Polishing is a critical surface finishing process in mechanical engineering that enhances the aesthetic and functional quality of workpieces by achieving a smooth, mirror-like surface. This article provides a detailed exploration of polishing principles, methods, materials, and operational techniques, offering practical insights for achieving high-quality surface finishes.
Principles of Polishing
Polishing involves the use of an elastic polishing wheel, either bonded or coated with abrasives, to perform soft grinding on a workpiece under high-speed rotation. The process removes micro-imperfections, resulting in a glossy surface. Polishing is typically divided into three stages: rough polishing, intermediate polishing, and fine polishing. Each stage employs specific tools, abrasives, and techniques to progressively refine the surface. The following are the primary polishing methods based on abrasive application:
Fixed Abrasive Polishing
In fixed abrasive polishing, abrasives are securely bonded to the polishing wheel using an adhesive, resembling grinding processes like those using grinding wheels or abrasive belts. The wheel rotates in the same direction as the workpiece feed to ensure a glossy finish. If the directions are opposite, the abrasives may cause scratches, resulting in a rougher surface. This method is effective for rough polishing due to its high cutting force, suitable for initial surface preparation.
Adhesive Abrasive Polishing
Adhesive abrasive polishing uses a polishing wheel with abrasives adhered using grease or similar media. Under applied force, the abrasives roll slowly within the lubricant, allowing all cutting edges to engage, maintaining the wheel’s long-term effectiveness. Friction heat and processing pressure trigger chemical reactions between the polishing agent’s fatty acids and the metal surface, forming compounds that are easily removed, thus enhancing polishing efficiency. This method is ideal for intermediate and fine polishing stages.
Liquid Polishing
Liquid polishing employs a polishing wheel made of highly absorbent materials, such as degreased wood or fine felt, impregnated with a polishing liquid containing abrasives. The process progresses through four stages: free polishing, embedded polishing, saturated passivation polishing, and shell-film polishing. When using fine felt wheels, the process may skip the free polishing stage due to the material’s softness and high absorbency, reducing overall polishing time. This method is particularly effective for complex surfaces requiring uniform finishing.
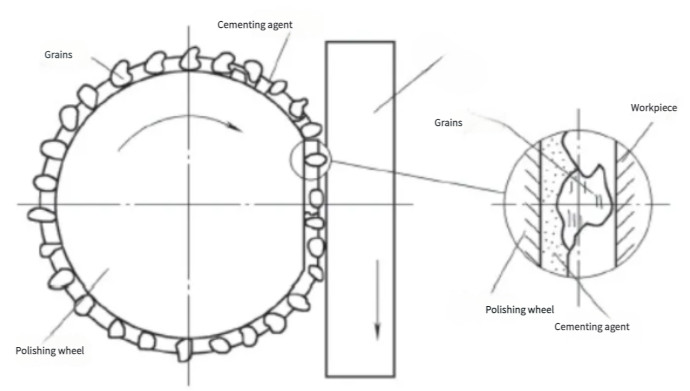
Polishing Wheel Materials
The choice of polishing wheel material significantly impacts the efficiency and quality of the polishing process. Common materials include cotton cloth, hemp, felt, leather, hard paper, softwood, and woolen fabrics, selected for their flexibility and compatibility with polishing agents. The material properties are tailored through preprocessing to enhance rigidity, durability, flexibility, and lubricant retention. Common treatments include bleaching, sizing, waxing, resin coating, and chemical processing.
For rough polishing, harder materials like canvas, felt, hard paper, cork, leather, or hemp are preferred to withstand higher polishing forces and improve efficiency. For intermediate and fine polishing, softer materials such as cotton cloth and felt are used due to their excellent flexibility and ability to retain polishing agents. The wheel’s elasticity and rigidity can be adjusted by altering stitching patterns (e.g., spiral, concentric, checkered, or radial) and stitch spacing. Larger stitch intervals increase elasticity, while smaller intervals enhance rigidity.
Polishing Stage | Recommended Materials | Eigenschaften |
---|---|---|
Rough Polishing | Canvas, Felt, Hard Paper, Cork, Leather, Hemp | High rigidity, withstands high pressure |
Intermediate/Fine Polishing | Cotton Cloth, Felt | High flexibility, excellent polishing agent retention |
Selection of Polishing Agents
Polishing agents are mixtures of abrasive powders, grease, or other media, formulated to suit specific materials and polishing stages. They are available in solid and liquid forms, with solid agents being the most widely used. Solid polishing agents are categorized into grease-based and non-grease-based types, while liquid agents include emulsified, grease-based, and non-grease-based variants.
Common solid polishing agents include:
- Sezar Polishing Paste (Fused Alumina): Suitable for rough polishing of carbon steel, stainless steel, and non-ferrous metals.
- Emery Paste (Fused Alumina, Silicon Carbide): Used for rough and intermediate polishing of carbon steel and stainless steel.
- Yellow Polishing Paste (Diatomaceous Earth): Applied for intermediate polishing of iron, brass, aluminum, and zinc.
- Bar-Shaped Iron Oxide: Ideal for intermediate and fine polishing of copper, brass, aluminum, and copper-plated surfaces.
- White Polishing Paste (Calcined Dolomite): Used for fine polishing of copper, brass, aluminum, copper-plated, and nickel-plated surfaces.
- Green Polishing Paste (Chromium Oxide): Employed for fine polishing of stainless steel, brass, and chrome-plated surfaces.
- Red Polishing Paste (Refined Iron Oxide): Suitable for fine polishing of gold, silver, and platinum.
- Plastic Polishing Agent (Microcrystalline Anhydrous Carbonate): Used for fine polishing of plastics, leather, and ivory.
Liquid polishing agents typically consist of chromium oxide mixed with an emulsion, used for specialized applications requiring fluid delivery of abrasives.
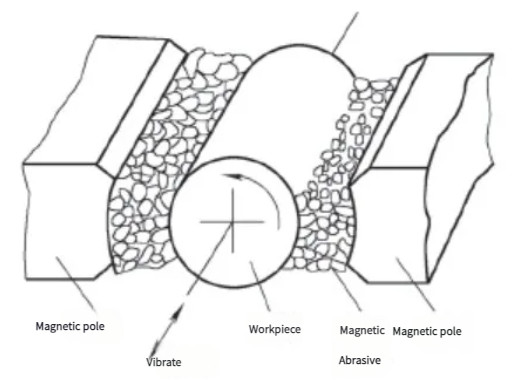
Abrasive Grain Size Selection
The grain size of abrasives in polishing agents directly affects surface roughness and polishing efficiency. Coarser grains result in higher surface roughness (larger Ra values) but offer greater material removal rates, while finer grains produce smoother surfaces (smaller Ra values) at the cost of lower efficiency. The following table outlines recommended grain sizes for specific surface roughness requirements:
Surface Roughness (Ra, μm) | Abrasive Grain Size |
---|---|
1.6–3.2 | F46–F60 |
0.4–0.8 | F100–F180 |
0.1–0.2 | F240–W28 |
0.025–0.05 | W20–W5 |
≤0.012 | <W5 |
When transitioning between polishing stages, it is critical to use a new polishing wheel to prevent contamination from coarser abrasive grains, which could compromise the surface finish.
Polishing Speed and Pressure
The polishing wheel’s peripheral speed and applied pressure are key parameters influencing efficiency and surface quality.
Peripheral Speed
Higher peripheral speeds reduce the cutting depth of abrasives, lowering surface roughness and increasing polishing efficiency. Recommended speeds vary by material:
- Steel, Cast Iron, Nickel, Chromium: 30–35 m/s
- Copper, Copper Alloys, Silver: 20–30 m/s
- Aluminium, Aluminum Alloys, Zinc, Tin: 18–25 m/s
Optimal speed selection balances safety, efficiency, and quality based on specific workpiece requirements.
Druck
Pressure affects material removal rates and surface quality. Higher pressures (10–30 MPa) are used in rough polishing to maximize efficiency, while lower pressures (5–10 MPa) are applied in fine polishing to enhance surface smoothness. Proper pressure calibration ensures consistent results without damaging the workpiece.
Alternative Polishing Techniques
Beyond wheel-based polishing, several specialized techniques are employed for specific applications:
Sandpaper/Sandcloth Polishing
This traditional method is versatile and can be performed manually or on lathes and grinders. Sandcloth with grain sizes of F150–F240 is used to achieve surface roughness values of Ra 0.1–0.8 μm. For complex geometries like inner holes or grooves, sandcloth impellers—resin-bonded abrasive sheets arranged in an involute pattern—are used for their flexibility and high-density abrasive distribution.
Liquid Polishing
Liquid polishing involves spraying a suspension of abrasives and liquid onto the workpiece surface at high speed using compressed air. This method achieves Ra values of 0.05–0.1 μm from an initial Ra of 0.2 μm, making it suitable for hard-to-reach surfaces like small holes, complex profiles, and narrow grooves.
Electrochemical-Mechanical Composite Polishing
This method combines electrolytic dissolution and mechanical abrasion. The workpiece (anode) and polishing head (cathode) are immersed in an electrolyte, with the polishing head rotating under pressure. The electrolyte forms a thin passivation film on the workpiece surface, which is easily removed by abrasives, achieving high efficiency and quality at low cost.
Ultrasonic-Electric Discharge Composite Polishing
Combining ultrasonic grinding and electric discharge, this method is three times more efficient than standalone ultrasonic polishing. It is ideal for small holes, narrow slots, and precision surfaces, achieving Ra values of 0.08–0.16 μm.
Magnetic Abrasive Polishing
Magnetic abrasives are aligned along magnetic field lines to form a “magnetic brush” that polishes the workpiece surface as it moves between magnetic poles. This technique achieves Ra values of 0.2 μm in 8–12 seconds, suitable for intricate geometries.
Schlussfolgerung
Polishing is a versatile and widely adopted surface finishing technique in mechanical processing, supported by both traditional practices and modern methodologies. By carefully selecting polishing wheels, agents, abrasive grain sizes, speeds, and pressures, manufacturers can achieve mirror-like finishes tailored to specific applications. Alternative techniques like liquid, electrochemical, ultrasonic, and magnetic polishing further expand the process’s applicability to complex geometries, ensuring high efficiency and quality across diverse industrial needs.