Swiss machining, also known as Swiss-style turning or Swiss screw machining, is a precision manufacturing process designed for producing small, intricate components with tight tolerances. Originating in Switzerland in the late 19th century for watchmaking, it has evolved into a critical technology across industries like medical, aerospace, and electronics. This guide provides a detailed exploration of Swiss machining, its applications, technical parameters, and operational difficulties, offering a clear and systematic understanding of the process.
Understanding Swiss Machining
Swiss machining utilizes specialized CNC lathes, known as Swiss-type lathes or Swiss screw machines, to manufacture complex parts with high precision. Unlike conventional CNC lathes, Swiss machines feature a sliding headstock and guide bushing, enabling the workpiece to move along the Z-axis while being supported close to the cutting tool. This design minimizes deflection and enhances accuracy, making it ideal for machining long, slender, or intricate parts.
The process was initially developed to produce watch components, attributed to Swiss watchmaker Jakob Schweizer in the 1870s. Today, modern CNC Swiss machines incorporate advanced automation, multiple axes (often five to thirteen), and live tooling, allowing simultaneous operations like turning, milling, drilling, and threading in a single setup. These machines can handle a variety of materials, including stainless steel, titanium, aluminum, brass, copper, and certain plastics, with tolerances as tight as ±0.0001 inches (0.0025 mm).
Swiss machining operates by feeding bar stock through a guide bushing, which supports the material near the cutting point. The sliding headstock advances the workpiece incrementally, allowing segmented machining that reduces vibration and improves precision. Many Swiss lathes include a sub-spindle for secondary operations, such as drilling or tapping the back of the part, enabling fully automated production without manual intervention.
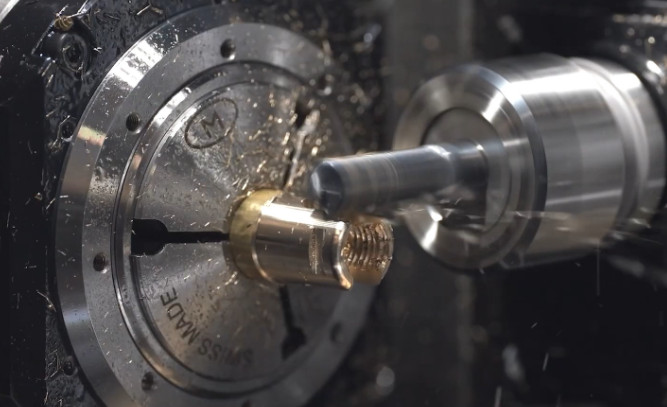
Key Components of Swiss Machining
Swiss-type lathes are engineered with unique features that distinguish them from conventional lathes. Below are the primary components that define their functionality:
- Sliding Headstock: Moves the workpiece along the Z-axis, allowing precise positioning and continuous machining without deflection.
- Guide Bushing: Provides support close to the cutting tool, reducing vibration and enabling high-precision machining of slender parts.
- Main Spindle: Rotates the workpiece at speeds typically ranging from 100 to 10,000 RPM, providing the kinetic energy for material removal.
- Sub-Spindle: Performs secondary operations, such as back-side machining, in sync with the main spindle, reducing cycle times.
- Tool Turret: Holds multiple cutting tools (up to 20 in some machines), allowing rapid tool changes and simultaneous operations.
- CNC Control Panel: Serves as the machine’s interface, enabling operators to input machining parameters, tool paths, and automation sequences.
- Coolant System: Delivers high-pressure coolant (up to 2,000 PSI) to dissipate heat, lubricate tools, and improve surface finish.
These components work in tandem to achieve the precision and efficiency that Swiss machining is known for, particularly in high-volume production of small parts.
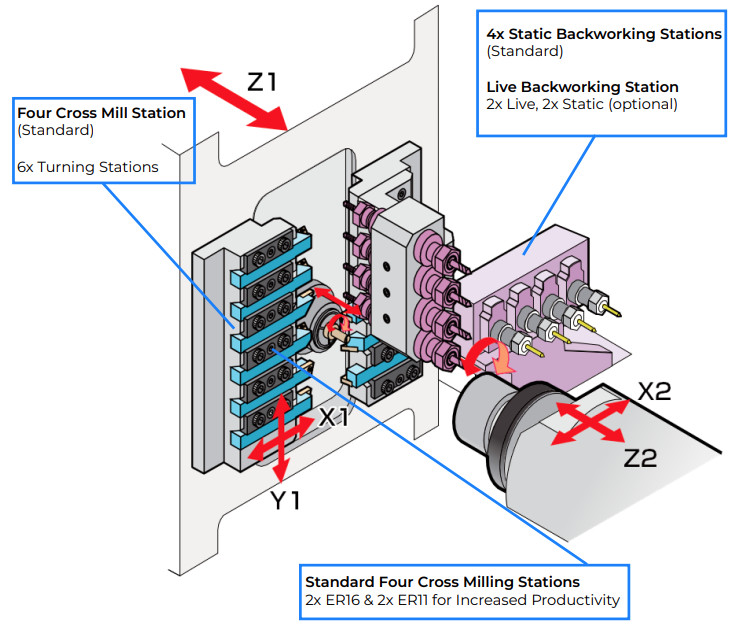
Applications of Swiss Machining
Swiss machining is widely used across industries requiring high-precision components. Its ability to produce complex geometries with tight tolerances makes it indispensable in the following sectors:
- Medical: Produces surgical screws, dental implants, orthopedic components, and other devices requiring biocompatible materials like titanium and stainless steel with tolerances within ±0.0005 inches (0.0127 mm).
- Aerospace: Manufactures connectors, fasteners, and hydraulic fittings, often using materials like Inconel or aluminum, with concentricity tolerances as low as 0.0001 inches (0.0025 mm).
- Electronics: Creates micro connectors, pins, and sockets for consumer electronics and semiconductors, using materials like copper and brass for electrical conductivity.
- Automotive: Produces shafts, bushings, and fuel system components, leveraging Swiss machining’s ability to handle high-volume production with consistent quality.
- Watchmaking: Continues to be used for gears, springs, and other intricate watch components, maintaining its historical roots.
The versatility of Swiss machining allows it to produce parts with diameters ranging from 0.008 inches (0.2 mm) to 1.375 inches (35 mm) and length-to-diameter ratios up to 50:1, making it suitable for both micro-machining and larger precision components.
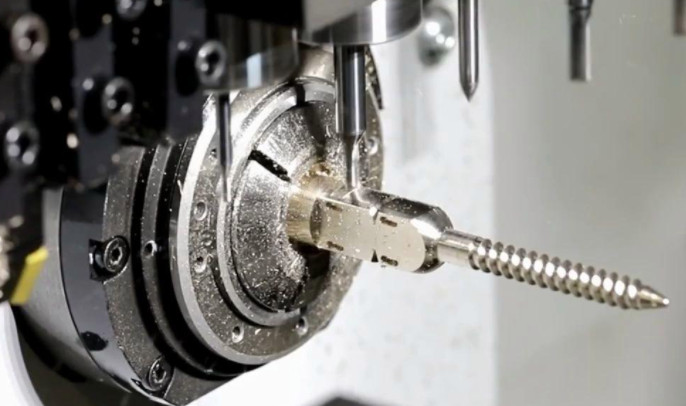
Technical Parameters of Swiss Machining
Swiss machining’s performance relies on precise control of technical parameters. Below is a table summarizing key parameters and their typical ranges:
Parameter | Typical Range | Description |
---|---|---|
Spindle Speed | 100–10,000 RPM | Determines the rotational speed of the workpiece, affecting cutting efficiency and surface finish. |
Feed Rate | 0.001–0.1 inches/rev (0.025–2.54 mm/rev) | Controls the rate at which the workpiece advances, impacting cycle time and tool wear. |
Tolerance | ±0.0001–±0.0005 inches (±0.0025–±0.0127 mm) | Defines the precision of machined parts, critical for medical and aerospace applications. |
Tool Count | Up to 20 tools | Enables multiple operations (turning, milling, drilling) in a single setup. |
Coolant Pressure | 500–2,000 PSI | Manages heat and chip evacuation, ensuring tool life and surface quality. |
Bar Diameter | 0.008–1.375 inches (0.2–35 mm) | Limits the size of the workpiece, typically suited for small to medium parts. |
These parameters are adjusted based on material properties, part complexity, and production requirements. For example, machining titanium requires lower feed rates and higher coolant pressure due to its poor heat conductivity, while aluminum allows faster feeds for quicker cycle times.
Difficulties in Swiss Machining
While Swiss machining offers unmatched precision, it presents several operational difficulties that require careful management. Below are the primary challenges encountered in the process:
- Guide Bushing Maintenance: The guide bushing is critical for precision but can cause issues like out-of-roundness or tool chatter if not properly maintained. Misalignment or wear can lead to dimensional inaccuracies, requiring regular inspection and adjustment. For example, a worn guide bushing may increase concentricity errors beyond 0.0005 inches (0.0127 mm).
- Chip Management: Long, stringy chips can tangle with spindles or workpieces, causing surface finish issues or machine jams. This is particularly problematic with materials like stainless steel or titanium. Adjusting feed rates (e.g., increasing to 0.05 inches/rev or 1.27 mm/rev) and using chip-breaking inserts can mitigate this issue.
- Tool Setup Complexity: Swiss machines often lack tool touch probes, making tool setting challenging. Operators must use offline tool presetters to ensure accuracy, which adds setup time. A single tool may perform multiple operations, and incorrect offsets can affect subsequent cuts, leading to scrap parts.
- Material Consistency: Variations in bar stock diameter (e.g., ±0.001 inches or 0.025 mm) can cause instability in the guide bushing, reducing precision. Ground bar stock is often required to maintain consistency, increasing material costs.
- Programming Complexity: Swiss machines require precise CNC programming to avoid tool collisions, especially with multi-spindle setups. Segmented machining demands careful coordination of tool paths and spindle movements, increasing the risk of errors if not properly managed.
These difficulties can be addressed through skilled operation, regular maintenance, and optimized programming. For instance, using CAM software tailored for Swiss machining can streamline tool path generation, while high-pressure coolant systems (1,000–2,000 PSI) help manage chips effectively.
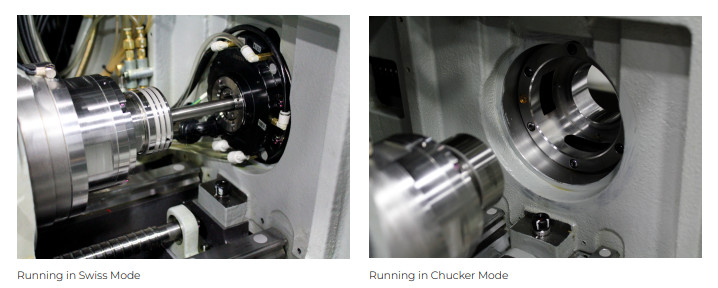
Comparison of Swiss Machining and Conventional CNC Lathes
To highlight the unique advantages of Swiss machining, the following table compares it to conventional CNC lathes:
Feature</ Tracey> | Swiss Machining | Conventional CNC Lathe |
---|---|---|
Headstock | Sliding, moves along Z-axis | Fixed, workpiece stationary |
Workpiece Support | Guide bushing near cutting tool | Collet or chuck, often at ends |
Tolerance | ±0.0001–±0.0005 inches | ±0.001–±0.005 inches |
Part Complexity | High, supports intricate geometries | Moderate, better for simpler parts |
Cycle Time | Faster due to simultaneous operations | Slower, single operation at a time |
Ideal Applications | Small, slender, high-precision parts | Larger, simpler components |
This comparison underscores Swiss machining’s superiority for small, complex parts with tight tolerances, while conventional lathes are better suited for larger, less intricate components.
Best Practices for Swiss Machining
To maximize efficiency and precision in Swiss machining, operators should adhere to the following best practices:
- Optimize Tool Selection: Choose tools based on material properties (e.g., coated carbide for titanium) to minimize wear and improve surface finish.
- Use Ground Bar Stock: Ensure consistent bar diameter to maintain guide bushing stability and precision.
- Adjust Feed and Speed: Fine-tune parameters (e.g., feed rates of 0.01–0.05 inches/rev for stainless steel) to control chip formation and extend tool life.
- Leverage CAM Software: Use specialized software to generate precise tool paths and minimize programming errors.
- Implement High-Pressure Coolant: Use coolant pressures of 1,000–2,000 PSI to manage heat and chips, especially for difficult materials like Inconel.
- Regular Maintenance: Inspect guide bushings and collets regularly to prevent wear-related inaccuracies.
By following these practices, manufacturers can mitigate difficulties and achieve consistent, high-quality results in Swiss machining operations.
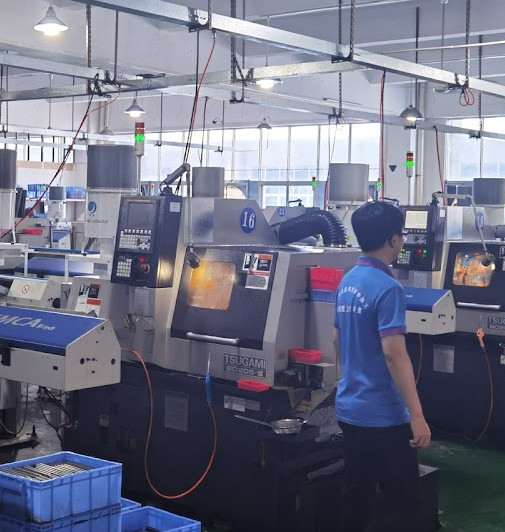
Precision Perfected with Kesu Swiss Machining
Unlock unparalleled accuracy and efficiency with Kesu’s Swiss machining service solutions. With expertise in handling complex geometries and materials like titanium and stainless steel, Kesu ensures consistent quality and fast turnaround. Trust Kesu to elevate your precision manufacturing needs with reliability and excellence. Kesu is a top-notch custom parts manufacturing provider offering high-quality and precise CNC machining services. In CNC precision machining Kesu is among the top manufacturer of machine parts all over the world and in China they are the top 5 best service providers of CNC precision machining parts.
Conclusion
Swiss machining is a cornerstone of precision manufacturing, offering unparalleled accuracy and efficiency for small, complex parts. Its unique design, featuring sliding headstocks and guide bushings, enables tight tolerances and high-volume production across industries like medical, aerospace, and electronics. While challenges like chip management and tool setup complexity exist, they can be addressed through proper maintenance, optimized parameters, and skilled operation. By understanding its components, applications, and best practices, manufacturers can leverage Swiss machining to meet the demands of modern precision engineering.
Frequently Asked Questions (FAQs) About Swiss Machining
What is the key difference between Swiss machining and conventional CNC turning?
The primary distinction lies in workpiece support and movement. Swiss machining uses a sliding headstock that moves the workpiece along the Z-axis, paired with a guide bushing that supports the material close to the cutting tool—minimizing deflection, especially for long, slender parts. Conventional CNC lathes have a fixed headstock, with the workpiece stationary, relying on collets or chucks for support (less precise for small or thin components).
Why is Swiss machining used in the medical industry?
Medical components (e.g., surgical screws, dental implants) require extremely tight tolerances (often ±0.0001–±0.0005 inches) and biocompatible materials (titanium, stainless steel). Swiss machining’s guide bushing design ensures precision, while its ability to handle small, intricate geometries (e.g., threaded or grooved surfaces) meets medical device standards.
Is Swiss machining cost-effective for low-volume production?
Swiss machines have higher setup and programming costs due to their complexity, making them more cost-effective for high-volume runs (thousands to millions of parts). For low-volume production, conventional CNC lathes may be cheaper, unless the part requires Swiss-level precision (e.g., aerospace micro-components).
What tolerances can Swiss machining achieve?
Swiss machining routinely achieves tolerances as tight as ±0.0001 inches (0.0025 mm) for critical features like concentricity or diameter. This precision is far superior to conventional lathes (typically ±0.001–±0.005 inches).
How long does it take to program a Swiss machine?
Programming complexity depends on part design. Simple parts may take a few hours, while intricate geometries (with multiple operations) can require 1–3 days using CAM software tailored for Swiss machining. Offline programming (with tool presetters) helps reduce setup time on the machine.