Anforderungen in der Fertigung Präzision und Effizienz um wettbewerbsfähig zu bleiben. Die 5-Achsen-CNC-Bearbeitung überwindet die Beschränkungen von Drei-Achsen-Systemen und ermöglicht die Herstellung hochwertiger, komplexer Teile. Ihre Flexibilität und Präzision machen sie für Branchen wie die Luft- und Raumfahrt, die Automobilindustrie, die Herstellung medizinischer Geräte und den Formenbau unverzichtbar. Nachfolgend finden Sie die wichtigsten Vorteile der 5-Achsen-CNC-Bearbeitung für Präzisionsteile.

Handhabung komplexer Geometrien
Mit der 5-Achsen-CNC-Bearbeitung lassen sich komplizierte und nicht standardisierte Geometrien mühelos bearbeiten. Im Gegensatz zu Drei-Achsen-Maschinen, die auf lineare X-, Y- und Z-Bewegungen beschränkt sind, verfügen 5-Achsen-Systeme über zwei Rotationsachsen (A und B oder C). Dadurch kann das Schneidwerkzeug das Werkstück aus jedem beliebigen Winkel anfahren, was die Bearbeitung komplexer Oberflächen, Hinterschneidungen und unregelmäßiger Formen in einer Aufspannung ermöglicht.
Anwendungen in der Luft- und Raumfahrt und im Turbinenbau
Die Luft- und Raumfahrt- sowie die Turbinenindustrie sind auf die 5-Achsen-Bearbeitung von Komponenten wie Turbinenschaufeln angewiesen, Laufräderund aerodynamische Teile. Diese zeichnen sich durch komplizierte Kurven, konturierte Oberflächen und enge Toleranzen (±0,005 mm oder besser) aus, die mit dreiachsigen Maschinen nur schwer ohne mehrfaches Einrichten erreicht werden können. Eine Turbinenschaufel kann die Bearbeitung von fünf Flächen mit präzisen Krümmungen erfordern. Die 5-Achs-Bearbeitung erledigt dies in einer Aufspannung und gewährleistet Maßhaltigkeit und Konsistenz.
Zu den Spezifikationen von High-End-5-Achs-Maschinen wie der DMG MORI DMU 50 gehören eine Positioniergenauigkeit von ±0,002 mm und Spindeldrehzahlen von bis zu 18.000 U/min - ideal für solche Anwendungen. Diese Maschinen bearbeiten Materialien wie Inconel oder Titan, die in der Luft- und Raumfahrt üblich sind, mit minimalem Werkzeugverschleiß.
Reduzierung von Einrichtungszeit und Fehlern
Mehrere Setups in Drei-Achsen-Bearbeitung führen zu Ausrichtungsfehlern und beeinträchtigen die Genauigkeit. Bei der 5-Achsen-Bearbeitung wird eine einzige Aufspannung verwendet, wodurch Fehler bei der Neupositionierung minimiert werden. Ein Formhohlraum, der mehrere Winkel erfordert, kann relativ zu einem Bezugspunkt bearbeitet werden, wobei Toleranzen von bis zu ±0,003 mm erreicht werden. Dies reduziert die Rüstzeit um bis zu 50% im Vergleich zu Drei-Achsen-Systemen, wie Fallstudien von Formenbauern zeigen, die Haas UMC-750 Maschinen einsetzen.
Die Bearbeitung in einer Aufspannung verbessert die Wiederholgenauigkeit, die für die Serienfertigung von Präzisionsteilen wie medizinischen Implantaten oder Automobilwerkzeugen entscheidend ist.
Rationalisierung des Arbeitsablaufs
Durch die Konsolidierung von Arbeitsgängen vereinfacht die 5-Achsen-Bearbeitung die Arbeitsabläufe. Ein komplexes Teil, z. B. eine Strukturkomponente für die Luft- und Raumfahrt, kann Folgendes erfordern fräsen, Bohren und Konturieren. 5-Achsen-Maschinen führen diese Arbeiten in einem einzigen Zyklus aus, wodurch sich der Bedarf an Handhabung und Vorrichtungen verringert. Dies senkt die Arbeitskosten und verkürzt die Vorlaufzeiten, wobei einige Hersteller von einer 30-40% kürzeren Gesamtbearbeitungszeit berichten.

Verbesserung von Präzision und Oberflächenqualität
5-Achsen-CNC-Bearbeitung liefert engere Toleranzen und hervorragende Oberflächengüte. Die gleichzeitige mehrachsige Bewegung sorgt für glattere Schnittwege und minimiert Vibrationen und Werkzeugauslenkungen. Dies ist entscheidend für Komponenten, die eine außergewöhnliche Genauigkeit erfordern, wie z. B. medizinische Implantate oder Hochleistungsmotorenteile.
Optimierte Werkzeugpfade
Durch die dynamische Werkzeugausrichtung bei der 5-Achs-Bearbeitung wird die Rechtwinkligkeit komplexer Oberflächen aufrechterhalten, wodurch die Wellenbildung reduziert und eine Oberflächengüte von Ra 0,2 µm erreicht wird. Für medizinische Implantate, bei denen die Oberflächenrauhigkeit aus Gründen der Biokompatibilität unter Ra 0,4 µm liegen muss, ist dies von entscheidender Bedeutung. Maschinen wie die Mazak INTEGREX i-400 erreichen Winkelgenauigkeiten von ±0,01 Grad und unterstützen diese Präzision.
Die Optimierung des Werkzeugwegs reduziert Bearbeitungsfehler. Bei der Bearbeitung eines parabolischen Reflektors sorgen 5-Achsen-Systeme für eine gleichmäßige Spankonzentration und vermeiden Abweichungen, die bei Drei-Achsen-Systemen aufgrund der begrenzten Achsensteuerung auftreten.
Minimierung der Nachbearbeitung
Hervorragende Oberflächenqualität durch 5-Achsen-Bearbeitung reduziert den Nachbearbeitungsbedarf. Motorenteile für die Automobilindustrie erhalten eine spiegelglatte Oberfläche (Ra 0,1-0,3 µm) direkt auf der Maschine, wodurch das Polieren entfällt. Dies spart 10-20% an Produktionskosten, da sekundäre Arbeitsgänge wie Schleifen minimiert werden. Die Daten der MU-5000V von Okuma zeigen eine Verbesserung der Oberflächengüte von 25% gegenüber dreiachsigen Systemen.
Konsistenz über Chargen hinweg
Die 5-Achsen-Bearbeitung sorgt für Gleichmäßigkeit in der Großserienfertigung. Durch die Aufrechterhaltung gleichmäßiger Schnittbedingungen werden in allen Chargen identische Teile hergestellt. Dies ist besonders wichtig für Branchen wie die Elektronikindustrie, wo Steckverbinder Toleranzen von ±0,01 mm erfordern. Fortschrittliche CAM-Software wie Siemens NX verbessert dies durch die Erzeugung präziser 5-Achsen-Werkzeugwege.
Verkürzung der Produktionszeit
Die 5-Achsen-CNC-Bearbeitung verkürzt die Produktionszyklen, indem sie die Mehrseitenbearbeitung in einer Aufspannung ermöglicht und so wiederholtes Umspannen überflüssig macht. Dies beschleunigt die Produktion und erhöht den Durchsatz, was für Branchen mit engen Terminen entscheidend ist.
Effizienz der Einzelaufstellung
Eine Form oder ein Werkzeug, das auf einer dreiachsigen Maschine mehrere Aufspannungen erfordert, kann in einem 5-Achs-Zyklus fertiggestellt werden. Eine Automobilform mit Hinterschneidungen und abgewinkelten Merkmalen benötigt 60% weniger Zeit auf einer 5-Achs-Maschine wie der Hermle C 42 U, die simultanes 5-Achs-Fräsen bei 15.000 U/min unterstützt. Diese Effizienz ist für die Automobil- und Unterhaltungselektronikbranche von entscheidender Bedeutung.
Minimierung von Ausfallzeiten
Reduzierte Rüstzeiten verringern die Maschinenstillstandszeit. Dreiachsige Systeme können 2 bis 3 Stunden für das Umrüsten komplexer Teile benötigen, während 5-Achs-Maschinen dieselbe Aufgabe in weniger als 30 Minuten erledigen. Dies steigert die Maschinenauslastung, wobei einige Betriebe nach der Umstellung auf die 5-Achsen-Technologie einen um 20% höheren Ausstoß melden.
Skalierbarkeit für große Projekte
5-Achsen-Bearbeitung skaliert effizient für große Projekte. Hersteller in der Luft- und Raumfahrtindustrie, die Strukturbauteile herstellen, profitieren von der Stapelverarbeitung mit minimalen Einrichtungsänderungen. Maschinen wie die FANUC Robodrill D21LiB5 bieten Zykluszeitreduzierungen von 15-25% und ermöglichen Skalierbarkeit ohne Qualitätseinbußen.
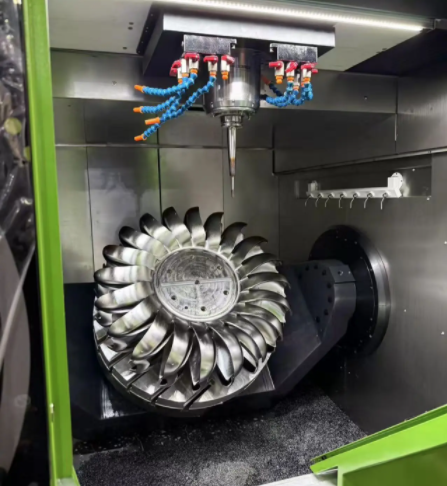
Verlängerte Lebensdauer und Kosteneinsparungen
Die 5-Achsen-CNC-Bearbeitung optimiert die Zerspanung durch die Beibehaltung idealer Werkzeugwinkel, was Stress und Verschleiß reduziert. Kürzere Werkzeuge mit weniger Überstand erhöhen die Steifigkeit, minimieren Vibrationen und verbessern die Leistung.
Optimierte Schnittbedingungen
Die Beibehaltung optimaler Schnittwinkel reduziert den Werkzeugverschleiß um 20-30%, wie Studien von Sandvik Coromant zeigen. Bei der Bearbeitung von Titan passen 5-Achs-Maschinen die Werkzeugwege an, um die Wärmeentwicklung zu minimieren, was die Werkzeuglebensdauer um bis zu 50% verlängert. Dies ist entscheidend für teure Werkzeuge wie Hartmetallfräser.
Geringere Wartungskosten
Geringerer Werkzeugverschleiß senkt die Kosten für Ersatz und Wartung. Ein einzelnes Hartmetallwerkzeug für die Titanbearbeitung kann $100-$300 kosten. Eine Verlängerung der Werkzeuglebensdauer um 30% spart den Betrieben mit hohem Durchsatz jährlich Tausende. Weniger Rüstvorgänge senken die Arbeitskosten, wobei einige Hersteller von Einsparungen von 15% berichten.
Energie-Effizienz
5-Achsen-Maschinen verbrauchen aufgrund kürzerer Zykluszeiten weniger Energie pro Teil. Eine Studie von GF Machining Solutions ergab, dass 5-Achsen-Systeme bei komplexen Teilen 10-15% weniger Energie verbrauchen als Drei-Achsen-Maschinen, was zu Kosteneinsparungen und Nachhaltigkeit beiträgt.
Bearbeitung schwieriger Materialien
In der modernen Fertigung werden Materialien wie Titanlegierungen, Edelstahl und Verbundwerkstoffe verwendet, die für ihre hohe Festigkeit und Zähigkeit bekannt sind. Die 5-Achsen-CNC-Bearbeitung zeichnet sich durch Präzision und Kontrolle bei der Bearbeitung dieser Materialien aus.
Präzision in widerstandsfähigen Materialien
Titan-Legierungen (z. B. Ti-6Al-4V) erfordern niedrige Schnittgeschwindigkeiten (50-80 m/min) und ein hohes Drehmoment. 5-Achs-Maschinen wie die Makino T1 sorgen für eine gleichmäßige Spanbelastung und erreichen Oberflächengüten von Ra 0,5 µm. Dies ist für Luft- und Raumfahrtkomponenten wie Fahrwerksteile von entscheidender Bedeutung.
Handhabung von Verbundwerkstoffen
Verbundwerkstoffe wie kohlenstofffaserverstärkte Polymere (CFK) sind anfällig für Delamination. Bei der 5-Achs-Bearbeitung werden spezielle Werkzeugwege verwendet, um den Faserauszug zu minimieren und saubere Kanten zu erzielen. Maschinen wie die CMS Ares bieten Spindeldrehzahlen von bis zu 24.000 U/min, ideal für die CFK-Bearbeitung.
Branchenübergreifende Vielseitigkeit
Von medizinischen Geräten (Implantate aus rostfreiem Stahl) bis hin zu Teilen aus dem Energiesektor (Inconel-Turbinenschaufeln) passt sich die 5-Achsen-Bearbeitung an die unterschiedlichsten Materialien an. Ihre Fähigkeit, Materialien mit hoher Härte (bis zu 60 HRC) zu bearbeiten, macht sie für High-End-Anwendungen unverzichtbar.

Präzise 5-Achsen-CNC-Bearbeitung mit Kesu Hardware
Die hochmodernen AFM 5-Achsen und Mikron 5-Achsen CNC-Bearbeitungszentren der Kesu Hardware Group bieten unvergleichliche Präzision und Vielseitigkeit für Branchen, die komplexe, hochwertige Komponenten benötigen.
Mit den fortschrittlichen Anlagen von Kesu, darunter die Mikron E 700U und die GMU-800EVO mit großem Hub (Plattformgröße 800 mm, X/Y/Z-Hub: 850/950/550 mm), bieten wir Lösungen für nicht standardisierte, hochpräzise Teile ohne Mindestbestellmenge aus einer Hand und erfüllen die strengen Anforderungen der Automobil-, Medizin-, Luft- und Raumfahrt- sowie der Elektronikindustrie. Laden Sie noch heute Ihre 2D/3D-Zeichnungen hoch, um ein sofortiges Angebot zu erhalten, und erleben Sie Kesus Engagement für Qualität und Effizienz.
Schlussfolgerung
Die fünfachsige CNC-Bearbeitung stellt einen bedeutenden Sprung nach vorn in der Präzisionsfertigungund bietet unvergleichliche Vorteile gegenüber herkömmlichen Drei-Achsen-Systemen. Ihre Fähigkeit, komplexe Geometrien zu bearbeiten, die Präzision zu erhöhen, die Produktionszeiten zu verkürzen, die Werkzeuglebensdauer zu verlängern und schwierige Materialien zu bearbeiten, macht sie zu einer unverzichtbaren Technologie für die Herstellung hochwertiger Präzisionsteile. Für Branchen, in denen Genauigkeit, Effizienz und Vielseitigkeit gefragt sind, ist die 5-Achsen-Bearbeitung nicht nur ein Werkzeug, sondern ein Wettbewerbsvorteil, der Innovation und Spitzenleistungen fördert.
Durch Investitionen in die 5-Achsen-CNC-Bearbeitung können Hersteller die Grenzen konventioneller Methoden überwinden, ihre Arbeitsabläufe rationalisieren und überlegene Produkte liefern, die den strengen Anforderungen der heutigen Märkte gerecht werden. Ganz gleich, ob Sie Komponenten für die Luft- und Raumfahrt, komplizierte Formen oder Hochleistungsteile für die Automobilindustrie herstellen, die Vorteile der 5-Achsen-Bearbeitung gewährleisten, dass Präzision und Effizienz Hand in Hand gehen.
FAQ: 5-Achsen-CNC-Bearbeitung für Präzisionsteile
Was ist die 5-Achsen-CNC-Bearbeitung?
Bei der 5-Achsen-CNC-Bearbeitung wird eine Maschine mit fünf Bewegungsachsen (X, Y, Z und zwei Rotationsachsen, typischerweise A und B oder C) verwendet, um komplexe Teile in einer Aufspannung zu bearbeiten, was eine größere Flexibilität und Präzision als bei 3-Achsen-Systemen bietet.
Wie verbessert die 5-Achsen-Bearbeitung die Präzision?
Es ermöglicht glattere Werkzeugwege, hält optimale Werkzeugwinkel ein und reduziert Vibrationen, wodurch Toleranzen von ±0,002 mm und Oberflächengüten unter Ra 0,4 µm erreicht werden.
Welche Branchen profitieren am meisten von der 5-Achs-Bearbeitung?
Die Luft- und Raumfahrt, die Automobilindustrie, die Medizintechnik und der Formenbau profitieren davon, weil sie komplexe Geometrien, enge Toleranzen und anspruchsvolle Materialien wie Titan und Verbundwerkstoffe benötigen.
Ist die 5-Achsen-Bearbeitung kosteneffizient?
Ja, es verkürzt die Rüstzeiten, verlängert die Werkzeugstandzeit und minimiert die Nachbearbeitung, was zu 15-30% Kosteneinsparungen bei Hochpräzisionsanwendungen führt.