-30 m/s, feed rate of 0.8-1 mm/s, and grinding depth of 0.005-0.01 mm optimize surface finish and dimensional accuracy. Parameter optimization minimizes thermal damage and ensures process stability.
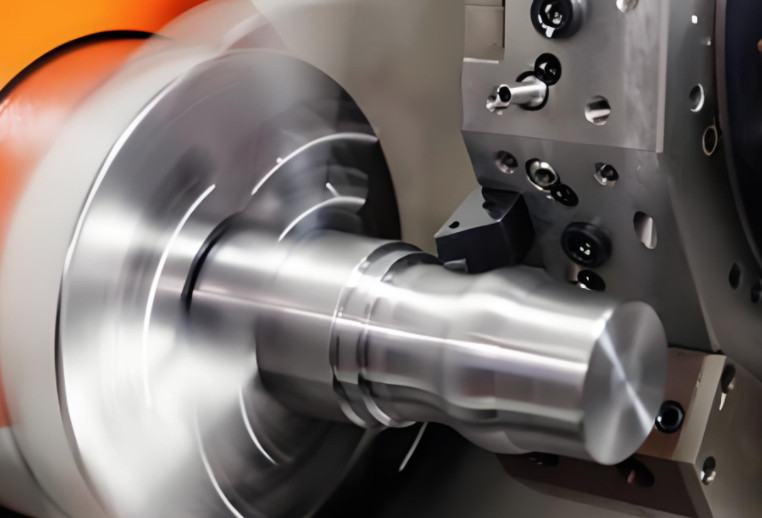
Specialized Machining
Electrical Discharge Machining (EDM): EDM uses high-temperature sparks (up to 10,000°C) to erode conductive materials like hardened steel or carbides. Pulsed voltage between a tool electrode (e.g., copper or graphite) and the workpiece melts and removes material, flushed away by dielectric fluid. EDM is ideal for complex mold cavities, narrow slots, or micro-holes, achieving tolerances of ±0.01mm to ±0.05mm.
Laser Machining: Laser machining uses focused, high-energy laser beams to melt or vaporize material. With spot diameters as small as micrometers, it enables micro-scale precision for metals, ceramics, and polymers. Applications include chip cutting, automotive welding, and aerospace component fabrication, with surface roughness of Ra 0.1μm to Ra 0.5μm.
Electron and Ion Beam Machining: Electron beam machining uses high-energy electron beams to remove material through thermal energy, suitable for micro-holes or intricate parts like fuel injector nozzles. Ion beam machining employs ion sputtering for nanoscale precision, used in semiconductor etching or optical surface polishing, achieving tolerances below ±0.01μm.
Case Studies of Precision Machining Applications
The following case studies demonstrate precision machining applications across industries, highlighting specific techniques and parameters.
Aerospace: Turbine Blade Manufacturing
Aerospace turbine blades endure temperatures of 1850-2000K and centrifugal stresses of 140-560 MPa. Precision milling, grinding, and EDM achieve blade profile tolerances of ±0.05mm to ±0.1mm and surface roughness of Ra 0.1μm to Ra 0.2μm. The process includes:
- Rough Machining: Milling with a φ=dt1 cutter, depth of cut δd1.
- Finish Milling: Tapered cutters (φ=dt2, δd2 < δd1) for precision shaping.
- Final Reaming: Tapered reamers (φ=dt3, δd3 ≤ δd2) for cooling holes.
- Polishing: Grinding rods at 800-1000 rpm, feed rate 0.8-1 mm/s, for hole wall quality.
Five-axis CNC machining with in-process measurement ensures dynamic performance under high-speed rotation.
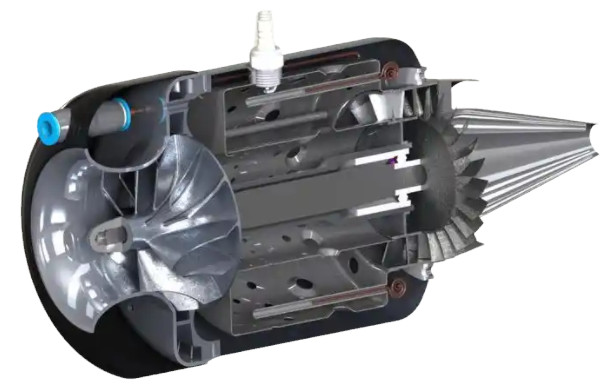
Energy: Gas Turbine Impeller
Gas turbine impellers require blade profile tolerances of ±0.02mm to ±0.05mm, thickness tolerances of ±0.1mm, and surface roughness of Ra 0.2μm to Ra 0.4μm. The process involves precision casting followed by five-axis CNC milling. Toolpath optimization via simulation and coordinate measuring machines (CMM) ensure dimensional accuracy.
Parameter | Specification |
---|---|
Blade Profile Tolerance | ±0.02mm to ±0.05mm |
Blade Thickness Tolerance | ±0.1mm |
Surface Roughness | Ra 0.2μm to Ra 0.4μm |
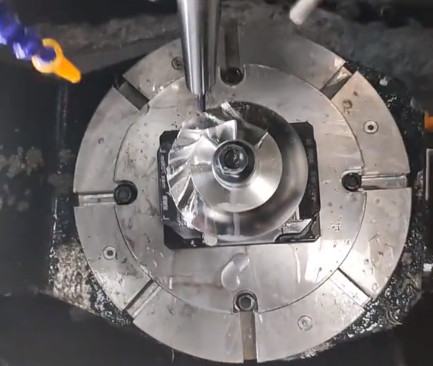
Electronics: Circuit Board and Component Manufacturing
Multi-layer circuit boards require drilling with hole diameter tolerances of ±0.05mm to ±0.1mm and positional accuracy of ±0.1mm to ±0.2mm. Precision resistors achieve ±0.1% resistance value accuracy through material thickness control (±0.005mm). Micro-capacitors maintain plate flatness of ±0.01μm and spacing accuracy of ±0.02μm, ensuring stable electrical performance.
Medical Devices: Surgical Tools and Implants
Surgical knife blades are machined to a thickness of 5-20μm, with straightness and flatness errors below ±0.01mm, verified by optical microscopy. Artificial joints achieve dimensional tolerances of ±0.05mm to ±0.1mm and surface roughness of Ra 0.05μm to Ra 0.1μm. Hydroxyapatite coatings (10-15μm thick, bonding strength ≥15MPa) enhance biocompatibility.
Component | Parameter | Specification |
---|---|---|
Surgical Knife | Blade Thickness | 5-20μm |
Surgical Knife | Straightness/Flatness Error | ±0.01mm |
Artificial Joint | Dimensional Tolerance | ±0.05mm to ±0.1mm |
Artificial Joint | Surface Roughness | Ra 0.05μm to Ra 0.1μm |
Scientific Research: Particle Accelerator Vacuum Systems
The SPIRAL2-DESIR linear accelerator uses magnetic-bearing turbomolecular pumps (e.g., HiPace 700 M) to achieve a vacuum of 1×10⁻⁹ hPa, with vibration levels below 0.05mm/s, ensuring stable ion beam transmission. Precision machining of pump components (e.g., molecular turbine impellers) ensures reliable performance in ultra-high vacuum environments.
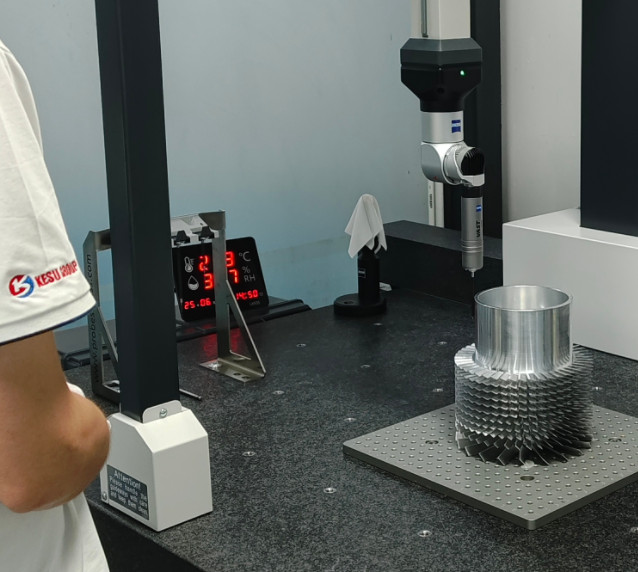
Kesu Precision Machining: Your Partner for Quality
At Kesu, we redefine precision machining with cutting-edge technology and unmatched expertise, delivering components with micro-level accuracy and superior quality. Kesu is a top-notch custom parts CNC machining manufacturing provider offering high-quality and precision machining services. In CNC precision machining Kesu is among the top manufacturer of machine parts all over the world and in China we are the top 5 best service providers of CNC precision machining parts.
FAQ About Precision Machining
What is precision machining?
Precision machining is a manufacturing process that achieves extremely tight dimensional accuracies (±0.1μm to ±1μm), shape accuracies (0.05μm to 0.1μm), and positional accuracies (0.1μm to 0.2μm), with surface finishes as fine as Ra 0.02μm to Ra 0.1μm. It is used to create high-performance components for industries like aerospace, electronics, and medical devices.
What factors make precision machining more difficult for certain materials?
The difficulty of precision machining depends on material properties such as hardness, thermal conductivity, ductility, and brittleness. For example, materials like titanium (hardness 300–350 HV) and Inconel (400–450 HV) are challenging due to high hardness and low thermal conductivity (6.7 W/m·K for titanium, 11 W/m·K for Inconel), which cause tool wear and heat buildup. Brittle materials like ceramics (e.g., silicon carbide, 2500–2800 HV) require specialized tools to avoid cracking.
What tolerances can be achieved in precision machining?
Tolerances depend on the material and setup. Metals like aluminum can achieve ±0.0005 inches, while titanium and stainless steel typically reach ±0.001 inches. Ceramics and composites can achieve ±0.001 mm with ultra-precision techniques like grinding or laser machining.
How is precision machining verified?
Techniques like coordinate measuring machines (CMM), optical microscopy, and in-process measurement ensure components meet specified tolerances and surface quality standards.
How does precision machining impact product performance?
By achieving tight tolerances and superior surface finishes, precision machining ensures components meet stringent functional requirements, enhancing reliability, efficiency, and safety in critical applications.