In mechanical machining, the role of layout workers is critical for ensuring product quality and optimizing resource use. These skilled professionals mark precise guidelines on workpieces to guide subsequent machining processes. Their expertise becomes particularly valuable when dealing with defective blanks, where deviations in shape or dimensions exceed technical tolerances. One specialized technique, known as "material borrowing," allows layout workers to reallocate processing allowances to salvage such blanks, reducing waste and economic losses. This method involves redistributing machining allowances to prioritize critical dimensions, ensuring the functionality of the final part despite initial imperfections. Below, we explore the significance of layout workers and detail the material borrowing technique through practical examples.
The Role of Layout Workers in Machining
Layout workers are experienced professionals responsible for marking reference lines and points on workpieces before machining. Their work ensures that subsequent operations, such as cutting, drilling, or turning, align with design specifications. This role requires a deep understanding of technical drawings, material properties, and machining processes. Layout workers use precision tools like scriber blocks, calipers, and surface plates to establish benchmarks that guide machining operations.
Their importance lies in their ability to interpret complex blueprints and translate them into physical markings on the workpiece. This ensures dimensional accuracy and alignment, particularly for parts with tight tolerances. In cases of defective blanks—where casting or forming errors result in misaligned features or insufficient material—layout workers employ creative strategies like material borrowing to salvage parts. Their expertise directly impacts production efficiency, product quality, and cost management, making them indispensable in machining workshops.
Layout workers also act as problem-solvers, addressing issues that arise from material imperfections. By carefully analyzing defects and adjusting machining plans, they prevent the scrapping of valuable blanks, thereby reducing material waste and production costs. Their role requires not only technical skill but also practical experience, as they often make critical decisions that balance functionality with manufacturing constraints.
Understanding Material Borrowing
Material borrowing is a technique used to salvage defective blanks by redistributing machining allowances to compensate for dimensional or positional errors. This method is particularly effective when blanks exhibit eccentricity, missing material, or other casting defects that render them non-compliant with technical specifications. Instead of discarding such blanks, layout workers strategically select a new reference point or datum to ensure sufficient material remains for machining critical features.
The process involves analyzing the defect, assessing the available material, and determining a new machining benchmark that optimizes the use of existing material. This approach prioritizes key dimensions or functional surfaces, ensuring the final part meets performance requirements. Material borrowing requires precise calculations and a thorough understanding of the part’s functional requirements, as well as coordination with clients or engineers to confirm acceptable deviations.
The technique is most commonly applied in scenarios where scrapping a blank would result in significant economic loss, such as in the production of large castings or expensive materials. By reallocating allowances, layout workers can transform an otherwise unusable blank into a functional part, demonstrating the technique’s value in cost-sensitive manufacturing environments.
Case Study 1: Managing Eccentricity in a Disc-Shaped Casting
Consider a disc-shaped casting with concentric inner and outer diameters, as shown in Figure 1 (not included here). In an ideal blank (Figure 2), the inner hole and outer diameter are perfectly concentric, with uniform machining allowances. However, casting errors can result in an eccentric blank, where the inner hole’s center is offset from the outer diameter’s center, as depicted in Figure 3. In this example, the eccentricity is 8 mm, creating a challenge for machining.
If the inner hole’s center (O1) is chosen as the layout benchmark (Figure 4), the inner hole has sufficient machining allowance, but the outer diameter lacks material at its thinnest point, with a shortfall of 3 mm. Conversely, if the outer diameter’s center (O2) is used as the benchmark (Figure 5), the outer diameter has adequate allowance, but the inner hole lacks 3 mm of material at its thinnest point. Neither approach is viable, as both result in insufficient material for machining.
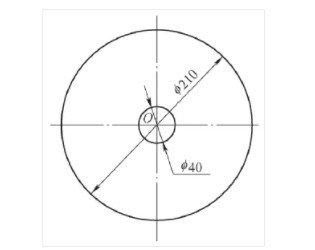
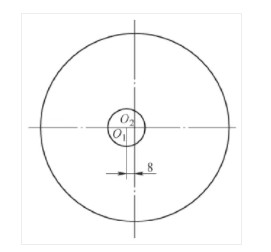
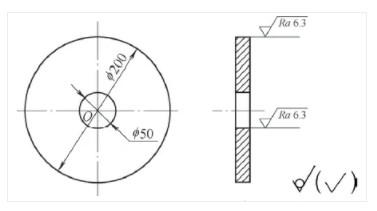
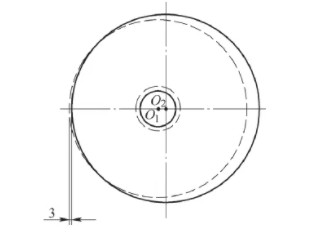
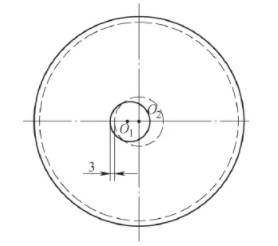
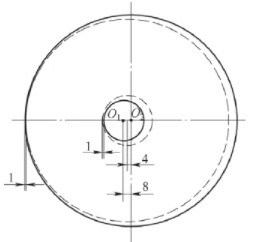
Material borrowing addresses this issue by selecting a new benchmark: the midpoint between the inner hole’s center (O1) and the outer diameter’s center (O2), as shown in Figure 6. This approach ensures that both the inner hole and outer diameter have at least 1 mm of machining allowance at their thinnest points. The calculations for this adjustment are straightforward:
- Eccentricity: 8 mm (distance between O1 and O2).
- New benchmark: Midpoint of O1 and O2, splitting the 8 mm eccentricity equally (4 mm offset from each center).
- Resulting allowances: Inner hole ≥ 1 mm, outer diameter ≥ 1 mm.
This method ensures that both critical features can be machined within tolerances, salvaging the blank and avoiding scrapping costs. The table below summarizes the outcomes of different benchmark choices:
Benchmark | Inner Hole Allowance | Outer Diameter Allowance | Outcome |
---|---|---|---|
Inner Hole Center (O1) | Sufficient | Short by 3 mm | Unusable |
Outer Diameter Center (O2) | Short by 3 mm | Sufficient | Unusable |
Midpoint (O1-O2) | ≥ 1 mm | ≥ 1 mm | Viable |
Case Study 2: Prioritizing Key Features in a Defective Blank
Another example involves a bearing seat bracket, as shown in Figure 7. The ideal blank (Figure 8) has a uniform 5 mm machining allowance on all sides. However, a casting defect results in a missing section at the lower-right corner, with a 25 mm x 25 mm notch (Figure 9). The total machining allowance in both horizontal and vertical directions is only 10 mm (5 mm per side), making it impossible to machine the part to exact specifications without addressing the defect.
After consultation with the client, it was determined that a small notch (up to 12 mm in length) in the lower-right corner would not significantly impair the part’s function as a bearing seat bracket. To salvage the blank, the layout benchmark was adjusted from the center of the blank (O) to a new point (O1), shifted 3 mm upward and 3 mm to the left (Figure 10). This adjustment yielded the following allowances:
- Left side: 2 mm
- Top side: 2 mm
- Right side: 8 mm
- Bottom side: 8 mm
- Semicircular groove: Sufficient allowance
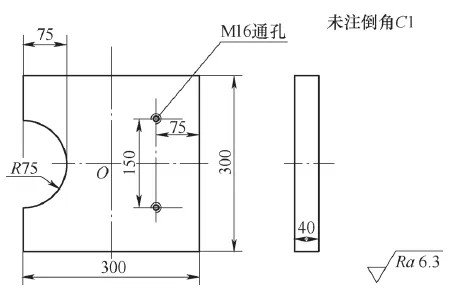
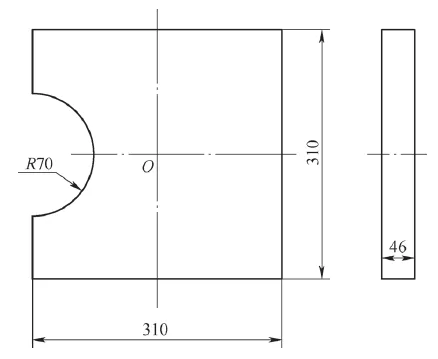
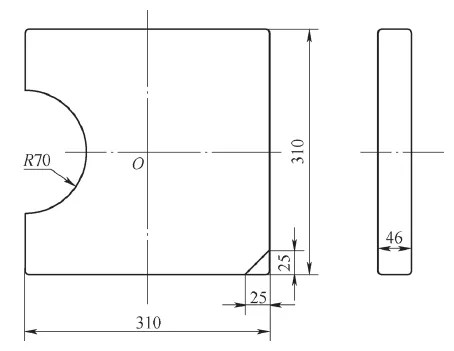
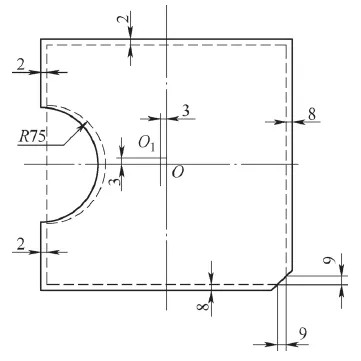
The resulting notch after machining was reduced to 9 mm x 9 mm, within the client’s acceptable limit of 12 mm. This approach ensured that critical features, such as the semicircular groove, were preserved, while the minor notch did not compromise functionality. The table below compares the original and adjusted benchmarks:
Benchmark | Left/Top Allowance | Right/Bottom Allowance | Notch Size | Outcome |
---|---|---|---|---|
Center (O) | 5 mm | 5 mm | 25 mm x 25 mm | Unusable |
Shifted (O1) | 2 mm | 8 mm | 9 mm x 9 mm | Viable |
Key Considerations in Material Borrowing
Material borrowing requires careful planning and execution to be effective. Layout workers must consider several factors:
- Defect Analysis: Accurately measure the extent of eccentricity, missing material, or other defects to determine feasible adjustments.
- Functional Priorities: Identify critical dimensions or features that must be preserved to ensure the part’s performance.
- Client Coordination: Communicate with clients or engineers to confirm acceptable deviations, as seen in the bearing seat example.
- Precision Tools: Use high-precision tools to mark new benchmarks accurately, ensuring machining aligns with the adjusted plan.
- Material Constraints: Ensure sufficient material remains for all critical surfaces after reallocation, avoiding compromises that could affect part integrity.
These considerations highlight the technical expertise and problem-solving skills required of layout workers, reinforcing their critical role in the machining process.
Conclusion
Layout workers play an essential role in mechanical machining by ensuring precision, optimizing material use, and salvaging defective blanks through techniques like material borrowing. This method allows for the reallocation of machining allowances to compensate for defects such as eccentricity or missing material, as demonstrated in the disc-shaped casting and bearing seat bracket examples. By prioritizing critical dimensions and coordinating with clients, layout workers minimize waste and reduce economic losses. Their expertise, combined with strategic approaches like material borrowing, underscores their importance in achieving high-quality outcomes in machining operations.