Aero-engine combustor casings are critical components that operate under extreme conditions, requiring high precision and durability. The complexity of their structure and the challenges posed by difficult-to-machine materials necessitate advanced machining techniques. Adaptive control technology has emerged as a solution to address inefficiencies and quality issues in traditional machining methods. This article explores the application of adaptive control in machining combustor casings, focusing on real-time monitoring, tool wear detection, spindle load control, and cutting parameter optimization.
Structural Features and Machining Challenges of Combustor Casings
Aero-engine combustor casings are characterized by complex geometries, including mounting edges, reinforcing ribs, nozzle seats, and grooves. These components are typically made from high-temperature nickel-based alloys GH4169, a high-temperature nickel-based alloy classified as a Class II forging with a hardness of ≤277 HBW. This material is notoriously difficult to machine due to its high strength, heat resistance, and tendency to cause rapid tool wear. The machining process requires a significant number of solid carbide tools, increasing costs and complexity.
During machining, several factors contribute to operational challenges:
- Tool Damage: Variations in material microstructure, uneven machining allowances, and inadequate coolant supply often lead to tool chipping or breakage.
- Spindle Load Fluctuations: Sudden changes in cutting conditions, such as tool wear, material inconsistencies, or collisions, cause significant spindle load variations, risking part rejection or machine damage.
- Operator Dependency: Traditional machining relies on operators manually adjusting feed rates via override switches when anomalies occur, making real-time monitoring and precise adjustments difficult.
- Long Cycle Times: The intricate geometry and material properties result in extended machining cycles, increasing production costs.
- Inconsistent Quality: Fixed cutting parameters in NC programs fail to account for dynamic machining conditions, leading to quality variations.
These challenges highlight the limitations of traditional machining methods, which struggle to integrate empirical expertise with data-driven process control, resulting in inefficiencies and quality inconsistencies.
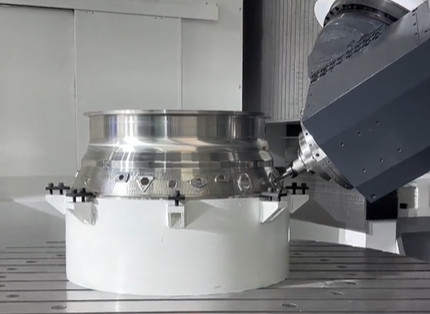
Adaptive Control Technology: A Paradigm Shift in Machining
Adaptive control technology integrates hardware controllers with the machine’s numerical control (NC) system to enable real-time monitoring and optimization of cutting parameters, such as spindle speed, torque, feed rate, and cutting force. By storing and analyzing machining data in a database, the system employs an internal intelligent expert system to monitor and adjust the CNC machining process dynamically. This technology addresses the limitations of traditional methods by ensuring consistent spindle loads, optimizing cutting parameters, and enabling unmanned operation with precise process control.
The intelligent expert system performs three key functions:
- Real-Time Data Acquisition: Monitors machining conditions, including vibrations, cutting forces, tool wear, material variations, sudden changes in machining allowance, and coolant system faults.
- Comprehensive Analysis: Evaluates spindle load and cutting parameters to assess machining performance.
- Predictive Monitoring: Anticipates machining conditions to prevent issues like tool breakage or spindle overload.
By referencing historical data and real-time machining information, the system determines whether the machining state is optimal. If deviations occur, it dynamically adjusts cutting parameters, such as feed rate, to maintain an optimal machining state, ensuring consistent quality and protecting the machine tool.
Tool Wear Monitoring with Adaptive Control
Traditional methods for detecting tool wear in combustor casing machining rely on subjective indicators, such as blade chipping, surface finish, chip color, or cutting noise. In fully enclosed machining environments, these methods are ineffective, as visual inspection and auditory cues are unavailable. Consequently, tool wear and lifespan cannot be accurately monitored, leading to unexpected tool failures and compromised part quality.
Adaptive control systems overcome these limitations by recording spindle power changes during the machining of a reference part, establishing a baseline for subsequent operations. During machining, the system continuously monitors spindle power and compares it to the baseline. Significant deviations, indicative of tool wear, trigger an automatic power anomaly alarm, prompting tool replacement without operator intervention.
The system generates real-time overload alarm curves, as shown in a typical monitoring chart:
- Orange Curve: Represents spindle overload due to tool wear over time.
- Blue Curve: Tracks material cutting rate over time.
- Green Curve: Indicates the activation status of the cutting load control system.
- Gray Curve: Monitors spindle rotation status.
- Red Line: Shows feed rate override adjustments.
- Green Line: Tracks spindle power variations.
- Red Triangle: Marks alarm events.
When tool wear reaches a predefined overload threshold, the system issues an alarm and adjusts the feed rate or halts machining to prevent damage. This eliminates the need for manual adjustments, ensuring consistent tool performance and extending tool life.
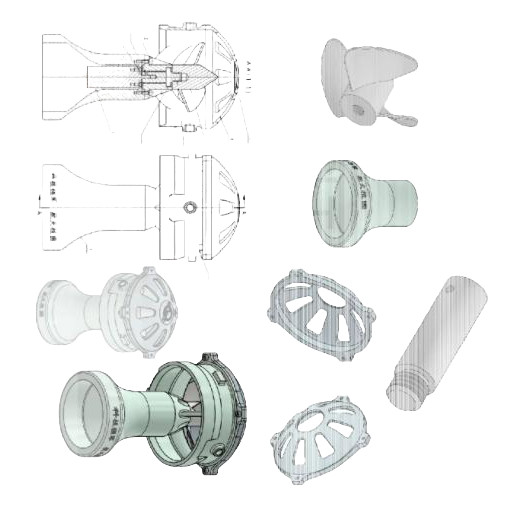
Spindle Load Control for Consistent Machining
In traditional machining, spindle load variations are monitored indirectly through auditory cues, requiring operators to manually adjust parameters to maintain load within safe limits. This approach is imprecise and reactive, often failing to prevent damage from sudden changes in cutting conditions, such as tool breakage, material inconsistencies, or coolant failures.
Adaptive control systems provide precise, real-time spindle load monitoring and control. By dynamically adjusting cutting parameters based on load variations, the system maintains spindle power within a safe range, transitioning from constant-speed to constant-load machining. For example, when anomalies like tool breakage or sudden changes in CNC machining allowance occur, the system automatically reduces the feed rate to a safe level. If the load exceeds the maximum allowable threshold, the system halts the machine and issues an alarm, preventing spindle damage.
A typical spindle load variation curve includes:
- Load Increase Response: The system reduces cutting speed as spindle load rises.
- Lower Limit Trigger: If the feed rate falls below a preset minimum, the machine stops, and an alarm is issued.
- Load Optimization: The system increases the feed rate to maximize spindle load within safe limits, ensuring efficient CNC machining.
This approach protects the spindle while maintaining consistent machining performance, reducing the risk of part rejection and equipment damage.
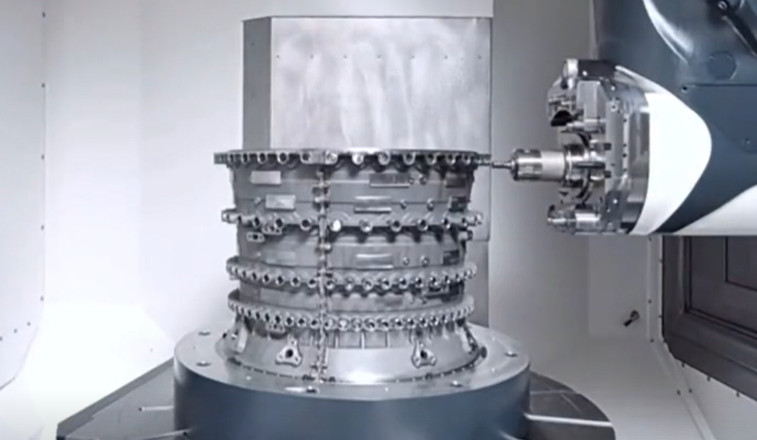
Cutting Parameter Optimization for Enhanced Efficiency
Traditional NC programs use fixed cutting parameters, which cannot adapt to dynamic machining conditions, such as varying machining allowances or tool wear. This results in inefficiencies, such as idle tool paths or slow feed rates, leading to prolonged machining times and inconsistent quality.
Adaptive control systems compare real-time cutting parameters with theoretical values stored in a database, automatically adjusting feed rates to optimize performance. This ensures scientifically optimized parameters, reducing tool collisions, protecting the machine, and shortening machining cycles. For instance, when machining combustor casings with a φ16R4mm solid carbide milling cutter, traditional methods allowed each tool to machine three nozzle seats, whereas adaptive control extended tool life to five nozzle seats per tool.
The following table illustrates the efficiency improvements achieved through cutting parameter optimization:
Parameter | Before Optimization | After Optimization |
---|---|---|
Machining Time (s) | 249,727 | 207,193 |
Efficiency Improvement (%) | - | 17.03 |
Note: Machining times exclude setup, alignment, tool setting, tool changes, program verification, and measurement times, with precision to the second.
By maintaining the machine in a saturated operating state while ensuring safety and quality, adaptive control maximizes equipment utilization, significantly reducing production times.
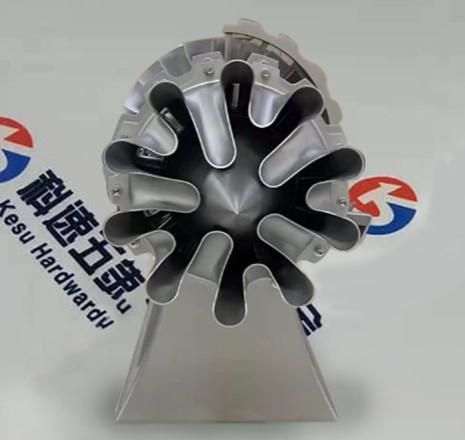
Kesu Adaptive Control: Redefine Precision Machining for Aero-Engine Combustor Casings
Kesu’s adaptive control technology is the game-changer for machining aero-engine combustor casings, tackling the toughest challenges of complex geometries and hard-to-machine high-temperature nickel-based alloys materials like GH4169 with unparalleled precision and efficiency. By integrating real-time monitoring of spindle load, automatic tool wear detection, and dynamic optimization of cutting parameters, it eliminates tool damage, reduces operator dependency, and slashes machining cycles by up to 17%—all while ensuring consistent, aerospace-grade quality. With Kesu, you move beyond fixed parameters and reactive adjustments, embracing a data-driven, adaptive approach that maximizes tool life, protects equipment, and transforms your production line into a hub of reliability and performance.
Conclusion
Adaptive control technology revolutionizes the machining of aero-engine combustor casings by addressing the limitations of traditional methods. Key outcomes include:
- Real-Time Spindle Load Monitoring: Optimizes feed rates to prevent spindle damage during anomalies like tool wear, material inconsistencies, or coolant failures, enabling a shift from constant-speed to constant-load machining.
- Tool Wear Monitoring: Automatically detects and responds to tool wear, extending tool life and reducing operator dependency.
- Process Optimization: Achieves a 17% improvement in machining efficiency by dynamically adjusting cutting parameters, ensuring precise control and consistent quality.
This technology enables unmanned, data-driven machining, allowing for precise production planning and optimal part quality. By integrating empirical data with real-time analysis, adaptive control ensures reliable, efficient, and high-quality machining of complex aero-engine components.