The motor shaft stands as a cornerstone in electric motors, tasked with transmitting torque and rotational motion to power machinery across diverse sectors, including automotive, aerospace, industrial equipment, and consumer appliances. Its production demands unparalleled precision, durability, and reliability, as even minor deviations can compromise motor efficiency, performance, and longevity. This article provides a thorough exploration of motor shaft machining, encompassing design, materials, processes, technologies, challenges, and optimization strategies. Drawing on advanced services like those offered by KeSu, we also spotlight the critical role of low-volume prototyping and production in accelerating innovation and ensuring quality, offering insights into how modern manufacturing meets the needs of both niche and high-performance applications.
Overview of Motor Shaft Machining
A motor shaft is a cylindrical metal component that converts electrical energy into mechanical energy, channeling power through gears, pulleys, or couplings to drive systems. Its design is highly variable, tailored to meet specific mechanical and environmental demands, making it both versatile and complex to manufacture. Key characteristics include:
- Types: Options range from solid shafts for heavy-duty applications to hollow shafts for weight reduction, tapered shafts for specialized fittings, keyed shafts for secure power transmission, splined shafts for high-torque systems, and threaded shafts for adjustable connections.
- Dimensions: Diameters span from a few millimeters in micro motors for precision devices to tens of centimeters in industrial motors for heavy machinery, with lengths customized to fit specific designs.
- Precision Requirements: Tolerances are stringent, typically ranging from ±0.01 mm for standard applications to ±0.0002 mm for high-precision systems, ensuring minimal vibration and optimal power transfer.
- Surface Quality: A smooth surface is essential to reduce friction and wear, with surface roughness (Ra) maintained between 0.2 and 0.8 μm to enhance durability and efficiency.
Machining motor shafts involves a sophisticated blend of Computer Numerical Control (CNC) technologies, material science, and post-processing techniques. The objective is to produce components that adhere to exacting design specifications while delivering long-term reliability. In low-volume production and prototyping, as exemplified by KeSu’s services, manufacturers prioritize flexibility, rapid iteration, and cost efficiency. These capabilities allow for quick validation of designs, enabling engineers to refine motor shafts for applications ranging from electric vehicle drivetrains to aerospace actuators, ensuring performance before scaling to mass production.
KeSu’s motor shaft prototyping services emphasize precision and speed, leveraging advanced CNC machining to produce prototypes in as little as 2-3 days. This rapid turnaround is critical for industries where time-to-market is a competitive factor, allowing designers to test multiple iterations without significant delays or costs.
Machining Process
Producing a motor shaft is a multi-faceted process that requires meticulous control at every stage to meet design and performance standards. From initial planning to final testing, each step is optimized to ensure quality and functionality. Below, we outline the key phases, highlighting how low-volume prototyping enhances efficiency and innovation.
Design and Planning
The journey begins with a detailed analysis of the shaft’s operational requirements:
- Load Analysis: Engineers evaluate torque, bending forces, axial loads, rotational speed, and environmental conditions—such as exposure to high temperatures or corrosive substances—to define the shaft’s mechanical demands.
- Dimension Calculations: The shaft’s diameter and length are calculated to resist torsion and deflection, using formulas such as:
\(\tau = \frac{T \cdot r}{J}, \quad J = \frac{\pi r^4}{2} \text{ (for solid cylindrical shafts)}\)
In this equation, \(\tau\) denotes shear stress, \(T\) is torque, \(r\) is the radius, and \(J\) is the polar moment of inertia. These calculations ensure the shaft can endure operational stresses without deformation or failure.
- CAD Modeling: Tools like SolidWorks or AutoCAD enable the creation of precise 3D models, incorporating features such as keyways, splines, or diameter transitions. In prototyping, these models are iterated quickly to test various configurations, a process streamlined by services like KeSu’s, which offer rapid design adjustments.
- Finite Element Analysis (FEA): Simulations assess stress distribution under real-world conditions, pinpointing potential weak points and optimizing the design. For prototypes, FEA is invaluable for validating concepts early, reducing the risk of costly revisions later.
In low-volume prototyping, rapid design iteration is a game-changer. KeSu’s expertise in CNC machining allows engineers to refine CAD models swiftly, producing prototypes that can be tested and modified within days. This agility is particularly beneficial for industries like automotive, where motor shafts must meet evolving standards for electric vehicle performance, or aerospace, where lightweight yet robust designs are critical.
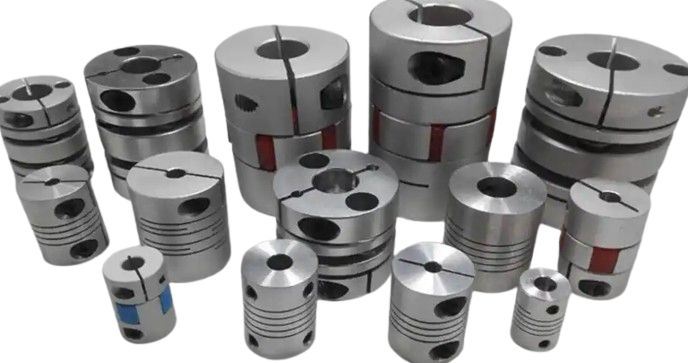
Material Selection
Material choice is a pivotal decision that affects the shaft’s strength, weight, corrosion resistance, and cost. The following table summarizes common materials used in motor shaft production:
Material | Properties | Applications | Cost |
---|---|---|---|
Carbon Steel (e.g., 1045) | High machinability, moderate strength, and hardness | General-purpose motor shafts for industrial motors | Low |
Stainless Steel (e.g., 304, 316) | Excellent corrosion resistance | Marine, chemical, or food processing environments | Moderate |
Alloy Steel (e.g., 4140, 4340) | High strength and toughness | Heavy-duty automotive or industrial shafts | High |
Aluminum | Lightweight, corrosion-resistant | Low-load aerospace or consumer electronics | Moderate |
Titanium | High strength-to-weight ratio, corrosion-resistant | High-performance aerospace or medical motors | Very High |
Material selection balances performance and cost. Carbon steel is economical for standard applications, while titanium is reserved for high-end uses due to its superior properties but higher cost. Heat treatments, such as quenching or tempering, can enhance material characteristics like hardness and durability. In prototyping, flexibility in material choice is crucial. KeSu offers a broad range of metals and engineering plastics, enabling clients to experiment with different materials to optimize performance and cost. For example, a prototype shaft for an electric vehicle motor might be tested in both aluminum and alloy steel to compare weight versus strength before finalizing the design.
Prototyping also allows for the exploration of advanced materials, such as composites or specialized alloys, which can offer unique advantages in niche applications. KeSu’s ability to machine a variety of materials ensures that prototypes accurately reflect the intended production specifications, facilitating seamless transitions to full-scale manufacturing.
Blank Preparation
The process starts with preparing the raw material, known as the blank:
- Blank Type: Manufacturers typically use hot-rolled or cold-rolled bars. Cold-rolled bars offer superior surface quality and dimensional accuracy but cost about 15% more, making them ideal for high-precision prototypes.
- Initial Cutting: Bars are cut to near-final length using band saws or automated cutting machines, ensuring minimal material waste and precise starting dimensions.
In low-volume production, blank preparation is optimized for efficiency. KeSu’s automated cutting processes ensure consistency, even for small batches, reducing setup times and costs compared to traditional high-volume methods.
Core Machining Technologies
Motor shaft machining relies on a suite of CNC techniques, each tailored to specific features of the shaft:
- Turning: CNC lathes shape the blank into a cylindrical form, controlling diameter and length with tolerances as tight as ±0.01 mm. For instance, reducing a diameter from 50 mm to 30 mm while maintaining concentricity is a common task in shaft production.
- Milling: Multi-axis CNC milling machines create keyways, splines, flats, or grooves, achieving tolerances like ±0.02 mm for keyway widths, essential for fitting gears or couplings.
- Grinding: Precision grinding delivers smooth surfaces and tight tolerances (±0.0002 mm), reducing surface roughness to Ra 0.4 μm using cylindrical or centerless grinders, critical for high-speed applications.
- Drilling: CNC drills produce through-holes or blind holes for hollow shafts or bolt installations, ensuring coaxiality and positional accuracy.
- Electrical Discharge Machining (EDM): Ideal for hard materials or intricate shapes like splines or micro-holes, EDM offers high precision but is slower, often used in prototyping complex designs.
- Threading: Internal or external threads are created for threaded shafts, adhering to standards like ISO M10, ensuring compatibility with mating components.
KeSu’s advanced 3-, 4-, and 5-axis CNC machines enable the production of complex motor shafts with minimal setups, enhancing accuracy and reducing lead times. For low-volume prototypes, this multi-axis capability is particularly valuable, allowing manufacturers to produce intricate features like splines or tapered sections in a single operation, streamlining the testing phase.
In practice, a prototype shaft for a drone motor might require a combination of turning for the main body, milling for a spline to connect to a propeller, and grinding to achieve a mirror-like finish. KeSu’s ability to integrate these processes ensures that prototypes are both functional and representative of final production parts.
Heat Treatment
Heat treatment enhances the mechanical properties of motor shafts:
- Quenching and Tempering: Increases hardness and strength while relieving internal stresses, achieving hardness levels like 50-55 HRC for 4140 steel.
- Carburizing or Nitriding: Boosts surface hardness and wear resistance, ideal for high-load shafts in industrial or automotive applications.
- Annealing: Reduces CNC machining stresses and improves workability, often used before final machining steps.
Post-treatment checks for deformation are essential, with straightening applied if needed. In prototyping, heat treatment is carefully controlled to ensure consistency, as variations can affect performance evaluations. KeSu’s in-house heat treatment capabilities allow for precise application, ensuring prototypes meet the same standards as production parts.
Surface Treatment
Surface treatments improve performance and aesthetics:
- Polishing: Reduces surface roughness to minimize friction losses, enhancing efficiency in high-speed motors.
- Plating: Chrome or nickel plating enhances corrosion and wear resistance, suitable for harsh environments like marine applications.
- Sandblasting: Improves surface texture in non-contact areas, often used for visual appeal in consumer products.
KeSu offers a range of surface finishes, from standard machined finishes (Ra 3.2 μm) to polished or coated surfaces, allowing clients to test different treatments during prototyping. For example, a shaft prototype for a medical device might undergo passivation to ensure biocompatibility, while an automotive shaft might be chrome-plated for durability.
Quality Control
Quality assurance is integral to motor shaft production:
- Dimensional Inspection: Coordinate Measuring Machines (CMM) or laser scanners verify diameters, keyway positions, and tolerances with precision.
- Surface Quality: Surface roughness measurements ensure Ra values align with specifications, critical for reducing wear.
- Non-Destructive Testing (NDT): Ultrasonic or magnetic particle testing detects internal cracks or defects, ensuring structural integrity.
- Dynamic Balancing: High-speed shafts are balanced to minimize vibration, a key requirement for applications like electric vehicle motors.
KeSu’s rigorous quality control processes, including ISO 9001-certified protocols, ensure that prototypes and low-volume parts meet exacting standards. For instance, a prototype shaft for a robotics application might undergo CMM inspection to verify spline geometry, followed by dynamic balancing to confirm performance at high RPMs.
Assembly and Final Testing
The shaft is assembled with components like gears, bearings, or couplings, with fit accuracy meticulously verified. Functional tests simulate real-world conditions, measuring vibration, noise, and torque transmission to ensure performance. In prototyping, these tests are critical for validating design assumptions. KeSu’s ability to produce fully assembled prototypes allows clients to evaluate the shaft in its intended system, identifying issues like misalignment or excessive vibration before production.
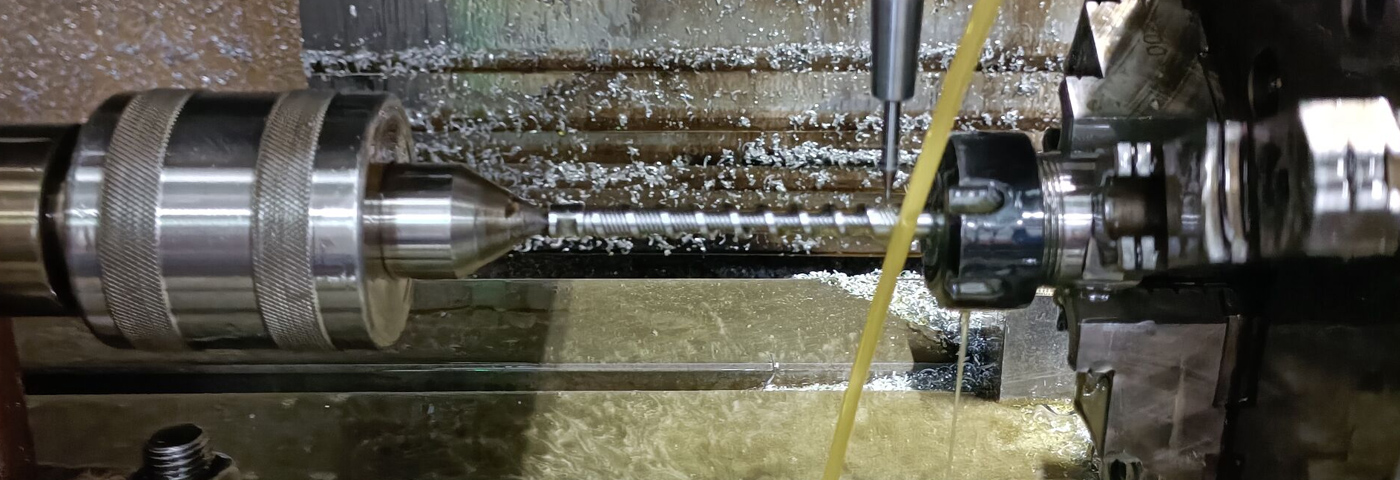
Find out Motor shaft CNC machining
Let our motor shafts power your equipment with unmatched strength!
Connect with our sales team for a free quote or technical consultation.
Key Technologies and Challenges
Motor shaft machining leverages cutting-edge technologies but faces significant challenges, particularly in achieving precision, managing costs, and ensuring durability. Below, we explore these issues and their solutions, with a focus on how prototyping addresses them.
High-Precision Machining
Challenge: High-speed motors, such as those in electric vehicles or drones, demand extreme concentricity and surface finish, with tolerances as low as ±0.0002 mm to prevent vibration and energy loss.
Solutions:
- Deploy high-precision CNC machines, such as Swiss-type lathes, for consistent accuracy.
- Use multi-axis machining to minimize clamping errors, reducing setup variations.
- Implement in-line measurement systems for real-time dimension monitoring, ensuring adherence to tolerances.
KeSu’s 5-axis CNC machines excel in producing high-precision prototypes, allowing for complex geometries to be machined in a single setup, which is critical for testing intricate shaft designs.
Material Machinability
Challenge: Hard materials like titanium alloys are difficult to machine, causing rapid tool wear, while hot-rolled steel may contain hard spots or inclusions that affect consistency.
Solutions:
- Employ advanced tool coatings, such as TiAlN, to extend tool life and improve cutting efficiency.
- Optimize cutting parameters, like low speed and high feed rates, to minimize heat generation and tool degradation.
- Use cold-rolled or free-machining steels, such as SAE 1117, for improved machinability in prototypes.
Prototyping allows manufacturers to test material machinability early. KeSu’s experience with diverse materials ensures that prototype shafts perform reliably, whether machined from stainless steel for corrosion resistance or titanium for aerospace applications.
Complex Geometries
Challenge: Features like splines, keyways, or tapered designs increase machining complexity, often requiring multiple operations and setups.
Solutions:
- Use 5-axis CNC milling machines to produce complex shapes in a single setup, enhancing accuracy.
- Employ specialized fixtures to ensure precise positioning during CNC machining.
KeSu’s multi-axis machining capabilities streamline the production of complex prototype shafts, enabling features like splines or helical grooves to be tested efficiently, reducing the need for costly reworks.
Cost Control
Challenge: High-precision machining and premium materials drive up costs, particularly in low-volume production, where economies of scale are limited.
Solutions:
- Implement automated loading/unloading systems, such as robotic arms, to boost efficiency by 30-50%.
- Optimize process paths to reduce machining time, leveraging CAD/CAM software for efficiency.
- Substitute cost-effective materials, like 1045 steel, for some alloy steels in non-critical applications.
Low-volume prototyping inherently focuses on cost efficiency. KeSu’s streamlined processes, including competitive pricing and rapid turnaround, make it feasible to produce small batches without excessive costs, ideal for startups or R&D projects.
Fatigue and Failure
Challenge: Motor shafts under cyclic loads are prone to fatigue fractures, particularly at stress concentration points like keyways or threads.
Solutions:
- Incorporate fillets, such as R0.5 mm at keyways, to reduce stress concentrations.
- Conduct fatigue analysis to ensure a safety factor of 2-10, depending on the application.
- Apply surface strengthening techniques, like rolling or shot peening, to enhance fatigue life.
Prototyping allows for fatigue testing early in development. KeSu’s ability to produce shafts with precise surface treatments ensures that prototypes can be stress-tested to validate durability, preventing failures in production.
Applications and Trends in Motor Shaft Machining
Motor shafts serve a wide array of applications, each with unique demands:
- Automotive: Electric vehicle motors require lightweight, high-strength shafts to maximize efficiency and range. Prototyping is critical to test designs under high RPMs.
- Aerospace: Shafts in actuators or propulsion systems demand precision and durability, often using titanium or composites to reduce weight.
- Industrial Machinery: Heavy-duty shafts in pumps or compressors need robust materials and wear-resistant coatings to handle continuous operation.
- Consumer Electronics: Micro motor shafts in devices like drones or cameras require ultra-precise machining to ensure compact, reliable performance.
Emerging trends are shaping motor shaft CNC machining. The rise of electric vehicles has increased demand for high-efficiency shafts, driving innovations in lightweight materials and precision manufacturing. Additive manufacturing is also gaining traction for prototyping, allowing complex internal geometries to be tested before CNC machining. Additionally, automation and AI-driven process optimization are reducing costs and improving consistency, particularly in low-volume production.
KeSu’s services align with these trends, offering rapid prototyping to test innovative designs and low-volume production to bridge the gap to mass manufacturing. Their focus on advanced materials and multi-axis machining positions them as a leader in meeting modern demands.
Conclusion
Motor shaft machining is a sophisticated, precision-driven discipline that integrates advanced technologies, material science, and rigorous quality control to produce components vital to modern machinery. From design and material selection to machining, heat treatment, and testing, each stage is meticulously executed to meet stringent performance standards. The advent of low-volume prototyping, as exemplified by KeSu’s rapid and precise services, has revolutionized the process, enabling manufacturers to innovate swiftly and cost-effectively. Despite challenges like high-precision demands, material machinability, and cost pressures, advancements in CNC technology, automation, and process optimization are driving progress. By leveraging these capabilities, manufacturers can deliver reliable, high-performance motor shafts that power everything from electric vehicles to aerospace systems, meeting the diverse needs of today’s dynamic industries.
FAQ
What is a motor shaft, and why is it important?
A motor shaft is a cylindrical component that transmits torque and rotational motion in electric motors. It’s critical because it converts electrical energy into mechanical power, directly influencing motor efficiency, performance, and durability across applications.
What materials are commonly used for motor shafts?
Common materials include carbon steel (e.g., 1045) for cost-effective strength, stainless steel (e.g., 304, 316) for corrosion resistance, alloy steel (e.g., 4140, 4340) for heavy-duty use, aluminum for lightweight applications, and titanium for high-performance needs.
How does prototyping benefit motor shaft development?
Prototyping allows designers to test and refine shaft designs quickly, validating performance, fit, and durability before production. Services like KeSu’s enable rapid iteration, reducing costs and time-to-market while ensuring quality.
What are the main challenges in motor shaft machining?
Challenges include achieving ultra-tight tolerances, machining hard materials, creating complex geometries, controlling costs, and preventing fatigue failures. Advanced CNC machines, optimized processes, and prototyping address these issues effectively.
How does low-volume production differ from mass production?
Low-volume production focuses on small batches (tens to thousands), offering flexibility and cost efficiency for prototyping or niche markets. Mass production targets large volumes, prioritizing economies of scale but requiring significant upfront investment.