The custom precision parts manufacturing process involves producing high-accuracy, reliable components tailored to client specifications. This systematic workflow ensures quality and precision through distinct stages: raw material procurement, design and drafting, machining, and inspection. Below, we analyze each stage, providing technical details and procedural insights to serve as a reference for manufacturers.
Raw Material Procurement
Raw material procurement is the foundational step in custom precision parts manufacturing. Selecting high-quality materials ensures the final product's performance and reliability. Manufacturers must identify reputable suppliers capable of providing materials that meet stringent standards.
Key considerations include material type (e.g., stainless steel, aluminum, titanium), grade (e.g., 304 stainless steel, 6061 aluminum), and specifications (e.g., tensile strength, corrosion resistance). For example, aerospace components often require titanium alloys with a tensile strength of 900–1200 MPa and a density of approximately 4.5 g/cm³. Suppliers must provide certifications, such as ISO 9001 or AS9100, to verify material quality.
The procurement process involves:
- Supplier Evaluation: Assess suppliers based on quality certifications, delivery reliability, and cost-effectiveness.
- Material Specifications: Define requirements, such as dimensional tolerances (e.g., ±0.01 mm) and chemical composition (e.g., carbon content ≤0.08% for certain steels).
- Testing and Verification: Conduct tests, such as spectrometry for chemical analysis or hardness testing (e.g., Rockwell C scale), to confirm material properties.
- Inventory Management: Maintain stock levels to avoid production delays, typically using just-in-time (JIT) systems to optimize storage costs.
Effective procurement minimizes defects and ensures a stable supply chain, directly impacting the quality of the final product.
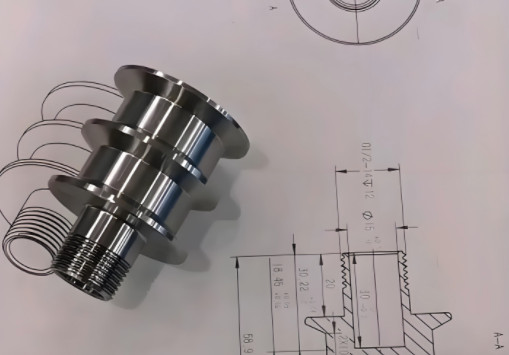
Design and Drafting
Design and drafting translate client requirements into precise technical specifications. This stage requires close collaboration with clients to ensure the component meets functional and dimensional needs.
Design begins with understanding the part’s application, such as load-bearing capacity or environmental conditions (e.g., operating temperatures from -40°C to 200°C). Engineers use software like AutoCAD, SolidWorks, or CATIA to create detailed 2D and 3D models. These models specify tolerances (e.g., ±0.005 mm for critical dimensions), surface finish (e.g., Ra 0.8 µm), and geometric features.
The drafting process includes:
- Requirement Analysis: Review client specifications, such as dimensional accuracy or material properties, to align with industry standards like ISO 2768.
- 3D Modeling: Develop models to visualize complex geometries, ensuring compatibility with machining capabilities.
- Technical Drawings: Produce drawings with annotations for dimensions, tolerances, and machining instructions.
- Design Review: Conduct simulations, such as finite element analysis (FEA), to verify structural integrity under specific loads (e.g., 500 N force).
Accurate design and drafting reduce manufacturing errors and ensure the part meets client expectations.
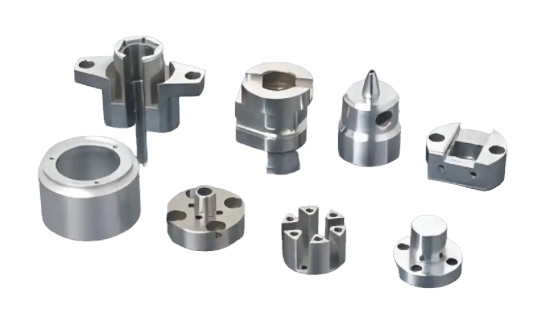
Machining and Manufacturing
Machining is the core of the precision parts manufacturing process, transforming raw materials into finished components. This stage employs various techniques, such as turning, milling, drilling, and grinding, depending on the part’s complexity and requirements.
High-precision equipment, such as CNC (Computer Numerical Control) machines, is critical. For example, a 5-axis CNC milling machine can achieve positional accuracy of ±0.002 mm. Machining parameters, such as cutting speed (e.g., 200 m/min for aluminum) and feed rate (e.g., 0.1 mm/rev), are optimized to ensure surface quality and dimensional accuracy.
The machining process involves:
- Process Planning: Select appropriate techniques based on material and geometry. For instance, hard metals like titanium require lower cutting speeds (50–80 m/min) to prevent tool wear.
- Tool Selection: Choose tools, such as carbide inserts with specific rake angles (e.g., 10°), to optimize cutting efficiency.
- Machine Setup: Calibrate machines to maintain tolerances, using fixtures to secure workpieces.
- Quality Monitoring: Implement in-process checks, such as real-time dimensional measurements, to detect deviations.
The following table summarizes common machining techniques and their applications:
Technique | Description | Typical Tolerance | Applications |
---|---|---|---|
Turning | Rotates workpiece against a cutting tool | ±0.01 mm | Shafts, bushings |
Milling | Uses rotating cutters to remove material | ±0.005 mm | Slots, complex surfaces |
Grinding | Abrasive process for high surface finish | ±0.002 mm | Bearings, gears |
Drilling | Creates precise holes | ±0.02 mm | Holes for fasteners |
Effective machining ensures components meet precise specifications while minimizing waste and production time.
Inspection and Testing
Inspection and testing verify that manufactured parts meet client specifications and industry standards. This stage is critical to ensuring quality and reliability.
Inspection methods include:
- Dimensional Inspection: Use coordinate measuring machines (CMM) with accuracy up to 0.001 mm to verify dimensions against tolerances.
- Surface Inspection: Measure surface roughness using profilometers, ensuring values like Ra 0.4 µm for critical components.
- Material Testing: Conduct non-destructive tests, such as ultrasonic testing, to detect internal defects.
- Functional Testing: Simulate operating conditions, such as pressure tests up to 10 MPa, to confirm performance.
Testing protocols follow standards like ISO 17025 for laboratory accreditation. Defective parts are either reworked or scrapped, while compliant parts are prepared for delivery.
The following table outlines common inspection methods and their parameters:
Method | Equipment | Accuracy | Purpose |
---|---|---|---|
CMM | Coordinate Measuring Machine | ±0.001 mm | Dimensional accuracy |
Profilometer | Surface Roughness Tester | ±0.01 µm | Surface finish |
Ultrasonic Testing | Ultrasonic Flaw Detector | Detects 0.1 mm defects | Internal defect detection |
Thorough inspection ensures only high-quality parts reach clients, enhancing trust and satisfaction.
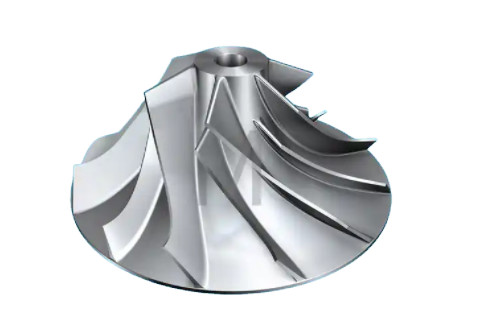
Case Study: Precision Manufacturing Example
A mechanical parts manufacturer implemented the described process to produce custom aerospace components. In raw material procurement, they sourced 316L stainless steel with a yield strength of 290 MPa from an ISO 9001-certified supplier. During design, engineers used SolidWorks to create models with tolerances of ±0.005 mm, verified through FEA. Machining involved 5-axis CNC milling with a spindle speed of 12,000 RPM, achieving a surface finish of Ra 0.6 µm. Inspection used a CMM and ultrasonic testing to confirm dimensional accuracy and material integrity. This systematic approach resulted in a 98% first-pass yield, meeting client requirements and improving operational efficiency.
Conclusion
The custom precision parts manufacturing process is a structured, technical workflow that ensures high-quality, reliable components. Through meticulous raw material procurement, precise design and drafting, advanced machining, and rigorous inspection, manufacturers can meet stringent client specifications. This systematic approach not only delivers consistent quality but also strengthens competitiveness in industries like aerospace, automotive, and medical devices. By adhering to industry standards and leveraging advanced technology, manufacturers can achieve operational excellence and client satisfaction.