Precision multi-cavity molds are critical in modern manufacturing, requiring high accuracy and efficiency to meet demanding production schedules. This article details optimized machining processes, including CNC, EDM, WEDM, GRI, and TUR, to enhance productivity and ensure quality in multi-cavity mold production. By implementing advanced techniques and in-process inspection methods, manufacturers can achieve significant efficiency gains while maintaining stringent accuracy standards.
Current Machining Status and Optimization Goals
The production of an 8-cavity test mold, as a reference, required 1,304 hours of total machining time. Extrapolating to a 128-cavity mold, the estimated machining time would be 20,864 hours, necessitating 208 machines over a 45-day cycle. This is resource-intensive and impractical for meeting typical customer delivery timelines. The primary goal is to reduce machining time by an average of 30% across all processes while achieving a 95% pass rate for part accuracy.
Key objectives include streamlining each process, reducing setup times, and minimizing rework caused by dimensional inaccuracies. The following sections outline specific improvements for each machining process, supported by practical tools and techniques to meet these targets.
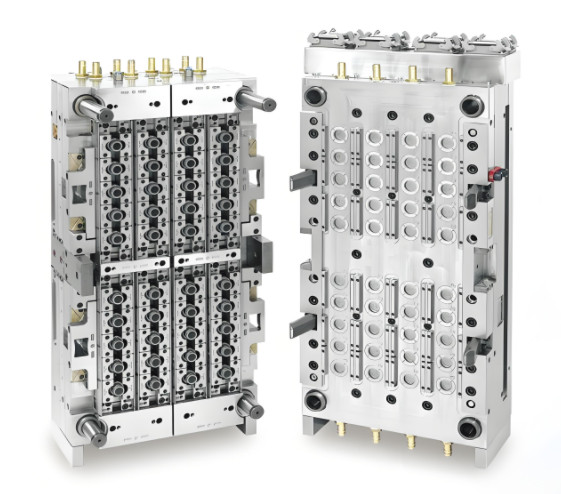
CNC Rough Milling Optimization
CNC rough milling is a foundational process in mold machining. The original approach used an offset rough milling strategy, which was computationally complex and time-consuming. By adopting PowerMILL software, developed by Delcam, the process was optimized through a "pre-drilling + contour strategy." This adjustment simplified tool paths, reducing machining time by 32%. PowerMILL’s robust safety features and versatile roughing and finishing strategies enabled precise control over tool movements, minimizing unnecessary cuts.
A custom fixture was designed to hold six parts simultaneously, suitable for manual handling and eliminating the need for individual part alignment. Previously, each part required four setups, totaling 24 setups for six parts and 12.6 hours of machining time. The new fixture reduced setups to four, with a total machining time of 8.6 hours (1.3 hours per part plus 0.2 hours per setup), achieving a 46% efficiency improvement.
TUR Process Optimization
The turning (TUR) process originally involved single-part machining with a 15mm process allowance, requiring additional wire-cutting to remove excess material. The optimized approach uses elongated raw material to machine eight parts in one setup, reducing machining time by 35%. Specific improvements include:
- Combined material preparation to complete machining in one setup, saving 0.5 hours per part in wire-cutting.
- Direct machining of sealing ring and water baffle grooves, reducing post-heat-treatment grinding by 0.3 hours per part.
- Reducing turning allowance from 0.3mm to 0.15mm, cutting semi-finishing time by 0.5 hours per part.
- Material cost reduction of 25%, requiring only 260mm of material for eight parts compared to 340mm previously.
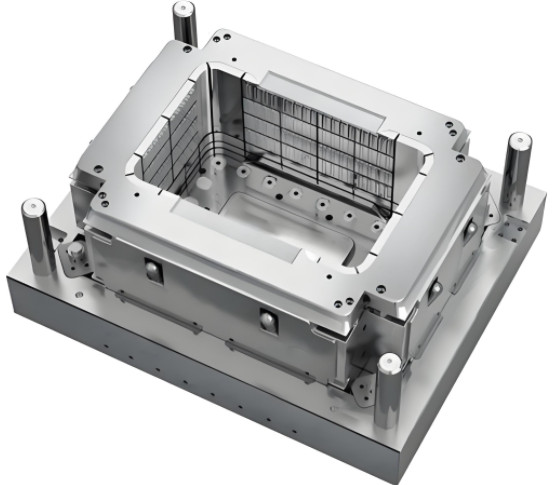
GRI Process Optimization
The grinding (GRI) process was enhanced by designing a dedicated fixture to eliminate individual part alignment. The original single-part process included a process allowance, requiring multiple setups. The new fixture enables batch processing, reducing alignment time by 0.3 hours per part and grinding time for sealing and water baffle grooves by 0.3 hours per part, achieving a 30% efficiency gain.
WEDM Process Optimization
Wire Electrical Discharge Machining (WEDM) originally involved single-part setups, requiring 12 setups for six parts and 7.2 hours of total machining time. A new fixture enables batch processing, reducing setups to one with 0.2 hours of alignment time and 5 hours of total machining time, yielding a 44% efficiency improvement. The fixture minimizes alignment errors and enhances machine utilization by enabling continuous operation.

CNC-RDS Fine Milling Optimization
The fine milling process (CNC-RDS) was optimized by adopting a fixture for batch processing and integrating CMM (Coordinate Measuring Machine) for off-machine measurement. Originally, single-part machining required 7.2 hours for six parts. The new approach reduces total machining time to 5.3 hours, achieving a 36% efficiency gain. Key improvements include:
- Fixture-based batch processing, reducing alignment time by 0.2 hours per part.
- Program linking software to streamline tool changes, eliminating three tool setups and preheating cycles (300 seconds each).
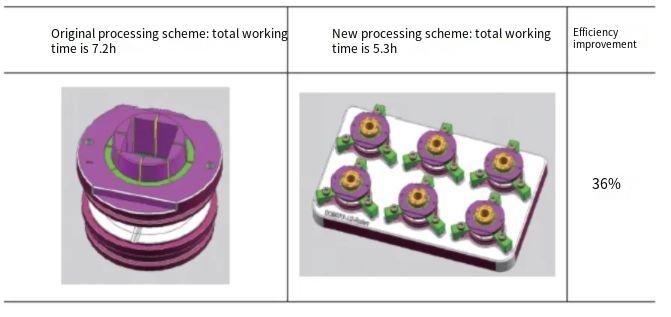
EDM Process Optimization
Electrical Discharge Machining (EDM) was significantly improved through automation and parameter adjustments. Key enhancements include:
- Implementation of an automated tool library for 24-hour unmanned operation.
- Electrode design optimization, merging electrodes and adjusting discharge parameters to reduce switching time, achieving an 83% efficiency increase.
- Hybrid EDM approach using coarse graphite for roughing and high-purity copper for finishing, improving surface quality.
- Parameter adjustments to achieve a VDI-14# surface finish (Ra 0.56µm), eliminating post-machining polishing.
- Optimized EDM parameters (e.g., model number E, segment numbers I, J, O, jump amplitude S, cycle T, speed F, finishing segment M, time U), reducing machining time from 4 hours 35 minutes to 2 hours 24 minutes.
Process | Original Time (h) | Optimized Time (h) | Efficiency Gain (%) |
---|---|---|---|
EDM | 4.58 | 2.4 | 83 |
CNC Rough Milling (6 parts) | 12.6 | 8.6 | 46 |
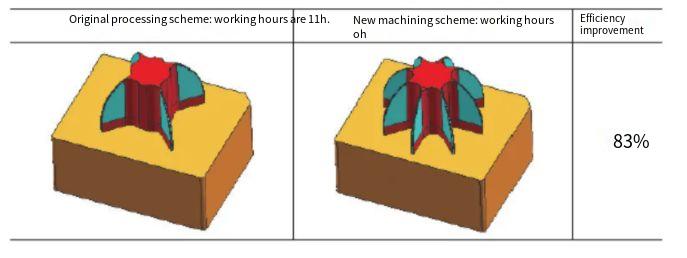
Fixture Development for Batch Processing
Custom fixtures were developed to enable batch processing across CNC, WEDM, and GRI processes. These fixtures reduce setup times and improve machine utilization by allowing multiple parts to be machined in a single setup. For example, CNC fixtures accommodate six parts for simultaneous machining of multiple surfaces, while WEDM and GRI fixtures enable rapid part switching and multi-surface grinding, respectively. This shift from single-part to batch processing enhances efficiency and ensures consistent part quality.
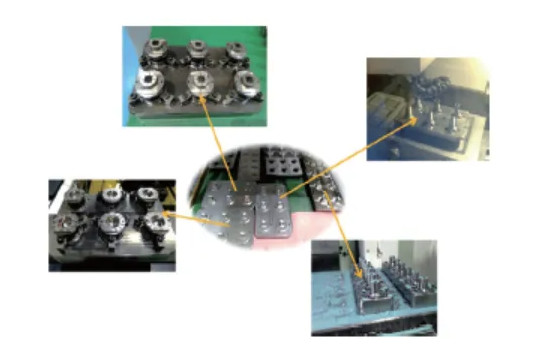
Coordinate Grinding for Precision Mold Frames
Coordinate grinding is essential for producing high-precision mold frames, particularly for guide pillars and bushings. Using a coordinate grinding machine with CBN (Cubic Boron Nitride) wheels ensures superior hardness (8000–9000 HV), low friction, and high thermal conductivity, capable of withstanding 1400–1500°C. This setup minimizes thermal damage to parts, enhances surface quality, and introduces compressive residual stress, ensuring precise positioning and shape accuracy critical for mold assembly.

In-Process Inspection for Accuracy Control
In-process inspection is vital for minimizing rework and ensuring dimensional accuracy. Custom inspection tools were developed to verify critical features during machining, reducing the risk of dimensional errors. Two key inspection methods include:
- Pass/Stop Gauge: For features like a φ13mm hole with a tolerance of 0.01–0.02mm, a 13.01mm pass gauge fits into the hole, while a 13.02mm stop gauge does not. If the pass gauge fits and the stop gauge does not, the feature is within tolerance; otherwise, immediate rework is performed.
- Side Taper Gauge: For a 3° side wall feature with a 0–0.003mm tolerance, a tight-fit height gauge is inserted, and the height difference between the gauge and part surface is measured using a dial indicator. A difference of 0–0.02mm indicates a side gap of 0.001mm, meeting tolerance requirements.
These tools, combined with CMM first-piece inspection, enable rapid, accurate verification, improving the first-pass yield and reducing rework-related positioning errors.
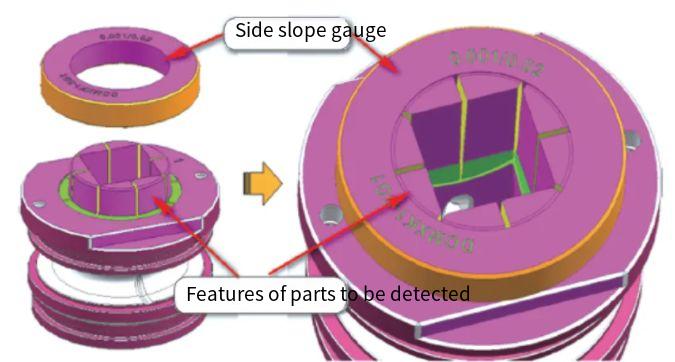
Conclusion
Through targeted optimizations in CNC, TUR, GRI, WEDM, and EDM processes, alongside fixture development and in-process inspection, the machining of precision multi-cavity mold parts achieved an average efficiency increase of 30% and a 90% pass rate. These improvements address the demands of high-precision mold production, offering practical and replicable methods for manufacturers to enhance productivity and quality in real-world applications.