Complex machining involves advanced manufacturing processes to produce intricate components with high precision. It integrates sophisticated equipment, skilled expertise, and meticulous planning to meet stringent specifications across industries like aerospace, automotive, and medical device manufacturing. This guide explores the framework of complex machining, details various machining types, and addresses key difficulties, including material challenges and precision requirements.
Understanding Complex Machining
Complex machining refers to the production of parts with intricate geometries, tight tolerances, or challenging materials using advanced tools and techniques. It often employs computer numerical control (CNC) systems, multi-axis machines, and specialized software to achieve consistent results. The process is critical for components requiring high accuracy, such as turbine blades, orthopedic implants, or precision gears.
A typical complex machining workflow includes:
- Design and Prototyping: Engineers create detailed CAD models, often using software like SolidWorks or AutoCAD. Prototypes are produced to validate designs before full-scale production.
- Toolpath Programming: CAM software generates toolpaths for CNC machines, optimizing cutting strategies for efficiency and precision.
- Machining Execution: Machines execute programmed instructions, often on multi-axis systems capable of simultaneous movements.
- Quality Control: Inspections using coordinate measuring machines (CMM) or laser scanners ensure parts meet tolerances, typically within ±0.001 mm for high-precision applications.
Prototyping is a cornerstone of complex machining. It allows engineers to test form, fit, and function, identifying issues early. For example, a prototype aerospace component may undergo stress testing to ensure it withstands operational loads, reducing costly revisions during production.
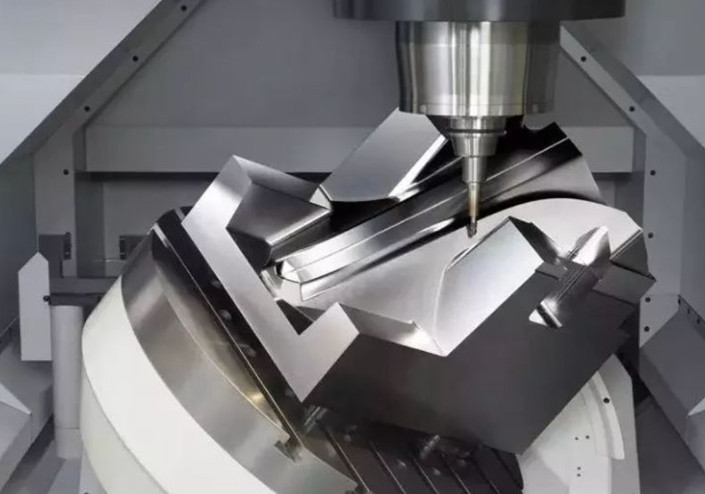
Types of Complex Machining
Complex machining encompasses various techniques, each suited to specific applications, materials, and geometries. Below are the primary types, with detailed explanations of their processes, capabilities, and use cases.
CNC Milling
CNC milling uses rotating tools to remove material from a workpiece, producing complex shapes like slots, pockets, and contours. Modern CNC mills often feature 3 to 5 axes, enabling simultaneous multi-angle cutting. For instance, 5-axis milling can produce a turbine blade with a single setup, reducing errors and time.
Key Parameters:
- Spindle Speed: 10,000–40,000 RPM, depending on material and tool.
- Tolerance: ±0.005 mm for high-precision applications.
- Materials: Aluminum, stainless steel, titanium, and engineering plastics.
Applications: Aerospace components, automotive molds, and intricate medical device parts.
CNC Turning
CNC turning rotates the workpiece against a stationary cutting tool, ideal for cylindrical parts like shafts or bushings. Advanced CNC lathes incorporate live tooling, allowing milling operations during turning, which enhances complexity without additional setups.
Key Parameters:
- Spindle Speed: 1,000–6,000 RPM.
- Tolerance: ±0.002 mm for precision turning.
- Materials: Steel, brass, copper, and composites.
Applications: Engine components, hydraulic fittings, and orthopedic screws.
Electrical Discharge Machining (EDM)
EDM uses electrical sparks to erode material, suitable for hard metals or intricate shapes unachievable with conventional cutting. Wire EDM and sinker EDM are common variants, with wire EDM cutting fine details using a thin wire as an electrode.
Key Parameters:
- Surface Finish: Ra 0.1–0.8 µm.
- Tolerance: ±0.001 mm for wire EDM.
- Materials: Tool steel, carbide, and titanium alloys.
Applications: Mold and die production, aerospace fasteners, and micro-components.
Laser Cutting and Machining
Laser machining uses focused beams to cut or engrave materials with high precision. It excels in thin materials and intricate patterns, often used for sheet metal or micro-machining applications.
Key Parameters:
- Laser Power: 500 W–10 kW, depending on material thickness.
- Cutting Speed: 0.5–20 m/min.
- Materials: Stainless steel, aluminum, and non-metals like ceramics.
Applications: Medical stents, electronic enclosures, and decorative components.
Additive-Assisted Machining
This hybrid approach combines additive manufacturing (3D printing) with subtractive machining. For example, a part may be 3D-printed to near-net shape, then machined to achieve tight tolerances. This reduces material waste and machining time for complex geometries.
Key Parameters:
- Tolerance: ±0.01 mm post-machining.
- Materials: Titanium, Inconel, and polymer composites.
Applications: Custom aerospace parts, medical implants, and rapid prototyping.
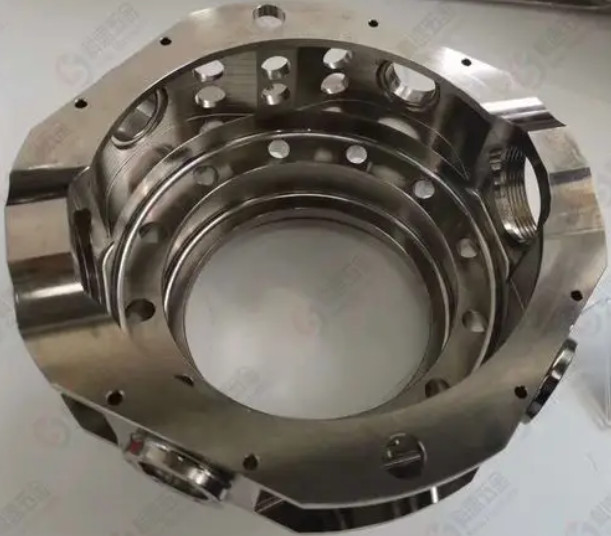
Difficulties in Complex Machining
Complex machining presents several operational challenges that impact efficiency, cost, and quality. Addressing these requires advanced equipment, skilled operators, and robust process planning. Below are the primary difficulties, with a focus on materials and precision.
Material Challenges
Machining difficult materials like titanium, Inconel, or ceramics poses significant hurdles due to their properties. These materials are often hard, heat-resistant, or brittle, leading to tool wear, thermal deformation, or surface defects.
Specific Issues:
- Titanium Alloys: Low thermal conductivity causes heat buildup, accelerating tool wear. Cutting speeds are typically limited to 30–60 m/min to prevent tool failure.
- Inconel: High strength and work-hardening tendencies require specialized carbide tools and cooling systems. Machining Inconel can take 2–3 times longer than steel.
- Ceramics: Brittle nature risks cracking during machining. Diamond-coated tools and low feed rates (0.01–0.05 mm/rev) are often necessary.
Solutions: Use of high-pressure coolant systems, cryogenic machining, or coated tools can mitigate these issues. For example, polycrystalline diamond (PCD) tools improve tool life by 10–20% when machining ceramics.
Precision and Tolerance Requirements
Achieving tight tolerances, often ±0.001 mm, is critical in complex machining but challenging due to machine limitations, thermal expansion, and tool deflection.
Specific Issues:
- Machine Accuracy: Older CNC machines may struggle to maintain tolerances below ±0.005 mm due to spindle runout or axis misalignment.
- Thermal Expansion: Temperature fluctuations in the workshop can cause dimensional variations. For example, a 1°C change can expand a 100 mm steel part by 1.2 µm.
- Tool Deflection: High cutting forces in hard materials can deflect tools, reducing accuracy. For instance, a 0.1 mm deflection can ruin a part requiring ±0.01 mm tolerance.
Solutions: Advanced CNC machines with linear scales, temperature-controlled environments, and in-process gauging systems improve precision. For example, laser interferometry can calibrate machines to within ±0.0005 mm.
Tool Wear and Maintenance
Complex machining often involves high-speed or heavy-duty cutting, accelerating tool wear. Worn tools lead to poor surface finish, dimensional errors, and increased costs.
Key Parameters:
Material | Tool Type | Typical Tool Life (min) |
---|---|---|
Aluminum | Carbide | 120–180 |
Titanium | Coated Carbide | 30–60 |
Inconel | Ceramic | 15–30 |
Solutions: Tool condition monitoring systems and predictive maintenance schedules can extend tool life. For example, vibration sensors can detect early signs of wear, reducing downtime by 15–20%.
Setup and Programming Complexity
Multi-axis machining and intricate geometries require complex setups and programming. Errors in toolpath generation or fixturing can lead to scrapped parts or machine damage.
Specific Issues:
- Multi-Axis Coordination: 5-axis machines require precise synchronization of movements, increasing programming time by 30–50% compared to 3-axis systems.
- Fixturing: Custom fixtures for irregular shapes can take hours to design and set up, increasing lead times.
Solutions: Simulation software like Vericut can verify toolpaths before machining, reducing errors. Modular fixturing systems also streamline setups, cutting preparation time by up to 25%.
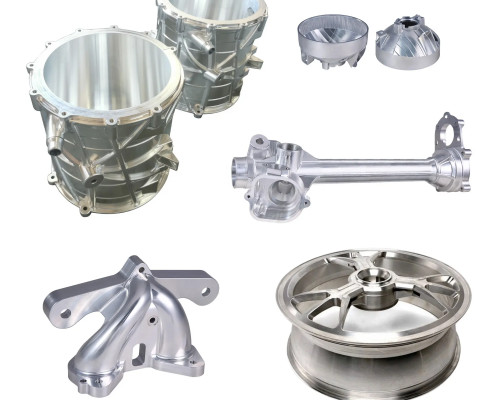
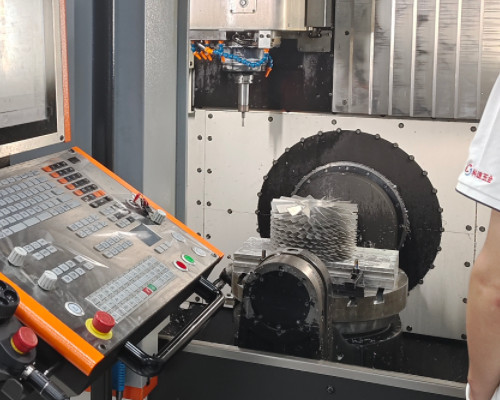
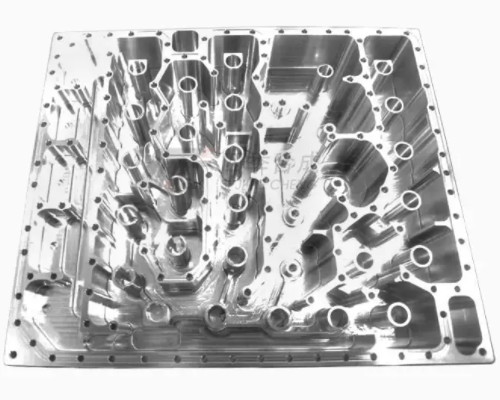
Best Practices for Complex Machining
To overcome difficulties and optimize complex machining, manufacturers can adopt the following strategies:
Practice | Description | Benefit |
---|---|---|
Tool Selection | Use material-specific tools (e.g., PCD for ceramics). | Extends tool life by 10–20%. |
Process Optimization | Optimize feed rates and cutting speeds via CAM software. | Reduces cycle time by 15–30%. |
Quality Assurance | Implement in-process inspection with CMM or laser scanners. | Ensures tolerances within ±0.001 mm. |
Additionally, investing in operator training and advanced software integration ensures consistent results. For example, real-time monitoring systems can reduce scrap rates by 10–15%.
Conclusion
Complex machining is a cornerstone of modern manufacturing, enabling the production of high-precision components across critical industries. By understanding its types—such as CNC milling, turning, EDM, laser machining, and additive-assisted methods—and addressing difficulties like material challenges, precision demands, and tool wear, manufacturers can achieve reliable outcomes. Adopting best practices, including optimized tool selection and quality assurance, further enhances efficiency and quality, ensuring complex machining meets the needs of demanding applications.
FAQ: Complex Machining
What is complex machining?
Complex machining refers to advanced manufacturing processes used to produce intricate, high-precision components with complex geometries, tight tolerances, or unique material requirements. It often involves multi-axis machining (e.g., 5-axis), specialized tools, and computer-aided manufacturing (CAM) software to handle designs that standard machining (e.g., 3-axis milling) cannot efficiently produce. Examples include aerospace turbine blades, medical implants, and automotive engine parts.
What are the key technologies used in complex machining?
Multi-axis machines: 4-axis, 5-axis, or more, allowing tools to move along multiple axes simultaneously for complex shapes.
CNC (Computer Numerical Control) systems: Automate machining processes with pre-programmed instructions for precision and repeatability.
CAM software: Translates 3D CAD models into machine-readable code, optimizing tool paths to avoid collisions and reduce cycle times.
Specialized cutting tools: Carbide, ceramic, or diamond-coated tools designed for hard materials (e.g., titanium, Inconel) or fine detailing.
Metrology tools: Laser scanners, coordinate measuring machines (CMMs), and 3D inspection systems to verify tolerances (often as tight as ±0.0001 inches).
How do I choose a complex machining service provider?
Look for providers with:
Experience in your industry (e.g., aerospace certifications like AS9100).
Advanced equipment (5-axis machines, in-house metrology tools).
Skilled programmers and machinists familiar with your materials.
A track record of meeting tight deadlines and tolerances.
Transparent communication (e.g., sharing tool path simulations or inspection reports).