Carbon steel, an alloy of iron and carbon (0.05% to 2.1% carbon), is widely used in manufacturing due to its strength, versatility, and cost-effectiveness. Machining carbon steel involves cutting, shaping, and finishing to produce precise components. Its properties, such as hardness and toughness, vary with carbon content and alloying elements, impacting machinability. This guide details the machining process, types of carbon steel, specific parameters, and key difficulties encountered during machining.
Understanding Carbon Steel for Machining
Carbon steel’s machinability depends on its composition and microstructure. Carbon content primarily dictates hardness, strength, and ductility, while alloying elements like manganese, sulfur, or phosphorus influence cutting behavior. Machining requires selecting appropriate tools, speeds, and feeds based on the steel’s grade and condition (annealed, normalized, or hardened).
Key factors affecting machining include:
- Carbon Content: Low-carbon steels (0.05%–0.3%) are softer and easier to machine but prone to gummy chip formation. Medium-carbon (0.3%–0.6%) and high-carbon (0.6%–2.1%) steels are harder, increasing tool wear.
- Microstructure: Ferritic, pearlitic, or martensitic structures impact cutting resistance and surface finish.
- Alloying Elements: Sulfur improves machinability by forming soft inclusions, while phosphorus can embrittle the material.
- Heat Treatment: Annealed steel machines better than hardened steel, which requires robust tools.
Proper material selection and preparation, such as normalizing to refine grain structure, optimize machining outcomes.
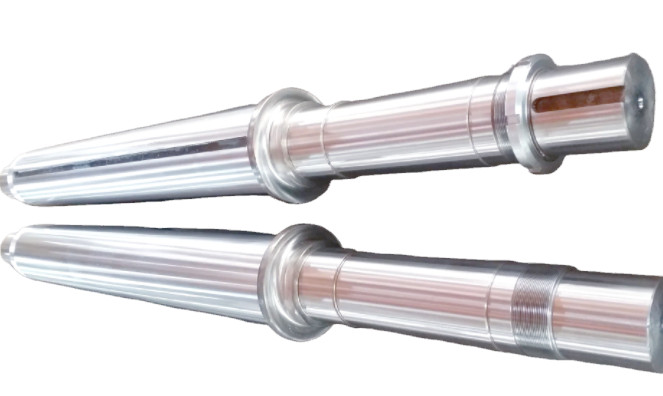
Types of Carbon Steel for Machining
Carbon steels are categorized by carbon content, each with distinct machining characteristics. Below is a breakdown of the main types, their properties, and machining considerations.
Type | Carbon Content | Properties | Machining Considerations |
---|---|---|---|
Low-Carbon Steel | 0.05%–0.3% | Soft, ductile, low strength | Easy to machine; prone to built-up edge (BUE) and stringy chips; use high speeds and light cuts. |
Medium-Carbon Steel | 0.3%–0.6% | Moderate strength, good toughness | Balanced machinability; requires sharp tools and moderate speeds to avoid excessive tool wear. |
High-Carbon Steel | 0.6%–2.1% | High strength, very hard | Difficult to machine; high tool wear; use low speeds, heavy feeds, and carbide or ceramic tools. |
Free-Machining Steel | 0.05%–0.3% (with sulfur/lead) | Enhanced machinability | Excellent for high-speed machining; sulfur/lead reduces chip adhesion; use standard tools. |
Machining Processes for Carbon Steel
Common machining processes for carbon steel include turning, milling, drilling, and grinding. Each process requires specific parameters to achieve precision and efficiency.
Turning
Turning involves rotating the workpiece against a cutting tool to remove material. For carbon steel:
- Tool Material: High-speed steel (HSS) for low-carbon steel; carbide or coated carbide for medium/high-carbon steel.
- Cutting Speed: 90–150 m/min for low-carbon steel; 60–90 m/min for medium-carbon; 30–60 m/min for high-carbon.
- Feed Rate: 0.1–0.3 mm/rev for low-carbon; 0.08–0.2 mm/rev for medium/high-carbon.
- Depth of Cut: 0.5–3 mm, depending on steel hardness and tool rigidity.
- Coolant: Use water-based or oil-based coolant to reduce heat and improve surface finish.
Low-carbon steels may form long, stringy chips, requiring chip breakers. High-carbon steels demand rigid setups to counter increased cutting forces.
Milling
Milling uses rotating multi-point tools to remove material. Parameters vary by steel type:
- Tool Material: Carbide or coated carbide for durability; HSS for less demanding applications.
- Cutting Speed: 100–200 m/min for low-carbon; 70–120 m/min for medium-carbon; 40–80 m/min for high-carbon.
- Feed per Tooth: 0.05–0.15 mm/tooth for low-carbon; 0.03–0.1 mm/tooth for harder grades.
- Depth of Cut: 1–5 mm for roughing; 0.2–1 mm for finishing.
- Coolant: Flood coolant for heat dissipation; dry machining possible for free-machining steels.
Climb milling is preferred for better surface finish, but conventional milling may reduce tool chatter in harder steels.
Drilling
Drilling creates holes using twist drills or specialized tools. Considerations include:
- Tool Material: HSS with cobalt for low/medium-carbon; carbide for high-carbon.
- Cutting Speed: 20–40 m/min for low-carbon; 15–25 m/min for medium/high-carbon.
- Feed Rate: 0.05–0.2 mm/rev, adjusted for drill diameter and steel hardness.
- Coolant: High-pressure coolant to clear chips and reduce heat in deep holes.
Peck drilling is recommended for deep holes to prevent chip clogging and tool breakage.
Grinding
Grinding achieves tight tolerances and smooth surfaces, often used for hardened high-carbon steels.
- Wheel Type: Aluminum oxide for general use; cubic boron nitride (CBN) for high-carbon steels.
- Wheel Speed: 20–30 m/s for aluminum oxide; 40–60 m/s for CBN.
- Feed Rate: 0.01–0.05 mm/pass for finishing; 0.1–0.3 mm/pass for roughing.
- Coolant: Essential to prevent burning and maintain wheel integrity.
Grinding requires precise wheel dressing to maintain accuracy and avoid thermal damage.
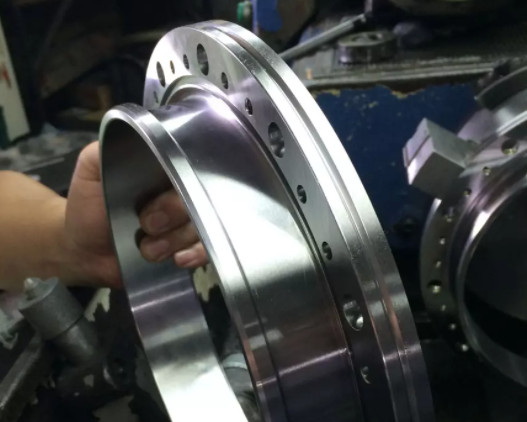
Key Difficulties in Carbon Steel Machining
Machining carbon steel presents several difficulties, particularly with higher carbon content or improper setup. Below are the primary issues and mitigation strategies.
Tool Wear and Failure
High-carbon steels are abrasive, causing rapid tool wear, especially with HSS tools. Carbide tools with coatings like TiN or TiAlN extend tool life. Parameters must balance cutting speed and feed to minimize wear while maintaining productivity.
Built-Up Edge (BUE)
Low-carbon steels tend to form BUE, where material adheres to the tool, degrading surface finish and causing tool breakage. Using sharp tools, higher cutting speeds, and effective coolant reduces BUE formation.
Chip Formation
Low-carbon steels produce long, stringy chips that can entangle machinery, while high-carbon steels form short, brittle chips. Chip breakers and optimized feed rates help manage chip flow. For deep drilling, peck cycles clear chips effectively.
Heat Generation
High cutting speeds or hard steels generate significant heat, leading to thermal expansion, tool softening, or workpiece distortion. Coolants, lower speeds, and heat-resistant tools (e.g., carbide) mitigate these issues.
Surface Finish Quality
Achieving a smooth surface on high-carbon steels is challenging due to hardness and tool vibration. Finishing passes with low feed rates, sharp tools, and vibration-dampening setups improve results. Typical surface roughness targets are Ra 0.8–3.2 µm for general machining and Ra 0.2–0.8 µm for precision work.
Machine Rigidity and Vibration
Harder steels require rigid machine setups to prevent chatter, which affects dimensional accuracy and tool life. High-torque machines, secure fixturing, and balanced tools minimize vibration.
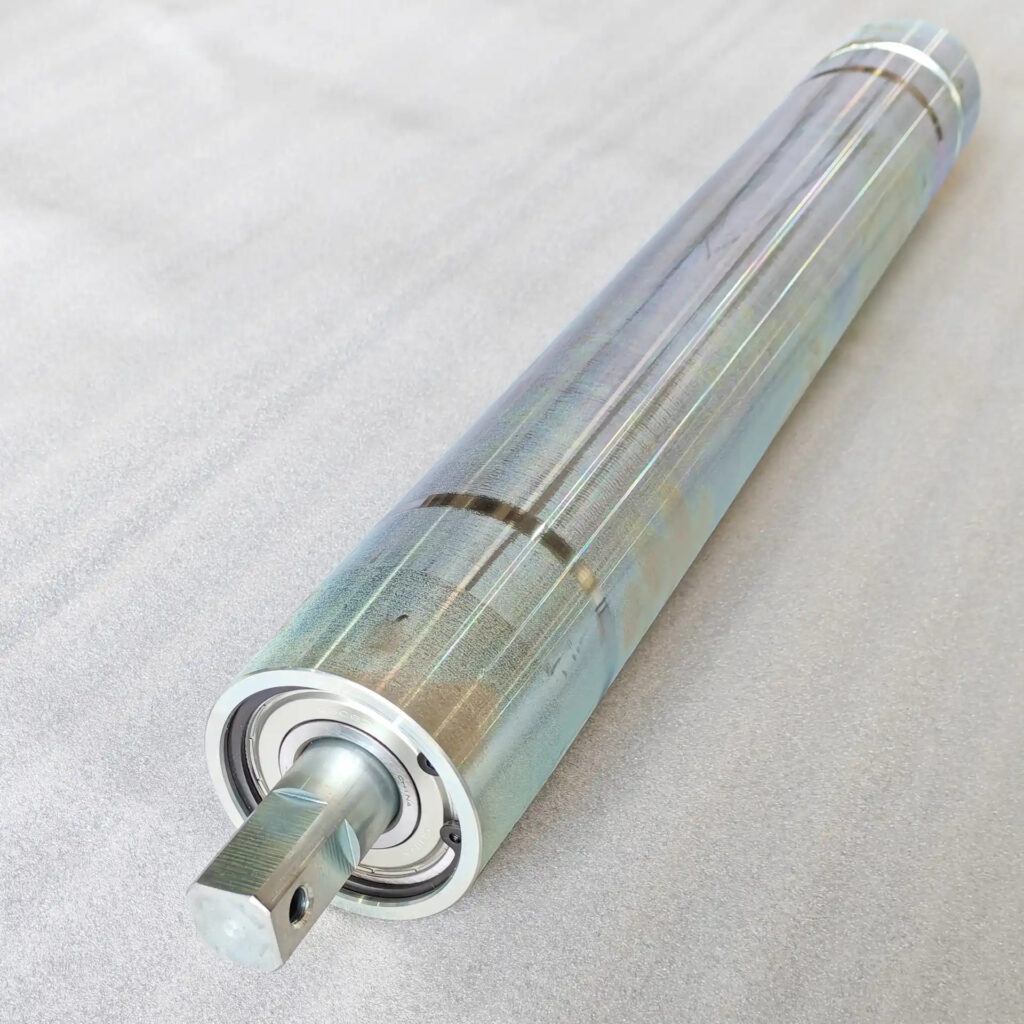
Recommended Machining Parameters
Precise parameters depend on the steel grade, tool material, and machining process. The table below provides general guidelines for turning and milling.
Process | Steel Type | Cutting Speed (m/min) | Feed Rate | Depth of Cut (mm) |
---|---|---|---|---|
Turning | Low-Carbon | 90–150 | 0.1–0.3 mm/rev | 0.5–3 |
Turning | Medium-Carbon | 60–90 | 0.08–0.2 mm/rev | 0.5–2.5 |
Turning | High-Carbon | 30–60 | 0.08–0.15 mm/rev | 0.3–2 |
Milling | Low-Carbon | 100–200 | 0.05–0.15 mm/tooth | 1–5 |
Milling | Medium-Carbon | 70–120 | 0.03–0.1 mm/tooth | 1–4 |
Milling | High-Carbon | 40–80 | 0.03–0.08 mm/tooth | 0.5–3 |
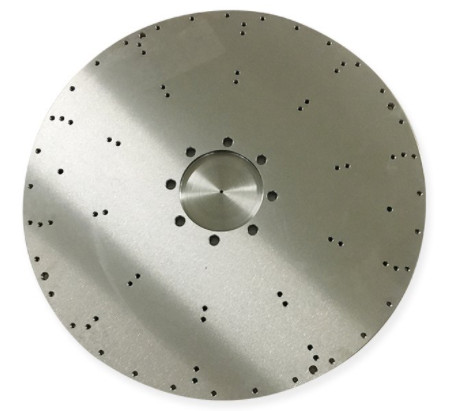
Best Practices for Effective Machining
To optimize carbon steel machining, consider the following:
- Tool Selection: Use carbide or coated tools for high-carbon steels; HSS for low-carbon or free-machining steels.
- Parameter Optimization: Adjust speeds and feeds based on steel hardness and tool life requirements.
- Coolant Use: Apply appropriate coolants to manage heat and chip evacuation, especially in drilling and grinding.
- Machine Maintenance: Ensure machine rigidity and regular tool inspection to prevent defects.
- Workpiece Preparation: Normalize or anneal high-carbon steels to improve machinability before processing.
By addressing material properties, selecting suitable tools, and optimizing parameters, manufacturers can achieve high-quality results while minimizing difficulties.
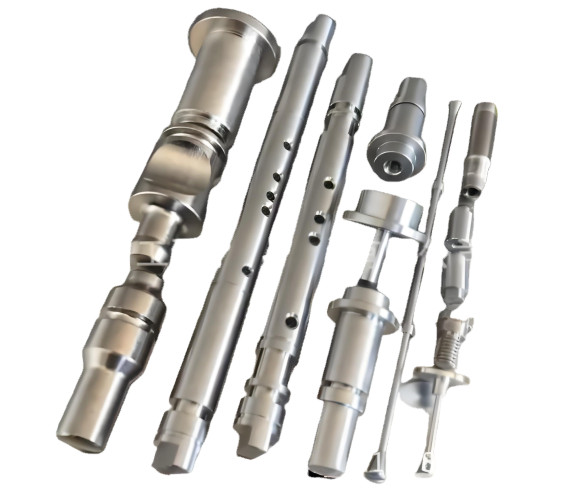