Aluminum machining is a critical process in manufacturing, valued for producing lightweight, durable, and precise components across industries like aerospace, automotive, and electronics. This guide provides a detailed exploration of aluminum machining, including material properties, processing techniques, and specific difficulties related to precision and complexity. The content is structured to offer technical insights for professionals seeking to optimize their machining processes.
Understanding Aluminum as a Machining Material
Aluminum is a preferred material for machining due to its unique properties, which make it versatile for various applications. Its low density, high strength-to-weight ratio, and excellent corrosion resistance are key advantages. Aluminum alloys, such as 6061, 7075, and 5083, are commonly used, each tailored to specific needs based on their mechanical properties.
Key properties of aluminum that impact machining include:
- Low Density: Aluminum has a density of approximately 2.7 g/cm³, significantly lower than steel (7.8 g/cm³), making it ideal for lightweight components.
- Corrosion Resistance: A natural oxide layer protects aluminum from environmental degradation, especially in alloys like 5083, used in marine applications.
- Thermal Conductivity: Aluminum’s high thermal conductivity (e.g., 237 W/m·K for 6061) aids heat dissipation but can complicate tool life if not managed.
- Machinability: Aluminum is softer than most metals, allowing faster cutting speeds but posing risks like chip adhesion and burr formation.
Aluminum alloys vary in composition, affecting their machinability. For example, 6061 offers good weldability and corrosion resistance, while 7075 provides higher strength for aerospace components prototyping. Selecting the appropriate alloy is critical to achieving desired outcomes in machining.
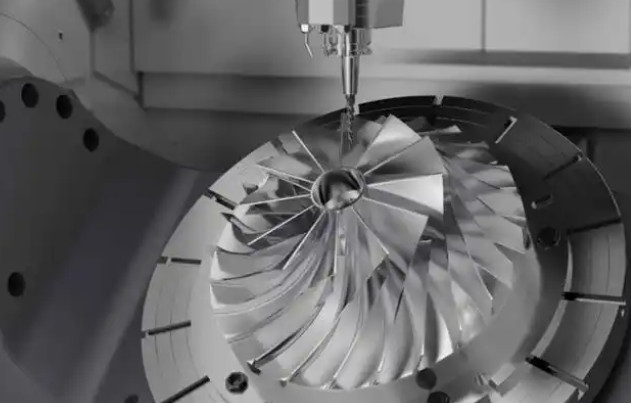
Types of Aluminum Machining Processes
Aluminum machining encompasses various techniques, each suited to specific geometries and applications. Below is a detailed overview of the primary machining processes used for aluminum, focusing on their technical aspects and parameters.
CNC Milling
CNC milling involves a rotating multi-point cutting tool that removes material from a stationary or moving aluminum workpiece. It is ideal for creating complex geometries, such as slots, grooves, and contoured surfaces. Multi-axis CNC milling machines (3-, 4-, or 5-axis) enhance precision for intricate parts.
Key Parameters:
- Cutting Speed: Typically 300–600 m/min for aluminum alloys like 6061, depending on tool material (e.g., carbide).
- Feed Rate: 0.1–0.5 mm/rev, adjusted based on tool diameter and alloy hardness.
- Depth of Cut: 0.5–2 mm for finishing, up to 5 mm for roughing.
- Tool Material: Carbide or polycrystalline diamond (PCD) tools for reduced wear and improved surface finish.
Applications: Aerospace brackets, automotive housings, and electronic enclosures.
CNC Turning
In CNC turning, the aluminum workpiece rotates while a single-point cutting tool shapes it into cylindrical parts like shafts, bushings, or rings. This process is efficient for producing symmetrical components with high precision.
Key Parameters:
- Spindle Speed: 1000–3000 RPM for aluminum, higher for softer alloys like 1000 series.
- Feed Rate: 0.05–0.3 mm/rev, balancing speed and surface quality.
- Depth of Cut: 0.2–3 mm, depending on the operation (roughing or finishing).
- Tool Geometry: Positive rake angles (e.g., 8–15°) to minimize cutting forces.
Applications: Automotive pistons, aerospace fittings, and cylindrical medical components.
CNC Drilling
CNC drilling creates precise holes in aluminum workpieces using a rotating multi-point tool. It is commonly used for fastener holes or mounting points in plates and blocks.
Key Parameters:
- Drill Speed: 1500–4000 RPM, adjusted for hole diameter and alloy type.
- Feed Rate: 0.05–0.2 mm/rev to prevent tool deflection.
- Coolant: Water-soluble or synthetic fluids to reduce heat and improve chip evacuation.
- Drill Material: High-speed steel (HSS) or carbide for durability.
Applications: Aerospace panels, automotive frames, and electronic circuit boards.
Laser Cutting
Laser cutting uses a high-powered laser beam to melt or vaporize aluminum, producing clean, precise cuts. It is suitable for thin sheets and intricate designs but less effective for thick materials.
Key Parameters:
- Laser Power: 1–4 kW, depending on material thickness (e.g., 1–6 mm).
- Cutting Speed: 1–10 m/min, slower for thicker sheets.
- Assist Gas: Nitrogen or oxygen to enhance cut quality and remove molten material.
Applications: Automotive body panels, decorative components, and thin aerospace parts.
Waterjet Cutting
Waterjet cutting employs a high-pressure stream of water mixed with abrasives to cut aluminum without generating heat, avoiding thermal distortion. It is ideal for complex shapes and thick materials.
Key Parameters:
- Water Pressure: 40,000–60,000 psi for efficient cutting.
- Abrasive Flow Rate: 0.5–1 kg/min, typically garnet.
- Cutting Speed: 0.1–1 m/min, depending on thickness (up to 150 mm).
Applications: Thick aerospace components, marine parts, and custom fabrications.
Electrical Discharge Machining (EDM)
EDM uses electrical sparks to erode aluminum, suitable for intricate shapes and hard-to-machine alloys. It is slower but offers high precision for complex geometries.
Key Parameters:
- Voltage: 50–300 V, adjusted for material removal rate.
- Pulse Duration: 1–100 µs to control precision and surface finish.
- Dielectric Fluid: Oil or deionized water to facilitate spark formation.
Applications: Precision molds, aerospace dies, and micro-components.
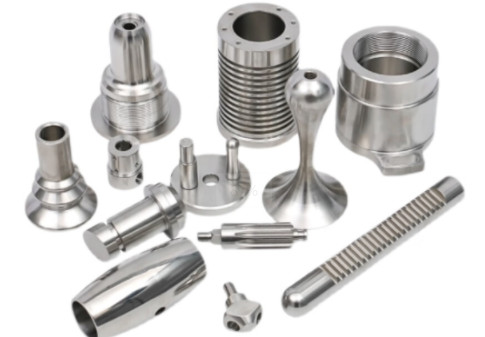
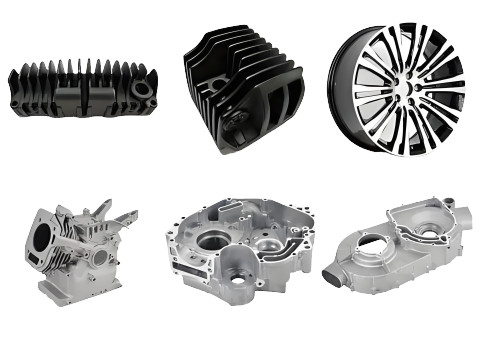
Difficulties in Aluminum Machining
While aluminum is highly machinable, specific difficulties arise due to its material properties and the complexity of desired outcomes. These challenges impact precision, tool life, and process efficiency.
Precision and Dimensional Accuracy
Achieving tight tolerances (e.g., ±0.002 mm) is critical in industries like aerospace and medical device manufacturing. Aluminum’s softness and high thermal conductivity pose challenges:
- Material Deformation: Aluminum’s low modulus of elasticity (e.g., 70 GPa for 6061) can lead to deflection under cutting forces, especially in thin-walled parts.
- Thermal Expansion: Aluminum’s thermal expansion coefficient (23.6 µm/m·K) causes dimensional changes during machining, requiring precise temperature control.
- Surface Finish: Chip adhesion and built-up edge (BUE) formation can degrade surface quality, necessitating sharp tools and effective coolants.
Solutions: Use low cutting forces, high-speed spindles, and coolant strategies to minimize heat buildup. Fixturing techniques, such as vacuum chucks, help reduce deformation.
Complexity of Geometries
Complex geometries, such as thin walls, deep pockets, or intricate contours, increase machining difficulty. Challenges include:
- Tool Accessibility: Deep or narrow features require long, slender tools, increasing the risk of vibration and tool deflection.
- Chip Evacuation: Complex shapes can trap chips, leading to tool damage or poor surface finish.
- Programming Complexity: Multi-axis CNC programming for intricate parts demands skilled operators and advanced software.
Solutions: Employ high-efficiency milling (HEM) toolpaths with low radial depth of cut (RDOC) and high axial depth of cut (ADOC). Use 3-flute end mills for better chip evacuation in complex operations.
Material-Specific Processing Issues
Aluminum’s properties create specific processing difficulties:
- Chip Adhesion: Aluminum’s stickiness can cause material to weld to the tool, increasing friction and tool wear.
- Burr Formation: Soft alloys like 1000 series are prone to burrs, requiring secondary deburring operations.
- Tool Wear: High cutting speeds, while beneficial for productivity, accelerate wear on uncoated tools.
Solutions: Use coated tools (e.g., ZrN or TiB2) to reduce adhesion. Optimize feed rates and apply lubricants like water-soluble fluids or minimum quantity lubrication (MQL) to improve chip flow.
Key Machining Parameters for Aluminum
Optimizing machining parameters is essential for efficiency and quality. The following table summarizes recommended parameters for common aluminum machining processes.
Process | Cutting Speed (m/min) | Feed Rate (mm/rev) | Depth of Cut (mm) | Tool Material |
---|---|---|---|---|
CNC Milling | 300–600 | 0.1–0.5 | 0.5–5 | Carbide, PCD |
CNC Turning | 200–500 | 0.05–0.3 | 0.2–3 | Carbide, HSS |
CNC Drilling | 150–400 | 0.05–0.2 | 0.5–10 | HSS, Carbide |
Best Practices for Aluminum Machining
To overcome difficulties and achieve optimal results, adhere to these practices:
- Tool Selection: Use sharp, coated tools (e.g., carbide with TiCN coating) to reduce adhesion and wear.
- Coolant Use: Apply water-soluble or synthetic coolants to dissipate heat and improve chip evacuation.
- Parameter Optimization: Balance cutting speed, feed rate, and depth of cut to minimize heat and tool wear while maintaining productivity.
- Workholding: Use secure fixturing to prevent workpiece vibration and deformation, especially for thin parts.
- Chip Management: Ensure effective chip removal through proper toolpath design and coolant flow to avoid tool damage.
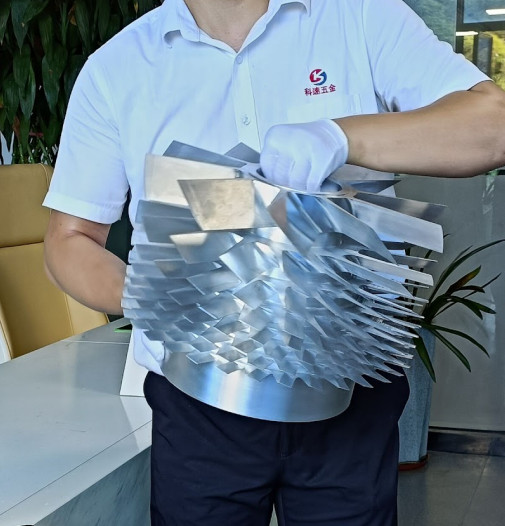
Precision Aluminum Machining by Kesu
Quality, Efficiency, Expertise. Craft complex parts with unmatched accuracy using advanced CNC technology. Partner with Kesu for reliable, high-performance solutions tailored to your industry aluminum machining needs.
Kesu is a top-notch custom aluminum parts manufacturing provider offering high-quality and precise CNC machining services. In CNC precision machining Kesu is among the top manufacturer of machine parts all over the world and in China they are the top 5 best service providers of CNC precision machining parts.
Conclusion
Aluminum machining is a versatile and efficient process, leveraging the material’s lightweight, corrosion-resistant, and machinable properties. By understanding the types of machining processes—such as CNC milling, turning, drilling, laser cutting, waterjet cutting, and EDM—and addressing difficulties like precision, complexity, and material-specific issues, manufacturers can achieve high-quality results. Optimizing parameters, selecting appropriate tools, and implementing best practices are critical to overcoming challenges and ensuring consistent performance in aluminum machining.
Aluminum Machining: Frequently Asked Questions (FAQ)
What is aluminum machining?
Aluminum machining is the process of shaping aluminum or its alloys using techniques like CNC milling, turning, drilling, laser cutting, waterjet cutting, or EDM to create precise components. It is critical in industries such as aerospace, automotive, and electronics due to aluminum’s lightweight, corrosion-resistant, and machinable properties, enabling high-performance parts with excellent strength-to-weight ratios.
Which aluminum alloys are best for machining?
Common alloys include:
6061: Balances strength, weldability, and corrosion resistance; ideal for automotive and structural parts.
7075: High strength for aerospace applications but harder to machine due to toughness.
5083: Excellent corrosion resistance for marine environments.
2024: High fatigue resistance for aerospace but prone to chip adhesion. Alloy selection depends on application requirements, such as strength, corrosion resistance, or machinability.
Why is aluminum easy to machine compared to other metals?
Aluminum is highly machinable for several reasons:
Low hardness: Most aluminum alloys (e.g., 6061, 7075) have lower hardness than steel, reducing tool wear.
High thermal conductivity: Aluminum dissipates heat quickly, preventing overheating of tools and workpieces.
Non-abrasive nature: Unlike cast iron (which contains graphite) or stainless steel (with chromium carbides), aluminum doesn’t scratch cutting tools easily.
Ductility: It chips away cleanly, reducing the risk of tool jamming or workpiece damage.
Can aluminum be machined to tight tolerances?
Yes. Aluminum’s low thermal expansion (compared to steel) and good stability allow tight tolerances:
Standard tolerances: ±0.01–0.05 mm for most operations.
Precision machining: ±0.001–0.005 mm with advanced equipment (e.g., CNC lathes with high-resolution encoders).
Alloys like 7075 and 6061 are often chosen for precision parts due to their stability after machining.
What post-machining treatments are common for aluminum?
Anodizing: Adds a protective, decorative oxide layer (improves corrosion resistance and wear).
Chromate conversion coating: Provides corrosion resistance (often a pre-treatment for painting).
Powder coating: For color and durability in consumer products.
Deburring: Removes sharp edges using tumbling, brushing, or electrochemical processes.