Selecting a CNC machining service provider requires a systematic evaluation of their capabilities to ensure they meet project requirements for precision, quality, and efficiency. This guide provides a detailed, professional framework to assess CNC service providers based on technical expertise, equipment, quality control, material handling, and operational processes. By focusing on measurable parameters and structured methodologies, this evaluation process ensures reliability and performance without speculative trends or challenges.
Assessing Technical Expertise and Workforce Competence
The technical expertise of a CNC service provider’s workforce is critical to achieving high-quality results. Skilled operators, programmers, and engineers ensure that complex designs are executed with precision. Evaluate the provider’s workforce by examining their qualifications, training programs, and experience in handling industry-specific projects.
Certifications and Training: Look for certifications such as ISO 9001:2015, which indicates a structured quality management system, or industry-specific credentials like AS9100 for aerospace. Verify if operators are trained in CAD/CAM software (e.g., Mastercam, Catia) and Geometric Dimensioning and Tolerancing (GD&T). Continuous training ensures employees stay updated on machining techniques and quality standards. For example, a provider with a workforce trained in GD&T can maintain tolerances as tight as ±0.01 mm, critical for high-precision industries.
Experience and Specialization: Assess the provider’s experience in your industry, such as aerospace, automotive, or medical. A provider with a portfolio of complex components (e.g., multi-axis machined parts with intricate geometries) demonstrates capability. Request case studies or references to confirm their expertise in handling similar projects. For instance, a provider experienced in machining titanium components for aerospace applications is likely to understand material-specific challenges like tool wear and thermal management.
Team Structure: A competent provider employs a balanced team of programmers, machinists, and quality inspectors. Programmers should be proficient in generating G-code for multi-axis machines, while machinists need hands-on experience with CNC mills, lathes, and EDM systems. Quality inspectors must be skilled in using measurement tools like Coordinate Measuring Machines (CMMs) to verify dimensional accuracy.
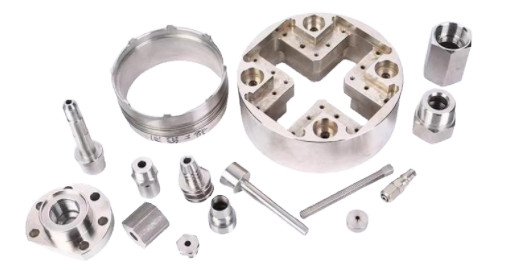
Evaluating Equipment and Machining Capabilities
The quality and range of a provider’s equipment directly impact their ability to meet project specifications. Modern CNC machines with advanced features ensure precision, efficiency, and versatility. Evaluate the provider’s equipment based on the following parameters:
Equipment Type | Key Parameters | Evaluation Criteria |
---|---|---|
3-Axis CNC Machines | Max part size: 1000 x 800 x 600 mm; Spindle speed: 12,000 RPM | Suitable for simple geometries; check for regular calibration and maintenance |
5-Axis CNC Machines | Max part size: 500 x 500 x 500 mm; Positional accuracy: ±0.005 mm | Capable of complex, multi-sided parts; verify multi-axis programming expertise |
Swiss-Type Lathes | Diameter range: 0.5–32 mm; Tolerance: ±0.002 mm | Ideal for small, high-precision parts; confirm high repeatability |
Wire EDM | Cutting accuracy: ±0.0025 mm; Max thickness: 300 mm | Suitable for hard materials; ensure electrical conductivity support |
Machine Maintenance and Calibration: Regular maintenance ensures machines operate at optimal levels. Verify if the provider follows a scheduled maintenance plan, including routine cleaning, lubrication, and tool calibration. For example, a well-maintained 5-axis CNC machine can achieve positional accuracy of ±0.005 mm, critical for intricate components.
Tooling and Automation: Assess the availability of automatic tool changers and advanced tooling systems (e.g., carbide tools with TiN coatings for stainless steel). Automation features like real-time monitoring and integrated reporting enhance production consistency. Providers with automated inspection systems can detect defects early, reducing rework costs.
Capacity and Scalability: Confirm the provider’s capacity to handle your project volume, from prototypes to high-volume production. For example, a shop with multiple 5-axis machines can process complex parts faster than one reliant on 3-axis systems. Check if they can scale operations without compromising quality.
Quality Control and Inspection Processes
A robust quality control (QC) system is essential to ensure parts meet specifications. Evaluate the provider’s QC processes by examining their inspection methods, certifications, and documentation practices.
Inspection Technologies: Advanced inspection tools like CMMs, laser scanners, and optical comparators ensure dimensional accuracy. For instance, CMMs can measure complex geometries with a precision of ±0.001 mm. Verify if the provider uses both contact and non-contact probes for comprehensive metrology. Non-destructive testing (NDT) methods, such as ultrasonic testing, are critical for assessing material integrity without damage.
Quality Management System (QMS): A formalized QMS, aligned with ISO 9001:2015, ensures systematic quality control. Check if the provider conducts First Article Inspections (FAI) to validate initial parts against design specifications. In-process inspections, monitoring parameters like cutting speed and tool wear, help maintain consistency. Final inspections should include detailed reports on dimensional accuracy, surface finish (e.g., roughness of 0.8–1.6 µm Ra), and geometric tolerances.
Traceability and Documentation: Comprehensive records of inspections, material certifications, and process parameters ensure traceability. For example, material certificates should specify alloy grades (e.g., Aluminum 6061-T6) and properties like tensile strength (310 MPa). Proper documentation supports audits and verifies compliance with industry standards.
Statistical Process Control (SPC): SPC uses data-driven methods to monitor production. By analyzing metrics like dimensional variation, providers can identify deviations early. For instance, a process with a CpK value of ≥1.33 indicates high capability to meet tolerances. Confirm if the provider uses SPC software for real-time quality management.
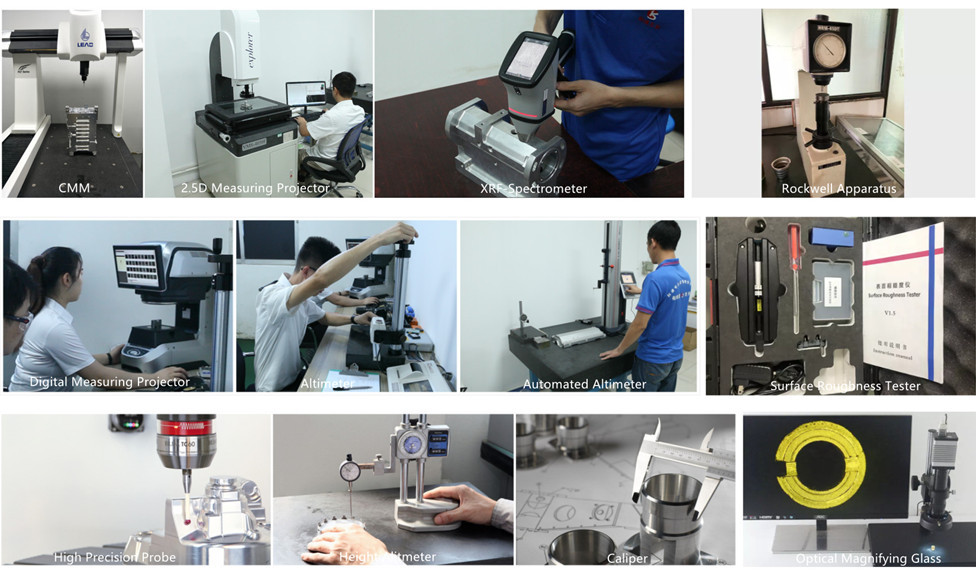
Material Handling and Processing Expertise
The ability to handle a wide range of materials is a key indicator of a provider’s capability. Different materials require specific machining parameters and expertise to achieve desired outcomes.
Material Versatility: Evaluate the provider’s experience with materials like aluminum, stainless steel, titanium, and engineering plastics (e.g., PEEK, Delrin). For example, machining aluminum 6061 requires sharp tools and high spindle speeds (10,000–15,000 RPM) to prevent heat buildup, while stainless steel demands robust tools with coatings like TiAlN to reduce wear.
Material Inspection: Raw material quality directly affects the final product. Verify if the provider conducts visual and chemical composition checks on incoming materials. For instance, a provider should confirm that stainless steel 304 meets ASTM A240 standards for corrosion resistance.
Surface Finish and Post-Processing: Assess the provider’s ability to achieve specific surface finishes, such as 0.4 µm Ra for medical implants. Post-processing capabilities like anodizing, heat treatment, or plating should be evaluated. For example, hardcoat anodizing increases wear resistance for aluminum parts, with a coating thickness of 25–50 µm.
Material | Machining Parameters | Applications |
---|---|---|
Aluminum 6061 | Spindle speed: 10,000–15,000 RPM; Feed rate: 0.1–0.3 mm/rev | Aerospace components, automotive parts |
Stainless Steel 304 | Spindle speed: 2,000–4,000 RPM; Coolant: High-pressure | Medical devices, food processing equipment |
Titanium Ti-6Al-4V | Spindle speed: 1,000–2,000 RPM; Tool: Carbide with TiN coating | Aerospace, implants |
PEEK | Spindle speed: 8,000–12,000 RPM; Feed rate: 0.05–0.2 mm/rev | Medical, electronics |
Operational Efficiency and Project Management
Efficient operations and clear communication streamline project execution. Evaluate the provider’s processes for quoting, production, and delivery to ensure reliability.
Quoting and DFM Feedback: A professional provider offers detailed quotes covering material costs, machining time, and post-processing fees. For example, material costs for titanium can be 5–10 times higher than aluminum, impacting the quote. Design for Manufacturability (DFM) feedback helps optimize designs, reducing costs by adjusting features like wall thickness (e.g., minimum 0.8 mm for aluminum).
Lead Time and Delivery: Assess the provider’s ability to meet deadlines. For instance, a shop offering quick-turn prototypes in 3–5 days demonstrates efficiency. Verify their logistics capabilities, including packaging and shipping options, to ensure parts arrive undamaged.
Communication and Support: Effective communication is critical for resolving issues. Check if the provider assigns dedicated project managers and offers regular updates. For example, a provider using cloud-based project management tools can provide real-time progress reports, enhancing transparency.
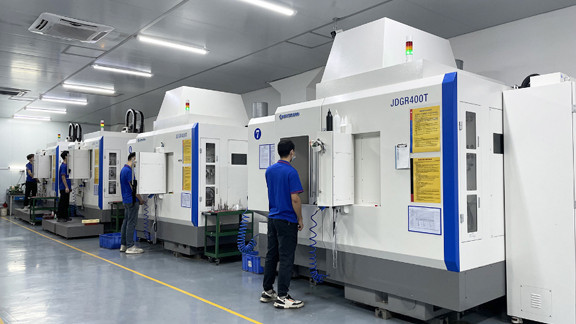
Cost-Effectiveness and Long-Term Value
While cost is a factor, focus on long-term value rather than the lowest price. Evaluate the provider’s ability to balance quality and affordability.
Cost Breakdown: Request detailed quotes specifying material, labor, tooling, and inspection costs. For example, a 5-axis machining job for a complex part may cost 20–30% more than 3-axis but reduces setup time, improving efficiency.
Long-Term Benefits: High-quality parts reduce rework and maintenance costs. A provider with durable dies (e.g., lasting 100,000 cycles) offers better value than cheaper, less reliable options. Assess their track record through customer testimonials or repeat business rates.
Scalability and Flexibility: A provider capable of scaling from prototypes to mass production without quality loss adds value. For instance, a shop with automated systems can handle batch sizes from 10 to 10,000 units efficiently.
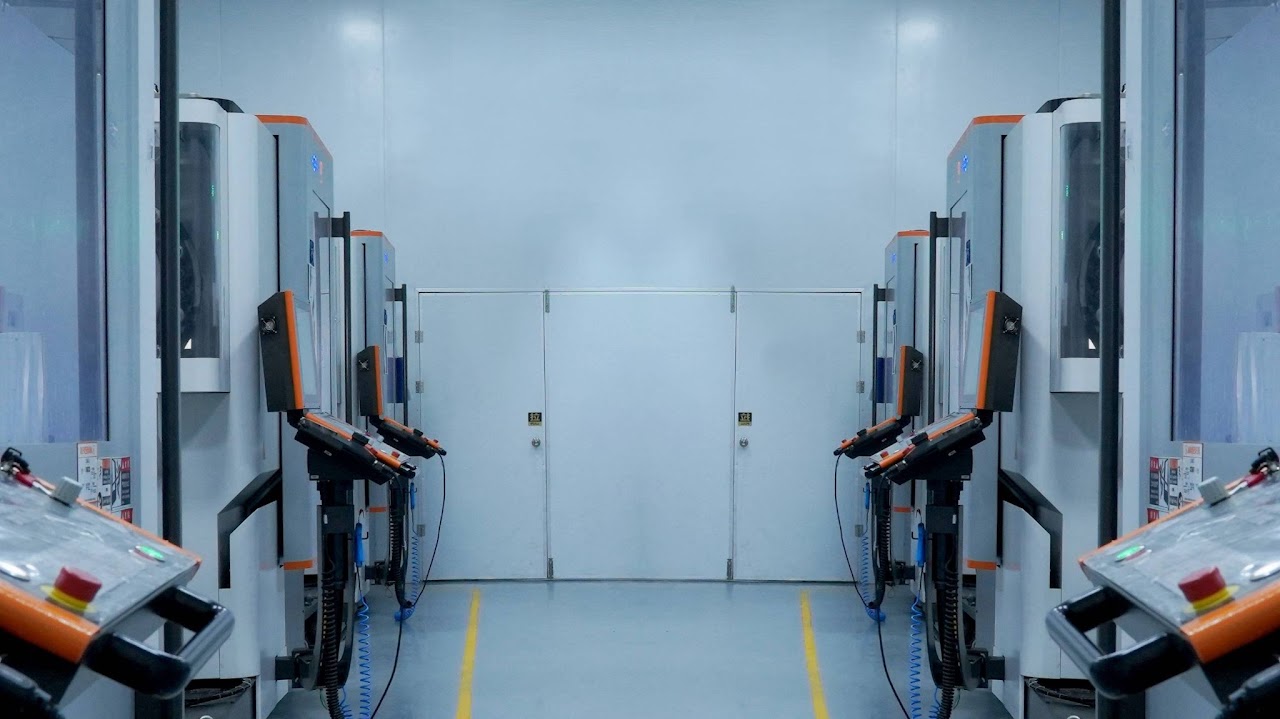
Kesu: Precision Machining, Engineered for Excellence
At Kesu, we don't just machine parts; we craft solutions. With a relentless focus on technical mastery, cutting-edge equipment, and an unwavering commitment to quality, we deliver CNC machining services that redefine precision and reliability. From intricate prototypes to high-volume production, Kesu ensures your project exceeds expectations, every time. Experience the difference that measurable parameters, rigorous quality control, and a deep understanding of materials can make.
Conclusion
Evaluating a CNC machining service provider’s capabilities requires a systematic approach focusing on technical expertise, equipment, quality control, material handling, operational efficiency, and cost-effectiveness. By examining certifications, machine specifications, inspection processes, and material expertise, you can ensure the provider meets your project’s precision and quality requirements. Use measurable parameters, such as tolerances of ±0.01 mm or surface roughness of 0.8 µm Ra, to set clear expectations. A thorough evaluation builds trust and ensures a reliable partnership for high-quality CNC machined parts.