China's CNC (Computer Numerical Control) machining industry has become a cornerstone of global manufacturing, offering high-efficiency production, competitive costs, and reliable outcomes for industries ranging from automotive to aerospace. This article provides a detailed examination of the factors that make Chinese CNC factories a preferred choice for precision manufacturing. By focusing on efficiency, cost, and reliability, we aim to deliver a comprehensive, technical overview grounded in industry expertise.
Efficiency in China's CNC Factories
Efficiency is a defining characteristic of China's CNC machining industry, driven by advanced infrastructure, skilled labor, and optimized processes. Chinese factories leverage modern equipment and large-scale operations to deliver high output with minimal downtime.
Advanced Machinery and Automation
Chinese CNC factories are equipped with state-of-the-art machinery, including 3-axis, 4-axis, and 5-axis CNC machines. These systems enable precise machining of complex geometries with tolerances as tight as ±0.001mm. Automation is widely integrated, with robotic arms and IoT-enabled systems streamlining workflows. For example, 5-axis CNC machines can perform multiple operations in a single setup, reducing machining time by up to 30% compared to 3-axis systems. Factories often use CAD/CAM software like Mastercam or Siemens NX to optimize tool paths, further enhancing production speed.
Skilled Workforce and Training
China's vast pool of skilled technicians and engineers is a critical factor in operational efficiency. Technical schools and vocational programs produce thousands of CNC operators annually, with many trained in G-code programming and machine maintenance. Factories maintain rigorous training protocols, ensuring operators can handle complex projects with minimal errors. This expertise allows for rapid setup times, often under 30 minutes for standard components, and efficient handling of high-volume orders.
Streamlined Supply Chain and Logistics
China's manufacturing sector benefits from a deeply integrated supply chain. Proximity to raw material suppliers and robust logistics networks ensures quick access to materials like aluminum, steel, and titanium. For instance, local sourcing of aluminum 6061 can reduce lead times by 20-40% compared to importing. Factories often operate near major ports, enabling cost-effective shipping options, with delivery times averaging 3-7 days for international orders. This integration minimizes delays and supports just-in-time production models.
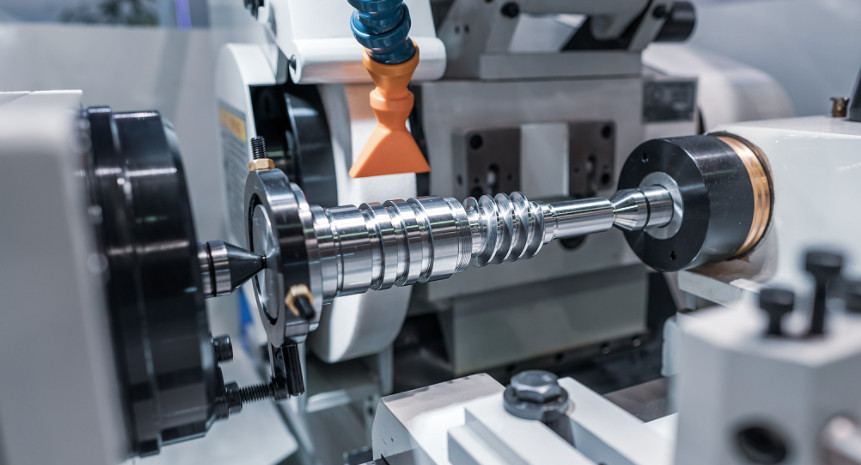
Cost Advantages of CNC Machining in China
Cost-effectiveness is a primary reason businesses worldwide choose Chinese CNC factories. Lower labor rates, economies of scale, and efficient material sourcing contribute to competitive pricing without sacrificing quality.
Labor and Operational Costs
Labor costs in China are significantly lower than in Western countries. Skilled CNC operators in China earn an average of $4-$8 per hour, compared to $20-$40 in the United States or Europe. Operational costs, including utilities and facility maintenance, are also reduced due to government subsidies and lower infrastructure expenses. For example, electricity costs for industrial use in China average $0.08-$0.12 per kWh, compared to $0.15-$0.25 in the U.S. These savings translate to CNC machining rates of $8-$30 per hour in China, versus $50-$100 in Western markets.
Material Sourcing and Pricing
China's extensive industrial base provides access to a wide range of materials at competitive prices. Common materials like stainless steel, brass, and ABS plastics are sourced locally, reducing costs by 15-25% compared to imported alternatives. Bulk purchasing agreements with suppliers further lower material costs. For instance, aluminum 6061, widely used in CNC machining, costs approximately $2-$3 per kg in China, compared to $4-$6 per kg in the U.S. Efficient material utilization, achieved through optimized nesting and cutting paths, minimizes waste and enhances cost savings.
Economies of Scale
Large-scale CNC factories in China benefit from economies of scale, allowing them to spread fixed costs over high production volumes. Factories with over 50 CNC machines can handle orders ranging from prototypes to thousands of units, reducing per-unit costs. For example, producing 1,000 units of a precision component can lower the cost per part by 20-30% compared to small-batch production. This scalability makes Chinese factories ideal for both low-volume prototyping and high-volume manufacturing.
Factor | China | USA |
---|---|---|
Hourly CNC Machining Rate | $8-$30 | $50-$100 |
Labor Cost (per hour) | $4-$8 | $20-$40 |
Material Cost (Aluminum 6061, per kg) | $2-$3 | $4-$6 |
Electricity Cost (per kWh) | $0.08-$0.12 | $0.15-$0.25 |
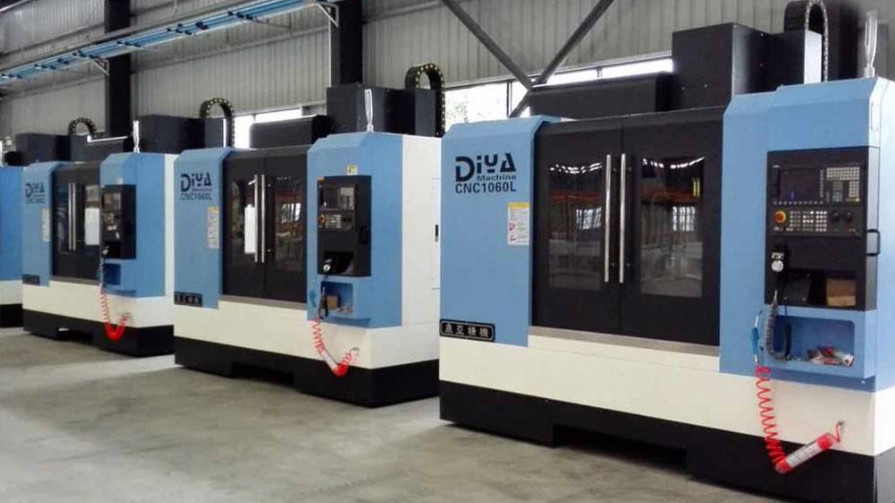
Reliability of Chinese CNC Factories
Reliability in CNC machining encompasses consistent quality, adherence to specifications, and dependable delivery. Chinese factories have made significant strides in establishing trust through certifications, quality control, and customer-focused services.
Quality Control and Certifications
Reputable Chinese CNC factories adhere to international standards, such as ISO 9001:2015, ensuring consistent quality. Advanced inspection tools, including coordinate measuring machines (CMM) and laser scanners, verify tolerances to within ±0.005mm. For example, automotive parts like engine components undergo 100% inspection to meet IATF 16949 standards. Factories also implement statistical process control (SPC) to monitor production, reducing defect rates to below 1% in high-precision projects.
Consistency in Production
Chinese CNC factories maintain consistency through standardized processes and advanced equipment. Multi-axis machines ensure repeatability, with deviation rates as low as 0.002mm across batches. For instance, CNC lathes produce cylindrical parts with surface finishes of Ra 0.8µm or better, meeting aerospace and medical industry requirements. Regular maintenance schedules, including predictive maintenance using IoT sensors, minimize machine downtime, ensuring uninterrupted production.
Customer Support and Communication
Reliable factories prioritize clear communication and responsive support. Many offer instant quoting platforms, allowing clients to upload CAD files and receive detailed quotes within 24 hours. Dedicated project managers facilitate direct communication, reducing errors due to miscommunication. For example, clear technical drawings and specifications provided upfront can prevent costly rework, saving 10-15% in production costs. Post-delivery support, including warranty services and replacement parts, further enhances reliability.
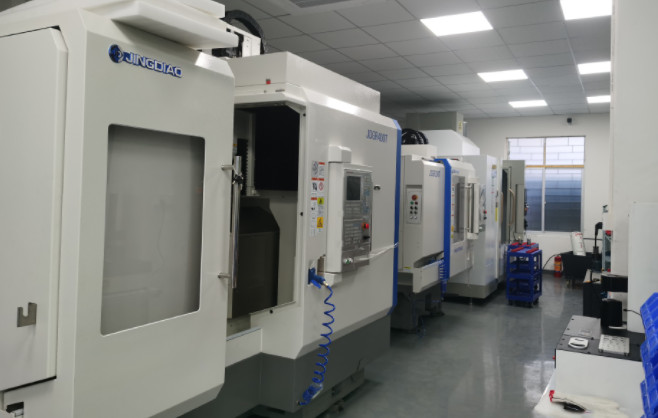
Key Considerations for Partnering with Chinese CNC Factories
While Chinese CNC factories offer significant advantages, certain considerations can impact project success. Addressing these ensures optimal outcomes without compromising efficiency, cost, or reliability.
Manufacturer Selection
Choosing a reputable manufacturer is critical. Factories with ISO certifications, a proven track record, and industry-specific experience (e.g., aerospace or medical) are preferable. Reviewing portfolios and client testimonials helps verify expertise. For example, a factory with experience in 5-axis machining for titanium parts is better suited for complex aerospace components than a generalist provider.
Communication and Specifications
Clear communication of design requirements is essential to avoid errors. Providing detailed technical drawings, specifying tolerances (e.g., ±0.01mm), and selecting appropriate materials upfront streamline production. Some factories offer design-for-manufacturability (DFM) feedback, optimizing designs to reduce machining time by 15-20% while maintaining quality.
Logistics and Lead Times
International clients must account for shipping costs and lead times. While China's logistics infrastructure supports rapid delivery (3-7 days for standard orders), customs duties and shipping method (air vs. sea) can affect costs. For example, air freight for a 100kg shipment may cost $500-$800, while sea freight costs $200-$400 but takes 2-4 weeks longer. Planning ahead avoids rush fees, which can increase costs by 10-20%.
Material | Properties | Common Applications |
---|---|---|
Aluminum 6061 | Lightweight, corrosion-resistant, high machinability | Engine blocks, aerospace components |
Stainless Steel 304 | Rust-resistant, strong, hygienic | Medical devices, food processing equipment |
Titanium | High strength-to-weight ratio, biocompatible | Aerospace parts, medical implants |
ABS Plastic | Impact-resistant, cost-effective | Consumer electronics, prototypes |
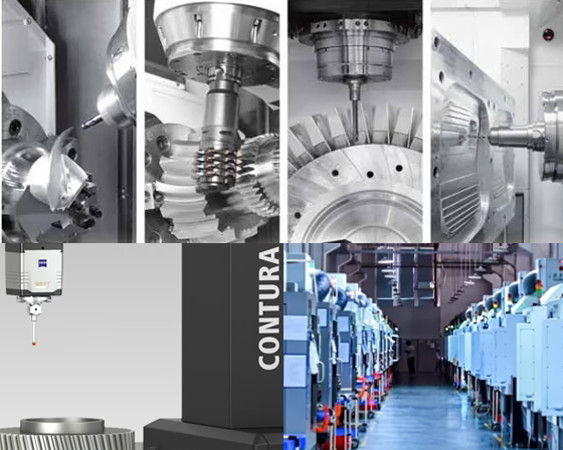
Experience the Kesu advantage: precision without the premium
Kesu leverages China's advanced CNC manufacturing to deliver unparalleled precision, speed, and cost-effectiveness for your projects. Our state-of-the-art 5-axis machines, highly skilled engineers, and rigorous ISO 9001:2015 quality control ensure flawless components with tolerances as tight as ±0.001mm. Benefit from significantly lower labor and material costs without compromising on quality or reliability. With Kesu, you gain a partner committed to streamlined communication, rapid prototyping, and on-time delivery from initial quote to final product.
Conclusion
China's CNC factories excel in delivering efficient, cost-effective, and reliable machining services. Advanced machinery, a skilled workforce, and integrated supply chains drive efficiency, while low labor and material costs ensure affordability. Rigorous quality control and responsive customer support underpin reliability. By carefully selecting manufacturers, communicating specifications clearly, and planning logistics, businesses can maximize the benefits of partnering with Chinese CNC factories. This combination of technical expertise, cost advantages, and dependable performance makes China a global leader in CNC machining.