The conical support block is a critical component in precision equipment, designed to meet stringent installation and operational stability requirements. Its manufacturing process involves addressing challenges related to material properties, high hardness, and exacting precision standards. This article provides a comprehensive analysis of the machining process, focusing on material selection, heat treatment, precision machining, and quality control to ensure compliance with technical specifications. The process is optimized to achieve the "one-time positioning" principle, ensuring accurate alignment during assembly without extensive adjustments.
Part Specifications and Requirements
The conical support block is an L-shaped component with a conical hole (Sφ40mm) serving as the primary positioning surface. This surface interfaces with mating parts through line contact to ensure precise alignment. The block is mounted onto the equipment's support frame via two perpendicular planes, A and B. Key requirements include:
- Conical Surface Precision: Surface roughness of Ra=0.4μm, with the theoretical center's distance to reference planes controlled within ±0.01mm.
- Perpendicularity: Planes A and B must maintain perpendicularity within ≤0.03mm.
- Hardness: 55–59 HRC, achieved through heat treatment.
- Durability: The component must withstand long-term operational stress without deformation to ensure equipment stability.
The conical hole features a countersunk base with an M5 threaded hole, adding complexity to the CNC machining process. These specifications demand a robust manufacturing process to balance precision, hardness, and structural integrity.
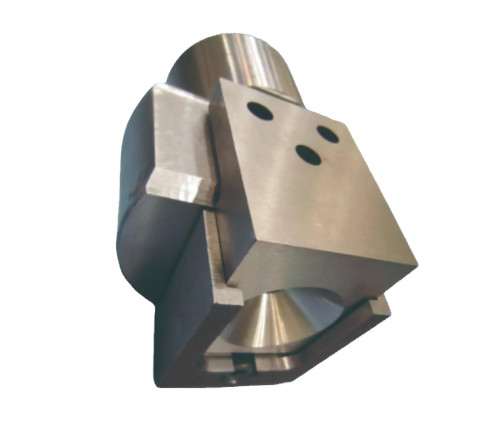
Structural Analysis of the Conical Support Block
The conical support block is made from 9Cr18 stainless steel, a high-carbon, high-chromium martensitic stainless steel known for its hardness and corrosion resistance. Despite its simple L-shaped structure with a conical hole, the part poses significant manufacturing challenges due to the combination of high precision, stringent tolerances, and elevated hardness requirements. Key structural features include:
- Conical Hole: The Sφ40mm conical surface requires a surface roughness of Ra=0.4μm and precise alignment of the theoretical center within ±0.01mm relative to reference planes.
- Perpendicular Planes: Planes A and B, used for mounting, require perpendicularity within ≤0.03mm.
- Threaded Hole: An M5 threaded hole at the base of the conical hole must be machined before heat treatment due to increased hardness post-quenching.
- High Hardness: The material must achieve 55–59 HRC, necessitating careful heat treatment to avoid cracking or deformation.
While individual features may be manageable in isolation, their combination in a single part creates significant manufacturing complexity. The process must address material machinability, heat treatment effects, and precision machining constraints to meet all requirements.
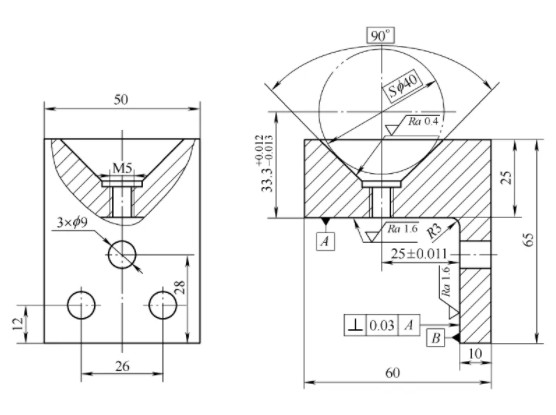
Process Flow Determination
The manufacturing process for the conical support block is designed to address the material's difficulty in machining, high hardness requirements, and stringent precision demands. The process involves multiple stages with strong sequential dependencies, impacting both quality and cost. The established process flow is as follows:
- Material procurement (bar stock)
- Blanking
- Rough machining
- Semi-finish machining
- Heat treatment (quenching)
- Acid pickling (if required)
- Semi-finish grinding of planes A and B
- Finish turning of the conical hole
- Finish grinding of planes A and B
- Grinding and polishing
- Final inspection
Each step is carefully planned to optimize machining allowances and ensure dimensional accuracy. For instance, the M5 threaded hole is machined before quenching due to the material's high hardness post-heat treatment. Acid pickling is included after quenching to remove oxide scale from oil quenching, ensuring clean surfaces for subsequent machining.
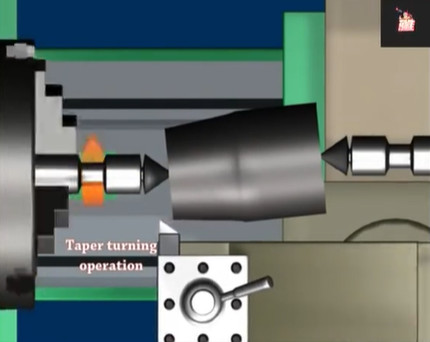
Blank Selection and Preparation
The choice of blank is critical to achieving the required mechanical properties and dimensional stability. The conical support block experiences significant pressure through line contact at the conical hole, necessitating a material and blank form that resists deformation under long-term use. The selected blank preparation process includes:
- Material: 9Cr18 stainless steel bar stock.
- Blanking: Cutting the bar stock to approximate dimensions.
- Forging: Forming the blank into a block shape to reduce stress concentrations at the L-shaped corner.
- Normalizing: Heat treatment to refine grain structure and minimize internal stresses before quenching.
A block-shaped blank is preferred over other forms to avoid the cost of custom molds and to enhance structural integrity by reducing stress concentrations. Normalizing ensures a uniform microstructure, improving the material's response to subsequent quenching and minimizing distortion.
Heat Treatment Process
Heat treatment is a pivotal step to achieve the required hardness (55–59 HRC) and durability. The process for 9Cr18 stainless steel involves quenching and low-temperature tempering to balance hardness, wear resistance, and corrosion resistance.
Heat Treatment Method
The standard heat treatment process includes:
- Quenching: Heating to 1,050°C followed by oil cooling to achieve a martensitic structure.
- Tempering: Heating to 200°C to relieve internal stresses while maintaining hardness at 58 HRC.
An alternative vacuum quenching method is available, which reduces surface oxidation. However, vacuum quenching results in a slightly coarser grain structure due to the removal of gas impurities that inhibit grain growth. The impact on toughness is minimal, making both methods viable. The heat treatment parameters are summarized in the table below:
Parameter | Oil Quenching | Vacuum Quenching |
---|---|---|
Quenching Temperature | 1,050°C | 1,050°C |
Cooling Medium | Oil | Nitrogen |
Tempering Temperature | 200°C | 200°C |
Hardness | 58 HRC | 58 HRC |
Both methods require precise temperature control using equipment with reliable thermocouples and automated parameter recording. The cooling medium (oil or nitrogen) is equipped with a circulation system to maintain consistent temperatures within process limits.
Post-Heat Treatment Processing
Post-heat treatment steps depend on the quenching method:
- Oil Quenching: Requires sandblasting and acid pickling to remove oxide scale. The M5 threaded hole, machined before quenching, may need manual thread repair after pickling.
- Vacuum Quenching: Minimal surface oxidation eliminates the need for extensive post-processing.
These steps ensure the part is ready for precision machining while maintaining surface integrity.
Precision Machining Process
Precision machining is critical to achieving the required dimensional and surface quality specifications. The process is divided into rough and finish machining stages, with careful consideration of machining allowances to accommodate heat treatment effects.
Rough Milling
Rough milling establishes the initial geometry while leaving sufficient material for subsequent operations. Key considerations include:
- Machining Allowances:
- Planes A and B (Ra=1.6μm): 0.4mm allowance for finish machining.
- Parallel planes: 0.2mm allowance.
- Conical hole: 0.2–0.3mm allowance for finish turning and polishing.
- Semi-Finish Grinding: Performed before finish turning to establish reference planes A and B with 0.1–0.2mm allowance for final grinding.
- Positioning: The 65mm upper plane and 60mm right plane are used as reference surfaces for finish grinding, each with a 0.2mm grinding allowance.
These allowances ensure that post-quenching distortions are accommodated while maintaining precision during final machining.
Finish Turning and Polishing
Finish turning of the conical hole is a critical step due to the high hardness (55–59 HRC) and stringent surface roughness requirement (Ra=0.4μm). A custom tooling setup is used to enhance alignment efficiency:
- Tooling Design: The workpiece is positioned using plane A and the M5 threaded hole, secured with a pin and clamped to a cylindrical fixture compatible with a self-centering chuck.
- Alignment: Conical surface alignment is controlled within ≤0.1mm to ensure uniform machining allowances across all surfaces.
- Finish Turning: Performed with minimal cutting depths to preserve dimensional accuracy.
- Grinding and Polishing: Grinding is conducted on a lathe with safety measures, followed by manual polishing to achieve Ra=0.4μm.
This process ensures the conical surface meets both dimensional and surface quality requirements.
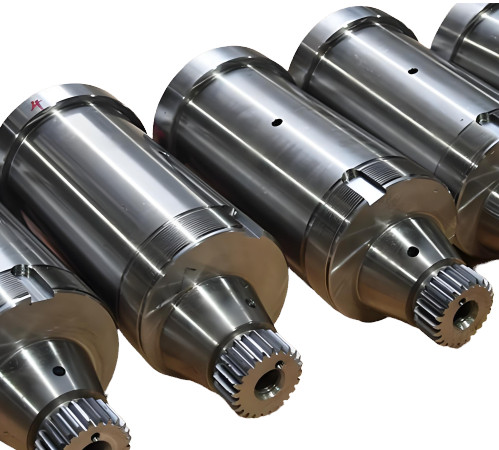
Quality Control and Validation
Quality control is integral to ensuring the conical support block meets all specifications. Key inspection steps include:
- Dimensional Inspection: Verifying the theoretical center's distance to reference planes within ±0.01mm using precision coordinate measuring machines.
- Surface Roughness: Measuring Ra=0.4μm on the conical surface with profilometers.
- Perpendicularity: Checking planes A and B for perpendicularity within ≤0.03mm.
- Hardness Testing: Confirming 55–59 HRC using a Rockwell hardness tester.
Process validation involved trial production runs to collect data, which informed process optimizations. The finalized process was implemented in production, and the components passed customer acceptance tests during on-site installation and commissioning, confirming process reliability for batch production.
Conclusion
The manufacturing process for the conical support block integrates material selection, heat treatment, and precision machining to meet stringent precision and durability requirements. By optimizing blank preparation, heat treatment parameters, and machining allowances, the process achieves the "one-time positioning" goal, ensuring accurate assembly without extensive adjustments. The use of custom tooling and rigorous quality control further enhances efficiency and reliability. This systematic approach has proven effective in production, delivering high-quality components that meet technical specifications and provide economic benefits through streamlined manufacturing.