Metal forming is a critical aspect of parts design and manufacturing, enabling the creation of components with precise shapes, sizes, and properties. This article explores eight primary metal forming processes: casting, plastic forming, machining, welding, powder metallurgy, metal injection molding, semi-solid forming, and 3D printing. Each process is detailed with its workflow, technical characteristics, applications, and limitations, providing a comprehensive and technical overview for professionals and engineers.
Casting
Casting involves pouring molten metal into a mold cavity that matches the desired part’s shape and size, allowing it to cool and solidify to form a blank or finished part. Known as liquid metal forming, this process is versatile and widely used across industries.
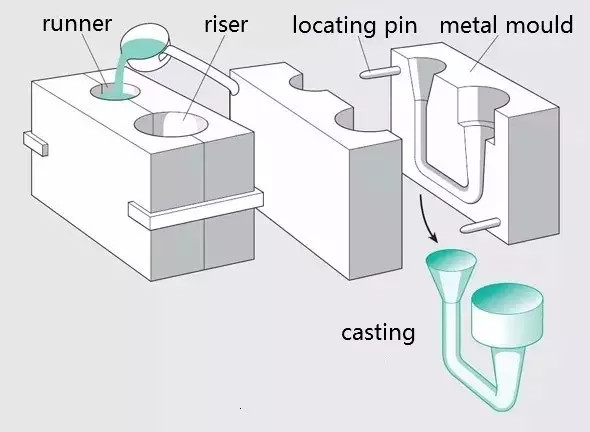
Process Workflow
The casting process follows these steps: molten metal preparation, mold filling, solidification and shrinkage, and casting removal.
Technical Characteristics
- Capable of producing parts with complex shapes, especially those with intricate internal cavities.
- Highly adaptable, suitable for various alloys and part sizes, from small components to large structures.
- Utilizes cost-effective materials, with recyclable scraps and low equipment investment.
- Limitations include high scrap rates, lower surface quality, and challenging working conditions.
Types of Casting
Casting encompasses several methods, each with distinct applications and characteristics. Below are the primary types:
Casting Method | Description | Applications | Advantages | Limitations |
---|---|---|---|---|
Sand Casting | Uses sand molds to produce castings, suitable for steel, iron, and most non-ferrous alloys. | Engine blocks, cylinder heads, crankshafts. | Ideal for complex shapes, low cost, wide material adaptability. | Lower precision, rough surface finish. |
Investment Casting | Uses wax patterns coated with refractory material, melted out to form a mold (lost-wax casting). | Turbine blades, impellers, small precision parts. | High dimensional and geometric accuracy, excellent surface finish. | Complex process, higher cost. |
Die Casting | Forces molten metal into a precision mold under high pressure. | Automotive parts, electronics, instruments. | High production efficiency, good surface quality, stable dimensions. | Prone to porosity, low plasticity, limited for high-melting-point alloys. |
Low-Pressure Casting | Fills molds under low pressure (0.02–0.06 MPa) for controlled crystallization. | Cylinder heads, wheel hubs. | High material utilization (90–98%), dense structure, suitable for thin-walled parts. | Limited to specific alloys and shapes. |
Centrifugal Casting | Pours molten metal into a rotating mold, solidifying under centrifugal force. | Pipes, cylinder liners, shafts. | High density, minimal defects, no need for cores in hollow parts. | Inaccurate inner diameters, rough internal surfaces. |
Gravity Die Casting | Fills metal molds under gravity, cooling to form castings. | Aluminum/magnesium alloy parts, steel castings. | High density, good dimensional accuracy, low environmental impact. | Requires gas venting, prone to cracking, high mold cost. |
Vacuum Die Casting | Removes gases from the mold cavity during die casting to reduce porosity. | High-quality automotive and aerospace parts. | Improved mechanical properties, better surface quality. | Complex mold sealing, higher costs. |
Squeeze Casting | Solidifies liquid or semi-solid metal under high pressure for direct part formation. | Aluminum, zinc, copper alloys. | Eliminates porosity, high precision, crack prevention. | Requires precise pressure control. |
Lost Foam Casting | Uses foam patterns vaporized by molten metal in a sand mold. | Engine blocks, complex pipe fittings. | High precision, no parting lines, clean production. | Requires precise foam pattern preparation. |
Continuous Casting | Continuously pours molten metal into a crystallizer for long castings. | Ingots, slabs, rods, tubes. | Uniform structure, high efficiency, simplified process. | Limited to consistent cross-section shapes. |
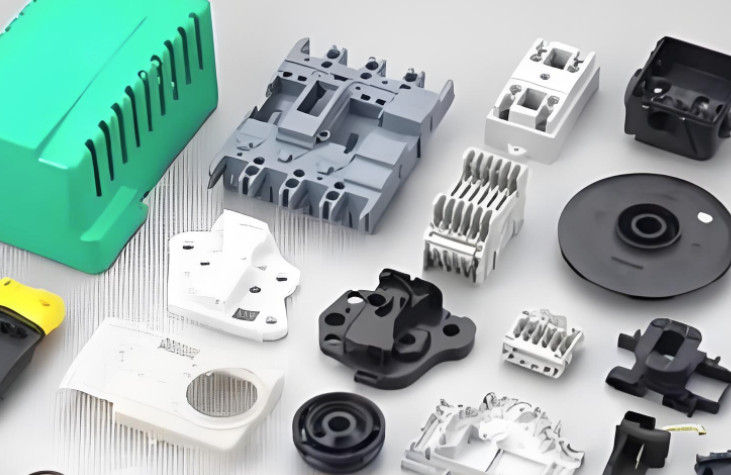
Plastic Forming
Plastic forming utilizes the plasticity of metals to shape parts under external forces, typically with minimal or no material removal. Common methods include forging, rolling, extrusion, drawing, and stamping.
Forging
Forging applies pressure via forging machines to deform metal blanks, achieving desired shapes and enhanced mechanical properties.
Workflow: Blank heating, roll forging preparation, die forging, trimming, punching, correction, heat treatment, cleaning, inspection.
Characteristics:
- Produces parts with superior strength, toughness, and impact resistance compared to castings.
- Saves material and reduces machining time.
- High production efficiency, especially in die forging.
- Free forging suits small-batch production with high flexibility.
Applications: Large rolling mill rolls, turbine rotors, crankshafts, connecting rods.
Rolling
Rolling passes metal blanks through rotating rollers to reduce cross-sectional area and increase length.
Workflow: Metal is compressed between rollers, producing profiles, plates, or tubes.
Characteristics:
- Suitable for producing profiles, sheets, and tubes in metals and some non-metals (e.g., plastics, glass).
- High throughput for continuous production.
- Types include longitudinal, transverse, and skew rolling.
Applications: Steel beams, aluminum sheets, copper tubes.
Extrusion
Extrusion forces metal through a die to reduce cross-sectional area and form elongated parts.
Workflow: Blank preparation, billet heating, extrusion, stretching/straightening, cutting, inspection, aging, packaging.
Characteristics:
- Produces a wide range of shapes with high precision and surface quality.
- Flexible for small-batch production but with significant material waste.
- Low equipment investment, suitable for automation.
Applications: Long rods, thin-walled parts, complex cross-section components.
Drawing
Drawing pulls metal through a die to reduce its diameter and achieve precise shapes.
Workflow: Metal is pulled through a die to form wires, rods, or tubes.
Characteristics:
- High dimensional accuracy and smooth surfaces.
- Simple tools, suitable for high-speed production of small cross-sections.
- Limited deformation per pass and overall length.
Applications: Metal wires, rods, tubes for industrial use.
Stamping
Stamping uses presses and dies to deform or separate sheet metal into desired shapes.
Workflow: Material is pressed or sheared to form parts.
Characteristics:
- Produces lightweight, rigid parts with uniform quality.
- High productivity, cost-effective for mass production.
- Good material utilization and recyclability.
Applications: Automotive bodies, appliance components, electrical cores.
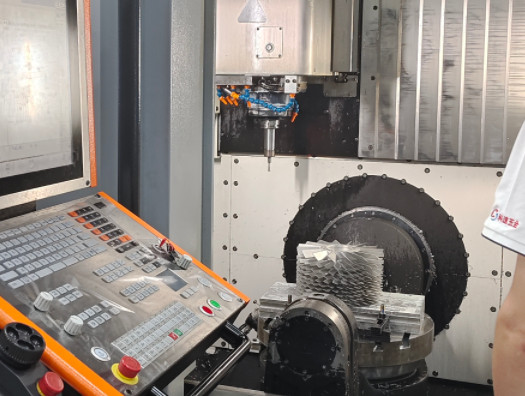
Machining
Machining removes excess material from a blank using cutting tools to achieve precise dimensions, shapes, and surface quality.
Workflow: Cutting excess metal to meet design specifications.
Characteristics:
- High precision for complex geometries.
- Applicable to various metals and alloys.
- Material waste due to removal process.
Applications: Precision parts for aerospace, automotive, and machinery industries.
Welding
Welding joins metal parts by heating, melting, or applying pressure, often with filler materials.
Workflow: Preparation, heating/pressure application, cooling, inspection.
Characteristics:
- Versatile for metals and thermoplastics.
- Strong, permanent joints.
- Requires skilled operation to avoid defects like porosity or cracks.
Applications: Shipbuilding, automotive frames, pipelines.
Powder Metallurgy
Powder metallurgy forms parts by compacting and sintering metal powders or mixtures with non-metal powders.
Workflow: Powder preparation, compaction, sintering, finishing.
Characteristics:
- Ideal for refractory metals, composites, and porous materials.
- High material efficiency, minimal waste.
- Ensures uniform composition and high purity.
- High mold costs for small batches.
Applications: Gears, bearings, cutting tools.
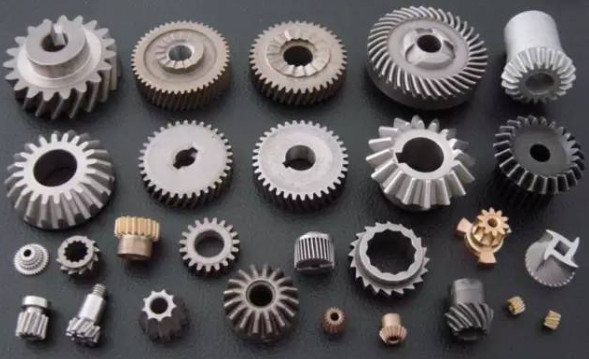
Metal Injection Molding (MIM)
MIM combines metal powders with a binder, injected into molds, followed by debinding and sintering.
Workflow: Mixing, molding, debinding, sintering, optional surface treatment.
Characteristics:
- Produces complex parts with high precision and low waste.
- High production efficiency, suitable for automation.
- Relies on binder quality for flow and shape retention.
Applications: Small, intricate parts for electronics, medical devices.
Semi-Solid Forming
Semi-solid forming uses semi-solid metal with unique flow properties to produce high-quality castings.
Workflow: Rheoforming (direct semi-solid processing) or thixoforming (pre-formed semi-solid billets).
Characteristics:
- Reduces defects like porosity and shrinkage.
- Lower molding temperatures extend mold life.
- Suitable for complex alloys unattainable by liquid casting.
Applications: Automotive pistons, aerospace components, consumer electronics.
3D Printing
3D printing, or additive manufacturing, builds parts layer-by-layer from digital models using metal powders or other materials.
Workflow: Digital modeling, material deposition, layer solidification, finishing.
Characteristics:
- High design flexibility for complex geometries.
- Minimal material waste compared to subtractive methods.
- Slower for large-scale production, high material costs.
Applications: Prototypes, aerospace components, medical implants.
Comparative Overview
Process | Material Efficiency | Precision | Complexity Handling | Production Scale |
---|---|---|---|---|
Casting | Moderate to High | Moderate | High | Small to Large |
Plastic Forming | High | High | Moderate | Medium to Large |
Machining | Low | Very High | High | Small to Medium |
Welding | High | Moderate | Low | Small to Large |
Powder Metallurgy | High | High | Moderate | Medium to Large |
Metal Injection Molding | High | Very High | High | Medium to Large |
Semi-Solid Forming</td | High | High | High | Medium |
3D Printing | High | High | Very High | Small to Medium |
Conclusion
The eight metal forming processes—casting, plastic forming, machining, welding, powder metallurgy, metal injection molding, semi-solid forming, and 3D printing—offer diverse solutions for manufacturing parts with varying complexity, precision, and scale. Selecting the appropriate process depends on factors like material type, part geometry, production volume, and cost constraints. This technical overview provides a foundation for engineers and manufacturers to make informed decisions in metal forming applications.