Custom machining is a cornerstone of modern manufacturing, enabling the production of highly precise, tailored components for a wide range of industries. Unlike mass production, custom machining focuses on creating parts that meet specific design requirements, often for unique or low-volume applications. This article delves into the intricacies of custom machining, exploring its processes, materials, applications, and benefits, with detailed technical parameters to provide a thorough understanding of this specialized field.
What is Custom Machining?
Custom machining refers to the process of manufacturing parts or components to exact specifications using advanced machining techniques. It involves removing material from a workpiece—such as metal, plastic, or composite—to achieve the desired shape, size, and surface finish. This process is highly customizable, allowing manufacturers to produce one-off parts, prototypes, or small batches tailored to a customer’s unique needs.
The precision and flexibility of custom machining make it indispensable in industries such as aerospace, automotive, medical devices, and robotics, where standard off-the-shelf components may not suffice. By leveraging technologies like Computer Numerical Control (CNC) machining, manufacturers can achieve tolerances as tight as ±0.001 mm, ensuring parts meet stringent performance criteria.
Key Characteristics of Custom Machining
Custom machining stands out due to several defining characteristics:
- Precision: Achieves tight tolerances and high-quality surface finishes, critical for high-performance applications.
- Customization: Parts are designed and fabricated to meet unique specifications, often based on customer-provided blueprints or CAD models.
- Versatility: Supports a wide range of materials and machining techniques, from milling to grinding.
- Scalability: Suitable for prototyping, one-off production, or small to medium production runs.
History and Evolution of Custom Machining
The roots of custom machining trace back to manual machining techniques, where skilled machinists used lathes, mills, and drills to craft parts by hand. The advent of CNC technology in the mid-20th century revolutionized the field, introducing automation and precision previously unattainable. Today, advancements in software, such as CAD (Computer-Aided Design) and CAM (Computer-Aided Manufacturing), have further enhanced the capabilities of custom machining, enabling complex geometries and rapid prototyping.
Core Processes in Custom Machining
Custom machining encompasses a variety of processes, each suited to specific applications and material types. Below, we explore the most common techniques, along with their technical parameters and use cases.
CNC Machining
CNC machining is the backbone of modern custom machining. It involves the use of computer-controlled machines to execute precise movements of cutting tools. CNC machines can perform multiple operations—such as cutting, drilling, and turning—in a single setup, reducing production time and improving accuracy.
Technical Parameters:
- Tolerance: ±0.005 mm to ±0.001 mm for high-precision applications.
- Spindle Speed: 10,000–30,000 RPM, depending on material and tool type.
- Axis Capability: 3-axis, 4-axis, or 5-axis machines for complex geometries.
- Materials: Aluminum, stainless steel, titanium, ABS plastic, PEEK, and more.
Use Cases: Aerospace components, medical implants, and automotive prototypes.
Turning
Turning involves rotating a workpiece while a stationary cutting tool removes material to create cylindrical or conical shapes. This process is typically performed on a lathe, either manual or CNC-controlled.
Technical Parameters:
- Tolerance: ±0.01 mm for general applications, ±0.002 mm for precision turning.
- Workpiece Diameter: Up to 500 mm for standard lathes, larger for specialized equipment.
- Surface Finish: Ra 0.8–1.6 µm (micrometers) for smooth finishes.
- Materials: Brass, copper, steel, and engineering plastics.
Use Cases: Shafts, bushings, and threaded components.
Milling
Milling uses rotary cutters to remove material from a stationary workpiece, creating flat surfaces, slots, or complex contours. CNC milling machines are highly versatile, capable of producing intricate parts with multiple features.
Technical Parameters:
- Tolerance: ±0.01 mm for standard milling, ±0.005 mm for high-precision milling.
- Tool Diameter: 0.5 mm to 50 mm, depending on the feature size.
- Surface Finish: Ra 1.6–3.2 µm for general milling, Ra 0.4 µm for fine milling.
- Materials: Aluminum, tool steel, and composites.
Use Cases: Enclosures, brackets, and molds.
Grinding
Grinding uses an abrasive wheel to remove small amounts of material, achieving ultra-fine surface finishes and tight tolerances. It is often used as a finishing process after other machining operations.
Technical Parameters:
- Tolerance: ±0.0005 mm for precision grinding.
- Surface Finish: Ra 0.1–0.4 µm for mirror-like finishes.
- Wheel Speed: 20,000–40,000 RPM for high-speed grinding.
- Materials: Hardened steel, ceramics, and carbides.
Use Cases: Cutting tools, bearings, and precision gears.
Materials Used in Custom Machining
The choice of material in custom machining is critical, as it affects the part’s performance, durability, and manufacturability. Below is a table summarizing common materials, their properties, and applications.
Material | Properties | Applications |
---|---|---|
Aluminum | Lightweight, corrosion-resistant, high strength-to-weight ratio | Aerospace components, automotive parts |
Stainless Steel | High strength, corrosion-resistant, durable | Medical devices, food processing equipment |
Titanium | High strength, low weight, biocompatible | Medical implants, aerospace fasteners |
ABS Plastic | Impact-resistant, easy to machine, cost-effective | Prototypes, consumer electronics |
PEEK | High temperature resistance, chemical resistance | Oil and gas components, medical instruments |
Material Selection Considerations
Selecting the right material involves evaluating several factors:
- Mechanical Properties: Strength, hardness, and toughness required for the application.
- Environmental Conditions: Resistance to corrosion, temperature, or chemical exposure.
- Machinability: Ease of cutting, shaping, or finishing the material.
- Cost: Balancing performance with budget constraints.
Applications of Custom Machining
Custom machining serves a diverse range of industries, each with unique requirements for precision and performance. Below are some key applications:
Aerospace
In aerospace, custom machining produces components like turbine blades, landing gear parts, and structural fittings. These parts require tight tolerances (e.g., ±0.002 mm) and materials like titanium or Inconel to withstand extreme conditions.
Automotive
The automotive industry relies on custom machining for prototypes, performance parts, and specialized components like engine blocks or suspension parts. Materials like aluminum and high-strength steel are common, with tolerances often in the ±0.01 mm range.
Medical Devices
Custom machining is critical for producing surgical instruments, implants, and diagnostic equipment. Biocompatible materials like titanium and PEEK are frequently used, with surface finishes as fine as Ra 0.2 µm to ensure patient safety.
Benefits and Challenges of Custom Machining
Custom machining offers numerous advantages but also comes with challenges that manufacturers must address.
Benefits
- High Precision: Achieves tolerances and finishes unattainable by other methods.
- Flexibility: Adapts to changing design requirements or material needs.
- Rapid Prototyping: Enables quick iteration and testing of designs.
- Customization: Meets unique specifications for niche applications.
Challenges
- Cost: Higher per-unit costs compared to mass production, especially for small runs.
- Lead Time: Complex parts may require longer setup and machining times.
- Skilled Labor: Requires experienced machinists and programmers for optimal results.
Quality Control in Custom Machining
Ensuring the quality of custom machined parts is paramount, as even minor deviations can lead to performance failures. Quality control measures include:
- Coordinate Measuring Machines (CMM): For precise dimensional inspections, with accuracy up to ±0.001 mm.
- Surface Profilometers: To measure surface roughness (e.g., Ra 0.1–3.2 µm).
- Non-Destructive Testing (NDT): Techniques like ultrasonic testing to detect internal defects.
- Statistical Process Control (SPC): Monitoring production to maintain consistent quality.
Future Trends in Custom Machining
The custom machining industry is evolving rapidly, driven by technological advancements and market demands. Key trends include:
- Additive Manufacturing Integration: Combining CNC machining with 3D printing for hybrid manufacturing.
- Automation and AI: Using AI-driven CNC systems to optimize tool paths and reduce errors.
- Sustainable Practices: Adopting eco-friendly materials and processes to minimize waste.
- Micro-Machining: Producing smaller, more precise components for electronics and medical devices.
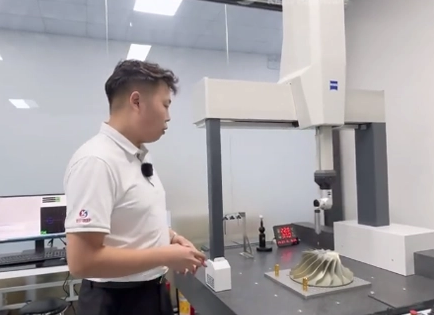
How Can KeSu Help You?
KeSu Manufacturing offers high-quality custom machining services to serve your business. We cover all processes in the supply chain, from 2D and 3D modeling to custom finishes to shipping your product.
To learn more about our capabilities and get your project started, complete our online contact form or request a quote today.
Conclusion
Custom machining is a vital manufacturing process that delivers precision, flexibility, and customization for industries ranging from aerospace to medical devices. By leveraging advanced techniques like CNC machining, turning, milling, and grinding, manufacturers can produce parts with tolerances as tight as ±0.001 mm and surface finishes as fine as Ra 0.1 µm. With a wide range of materials and applications, custom machining continues to evolve, driven by innovations in automation, AI, and sustainable practices. Whether for prototyping or small-batch production, custom machining remains a cornerstone of modern manufacturing, meeting the unique needs of customers and projects worldwide.
FAQs About Custom Machining
What is the difference between custom machining and standard machining?
Custom machining focuses on producing parts to specific, unique designs, often for one-off or low-volume applications. Standard machining typically involves mass production of generic parts with less emphasis on customization.
How long does custom machining take?
Lead times vary based on complexity, material, and quantity. Simple parts may take 1–3 days, while complex components with tight tolerances could take 1–2 weeks or more.
What materials can be used in custom machining?
Custom machining supports a wide range of materials, including metals (aluminum, steel, titanium), plastics (ABS, PEEK), composites, and ceramics, depending on the application.
Is custom machining cost-effective for small production runs?
While custom machining can be more expensive per unit than mass production, it is cost-effective for small runs or prototypes due to its flexibility and lack of need for expensive molds or tooling.