Aluminum alloys are widely used in industries such as aerospace, automotive, and marine due to their lightweight, high strength, and corrosion resistance. However, deformation during machining remains a significant challenge, impacting dimensional accuracy and product quality. This article provides a systematic and technical overview of methods to prevent deformation in aluminum alloy workpieces, emphasizing material characteristics, process routes, aging treatments, and clamping strategies. The methods are derived from practical experience and focus on achieving precision through effective process design.
Causes of Deformation in Aluminum Alloy Machining
Deformation in aluminum alloy machining arises from multiple factors related to material properties, machining processes, and structural characteristics of the workpiece. Understanding these causes is critical for developing effective prevention strategies.
- Internal Stress: Aluminum alloys, especially high-strength grades like 2A12, develop internal stresses during casting, forging, or heat treatment. These stresses are released during machining, causing elastic or plastic deformation.
- Thermal Effects: Cutting processes generate heat, leading to thermal expansion and contraction, which can distort thin-walled or large workpieces.
- Material Removal: Removing large amounts of material, particularly in roughing operations, disrupts the stress balance within the workpiece, resulting in deformation.
- Clamping Forces: Improper clamping applies uneven forces, causing elastic deformation that reverts to distortion upon release.
- Structural Weakness: Thin-walled or complex structures, such as those in aerospace components, lack sufficient rigidity, making them prone to deformation during machining.
These factors interact, amplifying deformation, particularly in precision components with tight tolerances (e.g., flatness of 0.025 mm or parallelism of 0.03 mm).
Conventional Machining Methods
Conventional machining methods for aluminum alloys aim to minimize deformation through controlled material removal and clamping techniques. The following methods are commonly employed.
Blanking Machining
Blanking, or nesting, involves milling the workpiece from a blank, leaving a small margin (0.10–0.15 mm) on the bottom surface. This method is ideal for workpieces requiring significant material removal, such as those with complex outer shapes or internal cavities. By reducing the amount of material removed in one pass, blanking minimizes heat generation and stress concentration, which are primary causes of deformation. It is particularly effective for thin-walled parts when combined with vacuum chucking, enabling machining of plates as thin as 0.5 mm.
Vacuum Chuck Clamping
Vacuum chucks secure the workpiece by adsorbing its positioning surface, often used with blanking to process thin-walled or complex parts. This method is versatile, accommodating flat, sloped, or curved surfaces, provided an adsorbable surface exists. Dedicated vacuum chuck fixtures, tailored to specific workpiece geometries, enhance stability and reduce deformation. For example, fixtures designed for impellers or shells ensure precise clamping without inducing stress.
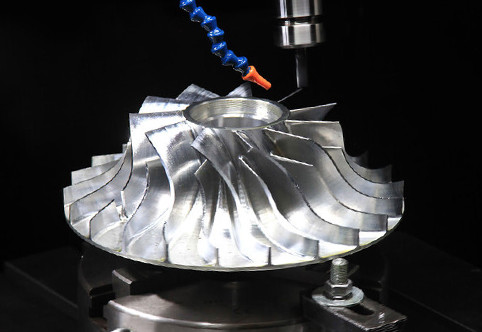
Reinforcement Ribs and Process Lugs
For workpieces with insufficient structural strength, adding reinforcement ribs or process lugs during roughing enhances rigidity. Ribs prevent deformation during clamping and machining, while lugs facilitate precise positioning for subsequent operations. These features are removed during finishing to avoid additional heat or stress. This method is suitable for small to medium-sized workpieces but less effective for oversized components due to increased material and machining complexity.
Comprehensive Application Example
A practical example involves a thin-walled aluminum alloy plate with complex front and back features. The process includes:
- Analyzing the structure to select the back as the positioning surface due to fewer machining requirements.
- Supplementing the positioning surface for vacuum chuck compatibility.
- Adding reinforcement ribs on the front to prevent deformation during roughing and positioning surface finishing.
- Using a dedicated vacuum chuck for front-side finishing after completing the positioning surface.
This approach ensures dimensional stability and meets tight tolerances.
Aging Treatments to Reduce Internal Stress
Aging treatments are critical for eliminating internal stresses in aluminum alloy workpieces, ensuring dimensional stability during machining. Two primary methods are used: indirect aging and direct aging.
Indirect Aging
Indirect aging integrates rough machining as a stress-relief process. After roughing, the workpiece is removed from the machine, allowing stresses to relax before finishing. Typically, roughing leaves a uniform margin of 0.5 mm per side. The unclamping and reclamping process facilitates stress release, mimicking natural aging without requiring extended downtime. This method is suitable for precision structural components, such as aerospace parts, and is efficient for batch production where roughing is completed before finishing.
Direct Aging
Direct aging includes artificial and thermal methods:
- Artificial Aging: Workpieces are left to rest for 24–48 hours after roughing, allowing natural stress relaxation. This method is slow but effective for large or thin-walled parts.
- Thermal Aging: Heat treatment accelerates stress relaxation, ideal for complex parts with large material removal. It ensures stable material properties, preventing deformation during subsequent machining or operation.
Both methods are widely used for high-precision components, such as dynamic parts (e.g., stator rings, turbine shells, or gearboxes), where stress elimination enhances long-term stability.
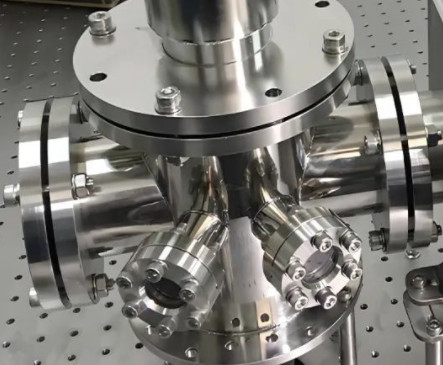
Preventing Datum Surface Deformation
Datum surfaces, critical for precision machining, often deform before finishing due to elastic properties of aluminum alloys. The following methods address this issue.
Milling with High Structural Rigidity
When milling is the only option, the workpiece must have sufficient structural strength to maintain flatness during datum surface machining. This requires careful planning of material removal to avoid stress imbalance.
Multi-Pass Milling for Thin Workpieces
For thin workpieces, multiple milling passes with face flipping reduce deformation. Each pass removes minimal material, gradually balancing stresses. However, slight deformation may persist, requiring additional measures.
Turning for Datum Surfaces
Turning is preferred for datum surfaces due to minimal heat generation. Unlike milling, which involves surface contact and heat buildup, turning uses point contact, reducing thermal and stress-induced deformation. For example, a 2A12-T4 aluminum alloy plate (120 mm × 400 mm × 12 mm, finished to 370 mm × 110 mm × 7 mm, with 0.03 mm parallelism and 0.025 mm flatness) was successfully machined using:
- Turning one side to a polished finish using a single-action chuck.
- Creating threaded holes around the blank on a machining center for fixture attachment.
- Using a dedicated turning fixture with reverse screw clamping to finish the thickness.
This approach achieved the required tolerances, unlike milling, which caused deformation due to heat and stress.
Clamping Strategies to Prevent Deformation
Proper clamping is essential to minimize deformation, particularly for aluminum alloys sensitive to clamping forces. The following table summarizes clamping methods and their applications.
Method | Description | Application |
---|---|---|
Dedicated Fixture with Special Clamps | Custom fixtures with pressure plates or reverse-thread clamps apply downward force, avoiding lateral stress. | Complex or thin-walled parts requiring precise clamping. |
Inner Hole with Small Boss Limit | Uses inner holes and small bosses for positioning, minimizing external force. | Parts with accessible inner features. |
Soft Jaws with Pins | Soft jaws with locating pins reduce clamping force while ensuring alignment. | Parts requiring light clamping to avoid deformation. |
V-Shaped Positioning Fixture | V-shaped fixtures with limit stops secure irregular shapes. | Workpieces with non-flat or curved surfaces. |
Single or Multi-Module Fixtures | Fixtures matching the workpiece’s contour provide uniform support. | Complex geometries requiring tailored support. |
These methods prioritize downward clamping forces over lateral forces (e.g., vise clamping), which cause elastic deformation in aluminum alloys.
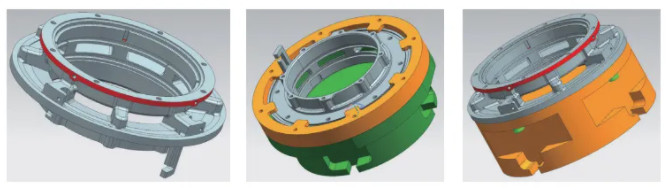
Process Improvements for Cast Aluminum Parts
Cast aluminum parts, such as those with pre-formed features, pose unique challenges due to low rigidity and internal stresses. A case study illustrates process improvements for a cast aluminum part requiring vertical hole tolerances of ±0.005 mm, flatness of 0.02 mm, and perpendicularity/parallelism of 0.03 mm.
- First Improvement: Hole shrinkage (0.005 mm per side) was observed after boring. The process was adjusted by increasing the boring allowance by 0.003 mm per side and adding two empty passes to reduce stress. Hole tolerances were met, but geometric tolerances failed.
- Second Improvement: Adding a light pass (0.08 mm allowance) on the large and opposing surfaces ensured both dimensional and geometric accuracy, addressing plastic deformation.
Material-Specific Considerations
Two common aluminum alloys, 2A12 and 6061, exhibit distinct machining behaviors:
- 2A12 Aluminum Alloy: A high-strength alloy used in aerospace and military applications. It has good machinability but is prone to deformation, requiring careful stress management.
- 6061 Aluminum Alloy: Widely used for its weldability and corrosion resistance, it machines well but is difficult to correct once deformed, except in specialized structures.
Advanced Techniques: Hard and Chemical Filling
Open Hard Filling
Open hard filling involves retaining external blank material connected by pins during roughing to enhance rigidity. After roughing, the connecting blocks are removed, stresses are released, and the blocks are reattached for finishing. This method reduces deformation by improving structural stability and facilitating stress relaxation.
Chemical Filling
Chemical filling is a specialized method for thin-walled parts, such as curved blades. A chemical substance fills the machined surface, solidifying to provide seamless support. This prevents deformation and chatter during finishing, though it is a niche technique requiring dedicated fixtures.
Fitter Correction
Fitter correction, primarily for plate-like parts, relies on skilled manual adjustment to achieve flatness (approximately 0.1 mm). It is applied after roughing or finishing but is limited to low-value parts due to its labor-intensive nature and dependence on operator expertise.
Conclusion
Preventing deformation in aluminum alloy machining requires a systematic approach combining material knowledge, process optimization, and precise clamping. By addressing internal stresses through aging treatments, optimizing machining sequences, and designing effective clamping solutions, manufacturers can achieve high precision and stability. The methods outlined, grounded in practical experience, provide reliable solutions for industries demanding tight tolerances.