Material selection is a critical aspect of precision parts manufacturing, directly impacting the performance, durability, and quality of the final product. Choosing the right material requires a thorough understanding of the application, environmental conditions, and manufacturing constraints. This guide provides a detailed, systematic approach to selecting materials for precision parts, focusing on metals, non-metals, and composites, along with key considerations to ensure optimal outcomes.
Metal Materials
Metal materials are widely used in precision parts manufacturing due to their strength, durability, and versatility. The choice of metal depends on the specific mechanical and environmental requirements of the application. Below, we explore the most common metal materials and their properties.
Steel
Steel is a popular choice due to its high strength, toughness, and machinability. It is available in various grades, each tailored to specific applications.
- Carbon Steel: Contains 0.05% to 2.1% carbon, offering a balance of strength and ductility. Low-carbon steel (e.g., AISI 1018) is easy to machine and weld, suitable for structural components. High-carbon steel (e.g., AISI 1095) provides greater hardness but is less ductile.
- Stainless Steel: Alloyed with chromium (at least 10.5%), stainless steel (e.g., 304, 316) offers excellent corrosion resistance, making it ideal for medical devices and marine applications. Its yield strength ranges from 200–600 MPa, depending on the grade.
- Tool Steel: Designed for high hardness and wear resistance (e.g., D2, H13), tool steel is used for cutting tools and dies. Hardness can reach 58–62 HRC after heat treatment.
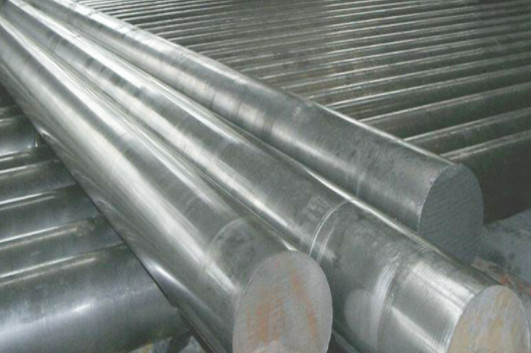
Aluminum
Aluminum is valued for its lightweight nature (density ~2.7 g/cm³) and corrosion resistance. It is commonly used in aerospace and automotive industries.
- Aluminum 6061: Offers a yield strength of ~276 MPa and excellent machinability, suitable for structural components.
- Aluminum 7075: With a higher yield strength (~503 MPa), it is used in high-stress applications like aircraft fittings.
Copper and Its Alloys
Copper and its alloys, such as brass and bronze, are selected for their electrical conductivity and corrosion resistance.
- Pure Copper: With 99.9% purity, it offers electrical conductivity up to 58 MS/m, ideal for electrical connectors.
- Brass (Cu-Zn): Combines strength (yield strength ~200–400 MPa) and machinability, used in fittings and valves.
- Bronze (Cu-Sn): Provides wear resistance and low friction, suitable for bearings and bushings.
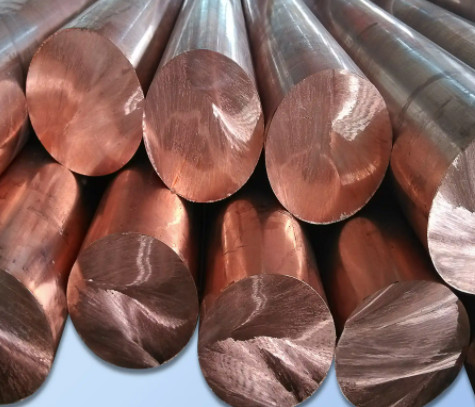
Selection Considerations for Metals
When selecting metals, consider the following parameters:
Property | Key Metrics | Application Relevance |
---|---|---|
Yield Strength | 100–600 MPa (varies by alloy) | Ensures structural integrity under load |
Hardness | 20–62 HRC | Determines wear resistance |
Corrosion Resistance | Dependent on alloy composition | Critical for harsh environments |
Machinability | Varies (e.g., aluminum > stainless steel) | Affects manufacturing efficiency |
Non-Metal Materials
Non-metal materials, such as plastics, ceramics, and glass, offer unique properties like light weight, corrosion resistance, and electrical insulation. These materials are essential in applications where metals are unsuitable.
Plastics
Engineering plastics are widely used in precision manufacturing for their versatility and cost-effectiveness.
- Polyamide (Nylon): Offers tensile strength of ~50–80 MPa and low friction, ideal for gears and bearings.
- Polycarbonate (PC): Known for high impact resistance (Izod impact strength ~800 J/m), used in protective covers.
- PEEK: A high-performance plastic with a tensile strength of ~100 MPa and thermal stability up to 250°C, suitable for medical and aerospace components.
Ceramics
Ceramics provide exceptional hardness, thermal stability, and electrical insulation but are brittle.
- Alumina (Al₂O₃): With a hardness of ~9 Mohs, it is used in cutting tools and insulators.
- Zirconia (ZrO₂): Offers fracture toughness of ~7–10 MPa·m¹/², suitable for high-wear applications like bearings.
Glass
Glass is used in optical and electronic applications due to its transparency and insulating properties.
- Borosilicate Glass: With a thermal expansion coefficient of ~3.3 × 10⁻⁶/°C, it is used in precision optical components.
- Quartz Glass: Offers high thermal stability (up to 1100°C) and is used in semiconductor manufacturing.
Selection Considerations for Non-Metals
Non-metal materials require careful evaluation of their limitations, such as brittleness in ceramics or thermal sensitivity in plastics. Key factors include:
- Thermal Stability: Ensure the material can withstand operating temperatures.
- Electrical Insulation: Critical for electronic components.
- Cost-Effectiveness: Plastics are generally cheaper than ceramics or glass.
Composite Materials
Composite materials combine two or more distinct materials to achieve superior properties, such as high strength-to-weight ratios and corrosion resistance. They are increasingly used in demanding applications.
Types of Composites
Common composites include fiber-reinforced and particulate composites.
- Carbon Fiber Reinforced Polymers (CFRP): With a tensile strength of ~600–800 MPa and density of ~1.6 g/cm³, CFRP is used in aerospace for lightweight, high-strength components.
- Glass Fiber Reinforced Polymers (GFRP): Offers tensile strength of ~300–500 MPa, used in automotive parts for cost-effectiveness.
- Metal Matrix Composites (MMCs): Combine metals with ceramics (e.g., Al-SiC), offering high stiffness (~100–150 GPa) for engine components.
Advantages and Applications
Composites excel in applications requiring a balance of strength, weight, and durability. For example, CFRP is used in aircraft wings, while MMCs are applied in high-temperature turbine blades.
Selection Considerations for Composites
Selecting composites involves evaluating:
- Cost: Composites like CFRP are expensive due to complex manufacturing processes.
- Manufacturing Complexity: Requires specialized techniques like lay-up or resin infusion.
- Environmental Resistance: Ensure compatibility with operating conditions.
Key Considerations in Material Selection
Beyond material properties, several practical factors influence the selection process. These considerations ensure the chosen material aligns with manufacturing goals and application requirements.
Cost
Material cost significantly affects the overall project budget. For instance, stainless steel is more expensive than carbon steel, while PEEK is costlier than nylon. Balancing cost with performance is essential.
Manufacturability
The ease of machining, forming, or joining a material impacts production efficiency. For example, aluminum 6061 is easier to machine than titanium, which has a low thermal conductivity (~7 W/m·K) and requires specialized tools.
Surface Treatment
Materials often require surface treatments to enhance performance.
Treatment | Purpose | Applicable Materials |
---|---|---|
Anodizing | Improves corrosion resistance | Aluminum, Titanium |
Electroplating | Enhances surface hardness | Steel, Copper |
Passivation | Removes surface contaminants | Stainless Steel |
Environmental Compatibility
Materials must withstand operating conditions, such as temperature, humidity, or chemical exposure. For example, stainless steel 316 is preferred in marine environments due to its resistance to chloride corrosion.
Reproducibility
Consistency in material properties across batches is critical for precision manufacturing. Certified materials with traceable specifications ensure reproducibility.
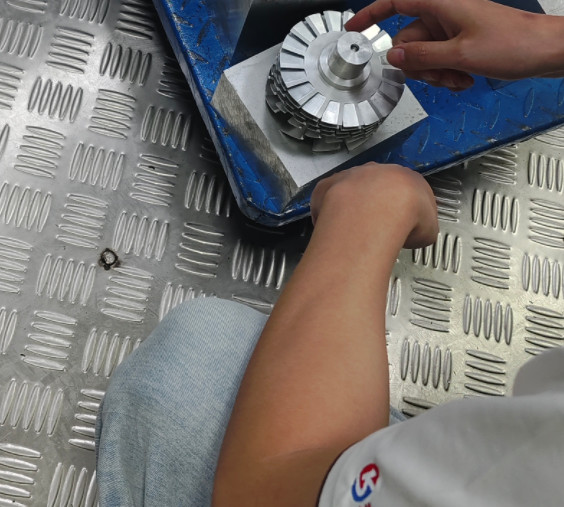
Common Issues in Material Selection
While material selection is critical, several challenges can complicate the process. Addressing these issues ensures better outcomes.
Inadequate Material Data
Incomplete or unreliable material data can lead to poor selections. Always source data from reputable suppliers and verify properties like tensile strength or thermal conductivity.
Overlooking Application-Specific Needs
Failing to account for specific requirements, such as fatigue resistance or thermal expansion, can result in part failure. For example, using aluminum in high-temperature applications (>200°C) may cause deformation.
Cost vs. Performance Trade-Offs
Selecting a cheaper material to reduce costs can compromise performance. For instance, replacing PEEK with nylon in high-temperature applications may lead to premature failure.
Conclusion
Material selection for precision parts manufacturing requires a systematic approach, balancing material properties, application requirements, and practical constraints. Metals like steel and aluminum offer strength and versatility, while non-metals like plastics and ceramics provide lightweight and insulating properties. Composites deliver superior performance for specialized applications. By carefully evaluating mechanical properties, cost, manufacturability, and environmental compatibility, manufacturers can ensure the production of high-quality, reliable parts. Addressing common issues, such as inadequate data or overlooking specific needs, further enhances the selection process, leading to optimal outcomes.