CNC (Computer Numerical Control) machining is a cornerstone of precision manufacturing, producing components with tight tolerances for industries such as aerospace, automotive, and medical devices. The quality of CNC-machined parts depends heavily on the condition of the equipment. Regular maintenance of CNC machines ensures consistent dimensional accuracy, surface finish, and material integrity, directly influencing the final product’s performance and reliability. This article examines how equipment maintenance affects quality in CNC factories, focusing on key maintenance practices, their impact on machining outcomes, and practical strategies for implementation.
Importance of CNC Equipment Maintenance for Quality Control
Maintenance of CNC machines is critical to achieving high-quality output. CNC machines operate with extreme precision, often within tolerances of ±0.002 mm. Any deviation in machine performance due to wear, misalignment, or inadequate lubrication can lead to defective parts, increased scrap rates, and costly rework. Regular maintenance minimizes these risks by ensuring that machines operate within specified parameters. For example, a well-maintained CNC machine can consistently produce parts with surface roughness values as low as 0.8–1.6 micrometers, meeting stringent industry standards.
Maintenance also reduces unplanned downtime, which can disrupt production schedules and lead to inconsistent quality. According to industry data, unplanned downtime can cost manufacturers thousands of dollars per hour, with emergency repairs being up to five times more expensive than scheduled maintenance. By implementing a robust maintenance program, CNC factories can maintain high-quality production, reduce waste, and improve operational efficiency.
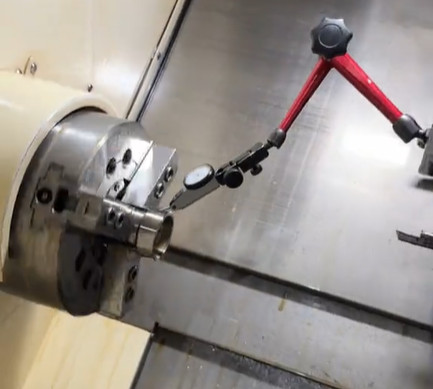
Key Maintenance Practices and Their Impact on Quality
Effective CNC equipment maintenance involves a combination of routine tasks, inspections, and advanced monitoring techniques. Below are the primary maintenance practices and their direct effects on part quality.
Routine Cleaning and Lubrication
CNC machines have numerous moving parts, such as spindles, slides, and bearings, that require regular cleaning and lubrication. Accumulated debris, such as metal shavings or coolant residue, can cause friction, leading to component wear and misalignment. For instance, excessive friction in a spindle bearing can increase runout, resulting in dimensional inaccuracies of up to 0.01 mm or more. Regular cleaning removes contaminants, while proper lubrication—using manufacturer-specified oils or greases—reduces friction and wear, ensuring smooth operation. This practice directly contributes to maintaining dimensional accuracy and surface finish quality.
Component Inspection and Replacement
Regular inspection of critical components, such as belts, bearings, and tool holders, is essential to identify wear before it affects machining quality. Worn bearings can cause vibrations, leading to surface finish irregularities, such as chatter marks, which may increase surface roughness beyond acceptable limits (e.g., above 3.2 micrometers). Replacing worn components promptly prevents these issues. For example, a CNC milling machine with a worn spindle bearing might produce parts with dimensional errors exceeding ±0.005 mm, whereas timely replacement ensures tolerances remain within ±0.002 mm.
Machine Calibration
Calibration ensures that CNC machines maintain their precision over time. Tools and machine axes must be regularly calibrated using precision instruments like laser interferometers or dial indicators. Miscalibration can result in dimensional inaccuracies, such as parts deviating by ±0.01 mm or more from design specifications. Regular calibration, typically performed every 6–12 months depending on usage, ensures that machines meet tolerances as tight as ±0.001 mm, critical for industries like aerospace. Calibration also involves checking backlash in ball screws, which, if unaddressed, can cause positional errors during machining.
Tool Maintenance and Monitoring
Cutting tools are central to CNC machining quality. Worn or damaged tools can lead to poor surface finishes, dimensional inaccuracies, and increased scrap rates. For example, a dull milling cutter can increase surface roughness to 6.3 micrometers or higher, compared to the desired 1.6 micrometers. Regular tool inspection, sharpening, or replacement, combined with real-time monitoring systems, ensures consistent performance. Advanced CNC machines use sensors to detect tool wear, allowing operators to replace tools before they compromise quality.
Coolant System Maintenance
Coolant systems regulate temperature and remove chips during machining. Contaminated or degraded coolant can lead to thermal expansion, causing dimensional errors of up to 0.02 mm in high-precision parts. Regular coolant replacement, filtration, and system cleaning maintain thermal stability and prevent chip buildup, which can mar surface finishes. For instance, maintaining coolant concentration at 5–10% as recommended by manufacturers ensures optimal heat dissipation and chip evacuation, preserving part quality.
Preventive vs. Predictive Maintenance Strategies
CNC maintenance strategies fall into two main categories: preventive and predictive. Each has a distinct impact on quality and operational efficiency.
Maintenance Type | Description | Impact on Quality |
---|---|---|
Preventive Maintenance | Scheduled tasks (e.g., lubrication, cleaning, calibration) based on time or usage intervals. | Ensures consistent machine performance, reducing defects by maintaining tolerances and surface finish standards. |
Predictive Maintenance | Data-driven approach using sensors to monitor machine conditions and predict failures. | Prevents unexpected failures, maintaining quality by addressing issues before they affect part accuracy. |
Preventive maintenance is proactive, involving regular tasks like weekly lubrication or monthly calibration to prevent issues. Predictive maintenance uses real-time data, such as vibration or temperature sensors, to anticipate failures. For example, predictive maintenance can detect bearing wear by analyzing vibration frequencies, allowing replacement before quality is compromised. Combining both strategies optimizes machine reliability and part quality.

Quality Control Integration with Maintenance
Maintenance directly supports quality control (QC) processes in CNC machining. QC involves inspections at various stages—first article, in-process, and final—to ensure parts meet specifications. Maintenance ensures that machines produce parts within tolerances, reducing the need for extensive inspections. For example, a well-maintained CNC lathe can consistently produce cylindrical parts with diameters within ±0.001 mm, minimizing QC rejections.
Key QC tools, such as coordinate measuring machines (CMMs) and micrometers, rely on machine precision to deliver accurate measurements. A misaligned machine can produce parts that pass visual inspections but fail dimensional checks, leading to costly rework. Regular maintenance ensures that machines align with QC standards, such as ISO 9001, which emphasizes consistent quality through documented processes.
Impact on Specific Quality Parameters
CNC maintenance influences several quality parameters critical to machined parts.
Dimensional Accuracy
Dimensional accuracy measures how closely a part’s dimensions match design specifications. Maintenance practices like calibration and tool monitoring ensure machines achieve tolerances as tight as ±0.001 mm. For example, a CNC milling machine with proper axis alignment can produce parts with consistent hole diameters, critical for assemblies in automotive applications.
Surface Finish
Surface finish affects a part’s functionality and aesthetics. Regular maintenance prevents issues like tool chatter, which can increase surface roughness beyond acceptable limits (e.g., 3.2 micrometers). For instance, maintaining spindle balance ensures smooth cutting, achieving finishes as fine as 0.4 micrometers for high-precision components.
Material Integrity
Proper maintenance preserves material properties by controlling machining conditions. Overheating due to poor coolant maintenance can alter material hardness, affecting performance. For example, maintaining coolant systems prevents thermal distortion in aluminum parts, ensuring hardness remains within specified Rockwell values (e.g., 60–70 HRB).
Practical Implementation of Maintenance Programs
Implementing an effective maintenance program requires a systematic approach. Below are key steps to ensure maintenance supports quality.
Step | Description | Frequency |
---|---|---|
Develop a Maintenance Schedule | Create a plan based on manufacturer guidelines and machine usage (e.g., daily cleaning, monthly calibration). | Daily to annually |
Train Operators | Ensure operators are trained in maintenance tasks and QC inspections to identify issues early. | Ongoing |
Use Monitoring Tools | Implement sensors for vibration, temperature, and tool wear to support predictive maintenance. | Continuous |
Maintain Documentation | Record maintenance activities and QC results for traceability and process improvement. | Per task |
A comprehensive maintenance program integrates these steps into daily operations, ensuring machines perform reliably. For example, a CNC shop producing 10,000 parts monthly can reduce scrap rates from 5% to 1% by adhering to a strict maintenance schedule, saving significant costs.
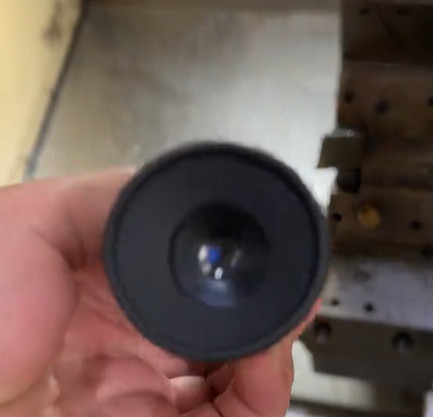
Common Maintenance-Related Issues and Solutions
While maintenance is critical, certain issues can arise if not properly managed.
Improper Lubrication: Inadequate or excessive lubrication can cause overheating or component wear. Solution: Follow manufacturer-specified lubricant types and intervals, such as applying ISO 68 oil every 40 hours of operation.
Delayed Calibration: Infrequent calibration leads to dimensional errors. Solution: Schedule calibration every 6 months or after 2,000 hours of operation, using tools like laser interferometers.
Tool Wear Neglect: Ignoring tool wear increases scrap rates. Solution: Use tool life management software to monitor usage and replace tools after 100–200 cutting hours, depending on material.
Addressing these issues proactively ensures consistent quality and minimizes production disruptions.
Conclusion
CNC equipment maintenance is a cornerstone of quality in precision manufacturing. By prioritizing routine cleaning, component inspection, calibration, tool maintenance, and coolant system care, CNC factories can achieve dimensional accuracy, superior surface finishes, and material integrity. Preventive and predictive maintenance strategies further enhance reliability, reducing defects and downtime. A well-implemented maintenance program, supported by trained operators and detailed documentation, ensures that CNC machines consistently produce high-quality parts, meeting the demands of industries where precision is paramount.