Golf equipment, including clubs and balls, significantly impacts performance in competitive play, such as stroke play or match play. Precision manufacturing ensures optimal swing mechanics, ball flight, and control across fairways, greens, and bunkers. This document details materials, prototyping, processing types, and manufacturing difficulties, focusing on technical specifications and systematic processes.
Equipment Role in Competitive Golf
Golf clubs (drivers, irons, wedges, putters) and balls are engineered for specific shots. Drivers require clubheads with high moment of inertia (MOI: 4500–5900 g·cm²) for forgiveness, achieving ball speeds of 150–180 mph. Wedges need precise groove depths (0.020–0.035 inches) for spin rates of 8000–12000 RPM. Putters demand face angle tolerances of ±0.5° for accurate green play. Golf balls balance core compression (70–100) and dimple depth (0.010–0.020 inches) for aerodynamic stability. These specifications are critical in tournaments like the PGA Championship, where equipment precision influences outcomes.
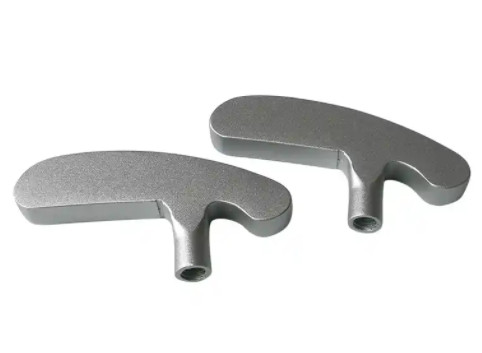
Materials in Golf Equipment
Materials are selected for strength, weight, and durability, tailored to component function. Key materials and their properties are outlined below.
Clubhead Materials
Clubheads use titanium alloys (Ti-6Al-4V, density: 4.43 g/cm³, tensile strength: 900–1000 MPa) for drivers, stainless steel (17-4 PH, hardness: 35–40 HRC) for irons, and carbon fiber composites (density: 1.5–1.8 g/cm³) for hybrids. Titanium requires casting at 1668°C or CNC machining with ±0.01 mm tolerances for face thickness (2.8–3.2 mm). Stainless steel undergoes forging or casting, followed by heat treatment. Composites involve layup and autoclave curing with 30–40% resin content.
Shaft Materials
Shafts are made from carbon fiber (modulus: 230–400 GPa, weight: 50–80 g) or steel (4140, yield strength: 415 MPa, weight: 100–130 g). Carbon fiber uses layered wrapping with fiber angles (0°, 45°, 90°) to control torque (2.0–5.0°). Steel is processed via cold drawing or heat treatment for stiffness.
Grip Materials
Grips use rubber or polyurethane (hardness: 50–60 Shore A), formed by injection molding with thickness of 1.0–1.5 mm. Molds require surface roughness (Ra: 0.8–1.6 µm) for consistent texture.
Golf Ball Materials
Golf balls feature a rubber core (compression: 70–100), ionomer or polyurethane mantle, and polyurethane cover (thickness: 0.5–1.0 mm). Dimples (300–400, depth: 0.010–0.020 inches) are molded or laser-etched for aerodynamic performance (drag coefficient: 0.22–0.25).
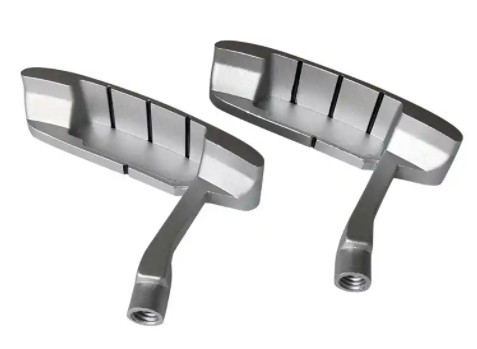
Prototyping Processes
Prototyping validates designs using CAD for 3D modeling and finite element analysis (FEA) for stress and aerodynamic simulation. 3D printing (e.g., SLS) produces clubhead and ball prototypes for testing weight distribution, MOI, and flight paths. Prototypes iterate to meet parameters like clubface angle (±0.5°) or dimple uniformity (±0.001 inches). Post-prototyping, molds are designed for mass production.
Processing Types
Manufacturing involves multiple processes, each tailored to component requirements. Key processes are detailed below.
Process | Application | Key Parameters |
---|---|---|
Casting | Titanium/stainless steel clubheads | Melting point: 1668°C (titanium); mold tolerance: ±0.05 mm |
Forging | Irons, wedges | Pressure: 100–200 MPa; hardness: 35–40 HRC |
CNC Machining | Clubface, grooves | Tolerance: ±0.01 mm; spindle speed: 10,000–20,000 RPM |
Injection Molding | Grips, ball covers | Temperature: 150–200°C; pressure: 50–100 MPa |
Surface Treatment | Clubhead polishing, ball dimples | Surface roughness: Ra 0.8–1.6 µm |
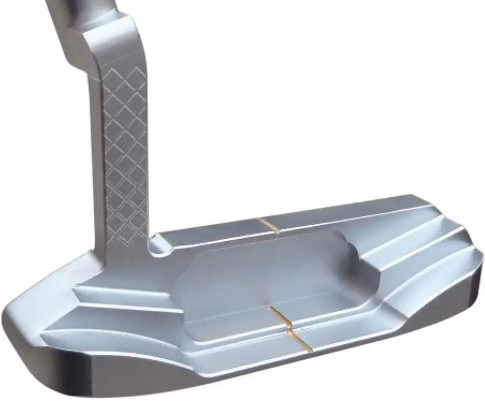
Manufacturing Difficulties
Precision and complexity define manufacturing difficulties, with specific constraints in each process.
Precision Requirements
Clubface angles and groove depths require tolerances of ±0.01 mm to ensure consistent ball spin and trajectory. CNC machining achieves this but demands high-precision tools and calibration. Golf ball dimples need depth uniformity (±0.001 inches) to maintain aerodynamic consistency, requiring advanced molding or laser etching.
Process Complexity
Titanium’s high hardness (35–40 HRC) increases tool wear in CNC machining, necessitating diamond-coated tools and cooling systems. Carbon fiber shaft production involves precise fiber alignment and curing (120–150°C, 2–4 hours), with deviations causing torque inconsistencies. Multilayer golf balls require exact bonding of core, mantle, and cover under tight temperature and pressure windows (150–200°C, 50–100 MPa).
Production Constraints
Small-batch customization for professional players requires frequent mold and parameter adjustments, increasing setup time. High material costs (e.g., titanium: $20–30/kg) and equipment maintenance (CNC machines: $100,000+) add financial constraints. Maintaining process stability across large-scale production is critical to avoid defects like voids in cast clubheads or uneven dimple patterns.
Conclusion
Golf equipment manufacturing integrates advanced materials, prototyping, and processing to meet competitive demands. From titanium clubheads to multilayer balls, each component requires precise engineering to achieve parameters like MOI, spin rate, and aerodynamic efficiency. Processes like casting, forging, and CNC machining address specific needs but face constraints in precision, complexity, and cost. Systematic manufacturing ensures equipment reliability, enabling players to perform optimally in diverse course conditions.
Golf Equipment Manufacturing FAQ
What types of golf equipment are typically manufactured?
Manufacturers produce a wide range of golf equipment. This includes golf clubs such as drivers, irons, wedges, putters, and fairway woods. Golf balls are another major product, along with golf bags designed for carrying clubs and accessories. Other items can be golf shoes, gloves, tees, and training aids. For example, companies like TaylorMade are well - known for their high - performance clubs, golf balls, and accessories.
How are golf clubs manufactured?
Golf clubs have different manufacturing processes depending on the type. For example, for clubheads, they can be forged or cast. In forging, a metal billet (such as titanium or steel) is heated and shaped using dies. Casting involves pouring molten metal into a mold. The shaft is often made from materials like graphite or steel. Graphite shafts are made by wrapping carbon fiber pre - impregnated with resin around a mandrel and then curing it under heat and pressure. After that, the clubhead and shaft are assembled, and a grip is added. Some clubs, especially high - end ones, may also undergo precision machining to ensure consistent performance.
Why are some golf clubs so expensive?
High - end golf clubs are expensive for several reasons. The manufacturing process often involves advanced technologies and high - quality materials. For example, clubs made with premium grades of titanium or high - modulus graphite shafts are costly to produce. Research and development costs are also significant, as manufacturers invest a lot in designing and testing new products. Brand reputation plays a role too; established brands with a history of innovation and high - performance products can command higher prices. Additionally, clubs that are custom - fitted or limited - edition models tend to be more expensive.
What are the benefits of custom - made golf equipment?
Custom - made golf equipment can significantly improve your performance. For clubs, the right length, lie angle, and shaft flex can help you make more solid contact with the ball, increase distance, and improve accuracy. It can also reduce the risk of injury by ensuring that the equipment is comfortable to use. Custom - made golf bags can be designed to fit your specific needs, whether it's having more pockets for accessories or a more ergonomic design for easier carrying. For golf balls, customization can give you a unique look on the course. Overall, custom - made equipment is tailored to your individual game, enhancing your enjoyment and performance.