The front valve body, a critical component in railway coupling systems, is a complex, irregularly shaped part that poses significant machining challenges. With increasing demands for product diversity and stringent quality requirements in the railway industry, traditional machining methods using conventional lathes and four-jaw chucks have proven inefficient. This article outlines a systematic approach to improving the machining pass rate of front valve body parts by implementing specialized chuck jaw modifications and transitioning to CNC lathe processing. The result is a significant reduction in auxiliary time, improved precision, and a pass rate increase to 99%, with processing time reduced from 60 minutes to 10 minutes per part.
Structural Characteristics and Technical Requirements of the Front Valve Body
The front valve body is a rostfreier Stahl forged part (material: ZG0Cr18Ni9) used in the BP valve of railway coupling systems. After solution treatment, it achieves a hardness of 170–200 HB, making it relatively easy to machine but prone to surface hardening during cutting. The part features a diamond-shaped geometry with complex surfaces, including external and internal grooves, chamfers, and rounded corners. Its technical requirements are stringent:
- Unspecified fillet radii range from R2 to R5 mm.
- Machined dimensions without tolerances follow GB/T 1804–2000 (Class M for linear and angular dimensions).
- Cast dimensions adhere to GB/T 6414–1999 (CT10 level for dimensional tolerances and machining allowances).
- Sharp edges must be deburred.
- Surface quality and dimensional accuracy are critical to ensure functionality in railway applications.
The part’s complex geometry, including external and internal contours, requires präzise Bearbeitung to meet dimensional tolerances and surface quality standards. The combination of material properties and geometric complexity necessitates advanced machining strategies to achieve high efficiency and quality.
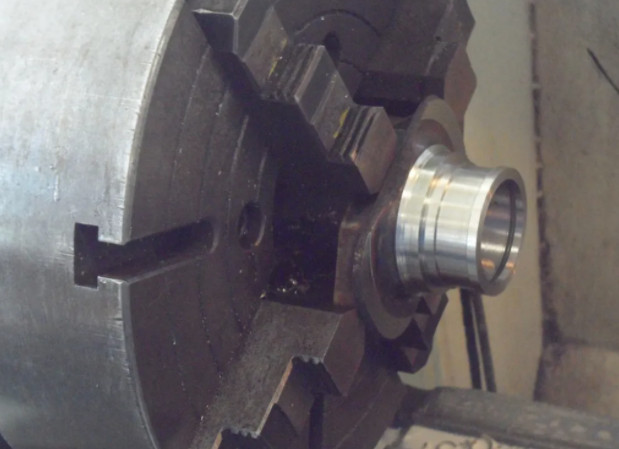
Issues with Traditional Machining Processes
The original machining process relied on conventional lathes with a four-jaw independent chuck, which presented several limitations:
- Material Machining Challenges: The ZG0Cr18Ni9 stainless steel, while machinable, tends to harden on the surface during cutting, accelerating tool wear and affecting surface quality. The material’s poor heat dissipation requires separating rough and finish machining, with a cooling period between steps to prevent dimensional inaccuracies due to thermal expansion.
- Clamping Inefficiencies: The four-jaw independent chuck requires individual adjustment of each jaw, making alignment time-consuming and prone to errors. Axial positioning is not possible, and machining one end requires switching to a three-jaw self-centering chuck for the other end, increasing auxiliary time. This process is labor-intensive and fatiguing for operators.
- Tooling Limitations: Conventional lathe tool posts accommodate up to four tools, but the front valve body requires at least five tools to machine external grooves, internal grooves, chamfers, and rounded corners. Frequent tool changes and re-alignments reduce efficiency and demand high operator skill.
- Low Efficiency and Quality: The combination of manual clamping adjustments, multiple tool changes, and cooling periods results in a processing time of approximately 60 minutes per part. The pass rate is inconsistent due to alignment errors and surface quality issues, failing to meet modern production demands.
Process Improvements for Enhanced Efficiency and Quality
To address the limitations of the traditional process, a two-pronged improvement strategy was implemented: specialized chuck jaw modification and adoption of CNC lathe machining. These changes optimized clamping stability, reduced auxiliary time, and improved machining precision.
Specialized Chuck Jaw Modification
The traditional four-jaw independent chuck was replaced with a modified three-jaw self-centering chuck featuring custom-designed jaws tailored to the front valve body’s geometry. The modification process involved:
- Design and Programming: Using NX software, a program was developed to machine the jaw contours to match the part’s external profile. The jaws were processed on a vertical machining center to ensure precision.
- Jaw Specifications: The jaws were machined to a depth of 10 mm to provide axial positioning, eliminating the need for manual alignment. Integral jaws were used instead of detachable ones to avoid complications from screw holes, ensuring a robust and repeatable clamping surface.
- Clamping Process: The modified jaws enable rapid clamping within seconds, as the part’s external profile aligns precisely with the jaw contours. Pre-clamping deburring of the part’s edges ensures accurate positioning.
This modification allows for stable, repeatable clamping with minimal setup time, addressing the inefficiencies of the four-jaw chuck. The axial positioning feature ensures consistent part orientation, reducing errors and auxiliary time.
Transition to CNC Lathe Machining
Replacing conventional lathes with CNC lathes significantly enhanced machining efficiency and quality. The key aspects of this transition include:
- Tooling Flexibility: CNC lathes accommodate a four-tool turret, sufficient to machine all required features (external and internal grooves, chamfers, and rounded corners) in a single setup, eliminating the need for frequent tool changes.
- Programmed Precision: CNC programming ensures consistent tool paths, reducing operator dependency and improving dimensional accuracy. The automated process minimizes human error and maintains tight tolerances.
- Reduced Cooling Time: CNC lathes enable optimized cutting parameters, reducing heat buildup and allowing rough and finish machining in closer succession, minimizing cooling delays.
- Enhanced Surface Quality: The precision of CNC machining results in superior surface finishes, meeting the stringent appearance and functional requirements of railway components.
The CNC lathe’s high flexibility and automation capabilities reduced processing time to approximately 10 minutes per part, a 70% improvement over the conventional method. The pass rate increased to 99%, driven by stable clamping and precise machining.
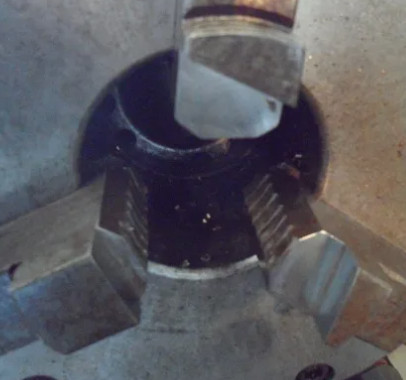
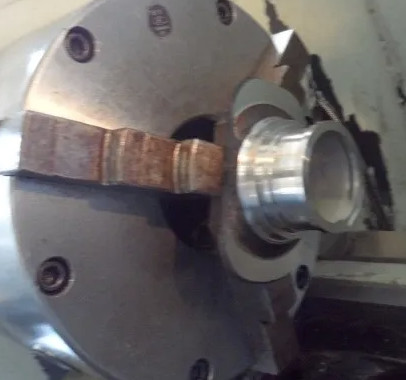
Optimized Machining Process Flow
The improved process flow is as follows:
Step | Operation | Beschreibung |
---|---|---|
1 | Rough Face Turning | Machine the end face to establish a reference surface. |
2 | Rough External Turning | Turn external contours and fillets (R2–R5 mm). |
3 | Rough Internal Turning | Machine internal bores and chamfers. |
4 | Rough External Grooving | Create external grooves as per design specifications. |
5 | Rough Internal Grooving | Machine internal grooves. |
6 | Finish Face Turning | Refine the end face to meet dimensional tolerances. |
7 | Finish External Turning | Complete external contours and fillets with high precision. |
8 | Finish External Grooving | Refine external grooves for accuracy and surface quality. |
9 | Finish Internal Turning | Complete internal bores and chamfers to final specifications. |
10 | Finish Internal Grooving | Refine internal grooves for precision and finish. |
11 | Part Reorientation | Flip the part to machine the opposite end face. |
12 | Rough and Finish Face Turning | Machine the second end face to complete the part. |
This streamlined process minimizes tool changes and clamping adjustments, ensuring efficiency and consistency.
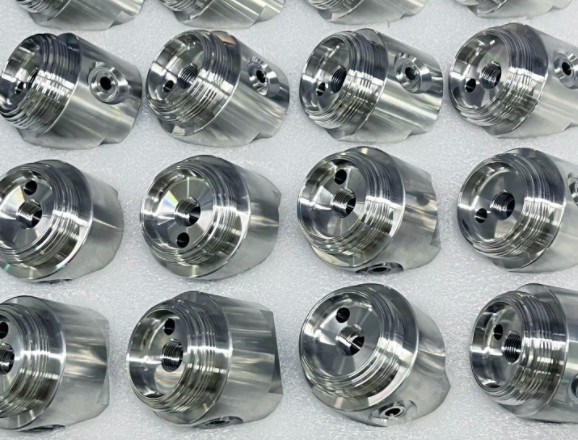
Results and Benefits of the Improved Process
The implementation of specialized chuck jaws and CNC lathe machining yielded significant improvements:
Metric | Traditional Process | Improved Process |
---|---|---|
Processing Time per Part | 60 minutes | 10 minutes |
Pass Rate | Inconsistent (approx. 80–90%) | 99% |
Tool Changes | Multiple (≥5 tools) | Single setup (4 tools) |
Clamping Time | High (manual adjustment) | Seconds (automated) |
Operator Skill Requirement | Hoch | Mäßig |
Additional benefits include:
- Reduced Labor Intensity: Automated clamping and CNC machining lower the physical and skill demands on operators.
- Kosteneffizienz: Faster processing and fewer tool changes reduce operational costs.
- Reliable Quality: Consistent dimensions and surface quality ensure compliance with railway industry standards.
- Timely Delivery: The shortened cycle time enables meeting tight production schedules.
Schlussfolgerung
The transformation of the front valve body machining process through specialized chuck jaw modifications and CNC lathe adoption demonstrates a practical, efficient, and reliable approach to addressing the challenges of complex part machining. The redesigned chuck jaws enable rapid, stable clamping, while CNC lathes provide precision and flexibility, reducing processing time by 83% and achieving a 99% pass rate. This methodology offers a replicable framework for machining similar irregularly shaped parts, providing a balance of efficiency, quality, and cost-effectiveness for high-demand industries like railway manufacturing.