Assessing the production capacity of a CNC (Computer Numerical Control) factory is a critical step in determining accurate delivery times for machined parts. Delivery time, or lead time, refers to the total duration from order placement to the final delivery of the product. Accurate assessment ensures customer satisfaction, efficient resource utilization, and competitive operations. This guide provides a systematic, technical, and reliable approach to evaluating CNC factory production capacity, focusing on practical methods grounded in industry experience. The process involves analyzing machine-hour capacity, workforce capabilities, raw material availability, order complexity, and quality control requirements to estimate realistic delivery schedules.
Understanding Production Capacity in CNC Machining
Production capacity represents the maximum output a CNC factory can achieve within a specific timeframe, typically measured in machine-hours or units produced. It is influenced by the number and type of CNC machines, operational hours, workforce efficiency, and material availability. For example, a factory with 10 CNC machines operating 24 hours a day has a theoretical daily capacity of 240 machine-hours (10 machines x 24 hours). However, real-world factors such as setup times, maintenance, and operator efficiency reduce this to an effective capacity.
To calculate production capacity, factories must first determine their machine-hour capacity. This involves multiplying the number of machines by their operational hours, adjusted for downtime. For instance, if a factory operates two 8-hour shifts with 10 machines and accounts for 1 hour of daily maintenance per machine, the effective capacity is 10 machines x 7 hours x 2 shifts = 140 machine-hours per day.
Capacity assessment also requires understanding the types of CNC machines available, such as 3-axis, 4-axis, or 5-axis mills, lathes, or EDM (Electrical Discharge Machining) systems. Each machine type has specific capabilities that affect production speed and part complexity handling. For example, 5-axis machines can reduce setup times for complex geometries, increasing throughput compared to 3-axis machines.
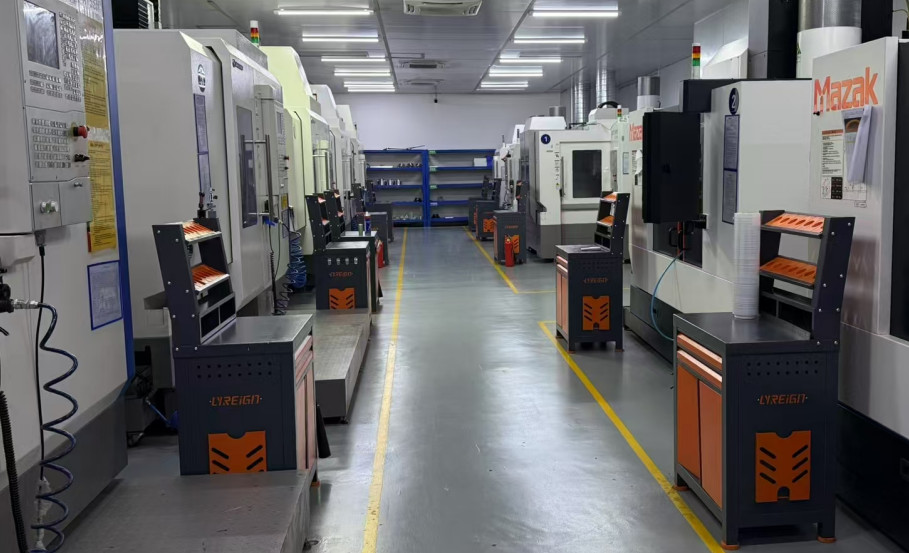
Key Factors Influencing Delivery Time
Several factors directly impact the delivery time of CNC machined parts. These include production capacity, part complexity, raw material supply, workforce efficiency, and quality control requirements. Each factor must be systematically evaluated to ensure accurate lead time estimates.
1. Machine-Hour Capacity and Scheduling
Machine-hour capacity is the foundation of production planning. To assess delivery time, factories must calculate the time required to produce a specific order based on the number of parts, machining operations, and cycle times. For example, if a part requires 30 minutes of machining time and the order is for 100 parts, the total machining time is 3,000 minutes (50 hours). If the factory has 140 machine-hours available daily, this order would take approximately 0.36 days (50 ÷ 140) of machine time, excluding setup and other non-machining activities.
Scheduling is equally critical. Factories must account for existing orders and prioritize based on customer deadlines. A production schedule that exceeds capacity leads to delays, while underutilization wastes resources. Using real-time job tracking systems can provide visibility into machine availability, helping planners allocate resources efficiently.
2. Part Complexity and Technical Requirements
The complexity of CNC machined parts significantly affects delivery time. Simple parts with basic geometries, such as flat plates or cylindrical components, require fewer machining operations and shorter cycle times. Complex parts with intricate features, tight tolerances (e.g., ±0.01 mm), or multi-axis machining demand more time for programming, setup, and processing.
For instance, a part requiring 5-axis machining may need multiple setups on a 3-axis machine, increasing production time by 20-30% compared to a single setup on a 5-axis machine. Factories should conduct a Design for Manufacturability (DFM) analysis to identify potential bottlenecks in the machining process, such as complex geometries that require specialized tooling or extended fixturing.
3. Raw Material Availability
Raw material supply directly influences lead time. Common materials like aluminum 6061 or stainless steel 304 are typically readily available, allowing production to start immediately. However, exotic materials like Inconel or titanium may require special ordering, adding 1-2 weeks to the lead time. Factories must verify material stock levels and supplier lead times before accepting orders. For example, if a supplier takes 5 days to deliver a specific grade of titanium, this must be factored into the delivery schedule.
Material quality also matters. Substandard materials can lead to machining defects, requiring rework and extending delivery times. Factories should maintain strong relationships with reliable suppliers to ensure consistent material quality and availability.
4. Workforce Efficiency and Skill Level
The skill level and availability of operators and programmers impact production capacity. Experienced operators can optimize machine setups, reducing changeover times by up to 15-20%. For example, a skilled operator might complete a setup in 30 minutes, while a less experienced one takes 45 minutes, directly affecting throughput.
Workforce scheduling is another consideration. Factories operating multiple shifts (e.g., two 8-hour shifts) can increase capacity, but fatigue or inadequate training may reduce efficiency. A factory with 20 operators working two shifts can theoretically handle twice the workload of a single-shift operation, but only if staff are adequately trained and managed.
5. Quality Control Requirements
Quality control (QC) processes, such as dimensional inspections, surface finish checks, and material testing, add time to the production cycle. For example, parts requiring 100% inspection with Coordinate Measuring Machines (CMMs) may take an additional 10-20 minutes per part compared to statistical process control (SPC) sampling. Strict QC requirements, common in aerospace or medical industries, can extend lead times by 1-2 days for high-volume orders.
Factories must balance quality and speed. Implementing real-time monitoring systems can detect deviations early, reducing rework time. For instance, automated tool wear measurement devices can predict tool life, preventing defects and minimizing downtime.
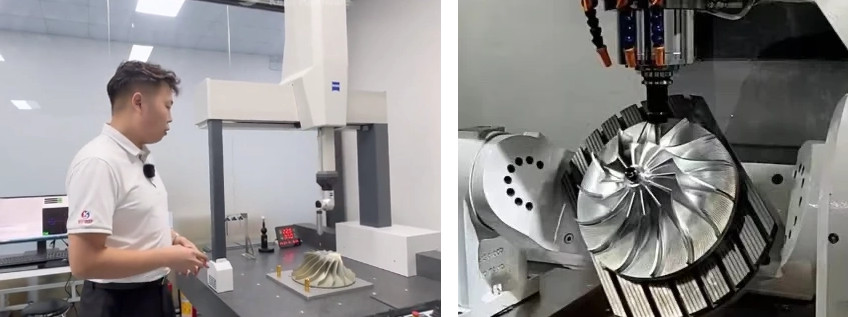
Systematic Approach to Delivery Time Assessment
A systematic approach to assessing delivery time involves integrating production capacity data with order-specific requirements. The following steps outline a reliable method:
Step 1: Order Analysis
Upon receiving an order, conduct a detailed review of the customer’s requirements, including part specifications, quantities, tolerances, and delivery deadlines. For example, an order for 500 aluminum parts with ±0.05 mm tolerances requires different resources than 50 titanium parts with ±0.01 mm tolerances. Use CAD/CAM software to analyze part designs and estimate machining times based on tool paths and cycle times.
Step 2: Capacity Evaluation
Compare the order’s requirements against the factory’s available capacity. Calculate the total machine-hours needed, including setup, machining, and inspection times. For instance, if an order requires 100 machine-hours and the factory has 140 machine-hours available daily, the order can be completed in less than a day, assuming no competing orders. Adjust for existing workloads and maintenance schedules to ensure realistic estimates.
Step 3: Material and Resource Verification
Confirm the availability of raw materials and workforce resources. If materials are not in stock, include supplier lead times in the schedule. Verify that operators and programmers have the necessary skills for the order. For example, a complex 5-axis part may require a senior programmer, whose availability must be confirmed.
Step 4: Production Scheduling
Create a detailed production schedule that allocates machine time, labor, and inspection resources. Use ERP (Enterprise Resource Planning) or MES (Manufacturing Execution System) software to track progress and adjust schedules dynamically. For example, if a high-priority order arrives, the schedule may need reallocation to meet deadlines without compromising existing commitments.
Step 5: Lead Time Communication
Communicate the estimated lead time to the customer, including a buffer for unforeseen delays (e.g., 10-15% additional time). For instance, if the calculated lead time is 5 days, quote 6 days to account for potential issues like machine downtime or material delays. Provide regular updates through order tracking systems to maintain transparency.
Practical Example of Delivery Time Assessment
Consider a factory with 12 CNC machines (8 milling, 4 turning) operating two 8-hour shifts, with 1 hour of daily maintenance per machine. The effective daily capacity is 12 machines x 7 hours x 2 shifts = 168 machine-hours. An order for 200 parts arrives, each requiring 20 minutes of milling and 10 minutes of turning (30 minutes total). The total machining time is 200 parts x 30 minutes = 6,000 minutes (100 hours).
Assuming no other orders, the machining time is spread across the 8 milling machines (160 minutes per part across 8 machines = 20 minutes per machine) and 4 turning machines (80 minutes per part across 4 machines = 20 minutes per machine). The order can be completed in approximately 0.6 days (100 ÷ 168), excluding setup and inspection. Adding 2 hours for setup and 4 hours for inspection increases the total to 106 hours, or roughly 0.63 days. Factoring in a 10% buffer, the quoted lead time is 0.7 days, assuming materials are available.
If materials require 3 days to procure, the total lead time becomes 3.7 days. This example demonstrates how capacity, part complexity, and material availability interact to determine delivery time.
Common Challenges in Delivery Time Assessment
While the above approach is systematic, certain challenges can complicate delivery time estimates:
Challenge | Description | Solution |
---|---|---|
Inaccurate Capacity Data | Outdated or incomplete data on machine availability or cycle times leads to incorrect estimates. | Implement real-time monitoring systems to track machine utilization and update capacity data regularly. |
Unexpected Downtime | Machine breakdowns or operator absences disrupt schedules. | Maintain a maintenance schedule and cross-train operators to ensure flexibility. |
Material Delays | Supplier issues or stock shortages extend lead times. | Build relationships with multiple suppliers and maintain a buffer stock of common materials. |
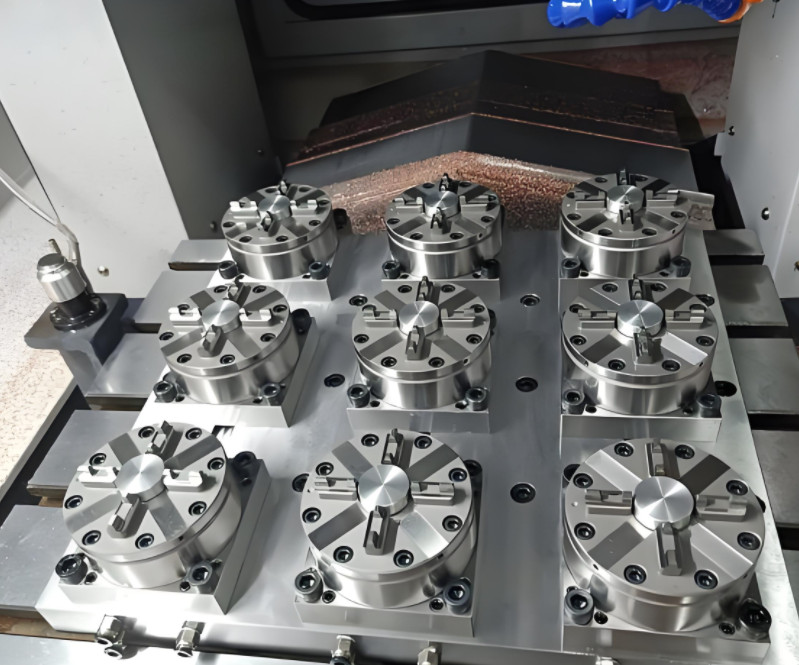
Best Practices for Reliable Delivery Time Estimates
To enhance the reliability of delivery time assessments, factories should adopt the following practices:
- Use Advanced Software: Implement ERP or MES systems to integrate capacity data, track production progress, and adjust schedules in real time.
- Conduct Time Studies: Regularly perform time studies to update cycle times and setup durations for accurate capacity calculations.
- Maintain Equipment: Schedule preventive maintenance to minimize unexpected downtime, ensuring consistent capacity.
- Train Workforce: Invest in operator and programmer training to improve efficiency and reduce errors.
- Communicate Clearly: Provide customers with realistic lead times and regular updates to build trust and manage expectations.
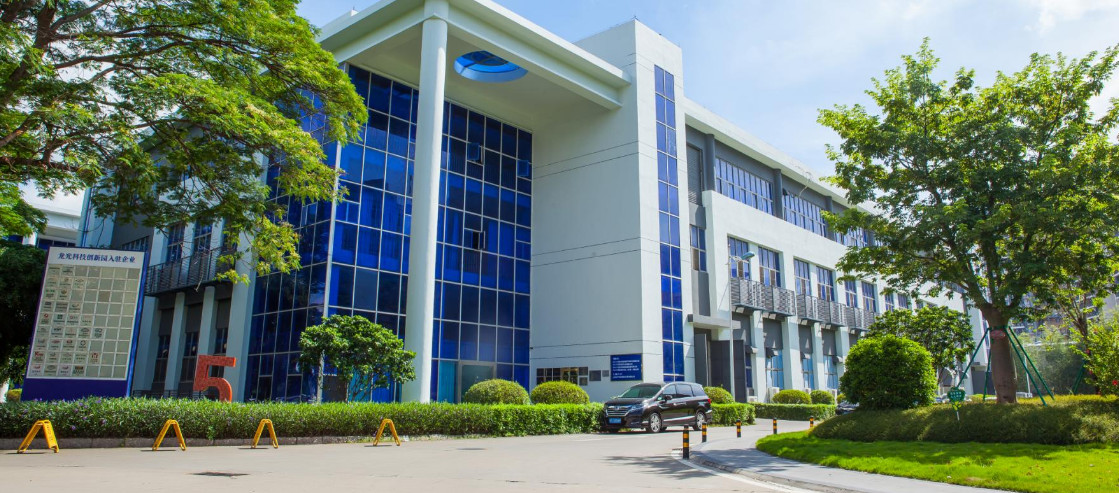
Kesu: Master CNC Production Capacity, Make Delivery Timelines Reliable and Controllable
Kesu deeply understands the core logic of CNC factory production capacity assessment. From calculating machine-hour capacity to optimizing processing cycles for complex parts, from integrating raw material supply chains to streamlining quality inspection processes, every step is grounded in data and guided by industry experience. Whether it’s precision parts requiring multi-axis machining or standard components for mass production, we can accurately lock in delivery timelines through systematic capacity analysis. What’s more, we reserve flexible buffers to handle unexpected situations, ensuring full transparency and control over your orders from placement to delivery. Trust Kesu to safeguard your production plans with reliable timelines.
Conclusion
Assessing CNC factory production capacity to determine delivery time requires a systematic approach that integrates machine-hour capacity, part complexity, material availability, workforce efficiency, and quality control requirements. By analyzing orders, evaluating resources, creating detailed schedules, and addressing potential challenges, factories can provide accurate lead times that enhance customer satisfaction and operational efficiency. Using real-time data, advanced software, and best practices ensures reliable and competitive delivery schedules, positioning CNC factories for long-term success.