This guide provides a detailed overview of car light mold design, their applications in automotive lighting systems, and the machining processes involved in their production. It covers mold functionality for light guides, material selection, prototyping techniques, and the complexities of achieving high precision in mold manufacturing. The focus is on technical processes, material properties, and the difficulties associated with machining molds for headlights, taillights, fog lamps, and other automotive lighting components.
Understanding Car Light Molds
Car light molds, also known as optical molds or tooling for light guides, are precision tools used to shape components like lenses and light pipes in automotive lighting systems. These molds are critical for producing parts that transmit light from sources, typically LEDs, to specific areas of a lamp, ensuring uniform illumination or aesthetic contours. Molds are typically made from high-grade steel or aluminum to withstand repeated use and maintain dimensional accuracy.
The design of a car light mold involves specifying cavity geometry, cooling channels, and ejection mechanisms. For example, a mold for a headlight light guide may have a cavity diameter of 7–10 mm with a surface finish of Ra 0.1 μm to ensure optical clarity. Cooling channels are designed with a diameter of 8–12 mm to maintain uniform mold temperatures (80–120°C for polycarbonate). Molds must also accommodate complex trajectories to support intricate light guide designs.
Molds are essential for mass-producing consistent, high-quality car light components. They enable the creation of precise optical surfaces that meet stringent automotive standards, such as ECE R112 for headlights.
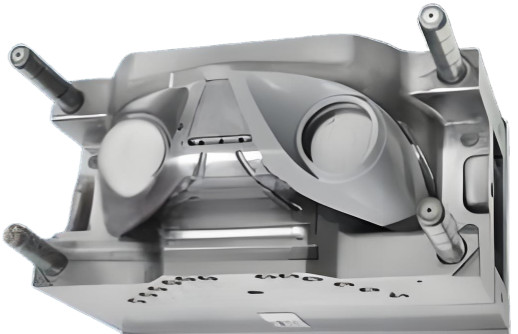
Applications of Car Light Molds in Automotive Systems
Car light molds are used to produce components for various automotive lighting systems, including headlights, taillights, fog lamps, daytime running lights (DRLs), and signal lights. Each application requires molds tailored to specific optical and mechanical requirements.
Headlight Molds create lenses and light guides that provide illumination up to 100 meters, requiring high-transparency materials like PMMA (92% light transmittance) and precise mold surfaces to minimize light scattering. Taillight Molds produce vibrant, heat-resistant components for brake and turn signals, demanding molds with durable coatings to withstand frequent thermal cycling. Fog Lamp Molds support components for low-visibility conditions, requiring robust materials and precise cavity designs to ensure thermal stability. DRL Molds focus on producing energy-efficient, durable components for enhanced visibility.
Molds for adaptive lighting systems are particularly complex, as they must accommodate dynamic light guide shapes that adjust beam direction based on vehicle movement, requiring tight tolerances and intricate cavity designs.
Machining Processes for Car Light Molds
Producing car light molds requires advanced machining processes to achieve the precision and surface quality necessary for optical components. The primary methods include CNC machining, electrical discharge machining (EDM), injection mold fabrication, and 3D printing for prototyping. Each process is suited to specific stages of mold development.
CNC Machining
Computer Numerical Control (CNC) machining is a subtractive process used to create high-precision mold cavities and cores. It employs 5-axis CNC machines to shape materials like tool steel (P20, H13) or aluminum. Key parameters include:
- Surface Finish: Ra 0.1–0.2 μm for optical-grade mold surfaces.
- Tolerance: ±0.01 mm to ensure precise part replication.
- Tool Type: Diamond-coated or carbide tools with a radius of 0.05–0.2 mm for fine details.
- Spindle Speed: 15,000–25,000 RPM to minimize vibration and tool wear.
CNC machining is ideal for prototyping and small-batch mold production, offering high accuracy for complex geometries like micro-optics or curved light guide cavities. However, it is time-intensive for large molds with intricate cooling channels.
Electrical Discharge Machining (EDM)
EDM is used to create intricate mold features, such as sharp corners or deep cavities, that are challenging for CNC machining. It uses electrical sparks to erode material, achieving high precision. Key parameters include:
- Surface Finish: Ra 0.05–0.1 μm for polished mold surfaces.
- Tolerance: ±0.005 mm for micro-features.
- Electrode Material: Copper or graphite for efficient material removal.
- Processing Time: 10–20 hours per cavity, depending on complexity.
EDM is critical for molds requiring fine details, such as textured surfaces for light diffusion, but it is slower than CNC machining for larger features.
Injection Mold Fabrication
Injection mold fabrication involves assembling precision-machined components (cavities, cores, and inserts) into a complete mold for mass production. Molten materials like polycarbonate or PMMA are injected into the mold at pressures of 100–150 MPa. Key parameters include:
- Mold Material: H13 steel for durability (up to 500,000 cycles) or aluminum for shorter runs (~10,000 cycles).
- Cooling Time: 20–40 seconds per cycle to prevent warping.
- Tolerance: ±0.02 mm for consistent part production.
This process is cost-effective for high-volume production but requires significant investment in mold design, often costing $50,000–$150,000 per mold.
3D Printing for Mold Prototyping
3D printing, particularly stereolithography (SLA), is used for rapid prototyping of mold inserts or temporary molds. It employs photopolymer resins to create detailed prototypes. Key parameters include:
- Layer Thickness: 25–50 μm for smooth surfaces.
- Material: High-temperature resins to withstand low-volume injection molding.
- Build Time: 12–24 hours for a single mold insert.
3D printing is ideal for early-stage mold design validation but is not suitable for production molds due to limited material durability.
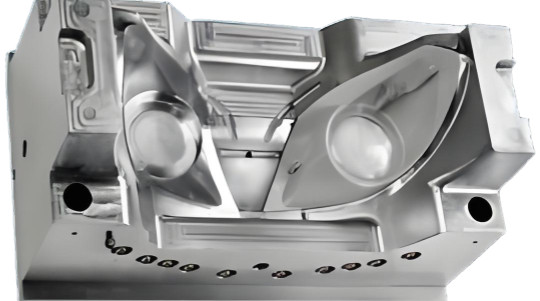
Materials for Car Light Molds
The choice of mold materials depends on production volume, cost, and optical requirements. The following table summarizes common mold materials and their properties:
Material | Hardness (HRC) | Thermal Conductivity (W/m·K) | Durability (Cycles) | Applications |
---|---|---|---|---|
P20 Steel | 28–32 | 34 | 100,000–300,000 | Medium-volume molds |
H13 Steel | 38–42 | 28 | 500,000+ | High-volume molds |
Aluminum | ~15 | 150 | 5,000–10,000 | Prototyping, low-volume molds |
H13 steel is preferred for high-volume production due to its durability, while aluminum is used for prototyping or short-run molds due to its lower cost and faster machining.
Prototyping Techniques for Car Light Molds
Prototyping is essential for validating mold designs before full-scale production. Common techniques include:
- CNC Machining: Produces high-precision mold inserts for testing cavity designs and optical performance.
- EDM: Creates prototype molds with intricate features, such as micro-textures for light diffusion.
- 3D Printing: Enables rapid iteration of mold inserts, suitable for testing cooling channel layouts or part ejection.
Prototypes are tested for dimensional accuracy, surface finish, and thermal performance under conditions simulating production (e.g., 100–150 MPa injection pressure and 80–120°C mold temperature).
Difficulties in Machining Car Light Molds
Machining car light molds presents several challenges due to the high precision and complexity required. Key difficulties include:
- Precision Requirements: Molds require tolerances of ±0.01 mm to ensure accurate part replication, particularly for optical surfaces that prevent light scattering.
- Surface Complexity: Freeform surfaces and micro-optics demand advanced machining techniques like 5-axis CNC or EDM, increasing production time.
- Material Hardness: Tool steels like H13 are difficult to machine, requiring specialized tools and slower cutting speeds to avoid wear.
- Thermal Management: Cooling channels must be precisely positioned to prevent defects like warping or sink marks, complicating mold design.
- Mold Polishing: Achieving a mirror-like finish (Ra 0.05–0.1 μm) for optical clarity is labor-intensive and requires skilled craftsmanship.
These challenges necessitate careful process planning, such as using diamond-coated tools for CNC machining or optimizing EDM parameters for fine details.
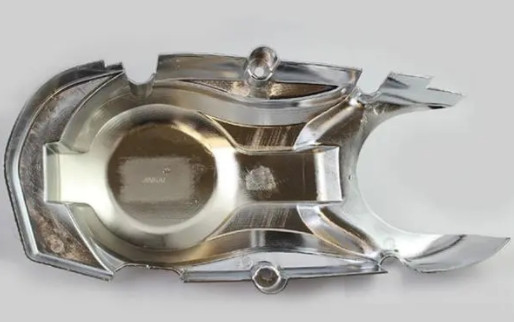
Comparison of Mold Machining Processes
The following table compares the key machining processes for car light molds:
Process | Precision (Tolerance) | Production Volume | Cost per Mold | Applications |
---|---|---|---|---|
CNC Machining | ±0.01 mm | Low (1–10 molds) | High ($10,000–$50,000) | Prototyping, mold inserts |
EDM | ±0.005 mm | Low (1–5 molds) | High ($5,000–$20,000) | Intricate mold features |
Injection Mold Fabrication | ±0.02 mm | High (100+ molds) | High ($50,000–$150,000) | Mass production |
3D Printing | ±0.1 mm | Low (1–10 molds) | Moderate ($1,000–$5,000) | Prototyping |
This comparison highlights the trade-offs between precision, cost, and production scale, guiding manufacturers in selecting the appropriate process.
Conclusion
Car light molds are critical for producing high-quality automotive lighting components, such as lenses and light guides for headlights, taillights, and fog lamps. Materials like H13 steel and aluminum are chosen for their durability and thermal properties, while processes like CNC machining, EDM, injection mold fabrication, and 3D printing cater to different stages of mold production. Despite challenges like precision requirements and surface complexity, these techniques enable the creation of molds that meet stringent automotive standards. By understanding mold design, applications, and machining difficulties, manufacturers can optimize processes for reliable, high-performance car light production.
FAQ: Car Light Molds – Design, Applications & Machining
What are car light molds, and why are they important?
Car light molds are precision tools used to shape optical components (e.g., lenses, light guides) for automotive lighting systems (headlights, taillights, etc.). They are critical because they ensure consistent production of parts with tight tolerances, optical clarity, and durability, meeting strict automotive standards (e.g., ECE R112 for headlights). Molds maintain dimensional accuracy even after repeated use, enabling mass production of high-quality lighting components.
What are the main challenges in machining car light molds?
Tight Tolerances: Molds require ±0.01 mm precision to avoid light scattering in optical components.
Surface Complexity: Freeform shapes and micro-optics demand advanced techniques like 5-axis CNC or EDM, increasing production time.
Material Hardness: Hard tool steels (e.g., H13) require specialized tools and slow cutting speeds to prevent wear.
Thermal Management: Cooling channels must be precisely designed to avoid defects like warping, adding complexity to mold layouts.
Polishing: Achieving mirror-like finishes (Ra 0.05–0.1 μm) for optical clarity is labor-intensive and requires skilled craftsmanship.
How much does a car light mold cost?
Costs vary by process and complexity:
CNC Machined Prototypes: $10,000–$50,000 (low-volume, high precision).
EDM for Intricate Features: $5,000–$20,000 (specialized for fine details).
Production Injection Molds: $50,000–$150,000 (high-volume, durable designs).
How do car light molds differ for different lighting systems (e.g., headlights vs. taillights)?
Headlight Molds: Produce high-transparency components (e.g., PMMA with 92% light transmittance) to support illumination up to 100 meters, requiring ultra-smooth surfaces to minimize light scattering.
Taillight Molds: Focus on heat resistance to withstand thermal cycling from brake/turn signals, often using durable coatings.
Adaptive Lighting Molds: Accommodate dynamic, shape-shifting light guides (adjusting beam direction based on vehicle movement), requiring intricate cavity designs and tight tolerances.