Copper is a highly versatile metal valued for its excellent electrical and thermal conductivity, corrosion resistance, and malleability. This guide explores copper’s properties, its wide-ranging applications, and the intricacies of machining copper, with a focus on precision, complexity, and processing difficulties. The following sections provide a detailed, technical overview of copper as a material, its practical uses, and the machining techniques employed to achieve high-quality components.
Copper Material Properties
Copper’s unique properties make it a preferred material in various industries. Its physical and chemical characteristics influence its machinability and suitability for specific applications. Below are the key properties of copper:
- Electrical Conductivity: Copper ranks second only to silver in electrical conductivity, with a conductivity of approximately 5.96 × 10⁷ S/m at 20°C, making it ideal for electrical components.
- Thermal Conductivity: With a thermal conductivity of about 401 W/(m·K), copper is highly effective for heat dissipation in applications like heat exchangers.
- Corrosion Resistance: Copper resists corrosion in most environments, particularly in air and water, due to the formation of a protective oxide layer.
- Malleability and Ductility: Copper is soft and highly ductile, allowing it to be shaped into complex forms, but this can complicate machining due to its tendency to deform.
- Density: Copper has a density of 8.93 g/cm³, which is relatively high compared to alloys like brass or bronze, affecting machining considerations.
- Non-Magnetic: Copper’s non-magnetic nature makes it suitable for applications in sensitive electronic environments.
These properties are critical when selecting copper grades for specific applications. Common grades include C101 (99.99% pure copper) for high-conductivity applications and C110 (electrolytic tough pitch copper) for better machinability.
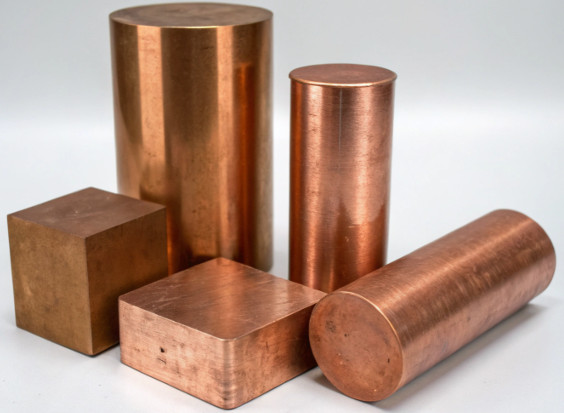
Applications of Copper
Copper’s versatility enables its use across multiple industries. Its electrical and thermal conductivity, combined with corrosion resistance, makes it indispensable in both functional and decorative applications. Below are key applications of copper:
- Electronics and Electrical Components: Copper is used in circuit boards, connectors, busbars, and wiring due to its superior electrical conductivity. For example, C110 copper is commonly used for busbars in power distribution systems.
- Heat Exchangers and Cooling Systems: Copper’s thermal conductivity makes it ideal for heat sinks, radiators, and cooling coils in automotive and aerospace industries.
- Plumbing and HVAC Systems: Copper’s corrosion resistance and formability make it a standard material for pipes, fittings, and valves in plumbing and heating systems.
- Medical Devices: Copper’s antibacterial properties and malleability allow for the production of precise components like surgical tools and medical equipment housings.
- Architectural and Decorative Uses: Copper’s aesthetic appeal and durability are leveraged in roofing, cladding, and ornamental fixtures.
- Industrial Components: Copper is used in bearings, gears, and welding nozzles due to its durability and wear resistance in specific alloys.
Each application requires careful consideration of copper’s grade and form (pure copper or alloy) to balance performance and cost.
Copper Machining Techniques
Machining copper is a critical process in manufacturing precision components. Copper’s softness, high ductility, and thermal conductivity present unique machining considerations. This section details the primary machining techniques, focusing on precision, complexity, and processing difficulties.
CNC Milling
CNC milling uses multi-point rotary cutting tools to remove material from a copper workpiece. The process is versatile, capable of creating grooves, slots, pockets, and complex contours. Key parameters for milling copper include:
- Cutting Speed: For pure copper, a cutting speed of 600–1000 m/min is recommended with carbide tools, while brass requires 2000–4000 fpm. Reduce speed by 15% for carbide tools or 20% for high-speed steel (HSS) when milling cast copper alloys with a cast skin.
- Feed Rate: A feed rate of 0.05–0.15 mm/tooth ensures precision while minimizing tool wear. High feed rates can increase temperatures, affecting surface finish.
- Tool Material: Carbide tools are preferred for their hardness and wear resistance, while HSS is suitable for less demanding applications.
Milling copper requires careful control to prevent burr formation and ensure tight tolerances, typically within ±0.0005 inches for high-precision parts.
CNC Turning
CNC turning involves rotating the copper workpiece against a stationary cutting tool to produce cylindrical components. This method is ideal for parts like connectors and fittings. Key considerations include:
- Spindle Speed: Speeds of 1000–3000 RPM are common for copper, adjusted based on workpiece diameter and tool material.
- Coolant Use: Water-based coolants or jet cooling methods prevent overheating, which can cause deformation in copper’s soft structure.
- Tool Geometry: A small tool nose radius (e.g., 0.4–0.8 mm) reduces roughness and improves surface quality.
Turning is cost-effective for producing symmetrical parts but requires precise control to avoid work hardening, where copper becomes brittle due to excessive deformation.
Drilling
Drilling creates precise holes in copper components, essential for fasteners or fluid passages. Parameters include:
- Drill Bit Material: Carbide or HSS drill bits are used, with carbide preferred for high-volume production due to its durability.
- Feed Rate: A feed rate of 0.05–0.2 mm/rev prevents excessive heat buildup and tool wear.
- Coolant: Continuous coolant application is critical to dissipate heat and remove chips, preventing clogging.
Drilling copper can be challenging due to chip entanglement, requiring optimized feed rates and peck drilling for deep holes.
Electrical Discharge Machining (EDM)
EDM uses electrical sparks to shape copper, ideal for complex geometries and hard copper alloys. Key parameters include:
- Voltage: Typically 50–300 V, depending on the alloy and desired precision.
- Pulse Duration: Short pulses (1–10 µs) ensure high precision for intricate designs.
- Dielectric Fluid: Deionized water or oil prevents arcing and removes debris.
EDM is slower than milling or turning but excels in producing intricate shapes with tolerances as tight as ±0.0001 inches.
Water Jet Cutting
Water jet cutting uses high-pressure water mixed with abrasives to cut copper sheets. It is suitable for thick copper (up to 50 mm) without heat distortion. Parameters include:
- Pressure: 40,000–60,000 psi for efficient cutting.
- Abrasive Type: Garnet abrasives are commonly used for copper.
- Cutting Speed: 50–200 mm/min, depending on thickness and precision requirements.
This method is ideal for prototypes and avoids thermal stress but may require secondary finishing for smooth edges.
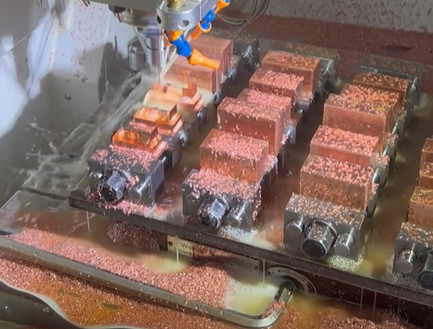
Machining Precision and Complexity
Achieving high precision in copper machining requires addressing the material’s softness and thermal conductivity. Complex geometries, such as internal cooling channels or intricate electrical components, demand advanced techniques and careful planning.
- Tolerances: Precision machining can achieve tolerances of ±0.0005 inches for milling and turning, and ±0.0001 inches for EDM. Tight tolerances increase machining time and cost.
- Complex Geometries: Multi-axis CNC machines (4- or 5-axis) are used for complex parts, reducing setups and improving accuracy. For example, 5-axis milling can create undercuts and curved surfaces unachievable with 3-axis machines.
- Surface Finish: Copper’s softness allows for excellent surface finishes (Ra 0.4–1.6 µm) but requires low feed rates and sharp tools to avoid burrs.
Complex designs increase machining difficulty, necessitating experienced operators and advanced equipment to maintain quality.
Machining Difficulties
Copper’s properties create specific machining difficulties that must be managed to ensure quality and efficiency. Below are the primary issues encountered:
Difficulty | Description | Solution |
---|---|---|
Burr Formation | Copper’s ductility leads to burrs, especially in milling and drilling, affecting surface quality. | Use sharp tools, low feed rates, and post-processing like deburring or tumbling. |
Work Hardening | Excessive deformation can harden copper, making it brittle and harder to machine. | Optimize cutting parameters and use coolant to reduce heat buildup. |
Tool Wear | High thermal conductivity and ductility increase tool wear, especially with pure copper. | Use carbide tools and maintain proper cutting speeds and feeds. |
Chip Management | Copper produces long, stringy chips that can clog tools, especially in drilling. | Employ peck drilling and effective coolant systems to clear chips. |
Addressing these difficulties requires careful selection of tools, machining parameters, and post-processing techniques to achieve desired outcomes.
Material Selection for Machining
Choosing the appropriate copper grade is critical for balancing performance and machinability. The following table compares common copper grades:
Grade | Composition | Machinability | Applications |
---|---|---|---|
C101 | 99.99% copper, 0.0005% oxygen | Poor due to softness | High-conductivity electrical components |
C110 | 99.9% copper, electrolytic tough pitch | Moderate, better than C101 | Busbars, connectors |
Brass (CuZn39Pb3) | Copper-zinc alloy with lead | Excellent, free-cutting | Valves, fittings, gears |
Bronze | Copper-tin-phosphorus alloy | Good, harder than pure copper | Bearings, gears |
For prototyping, C110 is often preferred for its balance of machinability and conductivity, while brass is chosen for complex, high-precision parts.
Design Considerations for Copper Machining
Effective design for manufacturability (DFM) is essential for copper machining. Key considerations include:
- Tolerances: Specify loose tolerances where possible to reduce machining time and cost while maintaining functionality.
- Geometry: Avoid deep pockets with small radii, as they increase tool wear and machining difficulty.
- Setup Reduction: Design parts to minimize the number of setups, reducing errors and production time.
- Material Selection: Match the copper grade to the application’s requirements, considering conductivity, strength, and machinability.
Collaboration with machining experts during the design phase can optimize outcomes and reduce costs.
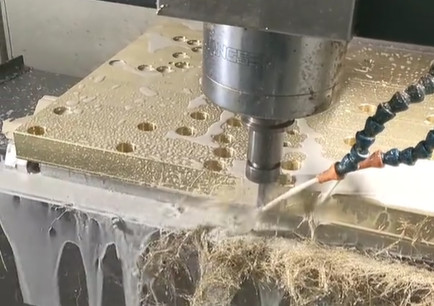
Post-Processing and Finishing
Post-processing enhances copper parts’ functionality and appearance. Common techniques include:
- Tumbling: Smooths rough edges and provides a uniform matte finish, ideal for complex geometries.
- Electropolishing: Improves surface finish (Ra 0.2–0.8 µm) and corrosion resistance.
- Electroplating: Adds protective coatings to enhance durability and reduce oxidation.
- Painting: Provides aesthetic appeal and additional corrosion protection for consumer-facing parts.
Finishing choices depend on the application, with electropolishing preferred for medical and electrical components.
Conclusion
Copper’s exceptional properties make it a vital material for applications in electronics, plumbing, medical devices, and more. Machining copper, however, requires careful consideration of its softness, ductility, and thermal conductivity to achieve high precision and complex geometries. Techniques like CNC milling, turning, drilling, EDM, and water jet cutting, combined with proper tool selection and parameter optimization, enable the production of high-quality copper components. By understanding copper’s properties, selecting appropriate grades, and addressing machining difficulties, manufacturers can meet the demands of diverse industries effectively.