Cast iron is a versatile and widely used material in industrial applications due to its robust mechanical properties, cost-effectiveness, and excellent machinability. This guide provides a detailed overview of cast iron types, their applications, and machining techniques, focusing on technical parameters and best practices to achieve high-quality results.
Understanding Cast Iron: Composition and Types
Cast iron is an iron-carbon alloy containing 2.5-4% carbon and 1-3% silicon, often alloyed with elements like manganese, phosphorus, and sulfur to enhance specific properties. Its microstructure, particularly the form of carbon (graphite or carbide), determines its mechanical characteristics and machinability. The primary types of cast iron are gray, ductile, malleable, and white cast iron, each suited for specific applications.
Gray cast iron features graphite flakes, offering good machinability and vibration damping. Ductile cast iron, with nodular graphite, provides higher strength and toughness but is harder to machine. Malleable cast iron, formed through heat treatment, balances strength and ductility. White cast iron, with iron carbide, is extremely hard and wear-resistant but brittle and challenging to machine.
Type | Carbon Form | Key Properties | Common Applications |
---|---|---|---|
Gray Cast Iron | Graphite Flakes | Good machinability, vibration damping | Engine blocks, machine bases |
Ductile Cast Iron | Nodular Graphite | High strength, toughness | Gears, crankshafts |
Malleable Cast Iron | Temper Carbon | Balanced strength and ductility | Pipe fittings, brackets |
White Cast Iron | Iron Carbide | High hardness, wear resistance | Wear plates, rollers |
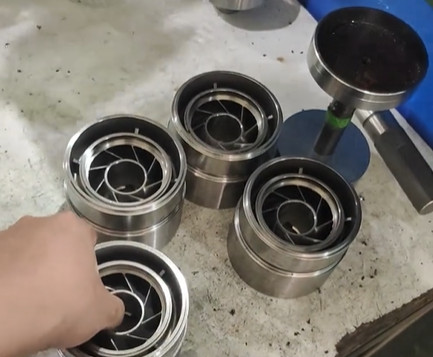
Applications of Cast Iron in Industry
Cast iron’s unique properties make it indispensable across various industries. Its ability to be cast into complex shapes and its cost-effectiveness drive its widespread use in automotive, machinery, and construction sectors.
Automotive Industry: Gray cast iron is commonly used for engine blocks, cylinder heads, and brake components due to its vibration damping and thermal conductivity. Ductile cast iron is preferred for crankshafts and gears, where higher strength is required.
Machinery and Tooling: Cast iron’s rigidity and damping properties make it ideal for machine tool bases, frames, and workholding fixtures like tombstones. Gray cast iron is often chosen for its machinability and stability.
Construction and Infrastructure: Malleable and ductile cast iron are used in pipe fittings, manhole covers, and structural components due to their durability and corrosion resistance. White cast iron is applied in wear-resistant surfaces like pump housings.
Other Applications: Cast iron is also used in marine equipment, such as seawater pump housings, and in industrial rollers due to its wear resistance and ability to handle high mechanical loads.
Machining Cast Iron: Techniques and Parameters
Machining cast iron requires careful consideration of its material properties, as each type presents unique characteristics that influence tool selection, cutting parameters, and machining techniques. Common operations include turning, milling, drilling, and grinding.
Turning: Turning cast iron involves adjusting cutting speed and feed rate based on the material’s hardness. Gray cast iron typically allows higher cutting speeds (80-120 SFM) due to its softer graphite structure, while ductile iron requires lower speeds (50-80 SFM) to prevent tool wear. Carbide inserts with grades like C2 or C3 are recommended for their durability.
Milling: Milling cast iron demands tools with optimal cutting angles to minimize forces and achieve a smooth surface finish. End mills with carbide or ceramic inserts are effective, particularly for finishing operations. Cutting speeds for gray cast iron range from 100-150 m/min, with feed rates of 0.1-0.3 mm/tooth.
Drilling: Drilling cast iron requires high-performance carbide drills, such as those with PC5300 or NC6315 grades, designed for cast iron. Speeds of 100-150 m/min and feed rates of 0.05-0.15 mm/rev are typical for gray cast iron, while ductile iron may require lower parameters to avoid chipping.
Grinding: Grinding is used for finishing cast iron parts to achieve tight tolerances and superfine surface finishes (4-7 Ra for iron). Silicon carbide or diamond abrasives are effective, with careful attention to avoid overheating the workpiece.
Operation | Material | Cutting Speed (m/min) | Feed Rate | Recommended Tool |
---|---|---|---|---|
Turning | Gray Cast Iron | 80-120 | 0.1-0.3 mm/rev | C2/C3 Carbide Inserts |
Turning | Ductile Cast Iron | 50-80 | 0.08-0.2 mm/rev | C2/C3 Carbide Inserts |
Milling | Gray Cast Iron | 100-150 | 0.1-0.3 mm/tooth | Carbide/Ceramic End Mills |
Drilling | Gray Cast Iron | 100-150 | 0.05-0.15 mm/rev | PC5300/NC6315 Carbide Drills |
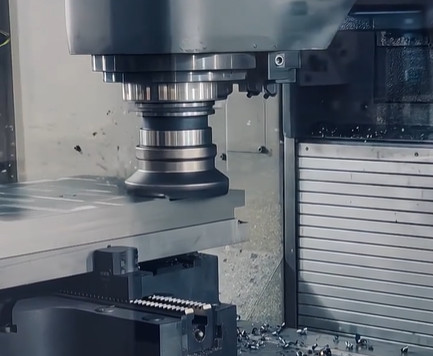
Tool Selection for Cast Iron Machining
Selecting the appropriate cutting tools is critical for efficient cast iron machining. Tool material, geometry, and coating directly impact tool life, surface quality, and productivity.
Carbide Tools: Carbide inserts, particularly C2 and C3 grades, are widely used for their balance of hardness and toughness. For high-speed operations, coated carbide inserts (e.g., NC6315 grade) with TiN or TiAlN coatings reduce wear and improve performance.
CBN Tools: Cubic Boron Nitride (CBN) tools, such as Sumitomo’s BNX10 or BNS800 grades, are ideal for high-speed machining of high-alloy cast iron. They offer excellent surface finish and reduced cycle times, particularly in intermittent cutting scenarios (e.g., turning slurry pump impellers at vc=75 m/min, ap=5 mm, f=0.1 mm/r).
Ceramic Inserts: Ceramic tools are suitable for finishing operations due to their thermal resilience and wear resistance. They are effective for high-speed milling, achieving surface finishes as low as 4 Ra.
Tool Geometry: Negative rake angles (e.g., WNMG inserts) are preferred for cast iron to handle the abrasive nature of the material. Sharp edges and small tip radii (0.8-1.2 mm) minimize cutting forces and improve surface quality.
Lubrication and Cooling Strategies
Lubrication and cooling are essential to manage heat and chip formation during cast iron machining. While gray cast iron is often machined dry due to its self-lubricating graphite, ductile and malleable cast iron benefit from coolant to reduce tool wear and improve surface finish.
Dry Machining: Common for gray cast iron, dry machining avoids coolant-related corrosion but requires robust dust management due to abrasive graphite particles. Shop vacuums and magnetic chip collectors are effective for maintaining a clean workspace.
Wet Machining: For ductile iron, semi-synthetic soluble cutting fluids with low foaming properties are recommended. Flood cooling (CFA) or internally cooled tools (ICT) can reduce cutting temperatures, with ICT systems circulating coolant through the insert for enhanced heat dissipation.
Compressed Air: In high-speed scenarios, compressed air assists with chip removal and cooling, particularly for milling operations, reducing the risk of built-up edge formation.
Workholding and Setup Considerations
Proper workholding ensures precision and stability during cast iron machining. Cast iron parts are often oversized, allowing flexibility in workholding arrangements.
Clamping: Pads and clamps are effective for securing cast iron, as vises may struggle to grip the material’s hard surface. Aluminum pads improve grip compared to steel blocks.
Setup Strategies: A two-step setup is common, with an initial cut to create reference geometry followed by a secondary setup to machine critical features. Rigid machine tools and precision fastening systems minimize vibration, especially for high-speed machining.
Tool Alignment: Ensuring the cutting tool is at or slightly below the centerline is critical, particularly for turning operations, to prevent chatter and achieve a smooth finish.
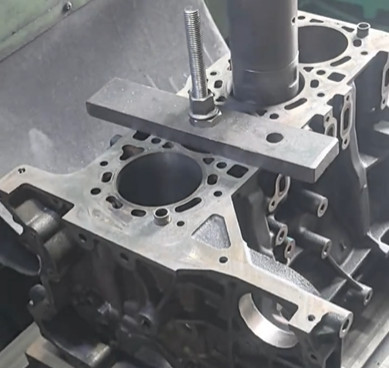
Surface Finishing and Post-Processing
Achieving high-quality surface finishes is a key objective in cast iron machining. Finishing operations focus on minimizing surface irregularities and meeting dimensional tolerances.
Finishing Tools: Carbide end mills (C2 grade) and ceramic inserts are ideal for finishing, achieving surface roughness values of 4-7 Ra. Multi-edge tools with specialized geometries reduce chatter and enhance finish quality.
Post-Processing: Fettling and linishing remove excess material (e.g., runners, risers) and smooth surfaces using abrasive belts or wheels. Shot blasting cleans castings and prepares them for coating or painting, enhancing durability.
Heat Treatment: Heat treatment, such as annealing, improves machinability and reduces internal stresses. For ductile iron, austempering enhances strength and toughness, requiring adjusted machining parameters post-treatment.
Quality Control and Inspection
Quality control ensures cast iron parts meet dimensional and mechanical specifications. Non-destructive testing and metallographic analysis are critical for verifying material integrity.
Metallographic Analysis: Unetched samples are examined to assess graphite morphology, size, and distribution, which influence mechanical properties. Etching with 3% Nital reveals the matrix structure for further evaluation.
Non-Destructive Testing: Ultrasonic thickness gauges (e.g., Nova TG110-DL) measure wall thickness (0.559-1,270 mm) and detect internal flaws. CMM optical scanners and computer tomography ensure dimensional accuracy to tolerances as tight as 0.005 mm.
Surface Roughness: Surface roughness is measured using profilometers, targeting 4-7 Ra for iron castings. Gaussian process regression (GPR) can predict roughness based on cutting parameters, with cutting speed and feed rate having the most significant impact.
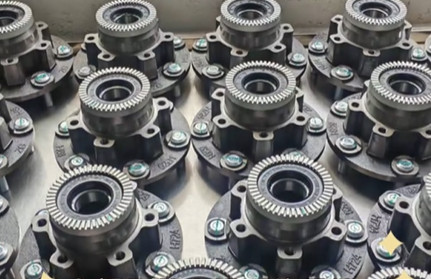
Conclusion
Cast iron remains a cornerstone material in industrial manufacturing due to its versatility, cost-effectiveness, and robust properties. Understanding its types, applications, and machining requirements enables manufacturers to optimize processes and achieve high-quality results. By selecting appropriate tools, cutting parameters, and workholding strategies, and implementing rigorous quality control, cast iron machining can deliver precision components for automotive, machinery, and construction applications.