Alignment pins are critical components in mechanical engineering, used to ensure precise positioning and alignment of parts in assemblies. These pins are essential in industries such as automotive, aerospace, manufacturing, and electronics, where accuracy is paramount. This article provides a detailed overview of alignment pins, including their types, materials, applications, and technical specifications. It is structured to offer a systematic understanding of their design and use in professional settings.
What Are Alignment Pins?
Alignment pins are cylindrical fasteners designed to locate and align components in an assembly with high precision. They ensure that parts are positioned correctly relative to one another, minimizing errors during manufacturing or assembly processes. Alignment pins are typically inserted into pre-drilled holes in mating parts, providing a reference point for accurate positioning. Their primary function is to maintain dimensional accuracy and repeatability in mechanical systems.
These pins are used in applications where tight tolerances are required, such as in jigs, fixtures, and machine tools. By constraining movement in specific directions, alignment pins reduce misalignment and ensure consistent assembly quality. They are available in various types, each suited to specific applications based on design requirements and load conditions.
Types of Alignment Pins
Alignment pins come in several types, each designed for specific purposes. The choice of pin depends on factors such as load-bearing capacity, installation method, and environmental conditions. Below are the primary types of alignment pins used in engineering applications.
Dowel Pins
Dowel pins are the most common type of alignment pins. They are cylindrical, solid pins with tight tolerances, typically used to align components in fixed positions. Dowel pins are often press-fit or slip-fit into holes, providing a secure and precise alignment. They are widely used in machinery, automotive assemblies, and furniture manufacturing.
Dowel pins are manufactured to precise diameters, ensuring a snug fit in corresponding holes. They are available in standard sizes, with diameters ranging from 1/16 inch to 1 inch (1.5 mm to 25 mm) and lengths from 3/16 inch to 6 inches (5 mm to 150 mm). Tolerances for dowel pins are typically in the range of ±0.0001 inches (±0.0025 mm) for high-precision applications.
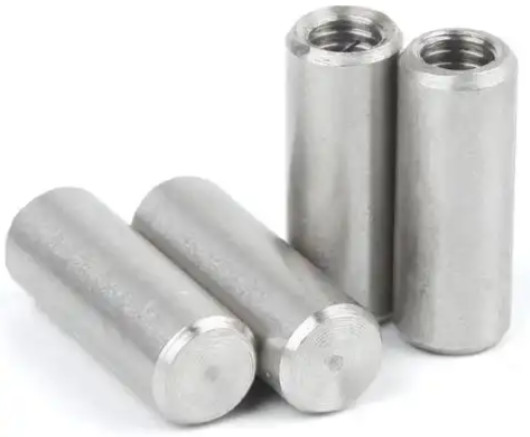
Locating Pins
Locating pins are designed to position workpieces in jigs and fixtures. They often feature a shoulder or flange to limit insertion depth, ensuring consistent positioning. Locating pins can have cylindrical, conical, or stepped profiles, depending on the application. They are commonly used in machining and inspection setups to hold parts securely during processing.
Locating pins are available in both fixed and adjustable configurations. Fixed locating pins are permanently installed, while adjustable pins allow for fine-tuning of position. Common materials include hardened steel and stainless steel, with diameters ranging from 3 mm to 20 mm and lengths up to 100 mm.
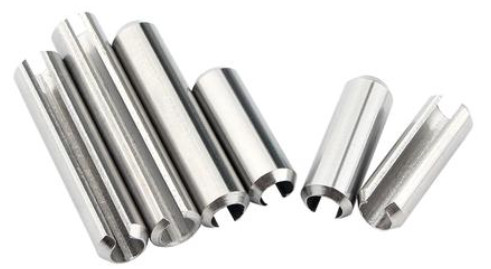
Taper Pins
Taper pins are conical pins that provide a self-locking mechanism due to their tapered shape. They are used in applications requiring a secure fit that can be easily removed for maintenance or disassembly. Taper pins are commonly found in mechanical assemblies, such as gear shafts and pulley systems.
The taper ratio for these pins is typically 1:48 (1 mm of taper per 48 mm of length). Standard sizes range from #0 (smallest) to #10 (largest), with diameters at the large end ranging from 2 mm to 10 mm. Taper pins are often made from carbon steel or stainless steel and require reamed holes for proper installation.
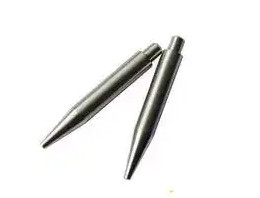
Spring Pins
Spring pins, also known as roll pins, are hollow, slotted pins that compress when inserted into a hole, creating a spring-like effect to hold them in place. They are used for light-duty alignment and are ideal for applications where parts may need frequent disassembly. Spring pins are less precise than dowel pins but are easier to install and remove.
Spring pins are available in diameters from 1 mm to 20 mm and lengths from 5 mm to 100 mm. They are typically made from spring steel or stainless steel, with a slotted design that allows for radial compression.
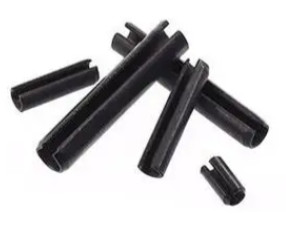
Materials for Alignment Pins
The material of an alignment pin affects its strength, durability, and suitability for specific environments. The choice of material depends on factors such as load requirements, corrosion resistance, and operating conditions. Below are the most common materials used for alignment pins.
Hardened Steel
Hardened steel is the most widely used material for alignment pins due to its high strength and durability. It is heat-treated to achieve a hardness of 50-60 HRC (Rockwell C scale), making it suitable for high-load applications. Hardened steel pins are often used in automotive and aerospace assemblies.
Stainless Steel
Stainless steel alignment pins offer excellent corrosion resistance, making them ideal for applications in harsh environments, such as marine or chemical processing. Common grades include 304 and 316 stainless steel, with 316 offering superior resistance to corrosion. Stainless steel pins have a slightly lower hardness (typically 30-40 HRC) compared to hardened steel.
Alloy Steel
Alloy steel pins are used in applications requiring a balance of strength and toughness. They are often coated with zinc or black oxide to enhance corrosion resistance. Alloy steel is commonly used in heavy machinery and industrial equipment.
Non-Metallic Materials
In some applications, non-metallic materials like nylon or ceramic are used for alignment pins. These materials are chosen for their lightweight properties, electrical insulation, or resistance to specific chemicals. However, non-metallic pins have lower strength and are used in low-load applications, such as electronics or plastic assemblies.
Applications of Alignment Pins
Alignment pins are used across various industries to ensure precision and reliability in mechanical assemblies. Their applications are diverse, ranging from simple fixtures to complex machinery. Below are key applications of alignment pins.
Automotive Industry
In the automotive industry, alignment pins are used to assemble engine components, transmission systems, and chassis parts. Dowel pins ensure precise alignment of engine blocks and cylinder heads, while locating pins are used in assembly jigs to position body panels accurately.
Aerospace Industry
Aerospace applications require alignment pins with high precision and reliability. They are used in the assembly of airframes, turbine engines, and avionics systems. Stainless steel and alloy steel pins are preferred due to their strength and corrosion resistance in high-altitude environments.
Manufacturing and Tooling
In manufacturing, alignment pins are integral to jigs, fixtures, and dies. They ensure that workpieces are positioned correctly during machining, welding, or inspection. Locating pins are commonly used in CNC machining setups to maintain repeatability.
Electronics
In electronics, alignment pins are used to position circuit boards and components during assembly. Non-metallic pins, such as those made from nylon, are often used to avoid electrical conductivity. Precision is critical to ensure proper alignment of connectors and components.
Technical Specifications of Alignment Pins
Alignment pins are manufactured to precise specifications to meet the demands of various applications. The table below provides an overview of common parameters for dowel pins, one of the most widely used types of alignment pins.
Parameter | Specification |
---|---|
Diameter Range | 1/16 inch to 1 inch (1.5 mm to 25 mm) |
Length Range | 3/16 inch to 6 inches (5 mm to 150 mm) |
Tolerance | ±0.0001 inches (±0.0025 mm) |
Material | Hardened Steel, Stainless Steel, Alloy Steel |
Hardness | 50-60 HRC (Hardened Steel), 30-40 HRC (Stainless Steel) |
Surface Finish | 0.8-1.6 µm Ra |
The specifications above are typical for dowel pins but can vary depending on the pin type and application. For example, taper pins have a specific taper ratio, while spring pins have slotted designs that affect their fit and retention.
Installation and Removal Techniques
Proper installation and removal of alignment pins are critical to maintaining their functionality and preventing damage to components. The techniques vary depending on the pin type.
Press-Fit Installation
Press-fit installation is used for dowel pins and some locating pins. The pin is inserted into a hole with a slightly smaller diameter, creating an interference fit. This requires a press or arbor tool to apply controlled force, ensuring the pin is seated without deforming the hole or pin.
Slip-Fit Installation
Slip-fit installation is used for pins that require easy removal, such as locating pins in temporary fixtures. The hole is slightly larger than the pin diameter, allowing the pin to slide in and out with minimal force. Precision machining of the hole is essential to maintain alignment accuracy.
Reaming for Taper Pins
Taper pins require a reamed hole with a matching taper to ensure a secure fit. A tapered reamer is used to prepare the hole, and the pin is driven in with a hammer or press. Removal typically involves tapping the small end of the pin to dislodge it.
Spring Pin Installation
Spring pins are installed by compressing the pin and inserting it into a hole. A hammer or press can be used, but care must be taken to avoid damaging the slotted structure. Removal involves driving the pin out with a punch or drift.
Standards and Certifications
Alignment pins are manufactured to industry standards to ensure consistency and reliability. Common standards include:
- ISO 8734: Specifies dimensions and tolerances for parallel dowel pins.
- ASME B18.8.2: Covers dowel pins used in the United States, including material and dimensional requirements.
- DIN 6325: Defines tolerances for hardened steel dowel pins in metric sizes.
- ISO 2338: Specifies unhardened parallel pins for general use.
Certifications such as ISO 9001 ensure that manufacturers adhere to quality management systems, guaranteeing consistent production of alignment pins.
Conclusion
Alignment pins are essential components in precision engineering, providing accurate positioning and alignment in a wide range of applications. From dowel pins to spring pins, each type serves a specific purpose, with materials and specifications tailored to meet industry demands. By understanding the types, materials, applications, and installation techniques, engineers and manufacturers can select the appropriate alignment pins for their projects. Adhering to industry standards ensures reliability and performance, making alignment pins a cornerstone of high-quality mechanical assemblies.