Electrical Discharge Machining (EDM), also known as spark machining, spark eroding, or wire erosion, is a non-traditional manufacturing process that uses electrical discharges to remove material from a workpiece. This guide provides a detailed overview of EDM, including its types, processes, materials, and the complexities and difficulties associated with achieving high precision in machining. EDM is widely used in industries such as aerospace, automotive, and medical device manufacturing, where intricate shapes and tight tolerances are required.
Understanding Electrical Discharge Machining (EDM)
EDM is a subtractive manufacturing process that relies on thermal energy from electrical sparks to erode material from a conductive workpiece. Unlike conventional machining methods, such as milling or turning, EDM does not involve physical contact between the tool and the workpiece, eliminating mechanical stresses and tool wear. The process uses a series of rapid, controlled electrical discharges between two electrodes—the tool electrode and the workpiece—submerged in a dielectric fluid, typically deionized water or hydrocarbon oil. When the voltage between the electrodes reaches a critical threshold, the dielectric fluid breaks down, creating a spark that generates localized heat (8,000–12,000°C), melting and vaporizing small amounts of material. The dielectric fluid cools the process and flushes away debris, ensuring precision and a clean working environment.
The absence of mechanical force makes EDM ideal for machining hard, conductive materials like titanium, tungsten carbide, and hardened steel, as well as fragile or intricate parts that would be damaged by traditional cutting methods. EDM achieves tolerances as tight as ±0.005 mm (±0.0002 inches) and surface finishes as smooth as 0.15–0.2 µRa, making it indispensable for applications requiring high precision and complex geometries.
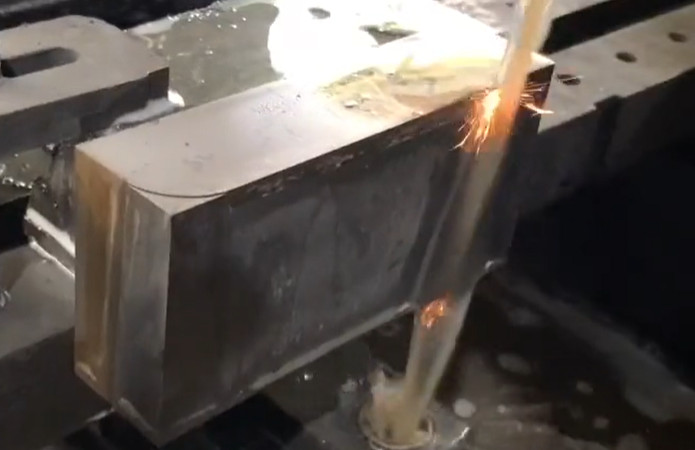
Types of Electrical Discharge Machining
EDM encompasses three primary types, each suited to specific applications and geometries. These are wire EDM, sinker EDM, and hole drilling EDM. Below is a detailed explanation of each type, including their mechanisms and applications.
Wire EDM
Wire Electrical Discharge Machining, also known as wire erosion or wire-cut EDM, uses a thin, electrically charged wire as the electrode to cut through the workpiece. The wire, typically made of brass or copper with diameters ranging from 0.05 mm to 0.35 mm, is guided by CNC-controlled diamond guides and fed from a spool to maintain precision. The wire does not physically contact the workpiece; instead, it creates sparks that erode material, producing intricate shapes and profiles. Deionized water is commonly used as the dielectric fluid to cool the process and flush debris.
Wire EDM is ideal for cutting complex two-dimensional shapes, such as dies, punches, and extrusion molds, with tolerances as tight as ±0.005 mm. It is widely used in industries like aerospace for turbine blade manufacturing and toolmaking for creating precise punches and dies. The process excels at producing sharp external contours and internal cutouts, though it requires a pre-drilled hole or edge to initiate cutting.
Sinker EDM
Sinker EDM, also referred to as ram EDM, plunge EDM, or die-sinking EDM, uses a machined electrode, typically made of graphite or copper, to erode a cavity into the workpiece. The electrode is shaped to mirror the desired cavity and is plunged into the workpiece, creating a negative impression. Hydrocarbon oil is commonly used as the dielectric fluid. The process is particularly effective for forming complex three-dimensional cavities, such as those required for injection molds and die-casting tools.
Sinker EDM achieves tolerances as tight as ±0.001 mm and is suitable for machining intricate internal features, such as sharp internal corners and deep cavities, which are challenging for conventional methods. It is commonly used in mold-making and aerospace for producing detailed components like compressor discs.
Hole Drilling EDM
Hole drilling EDM, sometimes called small hole EDM or "hole popper," is designed to create small, deep holes in conductive materials. It uses a rotating tubular electrode, typically brass or copper, through which dielectric fluid (usually deionized water) flows to flush debris. The process can produce holes as small as 0.038 mm (0.0015 inches) in diameter with aspect ratios exceeding 20:1, maintaining dimensional accuracy along the entire length.
This method is critical for applications like cooling channels in turbine blades and fuel injector nozzles in automotive and aerospace industries. Hole drilling EDM eliminates the need for deburring and can machine holes in hardened materials without compromising structural integrity.
Materials Processed by EDM
EDM is limited to electrically conductive materials, as the process relies on electrical discharges to erode material. Below is a table summarizing commonly machined materials and their applications in EDM.
Material | Properties | Applications |
---|---|---|
Hardened Steel | High strength, wear resistance | Molds, dies, cutting tools |
Titanium | High strength-to-weight ratio, corrosion resistance | Aerospace components, medical implants |
Tungsten Carbide | Extreme hardness, high melting point | Cutting tools, wear-resistant parts |
Inconel | High-temperature resistance, corrosion resistance | Turbine blades, engine components |
Copper | High electrical conductivity | Electrical components, electrodes |
Aluminum | Lightweight, good conductivity | Prototypes, aerospace parts |
EDM’s ability to machine these materials without regard to hardness makes it ideal for prototypes and production parts requiring high precision. For example, titanium and Inconel are challenging to machine conventionally due to their toughness, but EDM handles them effectively, producing smooth surfaces and intricate geometries.
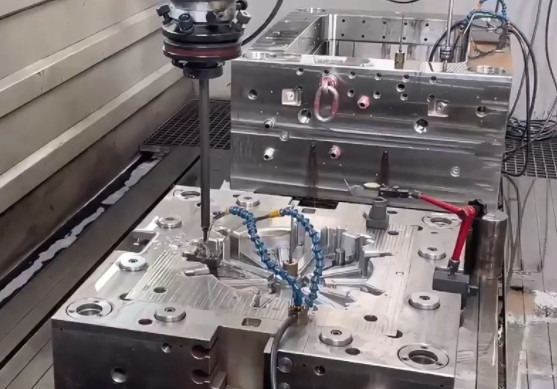
Difficulties in EDM: Precision, Complexity, and Machining Challenges
While EDM offers significant advantages, it presents several difficulties related to precision, complexity, and machining processes. These challenges require careful consideration to achieve optimal results.
Precision and Tolerance Control
Achieving tight tolerances, such as ±0.005 mm, demands precise control over multiple parameters, including electrode design, pulse duration, and dielectric fluid quality. Electrode wear, particularly in sinker EDM, can compromise dimensional accuracy, as the electrode erodes alongside the workpiece. For instance, graphite electrodes wear faster than copper in high-current applications, necessitating frequent replacement or compensation through CNC adjustments. Additionally, maintaining stable electrical thresholds in the sparking gap is critical. Contaminated dielectric fluid, containing conductive debris, can lead to unstable discharges, reducing precision and surface quality.
In wire EDM, wire breakage is a concern, especially when machining thick materials or using high feed rates. Advanced machines incorporate automatic wire-threading and breakage prevention systems, but these add complexity to setup and operation. Tolerances can also be affected by thermal expansion in the workpiece, requiring precise temperature control of the dielectric fluid.
Complexity of Setup and Operation
EDM requires complex setup procedures, particularly for sinker EDM, where custom electrodes must be machined to match the desired cavity. This increases lead time and cost, especially for prototypes or small-batch production. The setup process involves aligning the electrode and workpiece, selecting appropriate pulse settings, and ensuring proper dielectric fluid circulation. For intricate geometries, multiple electrodes may be needed to achieve the desired shape, further complicating the process.
CNC programming for EDM is more intricate than for conventional machining, as it must account for spark gap size (typically 0.01–0.05 mm), electrode wear, and material properties. Operators must have specialized knowledge to optimize parameters like pulse current, voltage, and frequency, which vary depending on the material and desired finish.
Machining Difficulty with Certain Materials
While EDM excels at machining hard materials, certain conductive materials, such as high-grade nickel alloys, pose difficulties due to their low thermal conductivity or high melting points. These materials may require slower machining speeds, increasing processing time. Additionally, EDM is ineffective for non-conductive materials like ceramics or plastics, limiting its versatility compared to other methods like laser cutting.
Deep holes in hole drilling EDM present another challenge. As the electrode penetrates deeper, debris removal becomes less efficient, potentially causing arcing or short circuits. This requires frequent adjustments to flushing pressure and electrode retraction cycles, slowing the process.
Surface Finish and Overcut Issues
While EDM can achieve smooth surface finishes (0.15–0.2 µRa), rapid machining at high currents can result in a "blasted" texture, requiring additional passes at lower currents to refine the surface. Overcut, where the spark gap removes slightly more material than intended, is another issue, particularly in wire EDM, with typical overcut ranges of 0.02–0.3 mm. This must be factored into electrode design and CNC programming to ensure dimensional accuracy.
The heat-affected zone (HAZ), though minimal compared to other thermal processes, can alter material properties, such as hardness or microstructure, in sensitive applications like aerospace components. Careful control of spark energy is necessary to minimize HAZ effects.
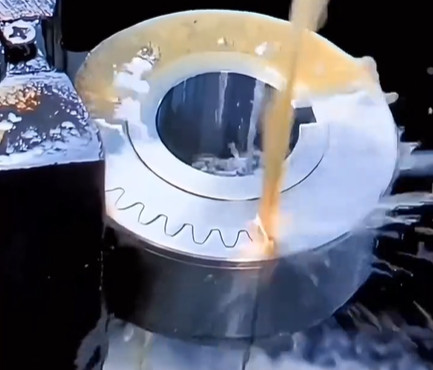
Applications of EDM in Industry
EDM’s ability to produce complex geometries and high-precision parts makes it invaluable across various industries. Below is a table summarizing key applications.
Industry | Applications |
---|---|
Aerospace | Turbine blades, cooling channels, engine components |
Automotive | Fuel injector nozzles, die-casting molds |
Medical | Implants, surgical tools, microelectronics |
Toolmaking | Injection molds, extrusion dies, punches |
EDM is particularly effective for producing prototypes and small-batch parts, where its precision outweighs its slower material removal rate. For example, in aerospace, EDM is used to create intricate cooling channels in turbine blades, while in medical manufacturing, it produces delicate components like pacemaker parts.
Conclusion
Electrical Discharge Machining is a powerful non-traditional machining process that excels at producing intricate shapes and tight tolerances in hard, conductive materials. Its three main types—wire EDM, sinker EDM, and hole drilling EDM—offer unique capabilities for applications ranging from aerospace components to medical implants. However, challenges such as electrode wear, complex setup, and material-specific difficulties require careful management to achieve optimal results. By understanding the process, materials, and limitations, manufacturers can leverage EDM to meet demanding precision requirements in various industries.
FAQs About Electrical Discharge Machining (EDM)
What is Electrical Discharge Machining (EDM), and how does it work?
EDM is a non-traditional manufacturing process that uses controlled electrical sparks to erode material from a conductive workpiece. It works by creating rapid, high-temperature sparks (8,000–12,000°C) between a tool electrode and the workpiece, both submerged in a dielectric fluid (e.g., deionized water or oil). The sparks melt and vaporize small amounts of material, while the dielectric fluid cools the process and flushes away debris. Unlike conventional machining, there is no physical contact between the tool and workpiece, avoiding mechanical stress or tool wear.
What materials can be machined with EDM?
EDM only works on electrically conductive materials because it relies on electrical discharges to erode material. Common materials include:
Hardened steel, titanium, and tungsten carbide (known for hardness and wear resistance).
High-temperature alloys like Inconel (used in aerospace).
Copper and aluminum (for their conductivity).
Non-conductive materials (e.g., ceramics, plastics) cannot be machined with EDM.
What are the main types of EDM, and how do they differ?
EDM has three primary types, each suited to specific tasks:
Wire EDM: Uses a thin brass/copper wire (0.05–0.35 mm diameter) as the electrode to cut complex 2D shapes (e.g., dies, turbine blades). Ideal for sharp contours and tight tolerances (±0.005 mm).
Sinker EDM: Uses a custom-shaped electrode (graphite/copper) to "plunge" and create 3D cavities (e.g., injection molds). Achieves ultra-tight tolerances (±0.001 mm) for intricate internal features.
Hole Drilling EDM: Uses a rotating tubular electrode to drill small, deep holes (0.038 mm diameter, 20:1 aspect ratio) in materials like turbine blades.
Is EDM suitable for large-scale production?
EDM is slower than conventional machining (e.g., milling) due to its incremental material removal. It is most cost-effective for:
Prototypes or small-batch production (where precision outweighs speed).
Complex parts impossible to machine with traditional methods (e.g., deep, narrow cavities).
Large-scale production may use EDM for critical components but often combines it with faster processes for efficiency.
What tolerances and surface finishes can EDM achieve?
EDM is valued for its precision:
Tolerances: As tight as ±0.001 mm (sinker EDM) to ±0.005 mm (wire EDM).
Surface finishes: As smooth as 0.15–0.2 µRa (comparable to polished metal), though faster machining may result in rougher finishes (requiring secondary passes).