Rapid prototyping is a critical process in product development, enabling designers and engineers to transform ideas into physical models for testing, validation, and feedback. By leveraging advanced technologies like 3D printing, CNC machining, and others, rapid prototyping accelerates the design cycle, reduces costs, and enhances flexibility. This article explores the various types of rapid prototyping, detailing their processes, materials, speeds, costs, and industry applications to provide a comprehensive understanding of their roles in modern manufacturing.
What is Rapid Prototyping?
Rapid prototyping refers to the quick fabrication of physical parts, models, or assemblies using 3D computer-aided design (CAD) data, primarily through additive manufacturing techniques like 3D printing. It allows companies to create prototypes for functional testing, user feedback, or market evaluation. Prototypes range from low-fidelity models, which differ significantly from the final product, to high-fidelity models that closely resemble the intended design. The process is iterative, enabling designers to refine products at various development stages.
The workflow typically includes:
- Design Creation: A 3D model is created using CAD software, forming the foundation for the prototype.
- Data Preparation: The CAD model is converted into a compatible format, such as STL, for the chosen prototyping technology.
- Machine Setup: The prototyping machine is calibrated and loaded with appropriate materials (e.g., resin, metal powder, or plastic filament).
- Prototyping: The machine builds the prototype layer by layer based on the CAD specifications.
- Post-Processing: The prototype undergoes finishing processes like sanding, painting, or assembly to achieve the desired properties.
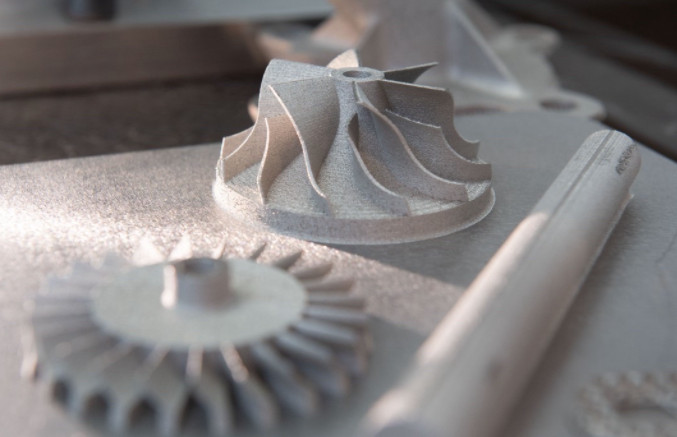
Types of Rapid Prototyping Technologies
Rapid prototyping encompasses a variety of technologies, each with unique processes, materials, and applications. Below is a detailed exploration of the primary methods used in industry today.
Stereolithography (SLA)
Stereolithography (SLA) is an additive manufacturing process that uses a computer-controlled ultraviolet (UV) laser to cure liquid photopolymer resin layer by layer. The laser traces the cross-section of the part on the resin surface, solidifying it, and the platform lowers to allow the next layer to form. Each layer bonds to the one below, building the prototype incrementally.
- Materials: Photopolymer resins that solidify under UV light, available in various formulations for flexibility, durability, or transparency.
- Speed: SLA offers fast build times, typically completing parts in hours, depending on size and complexity.
- Cost: High equipment and maintenance costs, but efficient for complex, high-precision prototypes.
- Applications: SLA is widely used in aerospace, automotive, and medical industries for intricate parts, molds, and dental models.
- Limitations: Limited material strength compared to engineering-grade materials and sensitivity to UV degradation.
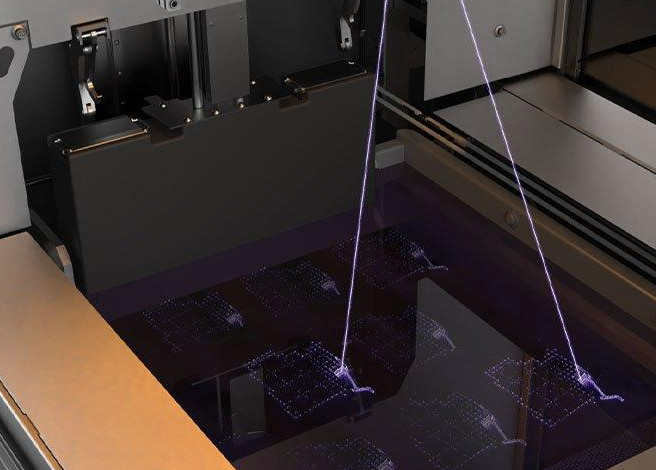
Selective Laser Sintering (SLS)
Selective Laser Sintering (SLS) employs a CO2 laser to fuse nylon-based or thermoplastic polyurethane (TPU) powders into solid parts. The laser sinters the powder on a heated bed, and a roller applies a fresh layer of powder after each pass, repeating until the part is complete.
- Materials: Nylon, TPU, or other polymer powders; some systems support metal or ceramic powders.
- Speed: Fast production cycles due to no need for support structures, ideal for complex geometries.
- Cost: Lower material costs due to powder recyclability, but high equipment costs.
- Applications: Used in aerospace, automotive, and electronics for durable prototypes, functional parts, and small-batch production.
- Limitations: Rough surface finish and limited fine detail compared to SLA.
Fused Deposition Modeling (FDM)
Fused Deposition Modeling (FDM) extrudes melted thermoplastic filament through a nozzle to build parts layer by layer. The filament solidifies as it cools, forming a robust prototype suitable for functional testing.
- Materials: Thermoplastics like ABS, polycarbonate, or ABS-polycarbonate blends.
- Speed: Moderate build speed, enhanced by automated calibration systems.
- Cost: Cost-effective due to high material utilization and long material lifespan, though support removal can be labor-intensive.
- Applications: Common in consumer goods, education, and automotive for prototypes, teaching models, and functional parts.
- Limitations: Visible layer lines and potential for warping in larger parts.
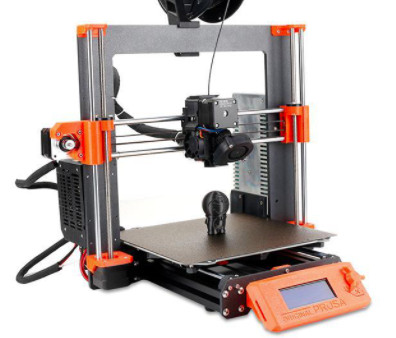
Digital Light Processing (DLP)
Digital Light Processing (DLP) uses a digital projector to flash an image of each layer onto a photopolymer resin, curing it instantly. This process is faster than SLA for certain applications due to its ability to cure entire layers simultaneously.
- Materials: Photopolymer resins with properties tailored for flexibility, strength, or clarity.
- Speed: High-speed production due to layer-by-layer projection, ideal for small, detailed parts.
- Cost: Moderate, depending on equipment and resin type; competitive for high-resolution prototypes.
- Applications: Used in projection systems, display technology, and high-precision prototype design.
- Limitations: Limited build volume compared to other methods.
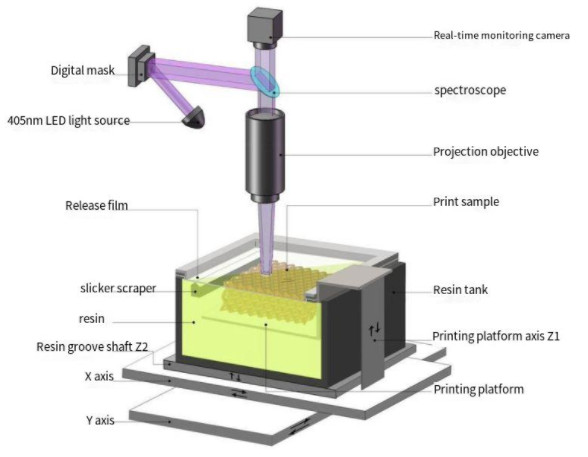
Laminated Object Manufacturing (LOM)
Laminated Object Manufacturing (LOM) layers adhesive-backed sheets of paper, plastic, or metal, cutting each layer with a laser or blade to form the prototype. The layers are bonded together to create the final shape.
- Materials: Paper, sheet metal, or polymer sheets.
- Speed: Fast for large parts due to the layer-cutting process.
- Cost: Low, thanks to inexpensive materials and simple equipment.
- Applications: Ideal for visual prototypes and marketing models in aerospace, automotive, and medical sectors.
- Limitations: Limited material strength and suitability for functional testing.

Binder Jetting
Binder Jetting deposits a liquid binding agent onto a powder bed to form parts layer by layer. The process is versatile and can produce full-color prototypes.
- Materials: Metal, ceramic, or sand powders.
- Speed: Fast due to rapid deposition and no need for support structures.
- Cost: Moderate, depending on powder type and part complexity.
- Applications: Used in automotive, medical, and aerospace for high-precision models and small-batch parts.
- Limitations: Post-processing (e.g., sintering) may be required for strength.
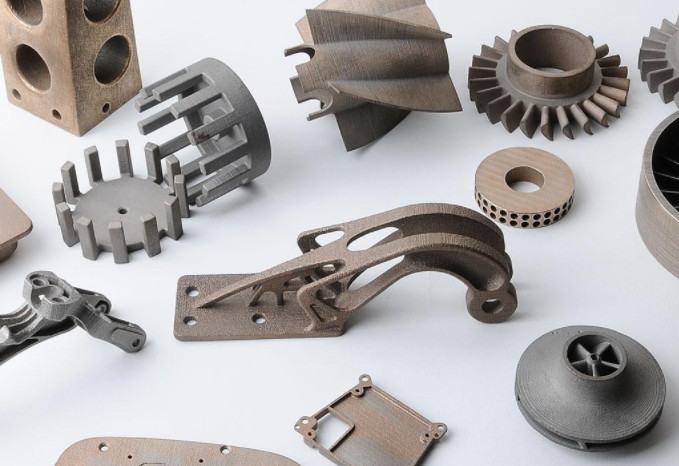
Direct Metal Laser Sintering (DMLS)
Direct Metal Laser Sintering (DMLS) uses a laser to sinter metal powders into dense, functional parts, ideal for complex geometries unachievable with traditional methods.
- Materials: Metal powders like nickel, cobalt, or iron-based alloys.
- Speed: Moderate, depending on part size and complexity.
- Cost: High due to expensive materials and equipment.
- Applications: Aerospace, automotive, and medical for high-stress, complex components.
- Limitations: Requires post-processing for optimal surface finish.
Electron Beam Melting (EBM)
Electron Beam Melting (EBM) uses a high-energy electron beam to melt metal powders in a vacuum, producing strong, heat-resistant parts.
- Materials: Titanium, cobalt-chromium, or other metal alloys.
- Speed: Faster than DMLS due to thicker layers and rapid scanning.
- Cost: High, but efficient material use can offset costs.
- Applications: Aerospace, medical implants, and industrial components.
- Limitations: Limited to conductive materials and requires a vacuum environment.
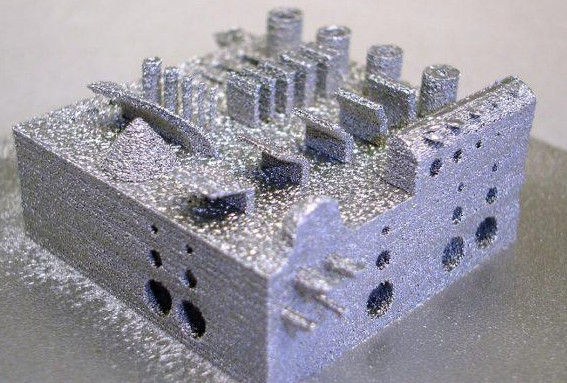
Selective Laser Melting (SLM)
Selective Laser Melting (SLM) fully melts metal powders with a high-power laser, creating dense, high-strength parts.
- Materials: Stainless steel, titanium, or other metal alloys.
- Speed: Moderate, depending on part complexity.
- Cost: High, but material efficiency reduces waste.
- Applications: Aerospace, medical, and automotive for high-performance parts.
- Limitations: High energy consumption and need for post-processing.
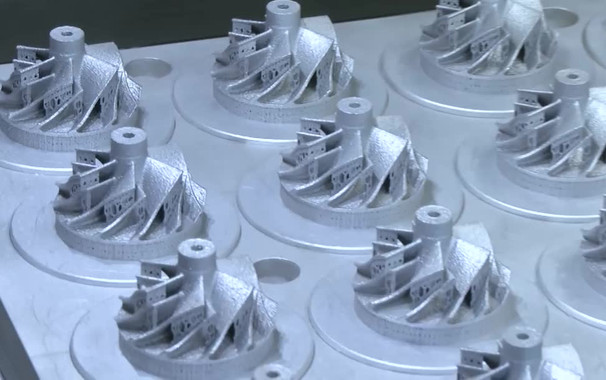
PolyJet Printing
PolyJet Printing sprays layers of liquid photopolymer resin, curing them instantly with UV light, allowing for multi-material and multi-color parts in a single print.
- Materials: Photopolymer resins in various colors and properties.
- Speed: Fast for high-fidelity, multi-material models.
- Cost: Varies based on material and complexity.
- Applications: Product design, medical models, and automotive components.
- Limitations: Limited material strength for functional testing.
Injection Molding for Prototyping
Injection molding, though traditionally a production method, is adapted for rapid prototyping using quick-turn molds. Molten material is injected into a mold to form parts.
- Materials: ABS, nylon, or other plastics.
- Speed: Moderate, requiring mold design and fabrication time.
- Cost: High for mold creation, but cost-effective for larger quantities.
- Applications: Automotive, electronics, and consumer goods for small-batch prototypes.
- Limitations: Mold fabrication delays prototyping speed.
CNC Machining
CNC machining is a subtractive process that removes material from a solid block using computer-controlled tools to create precise parts.
- Materials: Metals, plastics, or wood.
- Speed: Varies based on part complexity and machine capabilities.
- Cost: High due to precision equipment and tooling.
- Applications: Aerospace, automotive, and medical for complex, high-precision parts.
- Limitations: Material waste and limited geometric complexity compared to additive methods.
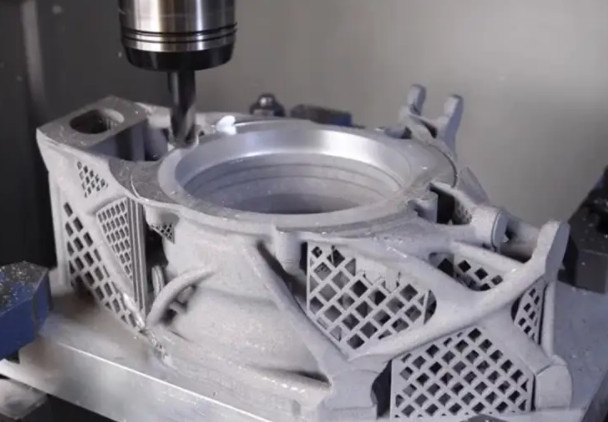
Water Jet Cutting
Water Jet Cutting uses high-pressure water, often mixed with abrasives, to cut materials into precise shapes for prototyping.
- Materials: Metals, plastics, glass, or composites.
- Speed: Fast for thin materials, slower for thicker ones.
- Cost: Moderate, depending on equipment and material.
- Applications: Automotive, aerospace, and art for intricate shapes.
- Limitations: Limited to 2D or 2.5D cutting; less suitable for complex 3D parts.
Comparison of Rapid Prototyping Technologies
Technology | Materials | Speed | Cost | Key Applications |
---|---|---|---|---|
SLA | Photopolymer resins | Fast | High | Aerospace, medical, dental models |
SLS | Nylon, TPU, metal powders | Fast | Moderate | Automotive, aerospace, functional parts |
FDM | Thermoplastics (ABS, polycarbonate) | Moderate | Low | Consumer goods, education, automotive |
DLP | Photopolymer resins | Very Fast | Moderate | Display tech, high-precision prototypes |
DMLS | Metal powders | Moderate | High | Aerospace, medical implants |
Key Considerations in Choosing a Prototyping Method
Selecting the appropriate rapid prototyping technology depends on several factors:
- Material Requirements: Match the material properties (strength, flexibility, heat resistance) to the prototype’s purpose.
- Geometric Complexity: Additive methods like SLS and DMLS excel in complex shapes, while CNC is better for precise, simple geometries.
- Speed Needs: DLP and SLS are faster for quick iterations, while CNC and injection molding may require more setup time.
- Cost Constraints: FDM and LOM are cost-effective for early-stage prototypes, while DMLS and EBM are suited for high-value applications.
- Application Type: Visual models may use LOM or PolyJet, while functional testing requires SLS, DMLS, or CNC.
Conclusion
Rapid prototyping technologies provide designers and engineers with versatile tools to transform concepts into tangible prototypes efficiently. From SLA’s precision to DMLS’s strength, each method offers unique advantages tailored to specific materials, speeds, costs, and applications. By understanding these technologies and their constraints, manufacturers can select the most suitable method to accelerate product development, improve design quality, and meet market demands effectively.