Precision machining is a subtractive manufacturing process producing components with tolerances below ±0.00254 mm (±0.0001 inches). Utilizing CNC machines, CAD, and CAM systems, it serves industries like aerospace, medical, and electronics. The process encounters significant technical difficulties, detailed below with parameters and solutions.
Primary Technical Difficulties
1. Maintaining Tight Tolerances
Producing parts with tolerances of ±0.00254 mm for turned components and ±0.0127 mm for milled features is technically demanding due to:
- Werkzeugverschleiß: Degradation of cutting tools reduces dimensional accuracy. For titanium (hardness: 36 HRC), diamond-coated carbide tools are required.
- Machine Calibration: CNC systems need calibration to ±0.001 mm. A 0.01 mm deviation can lead to part rejection in aerospace.
- Thermal Effects: Heat-induced material expansion affects dimensions. Titanium’s thermal conductivity (7.4 W/m·K) requires coolant flow rates of 10-20 L/min.
Solution: Employ real-time monitoring (e.g., laser interferometry), polycrystalline diamond (PCD) tools, and maintain environments at 20±0.5°C.
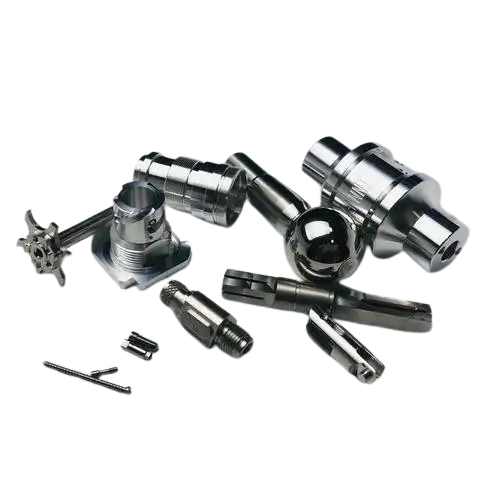
2. Material Machinability
Material properties significantly influence machining difficulty. Key materials and their characteristics are summarized below:
Material | Eigenschaften | Difficulty | Recommended Parameters |
---|---|---|---|
Titan | Thermal conductivity: 7.4 W/m·K, Hardness: 36 HRC | High tool wear, slow machining | Cutting speed: 30-60 m/min, Carbide/PCD tools |
Rostfreier Stahl | Prone to work hardening | Increased tool wear | Cutting speed: 100-150 m/min, Carbide tools |
Kunststoffe | Heat-sensitive | Deformation risk | Cutting speed: 50-100 m/min, Low feed rate |
Difficulty: Hard materials increase machining time by 2-3x compared to aluminum, elevating costs.
Solution: Optimize spindle speed (500-2000 RPM) and feed rate (0.05-0.2 mm/rev), using ceramic or carbide tools.
3. Micromachining and Miniaturization
Producing miniature parts for medical or electronics applications with ±0.001 mm tolerances presents significant difficulties:
Issue | Beschreibung | Difficulty |
---|---|---|
Handling | Micro-parts (e.g., 0.5 mm features) require specialized fixtures | Increased setup time |
Tool Durability | Micro-tools (0.1 mm drills) have 5-10% breakage rate | Higher tool replacement costs |
Oberfläche | Ra 0.1-0.4 µm required, affected by tool deflection | Compromised part quality |
Solution: Use ultra-precision machines with sub-nanometer accuracy and diamond turning for Ra < 0.1 µm finishes.
4. Complex Geometries
Machining intricate designs, such as aerospace turbine blades, requires multi-axis systems, posing difficulties:
- Tool Path Precision: Complex
G-Code
increases setup time by 20-30%. - Surface Integrity: Brittle materials like ceramics (fracture toughness: 4-6 MPa·m^0.5) risk microcracks.
- Equipment: 5-axis CNC systems require skilled operators and CAM software with <0.01 mm error margins.
Solution: Implement 5-axis machining and deterministic controllers for surface accuracy within 0.01 µm (e.g., KDP crystal fly cutting).
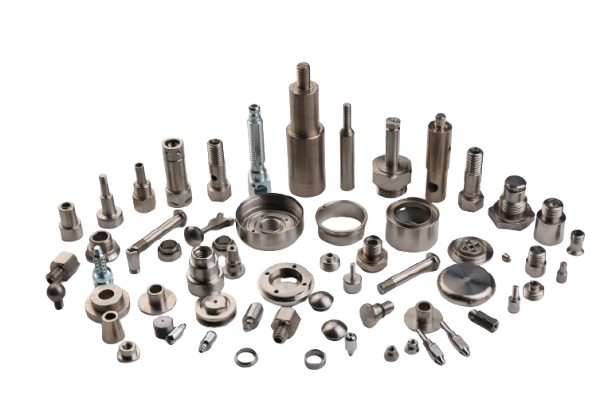
5. Quality Control and Traceability
Ensuring consistent quality in regulated industries involves significant difficulties:
Aspekt | Requirement | Difficulty |
---|---|---|
Measurement Precision | CMMs with ±0.001 mm traceability | High equipment cost |
Defect Detection | Identify 0.01 mm burrs | Risk of part failure |
Standards Compliance | ISO 9001/AS9100 validation | Extensive documentation |
Solution: Use automated inspection (e.g., laser scanning) and GR&R analysis for measurement validation.
Technological Solutions
Advancements mitigating these difficulties include:
- Machine Learning: Optimizes cutting parameters, reducing tool wear by 15-20%.
- Automatisierung: Robotics ensure repeatability with <0.005 mm variance.
- Hybrid Manufacturing: Combines additive and subtractive processes for complex geometries.
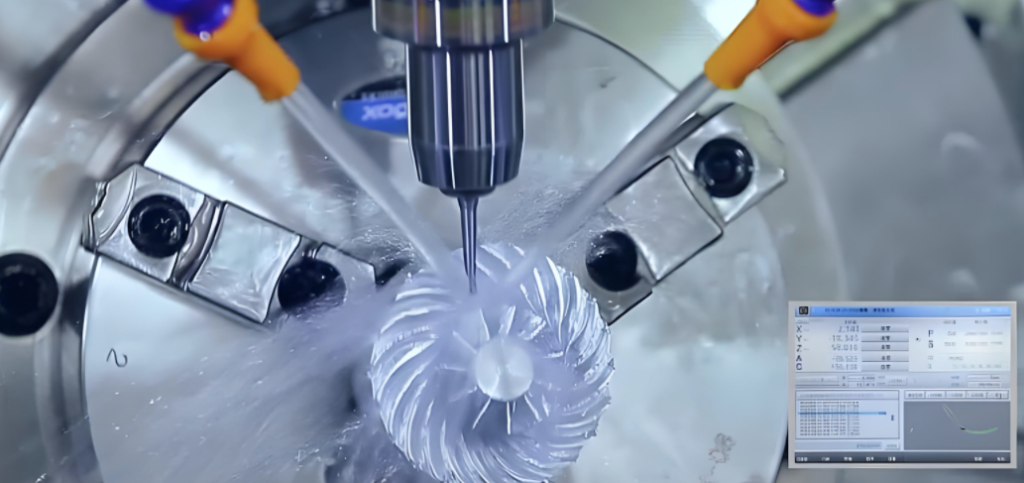
Schlussfolgerung
Precision machining requires addressing difficulties in tolerances, material machinability, miniaturization, complex geometries, and quality control. Advanced CNC systems, optimized parameters, and technologies like machine learning enable reliable production of high-precision components for critical applications.
Häufig gestellte Fragen
What defines precision machining?
Precision machining uses CNC systems to produce parts with tolerances below ±0.00254 mm, serving industries like aerospace and medical.
Why are tight tolerances difficult to achieve?
Tolerances of ±0.00254 mm demand precise tool control, frequent calibration, and thermal management, impacted by tool wear and material properties.
How does material selection affect machining difficulty?
Hard materials like titanium (36 HRC) or ceramics increase tool wear and machining time, requiring specialized tools and lower cutting speeds.