Thread machining, particularly for high-volume production of components like valve bodies for petroleum pipelines, often faces challenges related to inconsistent quality. This article presents a novel two-tool threading process designed to address issues such as tool wear, frequent machine stoppages, and unstable thread quality. By adopting a rough and finish threading approach, this method enhances machining efficiency, reduces tool replacement frequency, and improves thread precision. The following sections detail the process, its implementation, and solutions to common problems encountered during thread machining.
Background of Thread Machining Challenges
In large-scale production of 2''-11-1/2 NPT threads on cast steel valve bodies, conventional threading methods often lead to inconsistent quality. The standard approach involves using a single threading tool (e.g., 16 IR 11.5 NPT insert) to machine the thread in nine passes with progressively decreasing depths of cut. However, cast steel workpieces frequently contain defects such as porosity and sand inclusions, which cause intermittent cutting. This leads to rapid tool tip wear, frequent machine stoppages for tool replacement and measurement, and subsequent adjustments to the CNC machine. These interruptions result in discontinuous machining, unstable thread quality, and increased scrap or rework rates.
The primary issues include:
- Rapid tool wear due to material defects causing intermittent cutting.
- Frequent stoppages for thread measurement and tool replacement.
- Difficulty maintaining consistent thread dimensions and quality.
- Increased production time due to machine adjustments after tool changes.
To address these challenges, a two-tool threading process was developed, splitting the machining into rough and finish stages to improve efficiency and quality.
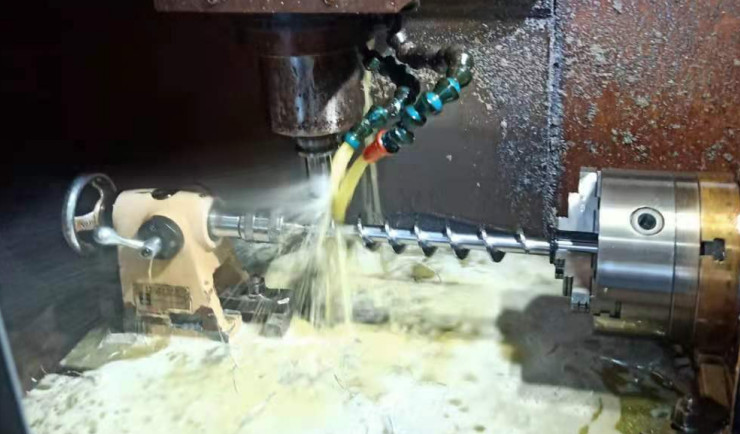
The Two-Tool Threading Process
The two-tool threading process uses separate rough and finish threading tools to machine threads in two distinct phases. The roughing tool removes the majority of the material in the initial passes, while the finishing tool completes the thread with minimal cutting depths. This approach mitigates the impact of material defects and reduces tool wear, leading to more stable thread quality and fewer machine stoppages.
Rough Threading
The rough threading tool performs the first six passes, removering the majority of the material with larger depths of cut. For the 2''-11-1/2 NPT thread, the roughing tool handles the bulk of the material removal, typically with cutting depths ranging from 0.5 to 1.0 mm per pass. Despite the higher cutting forces and impact from material defects, slight tool wear during roughing does not significantly affect the final thread dimensions or quality. This allows the roughing tool to continue cutting without immediate replacement, reducing downtime.
Key Parameters for Rough Threading:
Parameter | Value |
---|---|
Tool Type | 16 IR 11.5 NPT (Roughing Insert) |
Number of Passes | 6 |
Depth of Cut per Pass | 0.5–1.0 mm |
Spindle Speed | 400 rpm |
The roughing tool’s ability to withstand minor wear without affecting the final thread quality is a key advantage, as it minimizes the need for frequent tool changes and machine adjustments.
Finish Threading
The finishing tool performs the final three to four passes with smaller depths of cut, typically 0.1–0.2 mm per pass, to achieve the required thread dimensions and surface quality. The reduced cutting depth minimizes cutting forces and tool wear, ensuring consistent thread profiles and dimensional accuracy. If the finishing tool shows minor wear, it is replaced immediately to maintain precision, but the worn insert can be reused for rough threading, optimizing tool usage and reducing costs.
Key Parameters for Finish Threading:
- Tool Type: 16 IR 11.5 NPT (Finishing Insert)
- Number of Passes: 3–4
- Depth of Cut per Pass: 0.1–0.2 mm
- Spindle Speed: 600 rpm
The finishing tool’s low cutting depth ensures minimal tool wear, reducing the need for frequent replacements and maintaining thread quality.
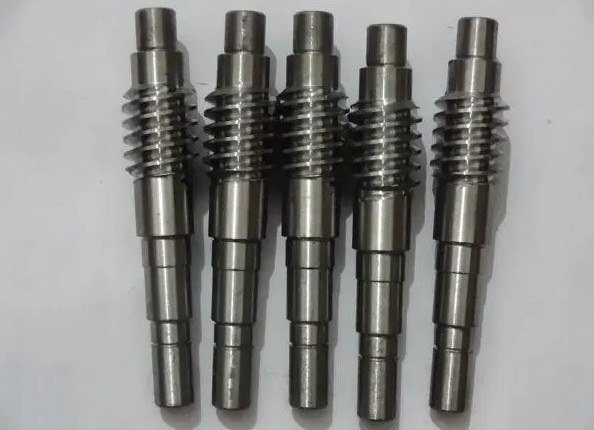
Benefits of the Two-Tool Process
The two-tool process offers several advantages over the conventional single-tool method:
- Reduced Tool Wear: The roughing tool absorbs the majority of the cutting forces and material defect impacts, preserving the finishing tool’s condition for precision work.
- Fewer Machine Stoppages: Minor wear on the roughing tool does not necessitate immediate replacement, allowing continuous machining and reducing downtime.
- Improved Thread Quality: The finishing tool’s minimal cutting depth ensures precise thread dimensions, tooth profiles, and surface finish, reducing scrap and rework rates.
- Cost Savings: Reusing slightly worn finishing inserts for rough threading reduces the need for new inserts, lowering tool costs.
- Enhanced Efficiency: Fewer tool changes and machine adjustments result in longer continuous machining periods, increasing throughput.
This process is particularly effective for threads requiring high dimensional accuracy, precise tooth profiles, small root radii, or minimal crest truncation, as well as for materials with poor machinability or inconsistent hardness.
Applications of the Two-Tool Process
The two-tool threading process is versatile and can be applied to various threading scenarios, particularly those with stringent requirements or challenging materials. Specific applications include:
- High-Precision Threads: Threads with tight tolerances on dimensions, tooth angles, and cumulative pitch errors, such as those used in aerospace or high-pressure systems.
- Small Root Radius or Crest Truncation: Threads requiring minimal root radius or crest truncation, where precise finishing is critical.
- Challenging Materials: Materials with poor machinability, uneven hardness, or defects requiring intermittent cutting, such as cast steel or heat-treated alloys.
While the process typically uses two tools, it can be extended to three or more tools for complex threads, depending on the workpiece and machining requirements.
Addressing CNC System Limitations
During the adoption of the two-tool process, a significant issue was identified with CNC systems: when rough and finish threading are performed at different spindle speeds, the thread paths may not align, leading to defective threads. Manual alignment of rough and finish threads is time-consuming and error-prone, limiting the process’s flexibility. For example, rough threading may require high-speed alloy tools (e.g., 400 rpm), while finishing may use high-speed steel tools at lower speeds (e.g., 600 rpm) for optimal surface finish. Misalignment due to speed differences can also occur during rework or deburring operations, increasing scrap rates.
To overcome this, a variable-speed thread alignment function was developed for CNC systems (e.g., Baoji B80T/B60). This function ensures thread path alignment across different spindle speeds, improving process reliability and flexibility.
Variable-Speed Thread Alignment Function
The variable-speed thread alignment function allows rough and finish threading at different speeds without misalignment. The setup involves:
- Running the Z-axis at 1000 mm/min in automatic or manual mode.
- Switching the CNC display to show “tracking error” using ALT + left/right cursor keys.
- Recording the Z-axis tracking error at 1000 mm/min and entering it into parameter 102049.
This function offers several benefits:
- Efficient Rework: During rework, low speeds (e.g., 100 rpm for M10×1 threads) allow easier observation of thread alignment, after which high-speed machining (e.g., 1000 rpm) can be applied without re-adjusting the starting point.
- Flexible Cutting Parameters: Operators can select optimal speeds for rough and finish threading based on tool and material requirements.
- Reduced Errors: Eliminates misalignment due to programming errors, preventing scrap and potential tool or machine damage.

Case Study: Machining a Locking Nut
A practical example involves machining an M100×2 locking nut for a lathe spindle. The nut, made of heat-treated 45 steel with embedded copper pins, exhibits uneven hardness, leading to inconsistent cutting forces and tool wear. The two-tool process was implemented with the following program:
T0101 (Rough Threading Tool) G99 M3 S400 G0 X95 Z5 G92 X98.8 Z-30 X99.3 X99.7 X100.0 X100.2 X100.3 G0 Z200 T0202 (Finish Threading Tool) G99 M3 S600 G0 X95 Z5 G92 X100.2 Z-30 X100.3 X100.4 X100.5 G0 X200 Z200 M30
The roughing tool removes material in five passes, leaving a small allowance (0.2–0.3 mm) for the finishing tool, which completes the thread in three to four passes. The finishing tool’s first pass serves as a check for thread alignment and roughing tool condition. If misalignment or excessive roughing tool wear is detected, adjustments are made to the roughing tool’s X and Z dimensions to maintain thread consistency without altering the finishing tool’s settings.
Thread alignment is verified using the coloring method, observing chip formation and shape during finishing. This approach ensures stable thread dimensions, reduces tool wear, and minimizes scrap rates.
Implementation Considerations
To maximize the two-tool process’s effectiveness, consider the following:
- Machine and Tool Rigidity: Ensure sufficient rigidity to handle the higher cutting forces during rough threading.
- Allowance for Finishing: Set the roughing allowance (e.g., 0.2–0.3 mm for triangular threads) based on thread type, machine capabilities, and tool condition.
- Tool Condition Monitoring: Regularly inspect the roughing tool for excessive wear to prevent impacts on finishing accuracy.
- CNC System Compatibility: Verify that the CNC system supports variable-speed thread alignment or implement manual adjustments carefully.
By addressing these considerations, the two-tool process can be adapted to various thread types and materials, ensuring consistent quality and efficiency.
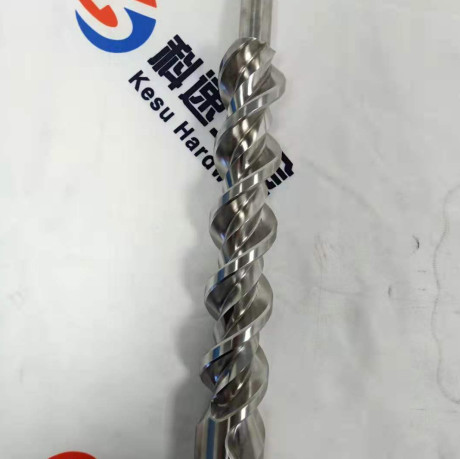
Unleash Precision and Efficiency with Kesu’s Two-Tool Threading Solution
Struggling with subpar thread quality, soaring tool costs, and endless production delays? Kesu’s revolutionary two - tool threading process is here to turn the tide. Specifically engineered for high - volume production, our solution divides threading into rough and finish stages. The roughing tool swiftly clears the bulk material, shrugging off minor wear without a hitch, while the finishing tool hones in on precision, crafting threads with impeccable accuracy and surface finish. Reusing worn finishing inserts for roughing slashes costs, and our variable - speed thread alignment function ensures flawless results every time. With Kesu, bid farewell to inefficiencies and hello to enhanced productivity, superior quality, and significant savings in your thread machining operations.
Conclusion
The two-tool threading process significantly improves thread machining quality by addressing tool wear, machine stoppages, and inconsistent thread quality. By splitting the process into rough and finish stages, it reduces downtime, enhances precision, and lowers tool costs. The addition of a variable-speed thread alignment function further improves flexibility and rework efficiency, making the process suitable for high-precision and challenging material applications. This method, supported by practical implementation and system enhancements, offers a reliable and efficient solution for high-volume thread machining.